Unleashing the Power of Gen AI and XR at Pfizer
Summary
TLDRThe video script details Fizer's journey in integrating XR and AI technologies to revolutionize manufacturing. George Hanaras introduces the Smart Factory team's efforts to enhance efficiency and reduce human error by leveraging AR and AI. Nicholas Hawley discusses the development of XR training to virtualize the manufacturing shop floor, improving accessibility and retention. San Sharma highlights the technical stack and AI's role in content creation and spatial awareness. The team shares insights on strategic collaborations, user adoption, and the importance of data standardization for effective AI integration.
Takeaways
- 😀 George Hanaras from Fizer's Smart Factory team discussed leveraging XR and AI technologies to improve manufacturing efficiency and reduce human error.
- 🛠️ The team identified pain points in manufacturing, such as complex procedures and environments, the need for guidance for operators, and issues with siloed systems.
- 🤖 They explored AR as a solution, experimenting with various hardware and software options to create immersive experiences that could be deployed in a regulated environment.
- 🔧 The decision was made to opt for an in-house development model, utilizing the Unity 3D engine and forming agile teams to develop and deploy AR solutions.
- 🔗 Emphasis was placed on integrating systems and data to bring the right information to the right user at the right time, standardizing and democratizing data for immersive experiences.
- 📚 The Smart Factory team recognized the need for digitizing tacit knowledge and providing end-to-end visibility of processes and tasks for operators.
- 🏆 The team has won awards for their work and is now exploring the integration of AI with AR, using predictive models and large language models to enhance manufacturing operations.
- 🎓 Nicholas Hawley highlighted the use of XR for training, emphasizing the importance of extending the reality of manufacturing assets to people for better training outcomes.
- 🌐 The Fizer Verse platform was introduced as a centralized hub for training content, enabling multi-user experiences and real-time interaction with trainers in virtual environments.
- 🛑 The journey of implementing XR in training involved starting with research, building proof of concepts, and eventually bringing development in-house for cost efficiency and agility.
- 🔮 Looking forward, the team is exploring AI in XR for asset optimization, generative voice and avatars, and the potential for AI to improve the user experience in manufacturing.
Q & A
Who is George Hanaras and what is his role in the Smart Factory team?
-George Hanaras is a member of the Smart Factory team at Fizer's diesel manufacturing organization. He is involved in leveraging innovative technologies like XR (Extended Reality) and AI to support manufacturing plants and improve front-line efficiency.
What is the primary goal of the Smart Factory team in terms of technology implementation?
-The primary goal of the Smart Factory team is to utilize innovative technologies such as XR and AI to support manufacturing plants, reduce human error, and enhance front-line productivity.
What challenges did Fizer's manufacturing plants face that led them to explore AR technology?
-The challenges included complex procedures and environments, the need for operators to navigate multiple siloed systems for information, unpredicted issues without clear root causes or corrective actions, and a significant amount of tacit knowledge not being digitized.
How did the Smart Factory team approach the integration of AR technology in their operations?
-They started by researching the market, identifying AR as a potential solution, and experimenting with various hardware and software components. They focused on high-value use cases and received positive feedback from early adopters, leading to the establishment of an in-house development model.
What is the significance of Unity 3D engine in the Smart Factory team's development process?
-The Unity 3D engine is at the center of their internal delivery pipeline, allowing the team to quickly develop prototypes and deploy AR solutions in a compliant manner.
How does the Smart Factory team ensure that the AR solutions are aligned with business requirements?
-They have formed internal agile teams consisting of 3D designers, artists, and developers who can convert business requirements into end-to-end AR experiences and deploy them compliantly.
What is the role of AI in the Smart Factory team's current initiatives?
-AI is used to train predictive models to find correlations in historical manufacturing data, allowing for instant notifications of deviations during new production runs. Additionally, AI is used to generate targeted action points and convert textual output into AR experiences.
What is the purpose of the 'connected worker interfaces' developed by the Smart Factory team?
-The connected worker interfaces aim to bring multiple systems together in a single pane of glass, enabling end-to-end visibility of processes and the visibility of the next critical task for the user, enhancing efficiency and reducing the need for manual data navigation.
How does the Smart Factory team address the issue of wearables not being mature enough for full shift adoption?
-They decided to use mobile devices with tablets, specifically, mounted on trolleys or movable carts, allowing operators to perform complex tasks hands-free when needed while still benefiting from the AR element.
What is the vision of Fizer for the convergence of XR and AI in the future of manufacturing?
-Fizer envisions XR to be the interface for AI on the shop floor, collecting data from various software processes into a single data channel, which then feeds into an AI system to make data smarter and more adaptive, aiding operators in making better decisions.
What are some of the technical considerations for deploying AR and VR applications in manufacturing as discussed by San Sharma?
-The technical considerations include content creation from CAD drawings and 360° scans, spatial awareness setup using image tracking or plane detection, development platforms like Unity and xcode, SDK APIs like AR kit and VR interaction toolkit, and networking libraries for multiplayer experiences. Additionally, there is a focus on data integration from IoT sensors and the use of XR content management systems for asset distribution and access.
Outlines
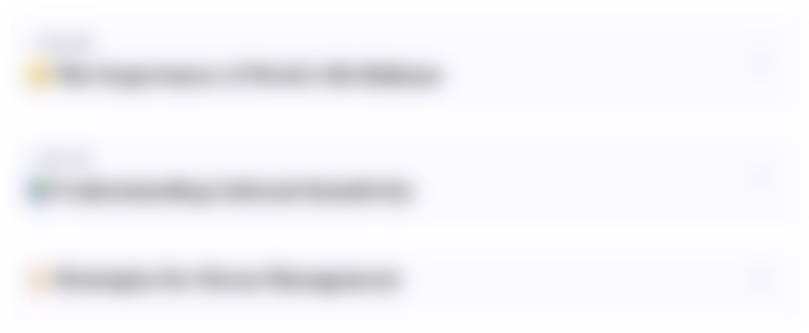
This section is available to paid users only. Please upgrade to access this part.
Upgrade NowMindmap
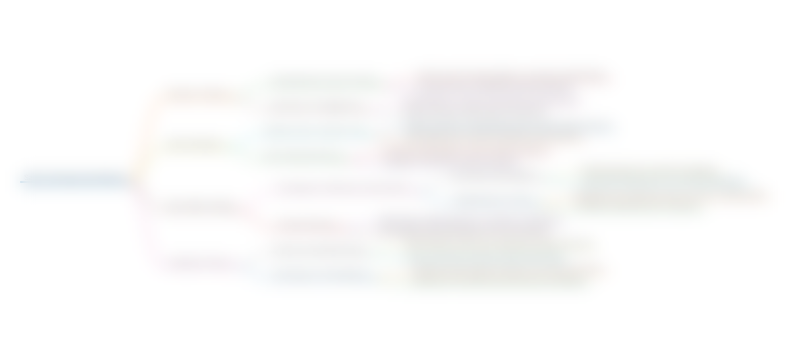
This section is available to paid users only. Please upgrade to access this part.
Upgrade NowKeywords
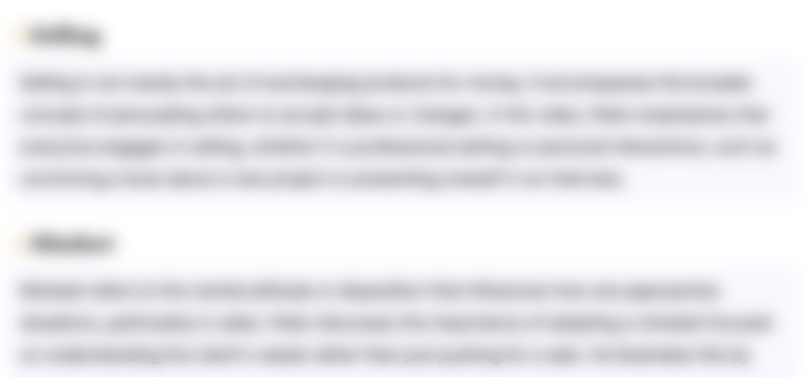
This section is available to paid users only. Please upgrade to access this part.
Upgrade NowHighlights
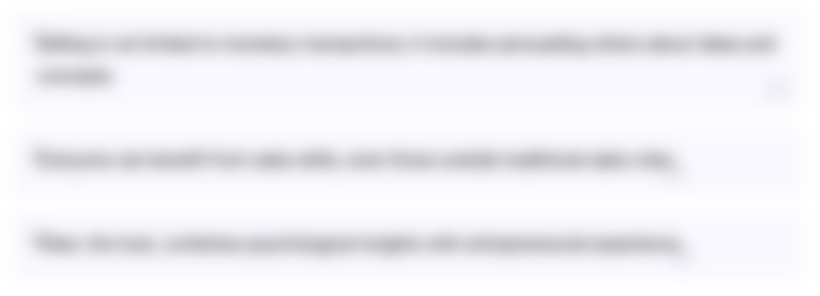
This section is available to paid users only. Please upgrade to access this part.
Upgrade NowTranscripts
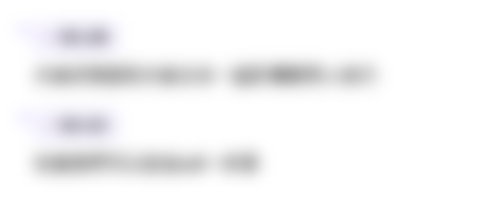
This section is available to paid users only. Please upgrade to access this part.
Upgrade NowBrowse More Related Video
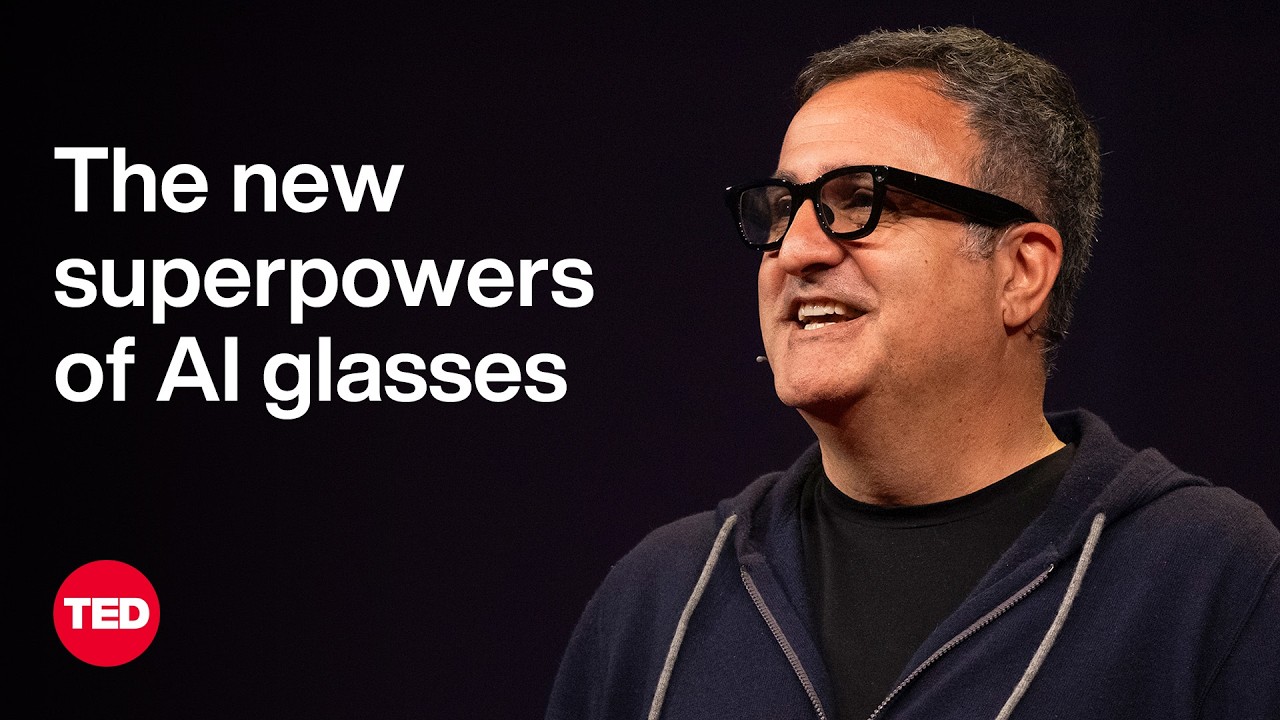
The Next Computer? Your Glasses | Shahram Izadi | TED

An explorer of extended reality in medtech
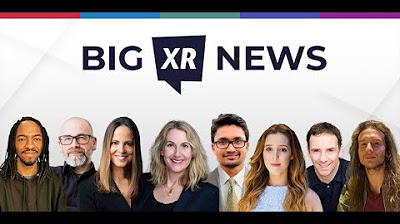
The Latest Big XR News: Recap on Highlights from 2023
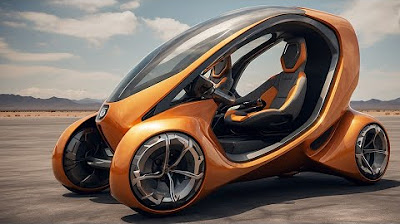
20 EMERGING TECHNOLOGIES THAT Will Change Our World | Upcoming Life Changing Technology 2050

Doctolib : Déployer une Stratégie IA Générative 🚀🤖 (#127)

Why AI and IOT Will Transform Both the Internet and the Global Economy | AI + IoT = AIoT
5.0 / 5 (0 votes)