What is Total Quality Management - TQM
Summary
TLDRTotal Quality Management (TQM) is an organizational approach focused on long-term success through customer satisfaction, continuous improvement, and employee involvement. Rooted in 1920s statistical quality control, TQM has evolved into principles like customer focus, process-centric management, and fact-based decision-making. It promotes cross-functional collaboration, data-driven problem solving, and process improvement to enhance quality and build a customer-focused culture. TQM's ultimate goal is delivering consistent value to customers by improving every aspect of the business, from products to processes, while fostering a blame-free, quality-driven environment across the organization.
Takeaways
- ๐ TQM stands for Total Quality Management, an approach used by organizations to achieve long-term success by focusing on quality goods and services.
- ๐ TQM's roots date back to the 1920s with Walter Shewhart's statistical methods, further developed by W. Edwards Deming in post-WWII Japan.
- ๐ฟ TQM principles have influenced modern methodologies such as Lean, Operational Excellence, Agile, ISO, and Six Sigma.
- ๐ก The core of TQM is built on eight principles: customer focus, employee involvement, process-centered approach, systems integration, strategic planning, fact-based decision-making, effective communication, and continuous improvement.
- ๐ TQM emphasizes a customer-centric approach, where customer feedback is crucial for developing and enhancing products and services.
- ๐ ๏ธ A key belief in TQM is that system and process failures, not people, lead to poor quality outcomes, hence the focus on process improvement.
- ๐ TQM is data-driven, relying on statistical process control and fact-based decision-making for quality management and improvement.
- ๐ The Plan-Do-Check-Act (PDCA) cycle and seven quality control tools are integral to TQM's continuous improvement practices.
- ๐ฅ Total involvement is a cornerstone of TQM, requiring participation from all levels of the organization to drive quality improvement.
- ๐ง TQM is not just a set of practices but also a strategic approach that integrates with the business strategy and involves change management and clear communication.
Q & A
What is Total Quality Management (TQM)?
-Total Quality Management (TQM) is an approach used by organizations to achieve long-term success by developing people and processes that can deliver the highest level of quality goods and services to customers.
What is the historical background of TQM?
-TQM has roots dating back to the 1920s when Walter Shewhart applied statistics to quality control in industrial processes. His student, W. Edwards Deming, further developed these ideas in post-World War II Japan in the late 1940s and 1950s.
What are the eight principles of TQM?
-The eight principles of TQM are: customer focus, employee involvement, being process-centered, integrating systems across the extended enterprise, strategic approach, fact-based decision-making, effective communication, and continuous improvement.
How does TQM contribute to productivity improvement?
-TQM contributes to productivity improvement by preventing errors and problems, faster problem-solving, improved supplier relationships, reducing total costs of quality, and recognizing and reducing risk.
What is the significance of customer focus in TQM?
-Customer focus in TQM is significant because it believes that an organization's success is based on delivering quality products, services, or experiences to the customer. TQM aims to not only meet but also exceed customer quality requirements using feedback for continuous improvement.
How does TQM view the role of systems and processes in quality outcomes?
-TQM believes that when there is a poor quality outcome, it is the systems and processes, not the people, that are at fault. Therefore, the focus is on building and improving processes that anyone can perform to provide value to the customer repeatedly and reliably.
What is the process-centric principle of TQM?
-The process-centric principle of TQM involves defining how work is done, identifying what it takes to deliver good quality, and maintaining standards. It also encourages everyone to pay attention to how work is done and continuously look for ways to make it easier, better, and faster.
How does TQM use data and analytics?
-TQM is a scientific approach to management that relies on data for tracking business performance, collecting customer feedback, and experimentation. Good decision-making in TQM is based on using facts and data to understand the situation rather than relying on feelings and opinions.
What is the role of management in TQM?
-Management plays a direct role in TQM activities through cross-functional improvement efforts and by creating an environment that supports engagement at all levels. They are responsible for providing training, encouraging improvement ideas, and leading by example with fact-based decision-making.
How does TQM integrate with the overall business strategy?
-TQM must be used to achieve the business strategy, with objectives tied to the overall strategy. A common practice for a strategic approach is hoshin planning or strategy deployment, which breaks down larger objectives into smaller ones at each organizational level, integrating and aligning efforts.
What does the term 'total' in TQM signify?
-In TQM, the term 'total' signifies three meanings: total involvement, where continuous improvement and quality management are part of every person's job; a focus on quality improvement across all parts of the enterprise; and total commitment from leadership to quality, which includes setting goals, providing training, and improving their own management processes.
Outlines
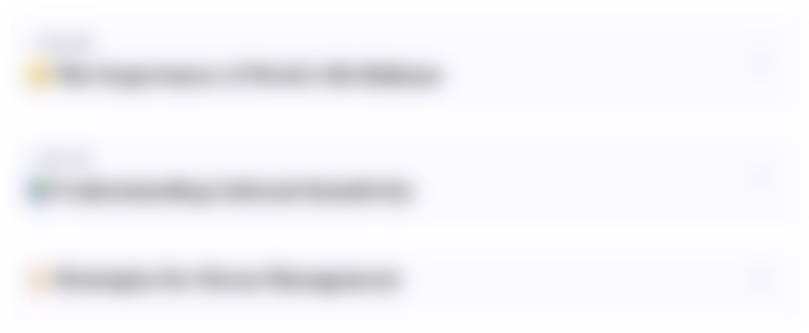
This section is available to paid users only. Please upgrade to access this part.
Upgrade NowMindmap
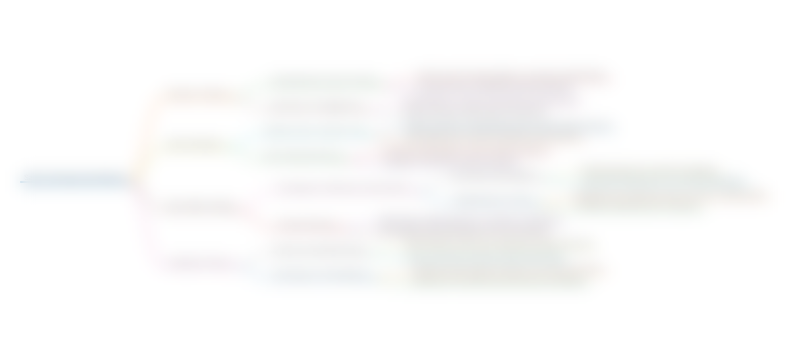
This section is available to paid users only. Please upgrade to access this part.
Upgrade NowKeywords
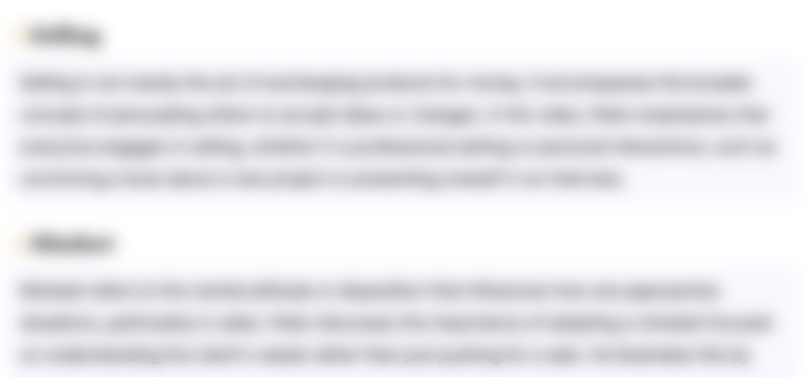
This section is available to paid users only. Please upgrade to access this part.
Upgrade NowHighlights
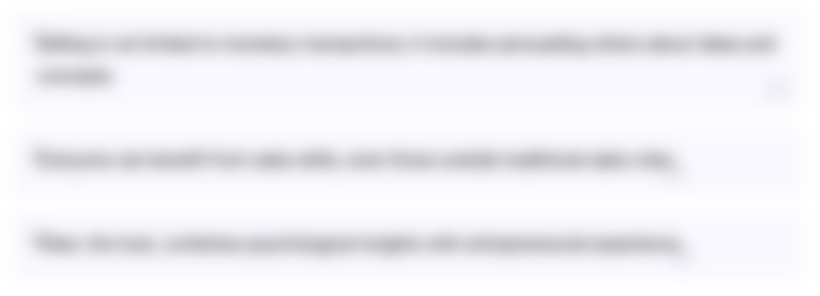
This section is available to paid users only. Please upgrade to access this part.
Upgrade NowTranscripts
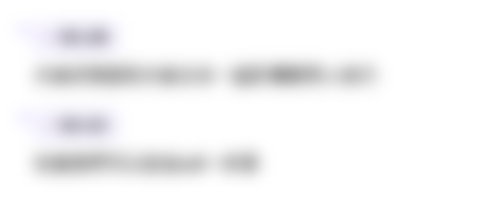
This section is available to paid users only. Please upgrade to access this part.
Upgrade NowBrowse More Related Video

tugas
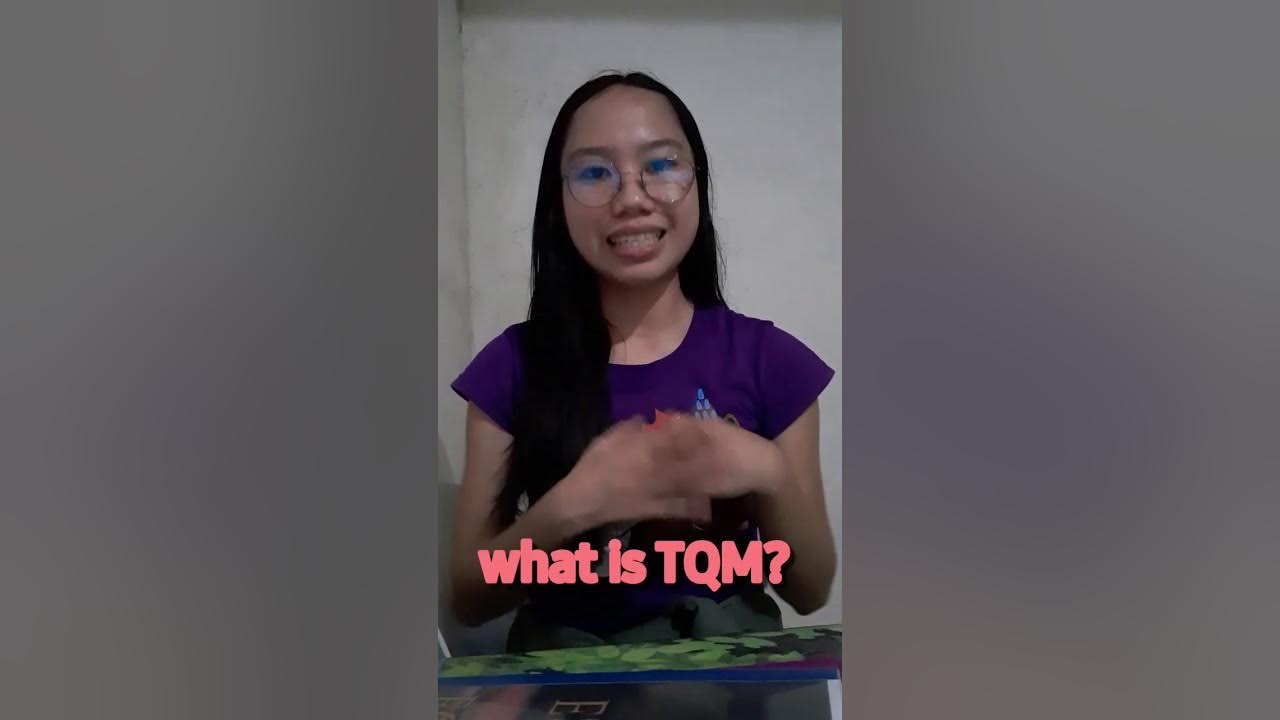
what is TQM? and the importance of TQM? Answered !

What is Total Quality management (TQM)? | 7 Principles of Total Quality Management
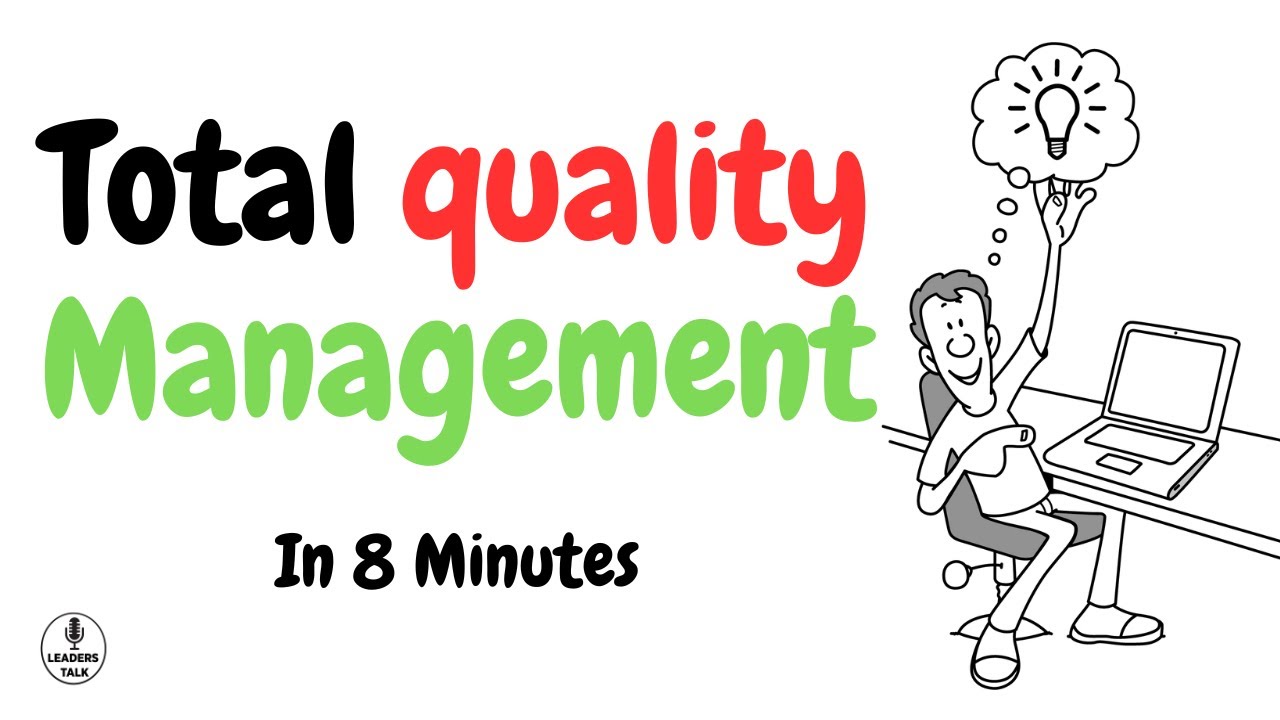
Total Quality Management Principles: A Comprehensive Overview

Penerapan Total Quality Manajemen (TQM) di PT Unilever Indonesia
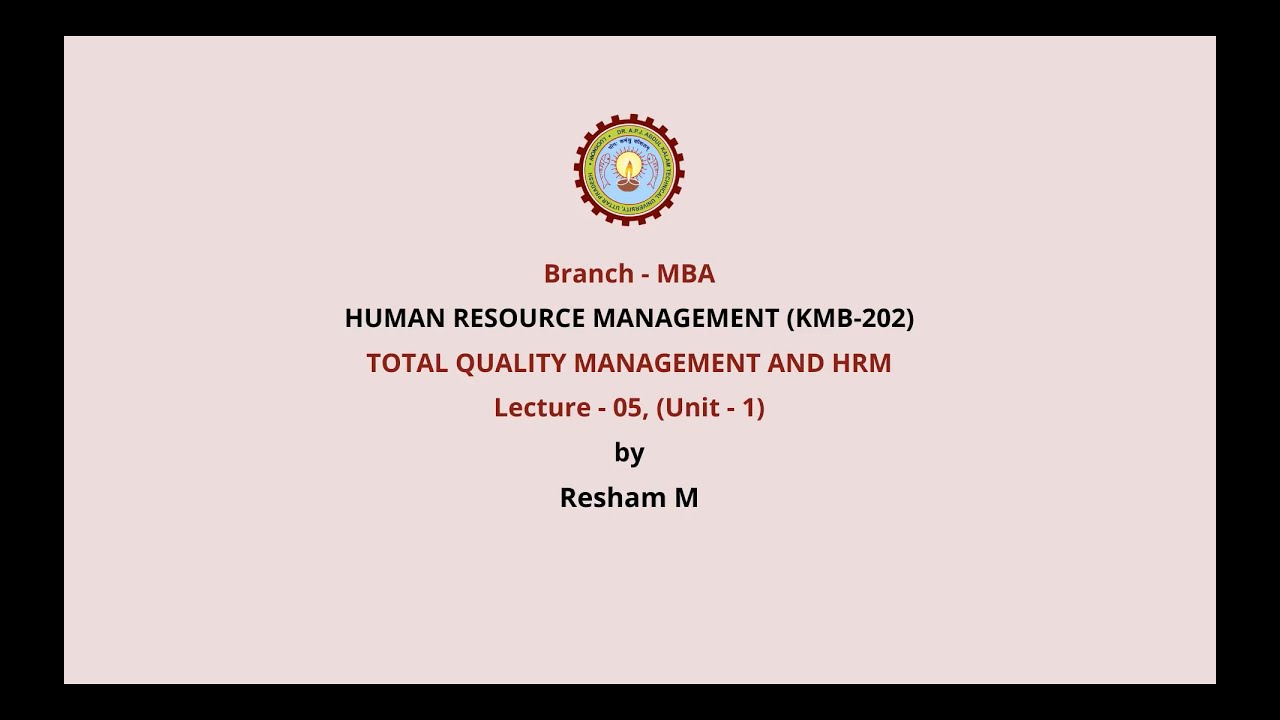
Human Resource Management | Total Quality Management and HRM | AKTU Digital Education
5.0 / 5 (0 votes)