Counterboring on a Manual Mill
Summary
TLDRThis tutorial demonstrates the process of counterboring on a manual mill, a technique used to ensure that socket head cap screws sit below the surface of a part. The key steps include measuring the bolt size, selecting the appropriate counterbore tool, setting the correct cutting depth, and using a quill stop for precision. The process involves slowly cutting the hole with lubrication, ensuring that the bolt head does not protrude. The tutorial is designed for those working with a manual mill to accurately seat bolts without surface interference.
Takeaways
- 😀 Counter boring is used for socket head cap screws to ensure the bolt head goes below the surface of the part.
- 😀 The principle behind counter boring is similar to countersinking, but counter boring involves creating a flat-bottomed hole for the bolt head.
- 😀 The counter bore tool has a pilot shaft that guides it into the hole, ensuring precise cutting.
- 😀 A counter bore tool is sized according to the bolt diameter, with labels like 6mm or 8mm for corresponding bolt sizes.
- 😀 To determine the correct depth for the counter bore, measure the bolt head thickness and ensure the counter bore is slightly deeper to keep the bolt head flush with the part surface.
- 😀 In this tutorial, a 6mm bolt is used, and the counter bore is set to a depth of at least 240-250mm.
- 😀 To ensure accuracy, the distance from the pilot tip to the bottom of the part must be at least the desired depth of the counter bore.
- 😀 Lock the quill once the counter bore touches the part to prevent any movement during the boring process.
- 😀 A quill stop is used to ensure the cutting tool only moves a precise distance, preventing over-cutting.
- 😀 The spindle should be turned on while the counter bore cuts, and a slower cutting speed (around 100-300 RPM) is recommended for better results.
- 😀 Use lubrication (such as oil) during the counter boring process to ensure smooth cutting and prevent overheating.
- 😀 After counter boring, check that the bolt head sits below the surface of the part and that the part can be turned over easily without the bolt being stuck.
Q & A
What is the purpose of counterboring?
-Counterboring is used to ensure that the head of a bolt sits below the surface of a part, preventing it from protruding above the surface. This is especially useful for socket head cap screws.
How does a counterbore tool work?
-A counterbore tool has a flat bottom and a pilot. The pilot aligns the tool with the hole, ensuring precise cutting, while the flat bottom matches the head of the bolt to create a recess.
What is the role of the pilot on a counterbore tool?
-The pilot is a shaft on the cutting tool that guides it into the hole, ensuring precise alignment and accurate cutting of the recess for the bolt head.
How do you determine the depth of the counterbore?
-The depth is determined by measuring the thickness of the bolt head and ensuring that the counterbore recess is slightly deeper than the thickness to ensure the head sits below the surface of the part.
What size counterbore should be used for a 6mm bolt?
-A 6mm counterbore should be used for a 6mm bolt. The counterbore tool will have a 6mm shaft and will create a recess sized to fit the 6mm bolt head.
Why is it important to measure the bolt head's thickness?
-Measuring the bolt head's thickness ensures that the counterbore is set to the correct depth, allowing the bolt head to sit flush with or below the surface of the part without protruding.
What should be the minimum depth for the counterbore if the bolt head is 2.30mm thick?
-The minimum depth for the counterbore should be 2.40mm to 2.50mm to ensure the bolt head sits below the part surface.
What is the function of the quill stop in counterboring?
-The quill stop is used to set a limit on how far the quill can move. It ensures that the counterbore tool does not cut too deep and maintains consistent depth during the process.
How does the knee of the mill affect the counterboring process?
-The knee of the mill is raised or lowered to position the part at the correct height for cutting. This ensures that the tool only touches the part when needed and prevents overcutting.
What spindle speed is recommended for counterboring?
-For counterboring, a slower spindle speed of 102 to 300 RPM is recommended. This slower speed allows for better control, especially when working with softer materials.
Outlines
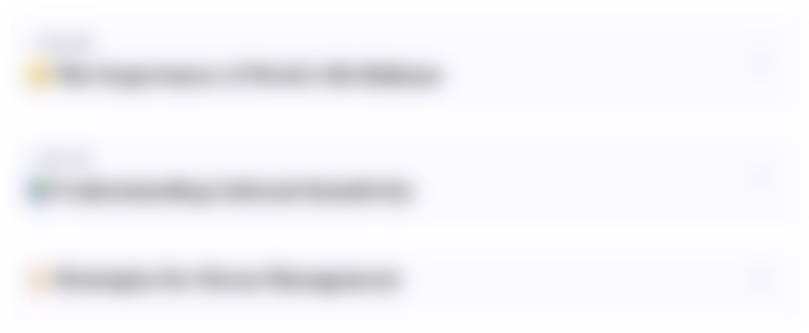
This section is available to paid users only. Please upgrade to access this part.
Upgrade NowMindmap
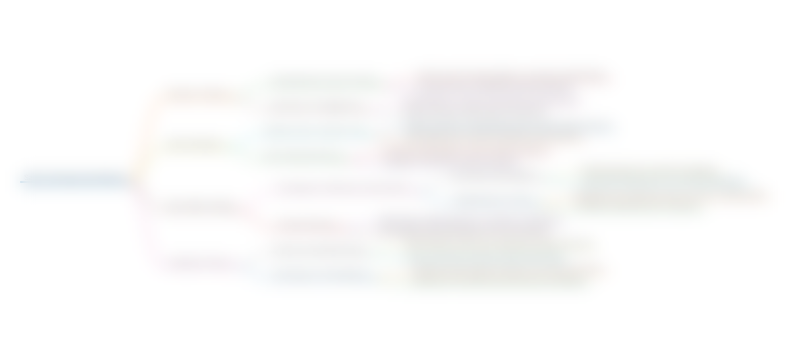
This section is available to paid users only. Please upgrade to access this part.
Upgrade NowKeywords
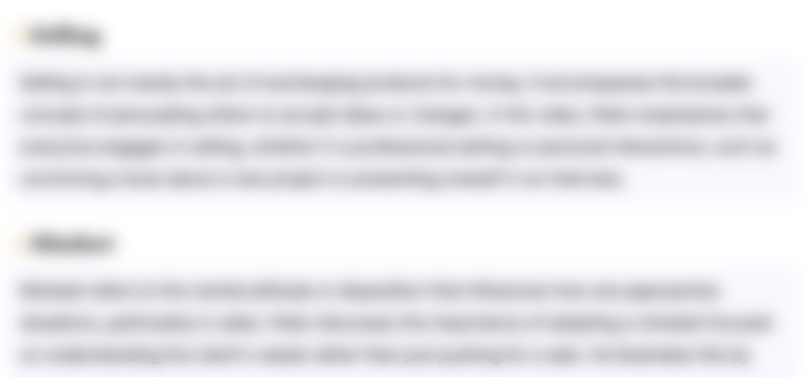
This section is available to paid users only. Please upgrade to access this part.
Upgrade NowHighlights
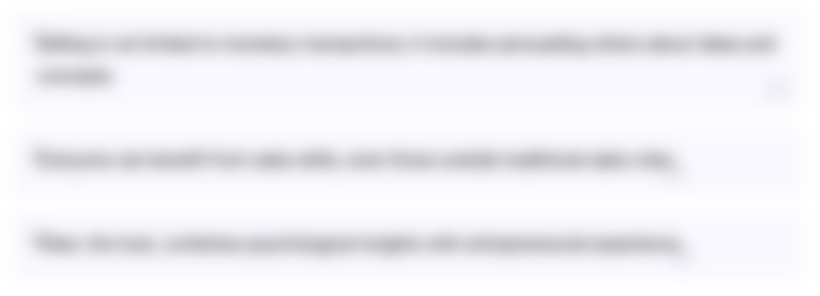
This section is available to paid users only. Please upgrade to access this part.
Upgrade NowTranscripts
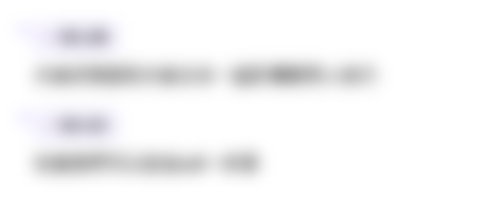
This section is available to paid users only. Please upgrade to access this part.
Upgrade NowBrowse More Related Video
5.0 / 5 (0 votes)