Boost Efficiency with Process Layouts in Manufacturing!
Summary
TLDRThis video highlights the critical role of factory layout in optimizing manufacturing efficiency. A well-designed layout streamlines material movement, machine placement, and worker interaction, akin to a well-organized kitchen. It discusses the advantages of process layouts, such as specialization, flexibility, and bottleneck reduction, while also addressing challenges like increased material handling costs and complex scheduling. Key design considerations include minimizing material flow, ensuring safety, and allowing scalability. The versatility of process layouts is illustrated through examples in manufacturing, healthcare, and restaurants, emphasizing their adaptability to meet unique industry needs.
Takeaways
- 🏭 A factory layout acts as a blueprint for operations, affecting material movement, machine placement, and worker interactions.
- ⚙️ Optimizing the factory layout can significantly enhance efficiency, reducing bottlenecks and improving overall productivity.
- 👨🍳 A well-designed layout is comparable to an organized kitchen, allowing seamless workflow and minimizing unnecessary movement.
- 📉 Process layouts group similar machines together, promoting specialization and increasing worker efficiency.
- 🔄 Flexibility is a key benefit of process layouts, allowing for easy adaptation to changes in product design or production volume.
- 🚧 Bottlenecks can be managed in process layouts by reallocating resources to slower operations.
- 💰 However, process layouts may lead to increased material handling costs due to longer transportation distances.
- 📦 Higher inventory levels can result from batch processing in process layouts, potentially tying up capital.
- 🗓️ Scheduling can be complex in process layouts, as multiple products may compete for the same resources.
- 🛠️ Factors to consider in process layout design include material flow, safety, flexibility, and scalability.
Q & A
What is the primary purpose of a factory's layout?
-A factory's layout serves as a blueprint for operations, dictating how materials move, where machines are placed, and how workers interact with their environment.
How does a well-designed factory layout impact production efficiency?
-A well-designed layout minimizes unnecessary movement and material handling costs, ensuring a smooth flow in the production process, which leads to faster production times, lower costs, and higher quality products.
What is a process layout, and what are its key features?
-A process layout, also known as a functional layout, groups similar machines or operations together, allowing for specialization of labor and equipment, flexibility in adapting to changes, and better management of bottlenecks.
What are some advantages of a process layout?
-Advantages of a process layout include specialization of labor and equipment, increased flexibility to adapt to changes, and improved ability to manage bottlenecks in production.
What are the disadvantages associated with process layouts?
-Disadvantages include increased material handling costs, potentially less efficient workflow compared to product layouts, higher inventory levels due to batch processing, and more complex scheduling due to competing product demands.
What factors should be considered when designing a process layout?
-Key factors include material flow to minimize travel distances, safety for workers, flexibility to adapt to changes, and scalability to allow for easy expansion or reconfiguration.
Can you provide examples of industries that utilize process layouts?
-Yes, industries that commonly use process layouts include manufacturing (e.g., machine shops), healthcare (e.g., hospitals), and service industries (e.g., restaurants).
How do process layouts contribute to the management of bottlenecks?
-In a process layout, bottlenecks can be addressed by reallocating resources or adding more machines or workers to the bottleneck operation, thereby improving overall workflow.
Why is optimizing factory layout considered a necessity in today's competitive landscape?
-Optimizing factory layout is essential for staying competitive, as companies that fail to do so risk falling behind competitors who utilize efficient layout designs to enhance productivity and reduce costs.
What is the role of safety in process layout design?
-Safety is crucial in process layout design; the layout should provide adequate space for workers to move safely and operate equipment without the risk of injury, ensuring a safe working environment.
Outlines
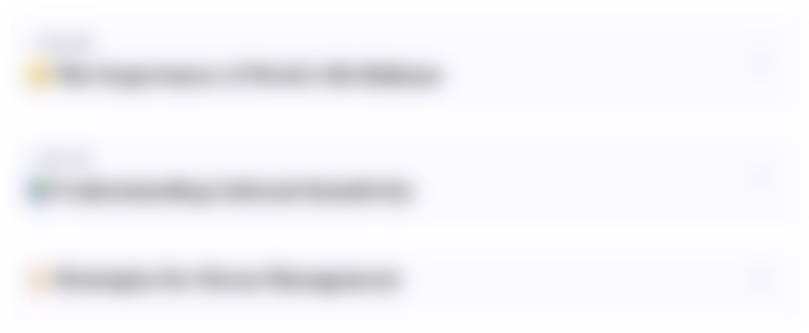
This section is available to paid users only. Please upgrade to access this part.
Upgrade NowMindmap
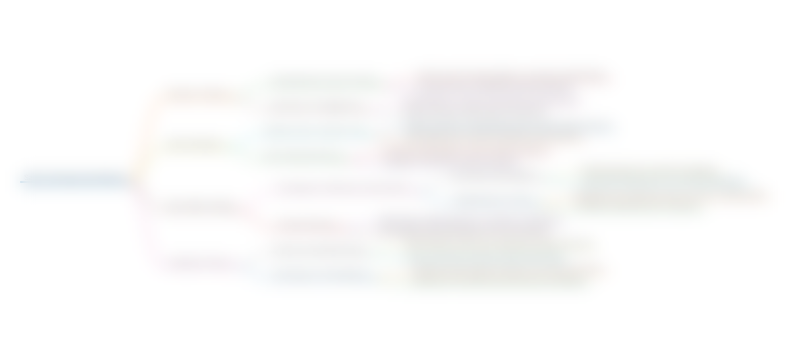
This section is available to paid users only. Please upgrade to access this part.
Upgrade NowKeywords
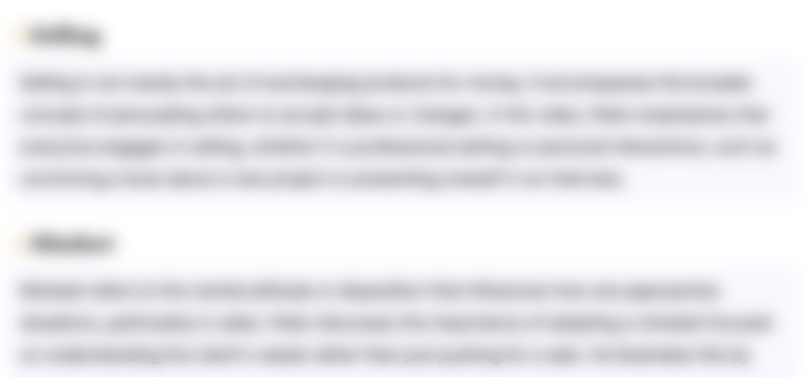
This section is available to paid users only. Please upgrade to access this part.
Upgrade NowHighlights
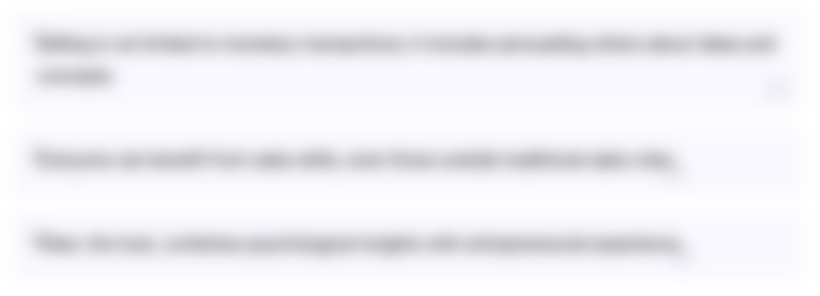
This section is available to paid users only. Please upgrade to access this part.
Upgrade NowTranscripts
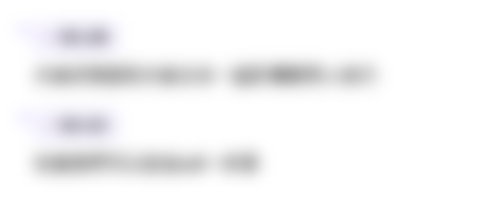
This section is available to paid users only. Please upgrade to access this part.
Upgrade Now5.0 / 5 (0 votes)