Which LAYER HEIGHT gives you the STRONGEST 3D prints?
Summary
TLDRIn this video, Stefan from CNC Kitchen explores how different layer heights in 3D printing affect the strength and layer adhesion of parts. He tests six different layer heights ranging from 0.05mm to 0.4mm, printing samples on a Prusa i3 Mk2.5 using Prusament PLA. The results show that thinner layers, particularly around 0.15mm, provide the best strength and layer adhesion, while thicker layers (0.3mm and above) significantly reduce strength. Stefan discusses the variables influencing print quality, including nozzle diameter, extrusion speed, and material properties, offering insights into optimizing 3D print performance.
Takeaways
- 😀 Layer height impacts the strength of 3D prints, especially in terms of layer adhesion.
- 😀 Thinner layers (e.g., 0.05mm) improve surface finish and reduce the 'stairstep' effect but may not always result in stronger prints.
- 😀 Thicker layers (e.g., 0.3mm to 0.4mm) can reduce the strength of 3D prints due to lower density and larger gaps between filament lines.
- 😀 The strength of parts printed with thinner layers may be better due to better bonding between layers, but this varies with material and print settings.
- 😀 Layer adhesion is a critical factor in strength, and failures in prints often occur between the layers themselves.
- 😀 A statistical size effect suggests that parts with fewer layers (thicker layers) are less likely to fail due to misprinting or defects.
- 😀 Testing showed that 0.15mm was the optimal layer height for strength and surface quality in most 3D prints using Prusament PLA.
- 😀 Weight-normalized values showed that thicker layers (0.3mm and 0.4mm) performed worse in terms of strength, even when accounting for material weight differences.
- 😀 The ratio of nozzle diameter to layer thickness is important for predicting print strength, with a 2:1 ratio being a practical limit for optimal strength.
- 😀 The printing temperature, speed, material, and cooling rate all play significant roles in print strength, and are variables worth exploring further in future tests.
- 😀 The results suggest that for the best strength-to-print-time ratio, it’s ideal to use layer heights up to 0.2mm with a 0.4mm nozzle.
Q & A
What is the main factor being investigated in the video?
-The main factor being investigated is the impact of layer height on the strength of 3D prints, particularly focusing on layer adhesion.
What range of layer heights was tested in the experiment?
-The layer heights tested ranged from 0.05mm to 0.4mm.
How does layer height affect print time?
-Print time is inversely proportional to layer height. Thicker layers result in shorter print times, while thinner layers increase print times.
What does the term 'layer adhesion' refer to in the context of this experiment?
-Layer adhesion refers to how well the individual layers of material bond together during the printing process, which affects the overall strength of the print.
What surprising result was found when testing prints with varying layer heights?
-The surprising result was that thinner layers (0.05mm to 0.2mm) performed the best in terms of strength, with 0.15mm being the strongest layer height.
Why did thicker layers (0.3mm and 0.4mm) perform poorly in the tests?
-Thicker layers performed poorly because they had more gaps between filament lines, resulting in weaker bonds between layers, and leading to a decrease in overall strength.
What does the term 'statistical size effect' refer to in the context of this experiment?
-Statistical size effect refers to the idea that parts with more layers (thinner layers) are more likely to fail at a weaker point because there are more potential failure sites, whereas fewer layers (thicker layers) reduce this risk.
What is the relationship between nozzle diameter and layer thickness for optimal strength?
-The strength of a 3D printed part begins to decrease if the layer thickness exceeds half the nozzle diameter. For a 0.4mm nozzle, it’s recommended not to go above a 0.2mm layer height for optimal strength.
How did the material appearance change with varying layer heights, particularly at 0.05mm?
-At 0.05mm layer height, the material showed irregular color due to longer exposure to heat, which could affect the pigment and polymer, causing discoloration.
What other factors, aside from layer height, can influence the strength of 3D prints?
-Other factors include the type of material used, print temperature, printing speed, extrusion width, and part cooling, all of which can significantly impact the strength and layer adhesion of 3D prints.
Outlines
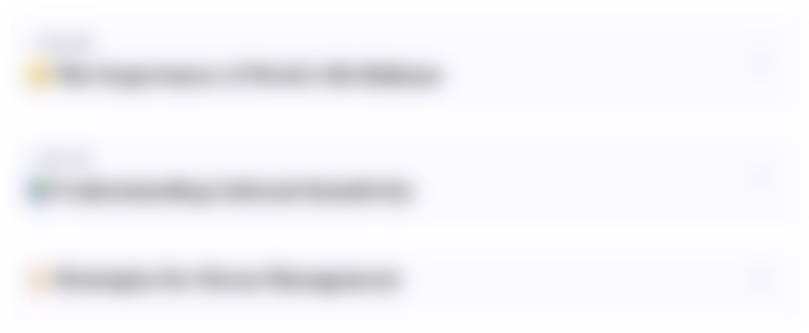
This section is available to paid users only. Please upgrade to access this part.
Upgrade NowMindmap
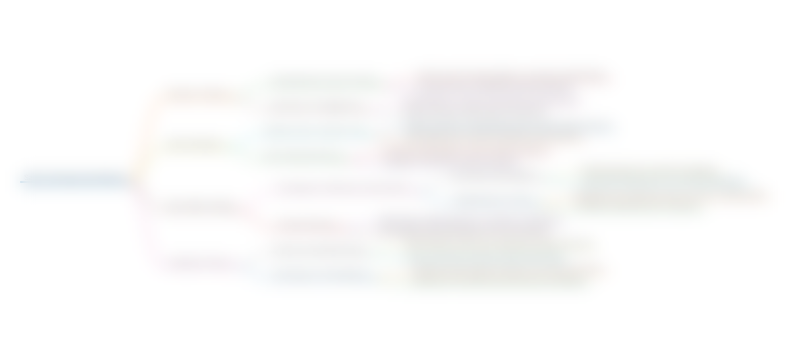
This section is available to paid users only. Please upgrade to access this part.
Upgrade NowKeywords
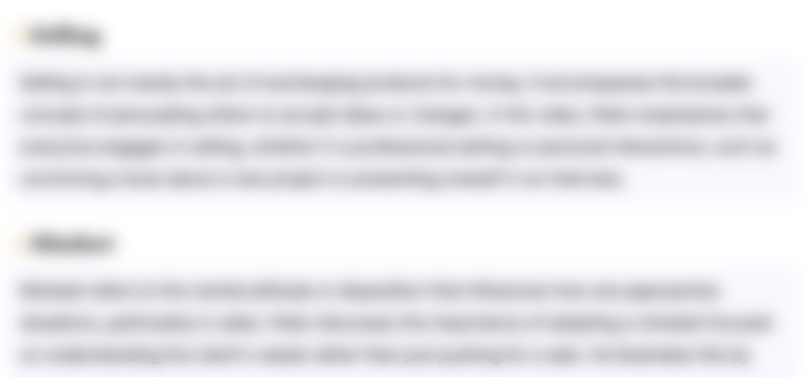
This section is available to paid users only. Please upgrade to access this part.
Upgrade NowHighlights
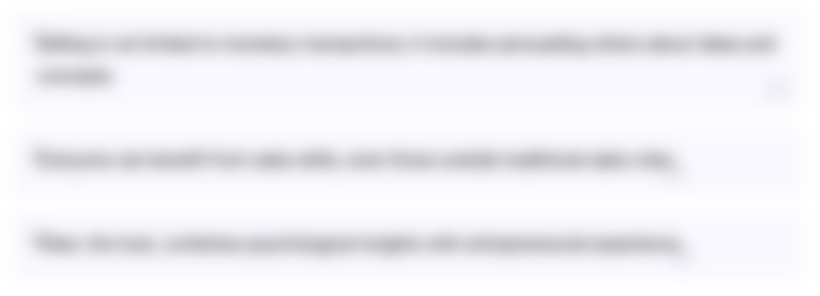
This section is available to paid users only. Please upgrade to access this part.
Upgrade NowTranscripts
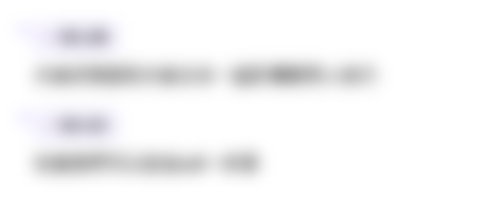
This section is available to paid users only. Please upgrade to access this part.
Upgrade Now5.0 / 5 (0 votes)