Inventory+
Summary
TLDRThe video script highlights the importance of having critical spares readily available to minimize downtime in emergencies. It introduces Rockwell Automation's Parts Management Agreement (PMA), which has evolved into an Inventory Plus Service Agreement. This new agreement offers onsite stock, priority replenishment from Rockwell Automation hubs, and a Repair Plus program for both Rockwell and non-Rockwell repairs. The one-year in-service warranty on all agreement stock is emphasized, positioning the agreement as a solution to reduce costs, optimize inventory, and minimize downtime.
Takeaways
- π οΈ Having critical spares on site is essential for emergency preparedness to avoid costly downtime due to component failures.
- π§ Rockwell Automation offers a Parts Management Agreement (PMA) that has evolved into an Inventory Plus Service Agreement.
- π¦ Onsite stock allows for immediate access to a customer's desired bill of materials stored on site for quick replacement of inoperative parts.
- π The bill of materials can be flexibly updated to reflect changes in the installed base, adding or deleting parts as needed.
- π’ Priority replenishment stock is maintained at Rockwell Automation Hub locations to ensure a continuous supply of critical spares.
- π Rockwell Automation replenishes parts from the priority stock as they are consumed from the onsite stock.
- π The agreement includes Repair Plus, which covers both Rockwell and non-Rockwell repair needs with an additional repair value beyond the repair span.
- π° The program aims to decrease costs, optimize inventory management, and minimize downtime for businesses.
- π The agreement provides a customer-determined repair spending amount, enhancing flexibility in repair services.
- β° A one-year in-service warranty is offered on all inventory plus agreement stock, ensuring quality and reliability.
- π€ For businesses seeking to improve their inventory and spare parts management, speaking with an ES&S account manager or service specialist is recommended to get started with the Inventory Plus Service Agreement.
Q & A
What is the main benefit of having critical spares on site in a plant?
-The main benefit of having critical spares on site is to be prepared for emergencies, reducing downtime and avoiding costly delays when a component fails on a critical machine.
What has the Rockwell Automation Parts Management Agreement recently evolved into?
-The Rockwell Automation Parts Management Agreement has recently evolved into an Inventory Plus Service Agreement.
What are the new features included in the Inventory Plus Service Agreement?
-The new features in the Inventory Plus Service Agreement include onsite stock, priority replenishment stock, and a repair plus customer determined repair spending amount.
What is onsite stock in the context of the Inventory Plus Service Agreement?
-Onsite stock refers to the traditional customer desired bill of materials stored on site for ready access when needed. It allows the customer to immediately replace inoperative parts with spares from the shelf.
How does the priority replenishment stock work?
-Priority replenishment stock involves storing the customer's bill of materials at Rockwell Automation Hub locations to replenish parts consumed from the onsite stock, ensuring that critical spares are always available.
What does the repair plus customer determined repair spending amount cover?
-The repair plus customer determined repair spending amount covers both Rockwell and non-Rockwell repair needs, offering additional repair value beyond the usual repair span.
Is there any warranty offered with the Inventory Plus Agreement stock?
-Yes, there is a one-year in-service warranty offered on all Inventory Plus Agreement stock.
How can the Inventory Plus Service Agreement help reduce costs?
-The Inventory Plus Service Agreement can help reduce costs by optimizing inventory and minimizing downtime through efficient management and replenishment of critical spares.
Who should be contacted to get started with the Inventory Plus Agreement?
-To get started with the Inventory Plus Agreement, you should talk to your ES& account manager or service specialist.
Can the bill of materials for onsite stock be updated?
-Yes, the bill of materials for onsite stock can be updated as the installed base changes, allowing parts to be added or deleted as needed.
Outlines
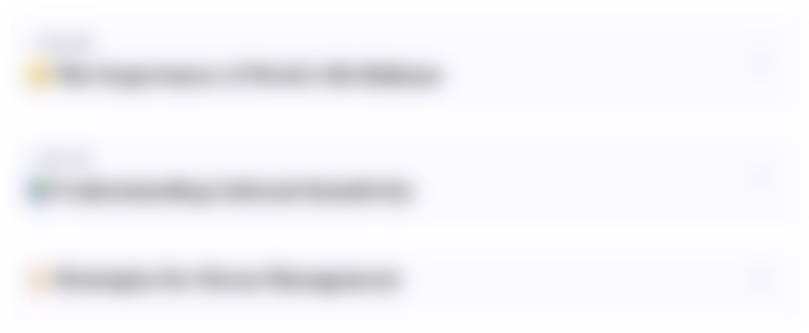
This section is available to paid users only. Please upgrade to access this part.
Upgrade NowMindmap
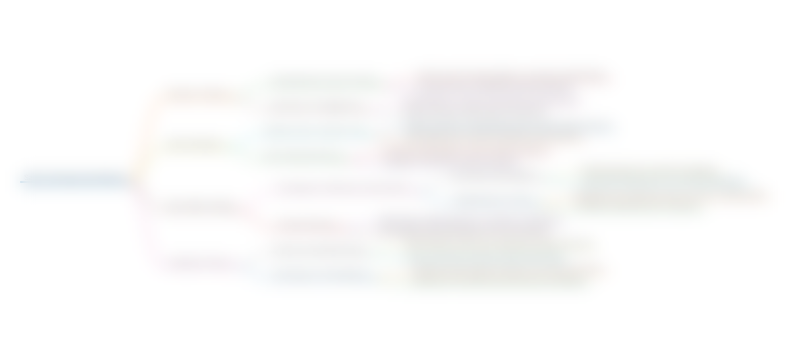
This section is available to paid users only. Please upgrade to access this part.
Upgrade NowKeywords
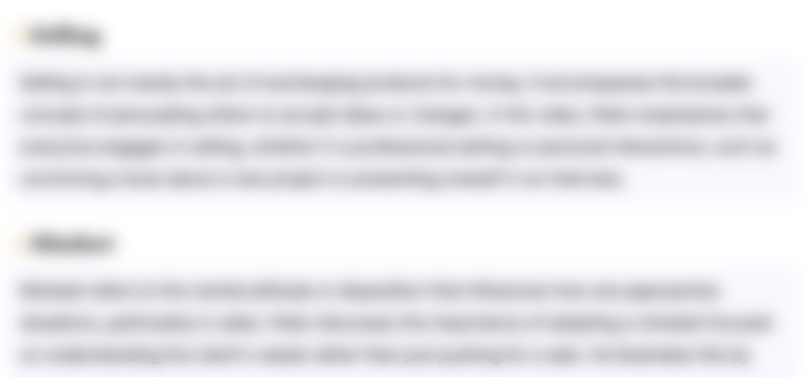
This section is available to paid users only. Please upgrade to access this part.
Upgrade NowHighlights
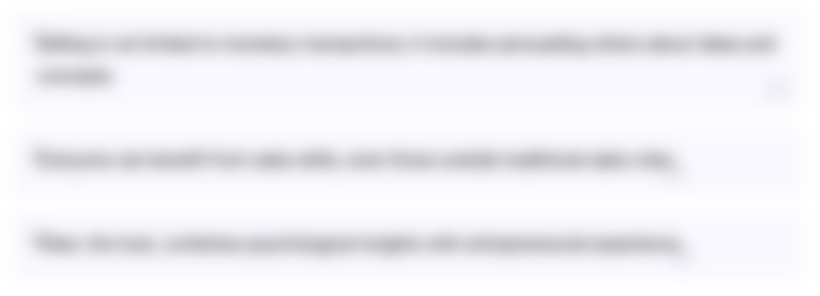
This section is available to paid users only. Please upgrade to access this part.
Upgrade NowTranscripts
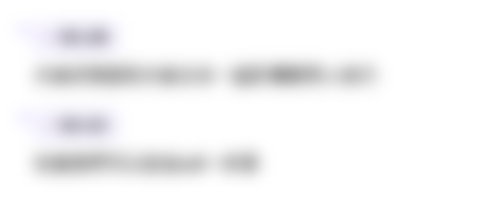
This section is available to paid users only. Please upgrade to access this part.
Upgrade NowBrowse More Related Video

Prepping Supplies You Need to Survive the First 2 Weeks of SHTF
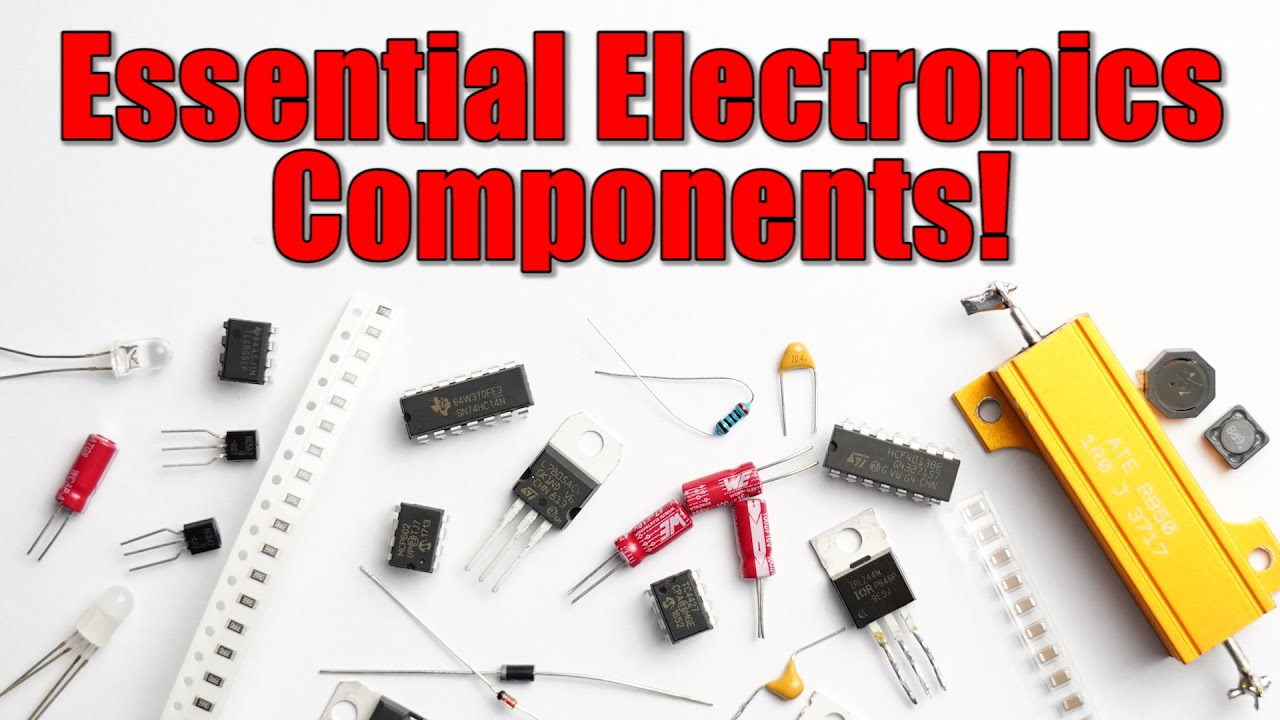
Essential Electronics Components that you will need for creating projects!

Business Impact Analysis - CompTIA Security+ SY0-701 - 5.2
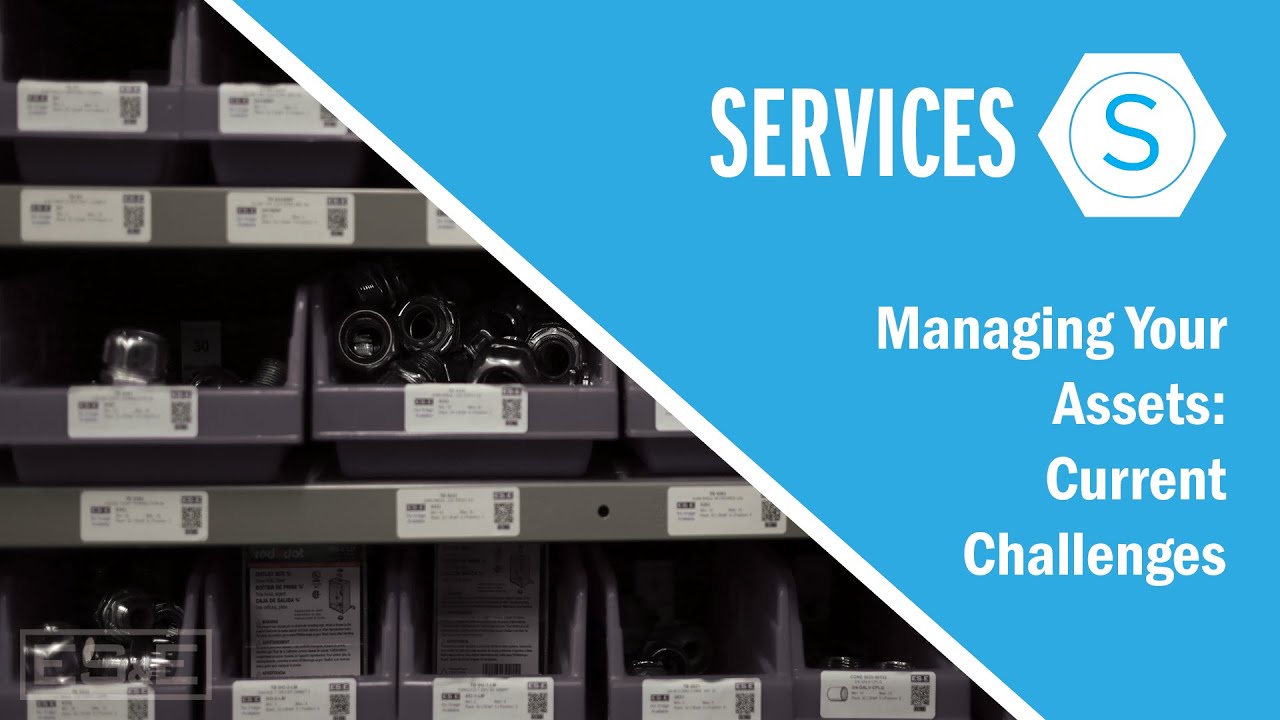
Managing Your Assets 02 - Current Manufacturing Asset Challenges
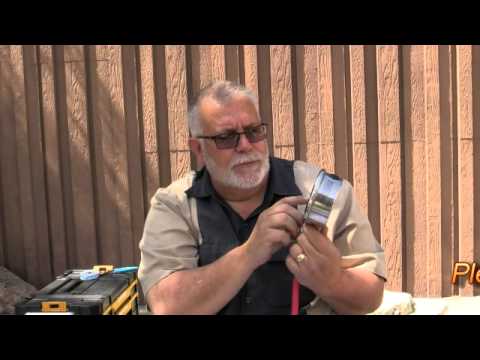
Basic Tools for a Irrigation Audit
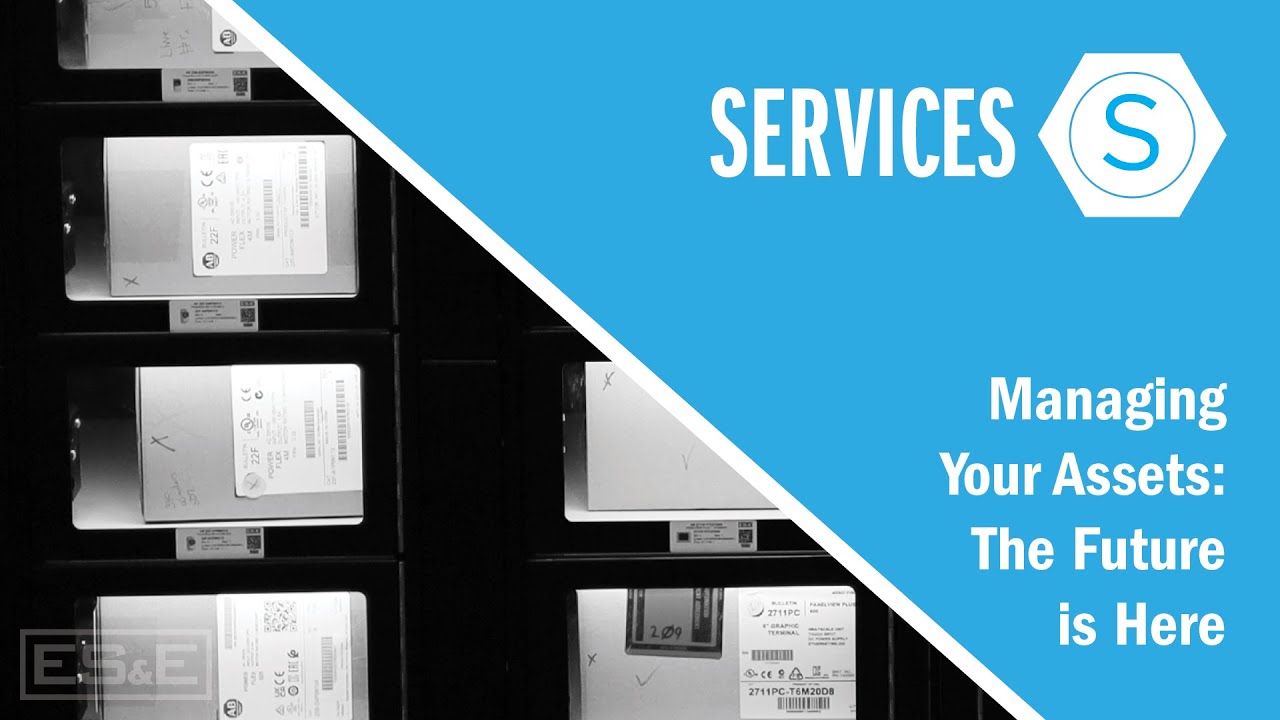
Managing Your Assets 04 - The Future is Here
5.0 / 5 (0 votes)