Processo de Fabricação do Alicate
Summary
TLDRThe script outlines the manufacturing process of a wrench, starting with the heating and cutting of a metal billet. It then describes hot compression molding to shape the wrench, followed by secondary hot compression and cooling. Chemical and thermal treatments are applied to relieve stress and harden the steel. The wrench undergoes abrasive polishing to refine its edges. Cold compression ensures the wrench's shape, and drilling creates holes for assembly. Broaching is used to form teeth and remove burrs. Finally, the wrench is tempered to enhance hardness and durability, and a finishing process smooths the surface, completing the wrench's production.
Takeaways
- 🔨 The manufacturing process of a wrench begins with the heating of a steel billet in a linear motion furnace.
- ♨️ The billet is then subjected to hot compression to shape it, followed by a second hot compression to refine its form.
- 🔩 The wrench undergoes symmetrical shaping to ensure it can fit onto bolts properly.
- 🔥 A chemical and thermal treatment is applied to relieve stresses and harden the steel, involving a closed furnace to maintain even temperature throughout the piece.
- 🛠 The wrench is polished using an abrasive material, specifically tumbling, which uses rotating abrasive chips to smooth and round the edges.
- ⚙️ Cold compression is applied to ensure the wrench's shape and dimensions are precise.
- 🗝️ Drilling processes are used to create holes in the wrench, such as the pass-through hole for the handle.
- 🔩 Broaching is mentioned for creating the teeth or grooves on the wrench's head, which is done through rotational and linear movement.
- 🔧 Milling is used to remove burrs and refine the wrench's teeth, ensuring a smooth and functional grip.
- 🔩 The final assembly involves securing the wrench with a pin and a screw, using machines that rotate and tighten the screw into the wrench's hole.
- ⚒️ The wrench is then tempered to increase its hardness and resistance, involving heating for austenitization, rapid cooling for martensitic structure, and final grinding for a smooth finish.
Q & A
What is the initial material used for manufacturing the pliers?
-The initial material used for manufacturing the pliers is a billet, which is a solid piece of metal.
What is the purpose of the linear movement in the initial stage of the process?
-The linear movement is used to cut the billet into equal lengths, ensuring uniformity for the subsequent manufacturing steps.
How are the cut billet pieces heated in the manufacturing process?
-The cut billet pieces are heated in a machine called a hot compression machine, which shapes them into the desired form.
What happens during the second hot compression process?
-During the second hot compression, the heated billet receives another function, which further refines its shape to resemble one side of the pliers.
Why are the pliers symmetrical after the hot compression processes?
-The pliers are symmetrical because the hot compression processes are designed to create a mirror image on both sides, ensuring that each half of the pliers is identical.
What is the purpose of the chemical and thermal treatment in the pliers manufacturing process?
-The chemical and thermal treatment is used to relieve stresses in the steel and to attract refractory materials, ensuring uniform temperature distribution across the piece.
How does the tumbling process contribute to the finishing of the pliers?
-The tumbling process uses abrasive materials to round off the corners and polish the pliers. The piece rotates in constant movement, and the abrasive chips polish the pliers.
What is the purpose of the cold compression after the tumbling process?
-The cold compression is used to ensure the final shape and size of the pliers, with the upper part of the machine pressing down on the piece to guarantee the form.
How is the hole for the pivot created in the pliers?
-The hole for the pivot is created using a drilling process, where the pliers are held in place and a drill bit removes the material to form the hole.
What is the function of the broaching process in the manufacturing of pliers?
-The broaching process is used to create the serrated edges or teeth on the jaws of the pliers. It involves a tool with teeth that move rotationally and linearly, cutting into the pliers to form the serrations.
What is the final process that the pliers undergo before they are considered complete?
-The final process the pliers undergo is tempering, which increases the hardness and resistance of the piece. This involves heating to organize the metal crystals (austenitization), followed by rapid cooling to achieve a martensitic structure, and finally, a process called burnishing to produce smooth surfaces.
Outlines
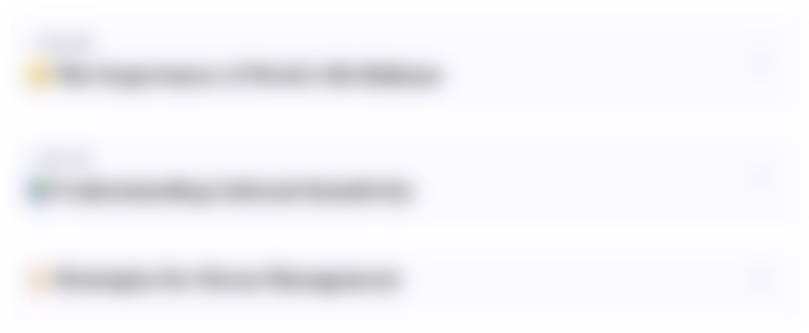
This section is available to paid users only. Please upgrade to access this part.
Upgrade NowMindmap
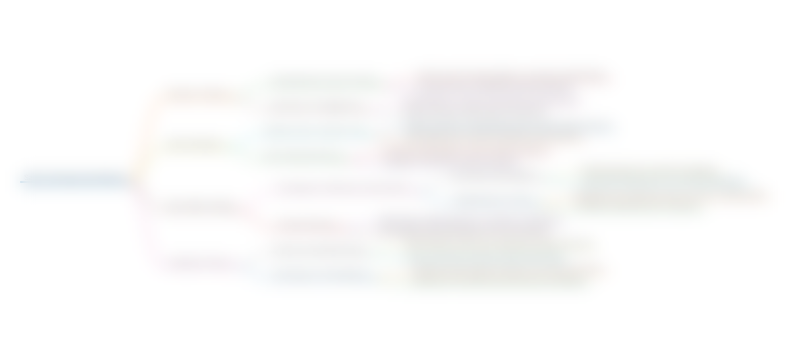
This section is available to paid users only. Please upgrade to access this part.
Upgrade NowKeywords
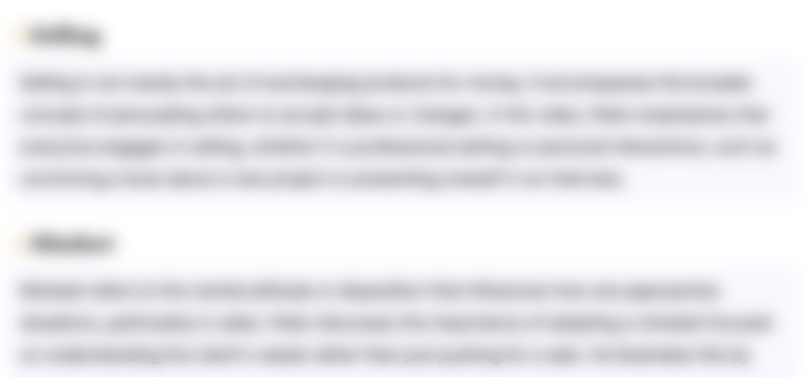
This section is available to paid users only. Please upgrade to access this part.
Upgrade NowHighlights
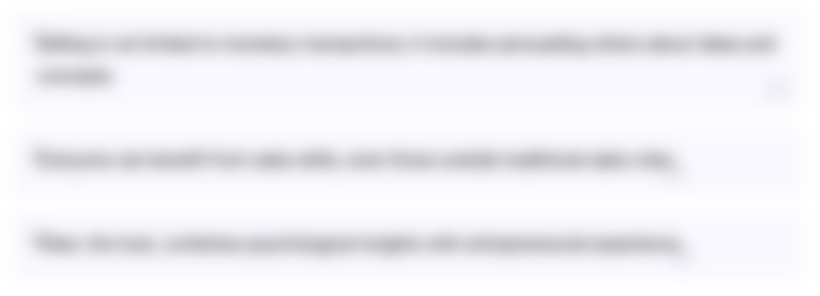
This section is available to paid users only. Please upgrade to access this part.
Upgrade NowTranscripts
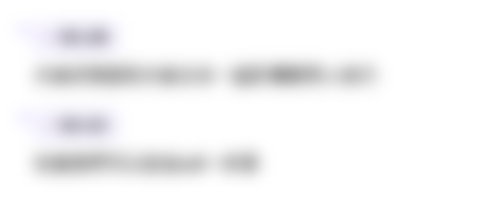
This section is available to paid users only. Please upgrade to access this part.
Upgrade Now5.0 / 5 (0 votes)