SysAp 7 1 Ladder Logic
Summary
TLDRThis video explains the fundamentals of PLCs (Programmable Logic Controllers) and ladder logic programming. It covers the PLC scan cycle, input-output operations, and logical processes like AND and OR conditions. Through practical examples, the video demonstrates how to use sensors and memory bits to control devices such as pumps and alarms. The content also highlights common errors in ladder logic, such as conflicting conditions, and teaches viewers how to build reliable control systems. This tutorial is aimed at those learning PLC programming and industrial automation.
Takeaways
- 😀 The PLC scan cycle consists of four discrete steps: reading inputs, executing logic, performing diagnostics and communication, and updating outputs.
- 😀 Ladder logic programming in PLCs involves representing logic in a schematic format with symbols for inputs, contacts, and outputs.
- 😀 In ladder logic, the PLC does not execute rungs sequentially, but rather evaluates input conditions and updates outputs in real-time.
- 😀 Understanding the difference between normally open (NO) and normally closed (NC) contacts is crucial for proper ladder logic programming.
- 😀 An AND operation in ladder logic requires both input conditions to be true for the output to be activated.
- 😀 An OR operation in ladder logic allows the output to be activated if at least one input condition is true.
- 😀 The output coil in ladder logic represents a device or internal memory bit and is activated when the corresponding rung is true.
- 😀 Faulty logic, such as using logically impossible conditions (e.g., both normally open and normally closed contacts simultaneously), can lead to dead code.
- 😀 Outputs in ladder logic must always be placed on the far right side of the rung, and only one output can be assigned per rung.
- 😀 Memory bits in ladder logic can be used to latch or unlatch outputs, allowing for control scenarios like holding a start button or stopping a pump after a set condition is met.
Q & A
What are the four main steps in a PLC scan cycle?
-The four main steps in a PLC scan cycle are: 1) Reading all inputs, 2) Executing the logic, 3) Performing diagnostics and communications, and 4) Updating all outputs. This cycle repeats constantly to ensure the PLC reacts to changes in real-time.
Why does the PLC not execute ladder logic rungs sequentially?
-The PLC does not execute rungs sequentially because it evaluates all inputs in parallel, checks the logic vertically, and then updates outputs. This ensures the PLC processes the entire program at once rather than executing one rung at a time.
What is the impact of having conflicting rungs in ladder logic?
-If conflicting rungs exist (one turning an output on and another turning it off), the output will never be activated because the PLC processes all the logic simultaneously. The output will remain in its initial state.
How can ladder logic be understood in terms of electrical circuits?
-Ladder logic can be understood as an electrical diagram where the rails represent power and ground, and the contacts act like switches in the circuit. This makes it easier for electricians to relate to, as it mirrors traditional relay logic diagrams.
What does the 'normally open' contact symbol represent in PLC programming?
-'Normally open' contact symbols represent inputs that are open (no signal) when the corresponding switch is not activated. When the input is activated (i.e., receiving voltage), the contact closes, allowing current to flow.
What is the difference between a normal output and a set output in ladder logic?
-A normal output will turn on when the rung conditions are true and turn off when those conditions are false. A set output, however, will remain on even after the rung goes false, and it will only be turned off when another rung resets it.
What is the purpose of using memory bits in PLC programming?
-Memory bits in PLC programming serve as internal storage for binary values. They are used to store temporary conditions, such as remembering whether a button was pressed or if a machine state needs to be maintained, without needing to continuously check inputs.
How does branching work in ladder logic?
-Branching in ladder logic allows multiple conditions (e.g., sensors or switches) to be evaluated in parallel. This helps create more complex control schemes, where multiple inputs can trigger outputs based on different combinations of conditions.
Why can't multiple outputs be placed in series on the same rung in ladder logic?
-Multiple outputs cannot be placed in series because each output must be independently controlled. Placing outputs in series could cause one output to interfere with the others, making the logic unreliable. Each output needs its own branch to ensure clear and isolated control.
What common logical error is demonstrated in the faulty rung with input 4 in the example?
-The logical error in the rung with input 4 involves using both a normally open and normally closed contact for the same input, which is logically impossible. An input cannot be both open and closed simultaneously, so this part of the logic will never be true and can be safely removed.
Outlines
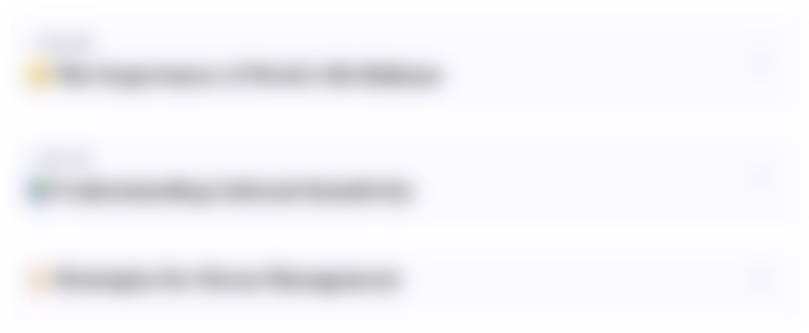
This section is available to paid users only. Please upgrade to access this part.
Upgrade NowMindmap
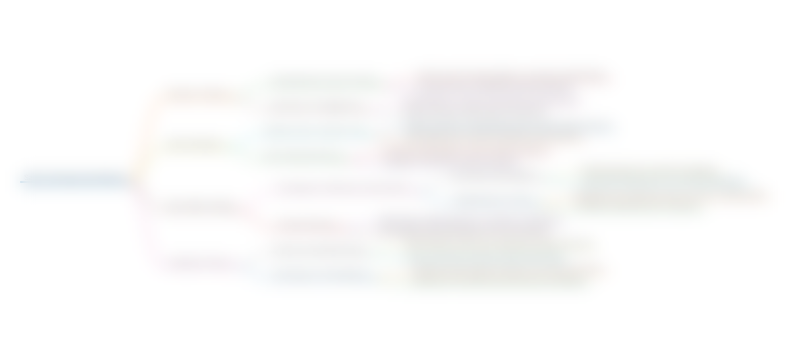
This section is available to paid users only. Please upgrade to access this part.
Upgrade NowKeywords
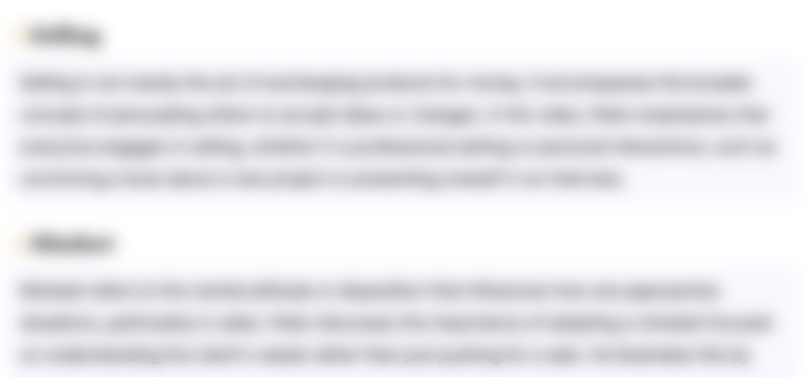
This section is available to paid users only. Please upgrade to access this part.
Upgrade NowHighlights
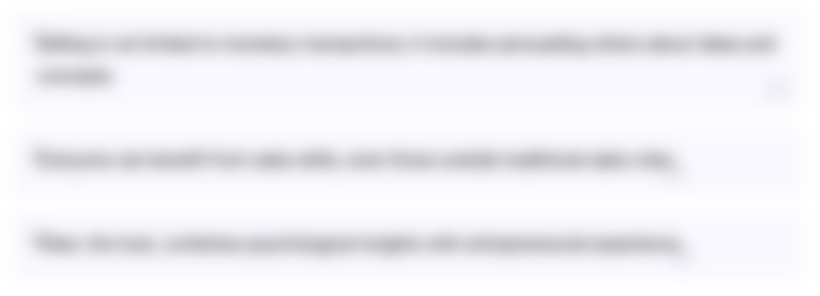
This section is available to paid users only. Please upgrade to access this part.
Upgrade NowTranscripts
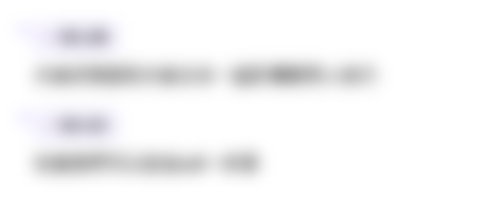
This section is available to paid users only. Please upgrade to access this part.
Upgrade NowBrowse More Related Video
5.0 / 5 (0 votes)