BBC Engineering Craft Studies EP 9 Material Removal Principles
Summary
TLDRThis video script explores various cutting processes used in engineering, including turning, drilling, and milling. It highlights the significance of cutting tool geometry, such as rake and clearance angles, in achieving efficient cuts and smooth surface finishes. Through experiments, it demonstrates how changes in tool design affect chip formation and power consumption during cutting. The script emphasizes the importance of selecting appropriate tool angles for different materials, showcasing how optimal rake angles can minimize power usage while maintaining tool integrity. Overall, it provides valuable insights into the mechanics of machining and the critical role of cutting tools in engineering.
Takeaways
- 🔧 Turning involves rotating a workpiece against a cutting tool to create cylindrical surfaces.
- 🔩 Drilling is a process where a rotating cutting tool generates holes in a stationary workpiece.
- 🛠️ Milling uses a rotating cutter to remove material from a workpiece fed into it, generating flat surfaces.
- 📏 Shaping involves the cutting tool moving across a stationary workpiece to create flat surfaces.
- 🔍 High-Speed Steel (HSS) is a common material for cutting tools, while tungsten carbide offers greater durability for cutting edges.
- ⚙️ Cutting tools often share a wedge shape for efficiency, which aids in chip formation and cutting performance.
- 🛡️ The clearance angle on a tool helps prevent rubbing against the workpiece, improving cutting efficiency.
- 🔄 The rake angle affects chip formation and power consumption; larger angles lead to shorter shear planes and lower power usage.
- 📊 Experimental observations indicate that increasing the rake angle improves chip flow and reduces cutting power requirements.
- ⚖️ The ideal rake angle for cutting materials like mild steel is between 10° and 20°, optimizing both tool life and efficiency.
Q & A
What are the main cutting processes discussed in the transcript?
-The main cutting processes discussed are turning, drilling, milling, and shaping.
How does the turning process work?
-In turning, the workpiece rotates while the cutting tool remains stationary, allowing the tool to shape the material into cylindrical forms.
What is the role of the rake angle in cutting tools?
-The rake angle is the angle between the cutting edge and the face of the tool. It influences chip formation and the amount of power consumed during cutting.
Why is the shape of cutting edges similar across different tools?
-Cutting edges are often wedge-shaped to promote efficient cutting and chip flow, which helps in reducing friction and wear.
What is the significance of the clearance angle in tool design?
-The clearance angle prevents the tool from rubbing against the workpiece, which enhances cutting efficiency and prolongs tool life.
How does chip formation affect the cutting process?
-Efficient chip formation ensures that material flows naturally over the tool, minimizing friction and wear while producing a better surface finish.
What happens to the cutting tool when using an incorrect rake angle?
-Using an incorrect rake angle can lead to poor chip formation, increased power consumption, and accelerated tool wear.
What did the experiments reveal about power consumption related to rake angle?
-The experiments showed that a larger rake angle results in a shorter shear plane and less power consumption, indicating a more efficient cutting action.
What materials were discussed in relation to suitable rake angles?
-The transcript mentions mild steel, brass, aluminum, and nylon, suggesting that different materials may require different optimal rake angles.
How is the performance of a cutting tool evaluated based on its geometry?
-The performance of a cutting tool is evaluated by examining its rake and clearance angles, chip flow behavior, and the power required for cutting materials.
Outlines
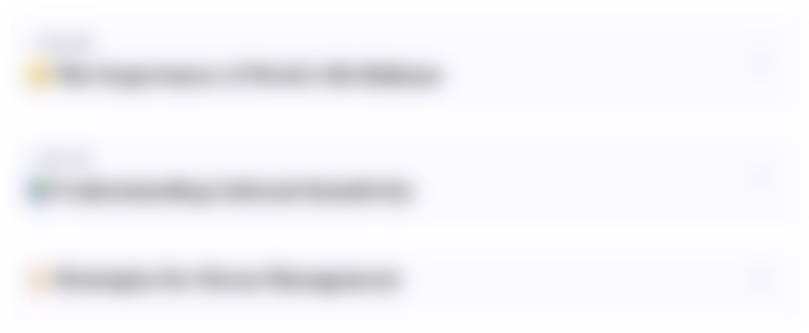
This section is available to paid users only. Please upgrade to access this part.
Upgrade NowMindmap
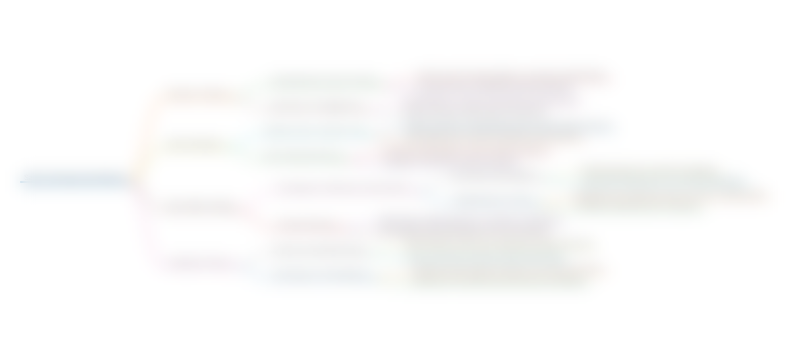
This section is available to paid users only. Please upgrade to access this part.
Upgrade NowKeywords
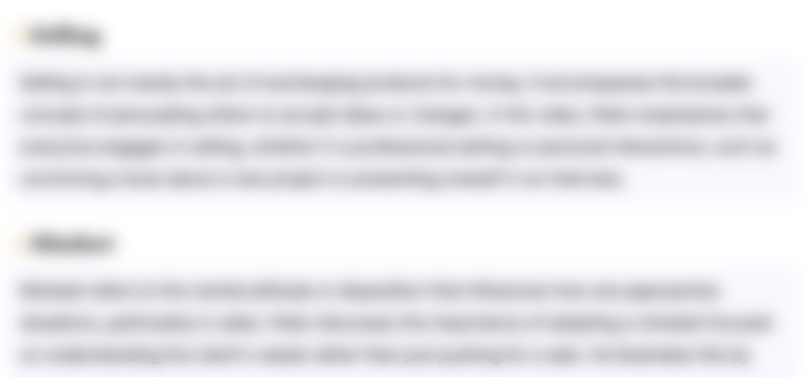
This section is available to paid users only. Please upgrade to access this part.
Upgrade NowHighlights
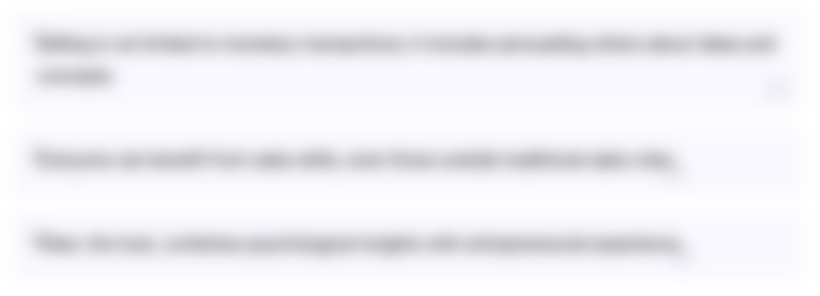
This section is available to paid users only. Please upgrade to access this part.
Upgrade NowTranscripts
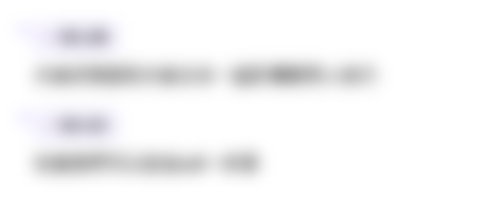
This section is available to paid users only. Please upgrade to access this part.
Upgrade NowBrowse More Related Video

All Lathe Machine Operations: Turning, Facing, Taper Turning, Boring, Knurling, Tapping, Forming
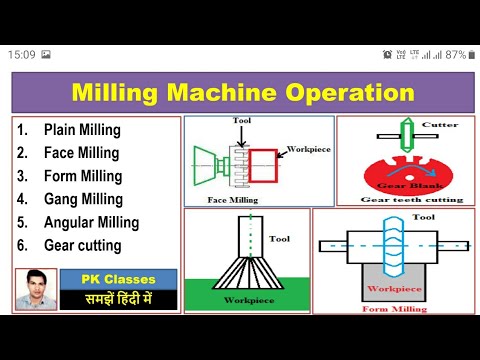
Milling Machine Operations (हिन्दी)
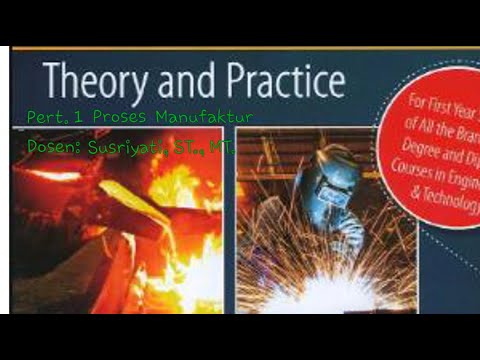
Pertemuan 1. Proses Manufaktur _ Pendahuluan

HEAVY DUTY LATHES. Most Mesmerizing Collection of CNC Machine Processes.
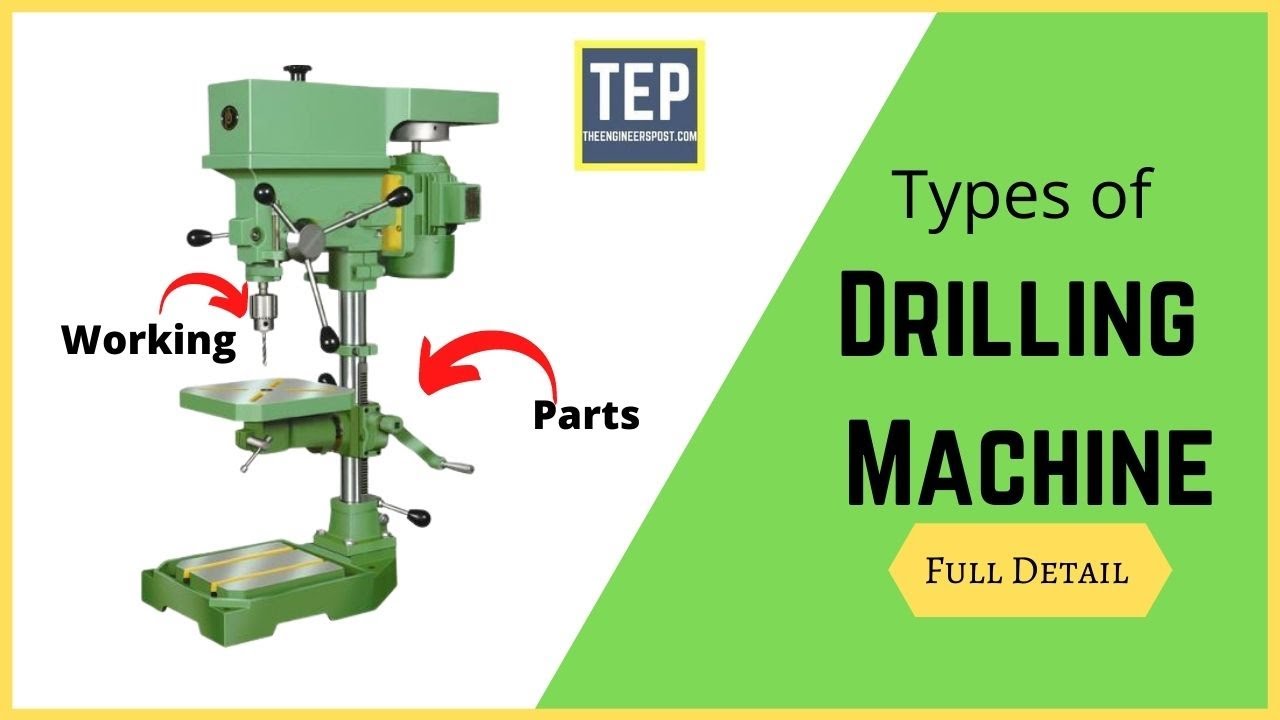
Drilling machine: Types, Parts, Operations, Working Principle, (Explained in detail)

Types of Drill jigs & Requirement of Drill jig ||Engineer's Academy||
5.0 / 5 (0 votes)