💡 How We Make Composite Hockey Sticks | TRUE TEMPER HOCKEY
Summary
TLDRThe video script discusses the process of co-molding a one-piece hockey stick, where the shaft and blade are compression molded together. This method ensures no defects are hidden inside, unlike bladder molding. The challenge lies in the high-pressure process that requires precise control to avoid visible defects on the shaft. The transparency of defects in co-molding is a double-edged sword, ensuring quality but demanding perfection.
Takeaways
- 🛠️ The process described is a co-molding technique used to create a one-piece sports equipment, specifically a hockey stick.
- 🎯 The shaft laminates extend through the entire blade, ensuring a strong and unified connection.
- 🔄 The blade is laid up directly on the shaft and then co-molded together with it.
- 🔩 The shape of the mandrel and the laminate design are crucial in defining the final shape and dimensions of the shaft.
- 🚫 The process requires high pressure and precision as any defects will be visible on the outside of the shaft.
- 🔍 The manufacturing process is tightly controlled to avoid defects that could lead to scrap products.
- 🆚 Compared to bladder molding, the co-molding process is less forgiving as defects are not hidden inside the shaft.
- 🚫 In bladder molding, defects can be internal and not visible, potentially leading to failures in use.
- 🏭 The bladder molding process is described as more manufacturing-friendly due to its ability to hide defects.
- ⚙️ The challenge of the co-molding process is also its strength, as it forces the manufacturer to maintain high quality standards.
Q & A
What is the process of co-molding a shaft with the blade?
-The process involves compression molding the shaft with the blade, where the shaft laminates extend all the way through the heel of the blade. The blade is laid up directly on the shaft and co-molded together to create a one-piece stick.
How does the mandrel shape and laminate design affect the final product?
-The shape of the mandrel and the laminate design are crucial as they define the final shape and dimensions of the shaft. The material is wrapped around the mandrel and undergoes a high-pressure process.
What challenges does the co-molding process present?
-One of the challenges is the high-pressure process where no materials are moved during cure. Any defects will be visible on the outside of the shaft, necessitating tight process control.
How does the visibility of defects in the co-molding process benefit the manufacturer?
-The visibility of defects ensures that the process must be perfect, as any defect will result in a scrap stick. This contrasts with bladder molding where defects can be hidden inside the shaft.
What is the difference between co-molding and bladder molding in terms of defect visibility?
-In co-molding, defects are visible on the outside of the shaft, whereas in bladder molding, defects are internal and not visible, potentially leading to unseen failures in the field.
Why is the co-molding process described as more manufacturing-friendly in comparison to bladder molding?
-The co-molding process is more manufacturing-friendly because it allows for immediate identification of defects, preventing the production and shipment of faulty products.
What is the potential consequence of an internal defect in a bladder-molded shaft?
-An internal defect in a bladder-molded shaft may not be visible but could lead to failure in the field, affecting the product's durability and reliability.
How does the high-pressure process ensure the quality of the co-molded shaft?
-The high-pressure process ensures quality by preventing any movement of materials during the curing phase, which would otherwise result in visible defects on the shaft's exterior.
What role does the laminate design play in the overall strength and performance of the one-piece stick?
-The laminate design is integral to the strength and performance of the one-piece stick, as it determines the structural integrity and the way forces are distributed throughout the shaft and blade.
How does the co-molding process affect the final product's durability?
-The co-molding process, due to its high-pressure nature and the need for tight process control, results in a more durable product with fewer defects that could lead to failure.
What is the significance of the music mentioned in the transcript?
-The mention of music in the transcript likely indicates that the video includes background music or sound effects to enhance the viewer's experience or to emphasize certain points in the process being described.
Outlines
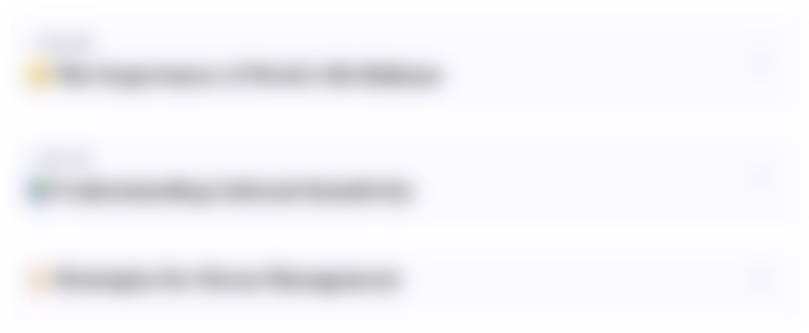
This section is available to paid users only. Please upgrade to access this part.
Upgrade NowMindmap
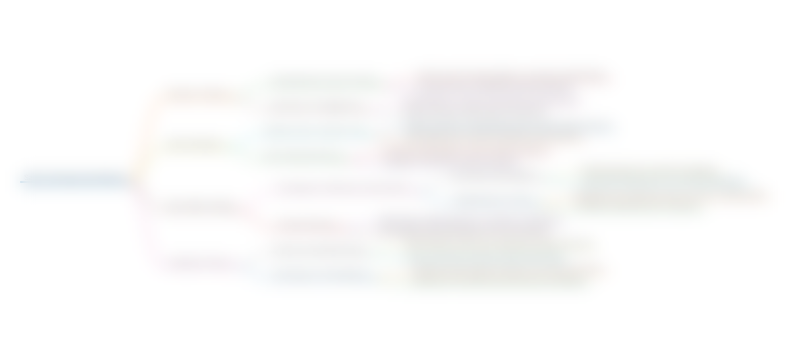
This section is available to paid users only. Please upgrade to access this part.
Upgrade NowKeywords
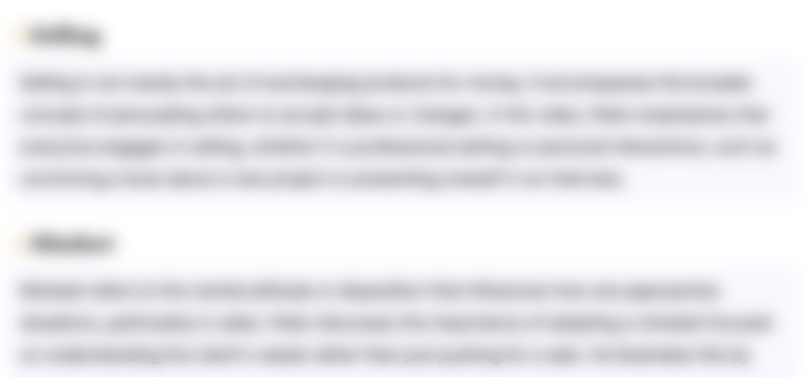
This section is available to paid users only. Please upgrade to access this part.
Upgrade NowHighlights
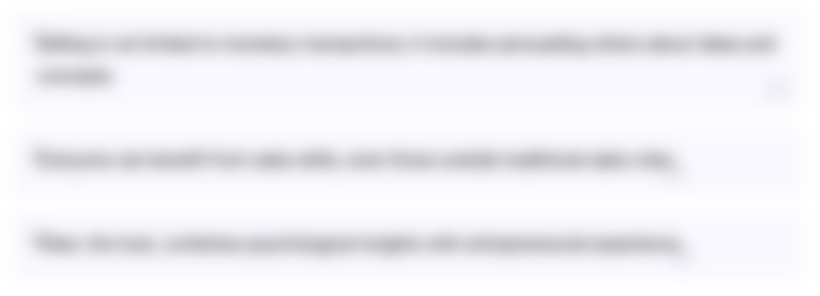
This section is available to paid users only. Please upgrade to access this part.
Upgrade NowTranscripts
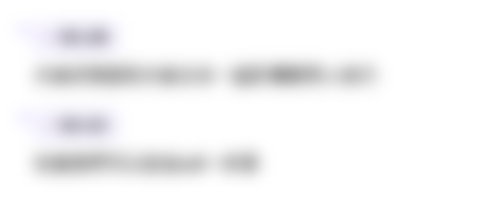
This section is available to paid users only. Please upgrade to access this part.
Upgrade Now5.0 / 5 (0 votes)