LEWIS BENDING STRESS at the Teeth of a Gear in Just Over 12 Minutes!
Summary
TLDRThis video explores gear design, focusing on two common failure types: bending and surface pitting. It introduces the Lewis bending equation, essential for calculating bending stress in gear teeth modeled as cantilever beams. The discussion includes the significance of the Lewis form factor, dynamic factors, and the role of pitch line velocity in gear operation. Through a practical example, viewers learn how to compute the maximum power transmission in a gear system while considering material properties and design factors. The video sets the stage for future topics on surface durability and gear performance.
Takeaways
- 😀 Bending failure in gears occurs when bending stress surpasses the yield or endurance strength.
- 😀 Surface failure, or pitting, arises when surface stress exceeds surface endurance strength.
- 😀 The Lewis bending equation remains essential for gear design despite its simplifications of real geometry.
- 😀 The maximum moment in a cantilever beam representing a gear tooth is located at the wall where forces are applied.
- 😀 Bending stress in gear teeth can be calculated using the cantilever beam model and the tangential force acting on the teeth.
- 😀 The Lewis form factor (Y) is a geometric parameter that influences the bending stress calculation based on tooth profile.
- 😀 Dynamic factor (kv) accounts for the effects of speed and inertia in rotating gears, critical for accurate stress assessments.
- 😀 The maximum tangential force is determined to ensure the bending stress does not cause plastic deformation in gear teeth.
- 😀 Power transmission capacity is limited by the weaker gear in a system, highlighting the importance of load distribution.
- 😀 Future discussions will focus on surface durability and pitting, essential for understanding gear longevity.
Q & A
What are the two primary failure modes in gear teeth?
-The two primary failure modes in gear teeth are bending failure and surface failure.
What conditions lead to bending failure in gears?
-Bending failure occurs when the bending stress exceeds the yield strength during moderate use or when it exceeds the bending endurance strength.
How does the Lewis bending equation simplify gear design?
-The Lewis bending equation simplifies the gear tooth geometry into a cantilever beam model, which allows for easier calculation of bending stress.
What is the significance of the Lewis form factor in gear design?
-The Lewis form factor is a geometric parameter that influences the bending stress calculations and is dependent on the circular pitch and the number of teeth.
What role does the dynamic factor (Kv) play in gear performance?
-The dynamic factor (Kv) accounts for the effects of speed and manufacturing processes on the stress experienced by gear teeth during operation.
How is the pitch line velocity calculated, and why is it important?
-Pitch line velocity is calculated as the product of angular velocity and pitch radius; it is important because it affects the stress levels and dynamic factor during gear operation.
What is the relationship between torque and bending stress in gear teeth?
-The maximum tangential force exerted on gear teeth is directly proportional to the torque; if this force is too high, it may cause bending stress that can lead to plastic deformation.
How can engineers ensure the maximum bending stress does not exceed allowable limits?
-Engineers can ensure the maximum bending stress remains within allowable limits by using a design factor, which divides the material's yield strength by the expected stress.
In the provided example, how was the maximum power that could be transmitted determined?
-The maximum power was determined by calculating the maximum tangential force, then using it along with angular velocity to find the power transmitted, ensuring it stayed within the allowable stress limits.
What factors might affect the calculation of a more reliable stress value in gear systems?
-Factors that may affect stress calculations include dynamic effects, geometric effects, size factors, surface factors, load distribution factors, and hardness ratios.
Outlines
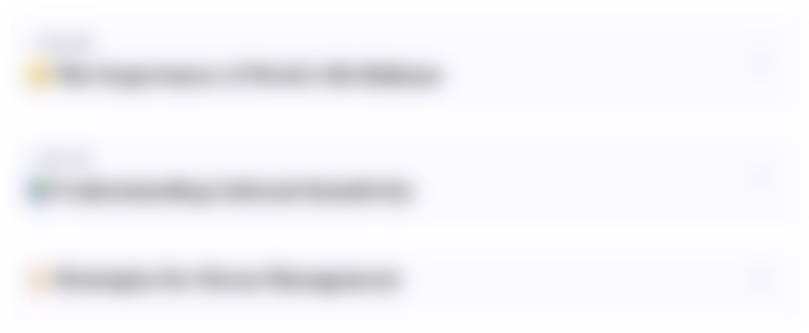
This section is available to paid users only. Please upgrade to access this part.
Upgrade NowMindmap
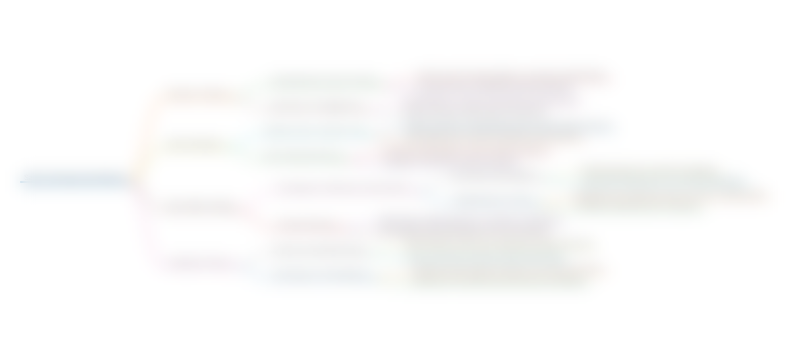
This section is available to paid users only. Please upgrade to access this part.
Upgrade NowKeywords
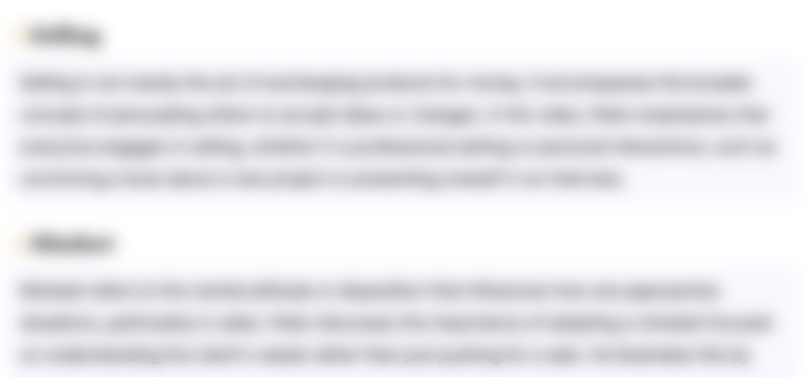
This section is available to paid users only. Please upgrade to access this part.
Upgrade NowHighlights
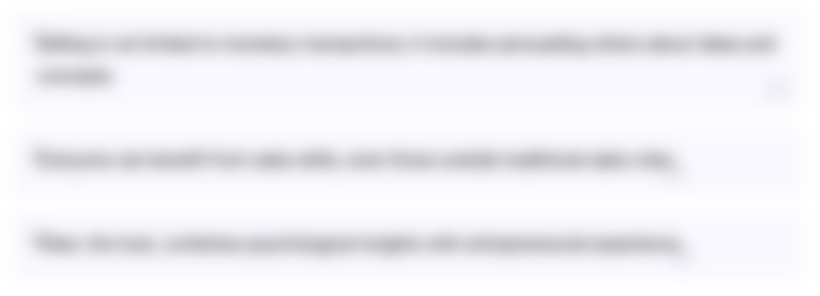
This section is available to paid users only. Please upgrade to access this part.
Upgrade NowTranscripts
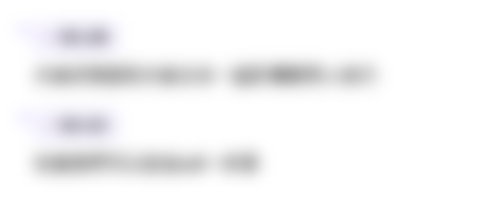
This section is available to paid users only. Please upgrade to access this part.
Upgrade NowBrowse More Related Video
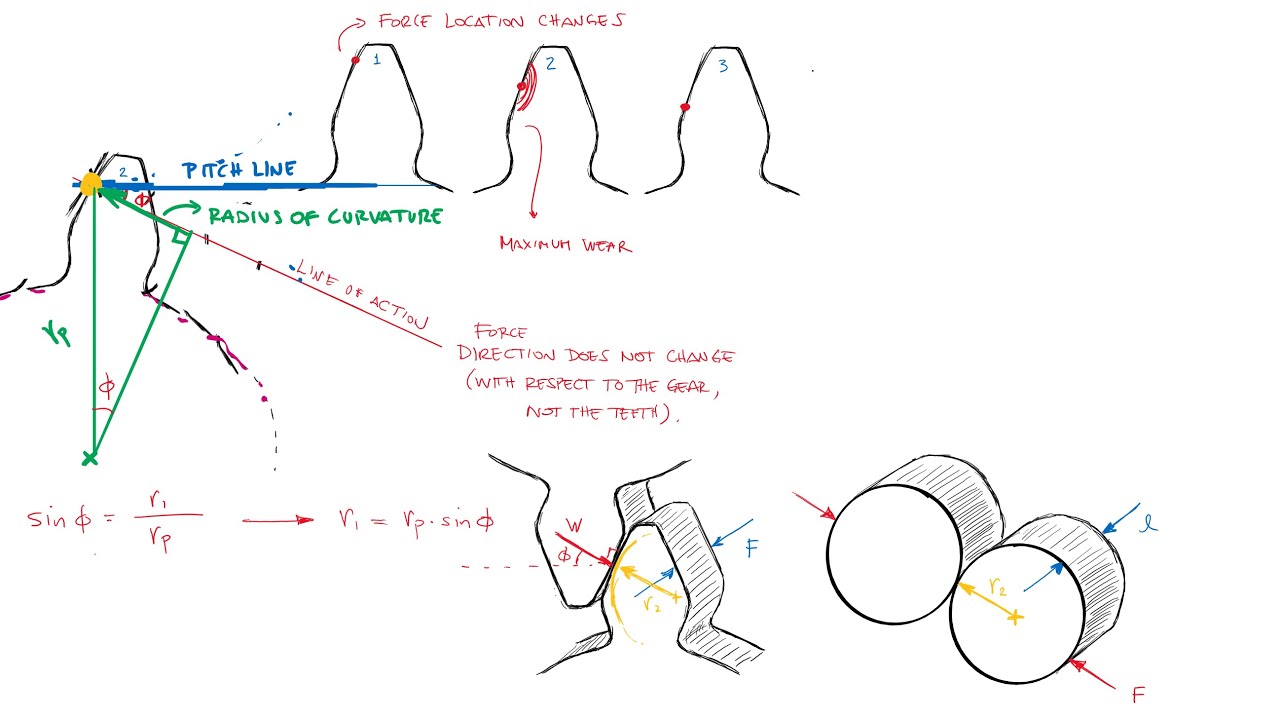
Gear PITTING - Surface Contact Stress Fatigue Failure in Just Over 10 Minutes!
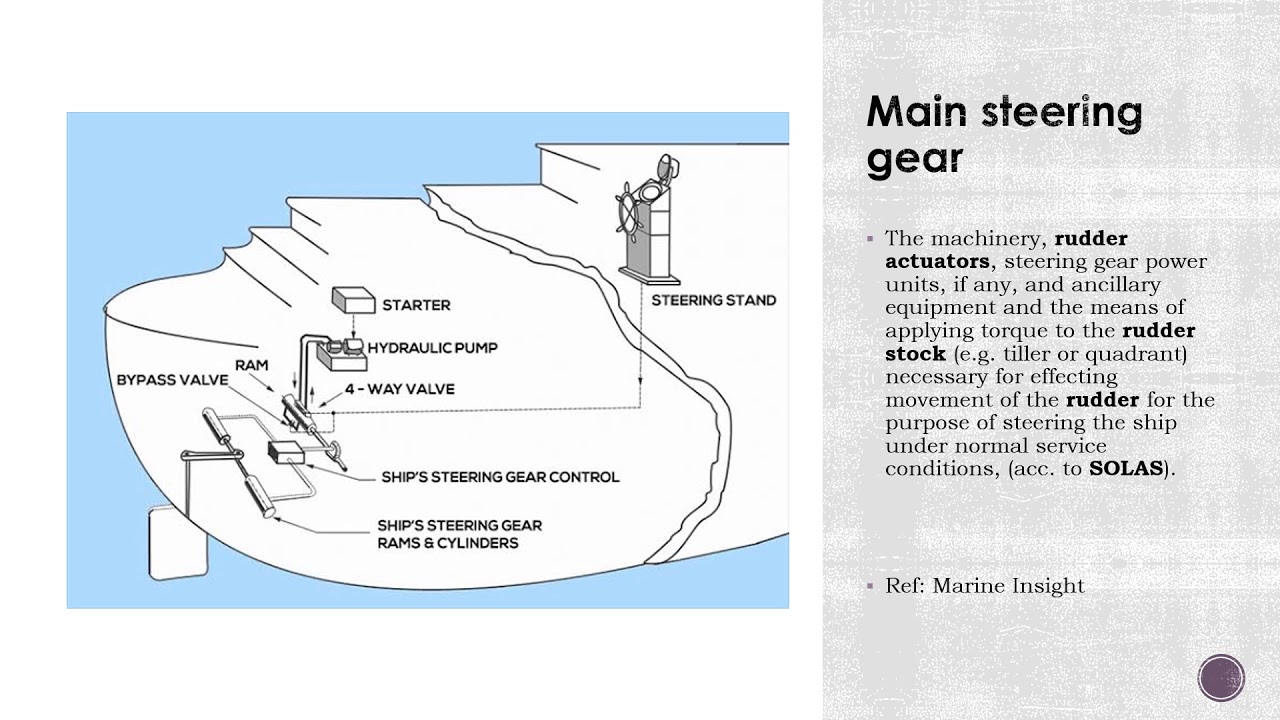
Different types of Steering Gears found on ships
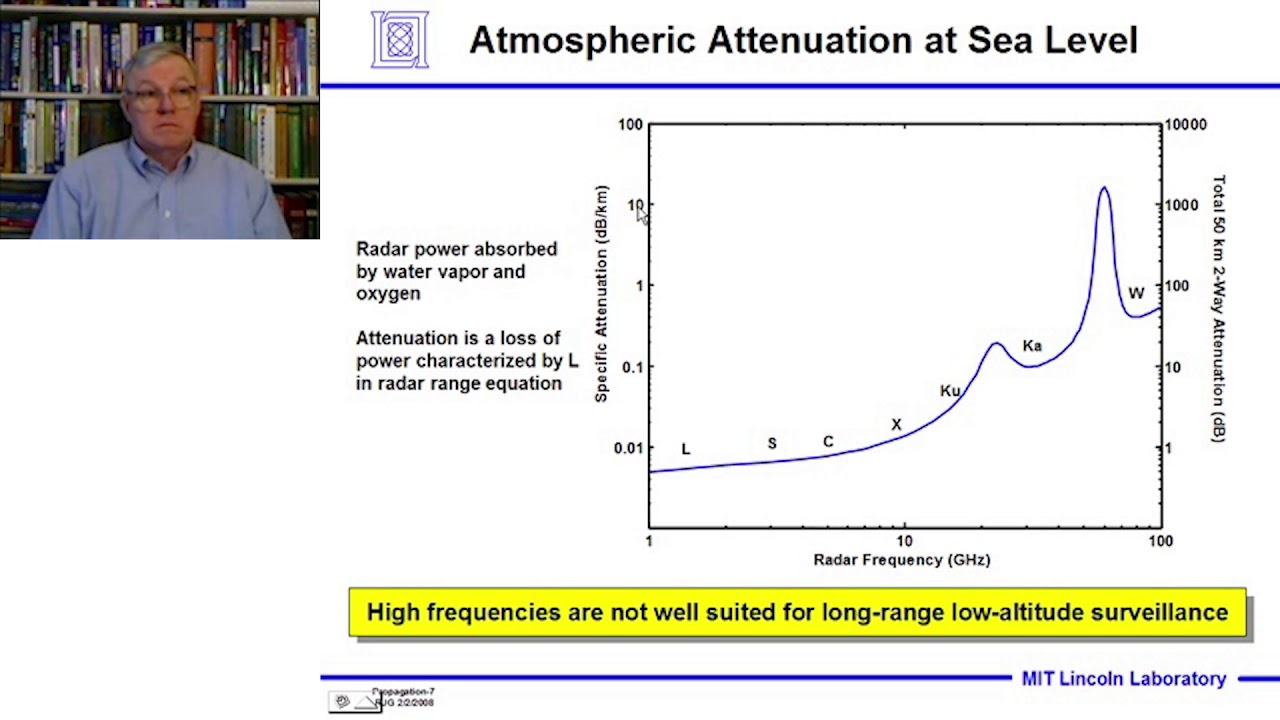
Introduction to Radar Systems – Lecture 3 – Propagation Effects; Part 1
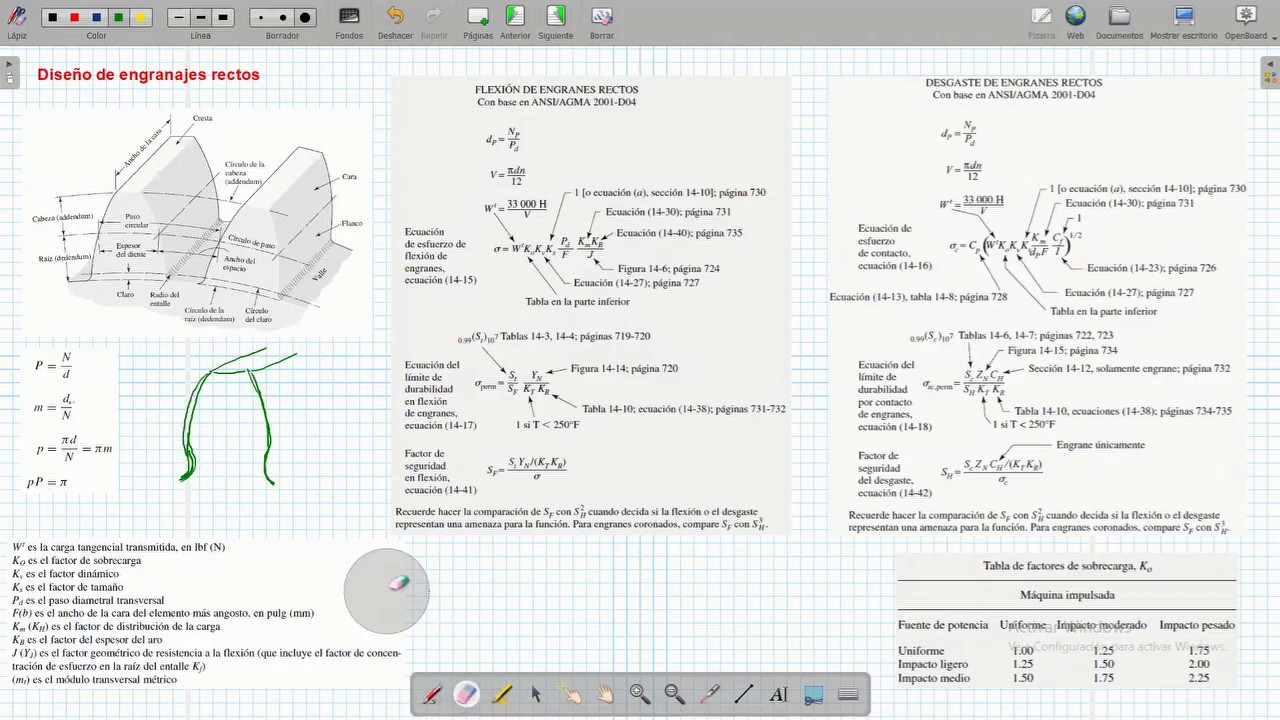
MetodologÃa ANSI/AGMA para diseño de engranes rectos y helicoidales parte 1
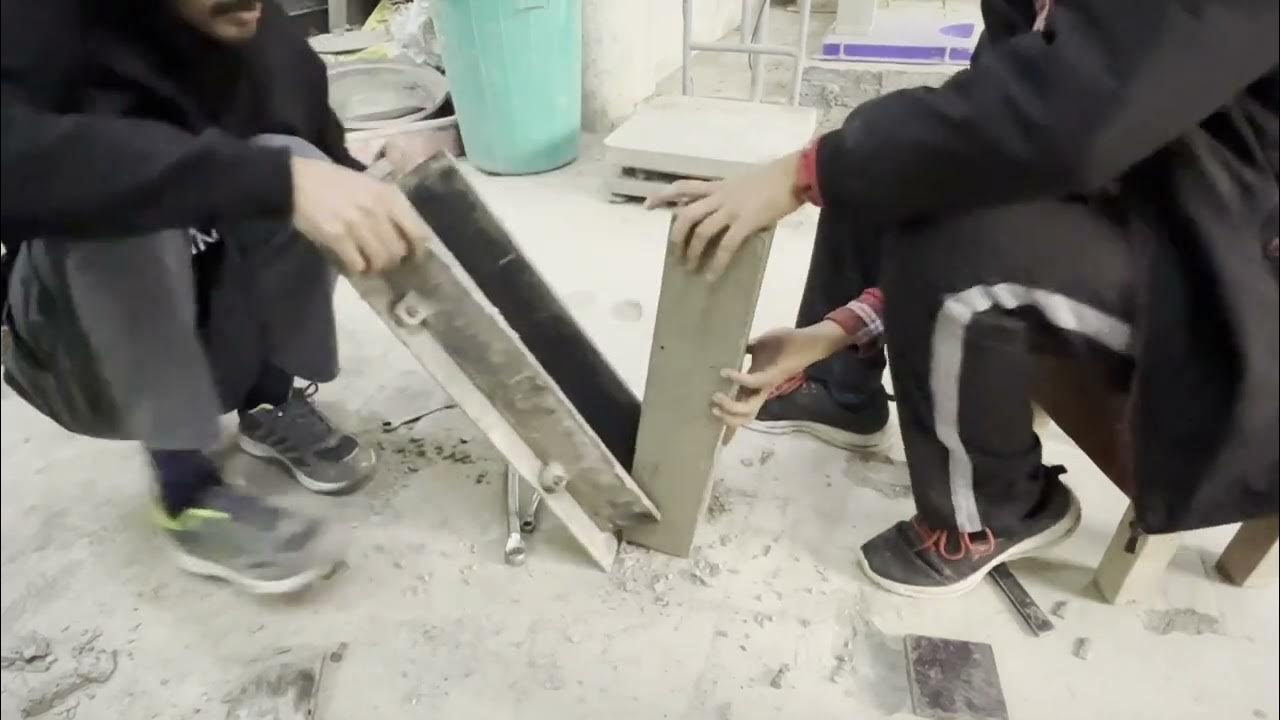
Expt 2. Flexural Strength Test of Concrete Beam
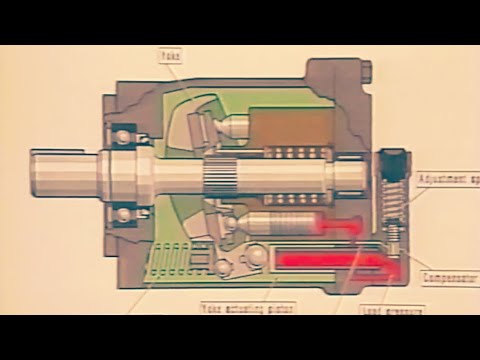
Hydraulic Training Series - Chapter 2 - Hydraulic Pumps
5.0 / 5 (0 votes)