Explaining Open and Closed loop Systems in Robotics - Control System Engineering
Summary
TLDRThis video script explains two main types of control systems in robotics: open-loop and closed-loop. Open-loop control systems operate without feedback, making them cost-effective and suitable for simple, repetitive tasks like material handling or sprinkler systems. In contrast, closed-loop (servo) systems use feedback to adjust operations, offering flexibility and precision for more complex tasks like machining and welding. While open-loop systems are ideal for stable, low-variation environments, closed-loop systems are better for dynamic and adaptable operations, though they require higher investment and maintenance expertise.
Takeaways
- π Open-loop control systems send signals from the computer to the system driver without feedback from the robot or system.
- π In open-loop systems, the robot performs tasks based on predetermined signals without adjustments during operation.
- π Open-loop control is used in about 35% of robots in the United States, typically in well-defined, repeatable systems.
- π A simple example of open-loop control is an industrial sprinkler system that operates based on set schedules without feedback.
- π Common applications of open-loop control include stop-and-go conveyor systems, machine tending, and material handling.
- π Open-loop systems are low-cost, simple to design, and efficient for tasks with low variation and predefined motion.
- π Closed-loop control systems, also known as servo control, use error-sensing feedback to adjust robot motions.
- π The key difference between open-loop and closed-loop systems is the presence of a feedback loop in closed-loop systems.
- π An example of closed-loop control is a sprinkler system that adjusts watering based on feedback from a moisture sensor in the soil.
- π Closed-loop systems offer greater flexibility, allowing for more complex tasks and multiple program executions, but require higher initial investments and skilled maintenance.
Q & A
What is the main difference between open loop and closed loop control systems in robotics?
-The main difference is that open loop systems do not use feedback to adjust operations, while closed loop systems rely on feedback to make real-time adjustments, improving accuracy and adaptability.
Can you explain how an open loop control system works in a robotics context?
-In an open loop control system, the controller sends signals to the system driver based on the initial conditions, but there is no feedback from the system to verify or adjust those signals. The system operates without corrections after the signal is issued.
What are some real-world applications of open loop control systems in robotics?
-Open loop control systems are used in applications such as conveyor systems with constant loading, punching holes in sheet metal, and material handling tasks, where the process is repeatable and predefined.
What are the advantages of open loop control systems?
-Open loop control systems are cost-effective, simple to implement, and offer high repeatability for tasks that do not require adjustments. They are ideal for well-defined, predictable processes.
What are the limitations of open loop control systems?
-The main limitations are the lack of adaptability and feedback. Open loop systems cannot correct errors or adjust if something goes wrong, making them unsuitable for dynamic or unpredictable tasks.
How does a closed loop control system differ in functionality compared to an open loop system?
-A closed loop control system incorporates a feedback loop, allowing sensors to provide data to the controller. This data enables the system to make real-time adjustments to improve performance and accuracy.
Can you provide an example of a closed loop system in a robotic application?
-An example of a closed loop system is a sprinkler system with a moisture sensor. The sensor measures soil moisture and sends feedback to the controller, which adjusts the water flow to maintain optimal moisture levels.
What are some advantages of closed loop control systems?
-Closed loop control systems offer greater flexibility, precision, and adaptability. They can handle more complex tasks, provide real-time adjustments, and improve overall system performance.
What are the disadvantages or challenges of using closed loop control systems?
-Closed loop systems tend to be more expensive and require more complex setup and maintenance. Skilled personnel are needed to operate and maintain these systems effectively.
In what types of robotic tasks are closed loop control systems most beneficial?
-Closed loop systems are most beneficial in tasks requiring high precision and adaptability, such as machining, welding, material handling, and assembly operations, where conditions may change dynamically and feedback is critical.
Outlines
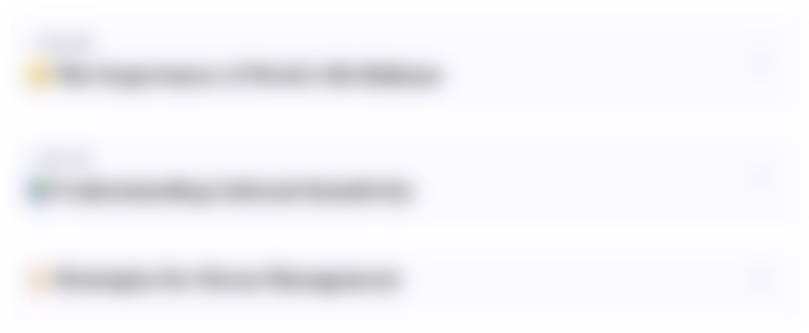
This section is available to paid users only. Please upgrade to access this part.
Upgrade NowMindmap
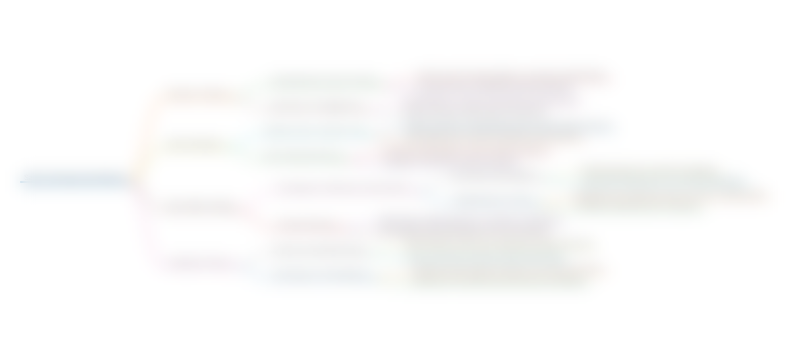
This section is available to paid users only. Please upgrade to access this part.
Upgrade NowKeywords
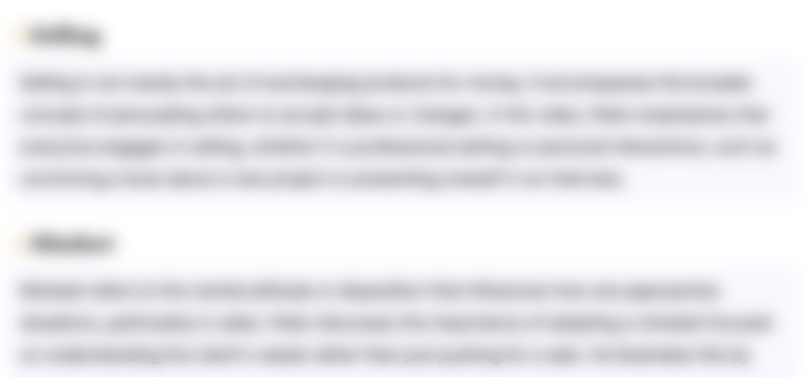
This section is available to paid users only. Please upgrade to access this part.
Upgrade NowHighlights
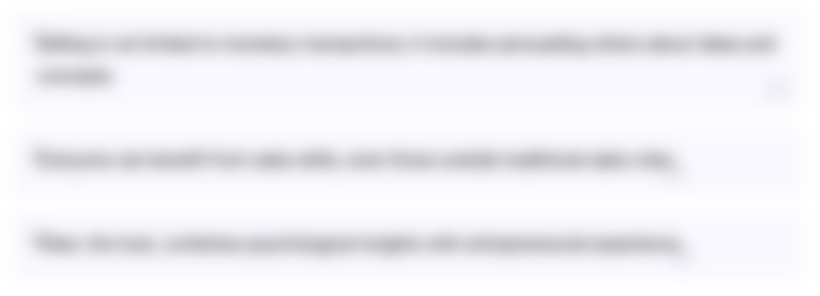
This section is available to paid users only. Please upgrade to access this part.
Upgrade NowTranscripts
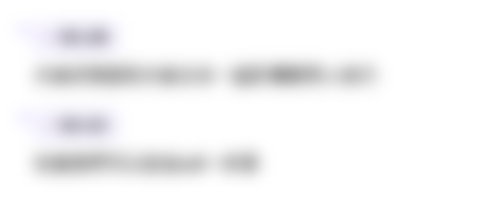
This section is available to paid users only. Please upgrade to access this part.
Upgrade NowBrowse More Related Video

Elements of Motion Control - Open and Closed-loop Control

Pengantar Teknik Robotika 6 - Pengantar Sistem Kendali

Sistem Kontrol || Open Loop dan Close Loop
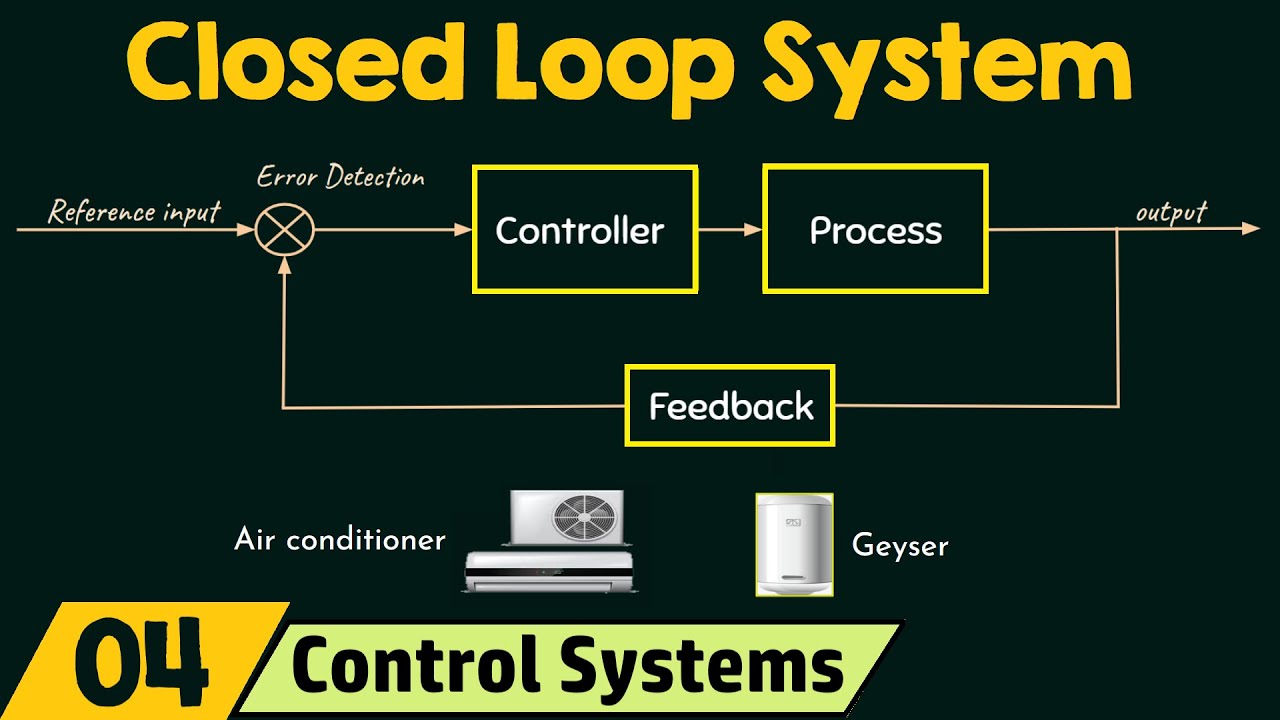
Closed Loop Systems

#131 Introduction to CONTROL SYSTEMS | open loop and closed loop control system || EC Academy

Everything You Need to Know About Control Theory
5.0 / 5 (0 votes)