Lezione 4B - CREAZIONE VSM - Parte 2 di 4 - Lean Thinking e Toyota Producition System - Zero sprechi
Summary
TLDRThe transcript discusses key performance indicators in business operations, focusing on production efficiency and waste reduction. It explains concepts like cycle time, changeover time, and lead time, emphasizing their importance in streamlining processes. The speaker uses examples to illustrate how to calculate productivity, efficiency, and quality, highlighting the significance of reducing work in progress and improving equipment utilization. The goal is to achieve a lean and efficient business operation.
Takeaways
- 😀 The script discusses key indicators for creating a streamlined process, avoiding waste, and measuring business performance.
- 🕒 It emphasizes the importance of 'takt time', a concept derived from German, which is the pace at which a product should be produced to meet customer demand.
- ⏱️ The script explains how to calculate 'takt time' using the formula: available working time divided by the demand for products.
- 🏭 It provides an example of a computer company's production process, illustrating how to determine the time required to produce one unit of a product.
- 📈 The concept of 'process time' is introduced, which is the time a piece takes to be produced from start to finish in a machine or process.
- 🔄 The script discusses 'changeover time' (also known as 'setup time'), which is the time it takes to switch a process from producing one product to another.
- 📊 'First Time Yield' and 'Roll Yield' are explained as indicators of production quality, showing the percentage of conforming products out of the total produced.
- 📋 The 'accuracy rate' of documents is mentioned as a measure of how complete and accurate a document is compared to what it should be.
- 🔢 The 'Full-Time Equivalent' (FTE) is introduced as a measure of the number of workers needed to meet production demands, calculated by dividing the total cycle time by the time per operation.
- 📉 The script highlights the significance of reducing 'work in progress' (WIP), which are the items in storage between machines, to decrease lead time and improve efficiency.
- 📊 The 'Overall Equipment Effectiveness' (OEE) is discussed as a measure of a machine's operational efficiency, calculated by multiplying availability, performance, and quality.
Q & A
What is the significance of the baton gesture in conducting a streamlined operation?
-The baton gesture, derived from the German term for a conductor's baton, symbolizes the rhythm and pace set by a metronome, which is crucial in measuring the performance of a business operation, particularly in terms of production output within a given time frame.
How is the daily production demand calculated in the example provided?
-In the example, a company is required to produce 180 PCs per week, working five days a week from 8:30 AM to 4:30 PM with a 30-minute lunch break. The available time is calculated by subtracting the break time from the total hours worked, resulting in 2200 minutes per week, and then dividing this by the production demand to find the time needed per PC.
What does the term 'cycle time' refer to in the context of production?
-Cycle time refers to the time it takes to produce one unit of a product from start to finish in a production process. It includes all the time a piece spends being processed, waiting, or being transported between different stages of production.
What is the difference between 'setup time' and 'lead time' in production?
-Setup time is the time required to prepare a machine or process for a new production run, including changing tools or materials. Lead time, on the other hand, is the total time it takes from when raw materials are ready to be transformed until the finished product is ready for the next stage or delivery.
How is the 'first time yield' calculated and what does it indicate?
-First time yield is calculated by dividing the number of conforming pieces produced by the total number of pieces produced. It indicates the efficiency of the production process in terms of producing quality products on the first attempt without needing rework or scrap.
What is the purpose of using 'process mapping' in a business?
-Process mapping is used to visually represent the steps in a process, identify inefficiencies or bottlenecks, and find ways to improve the process. It can be applied in both manufacturing and service industries to streamline operations and reduce waste.
How is the 'full-time equivalent' (FTE) calculated in a production process?
-The full-time equivalent is calculated by dividing the total cycle time of all operations by the cycle time per operator. This gives an indication of the number of operators needed to meet the production demand, considering the time each operator spends on each task.
What does the term 'work in progress' (WIP) refer to and why is it important?
-Work in progress refers to the items or materials that are in the process of being produced but are not yet complete. It is important because managing WIP effectively can significantly impact lead times and overall production efficiency.
How is the 'Overall Equipment Effectiveness' (OEE) calculated and what does it measure?
-OEE is calculated by multiplying the availability, performance, and quality percentages of a production process. It measures how effectively a production asset is utilized, considering downtime, production speed, and product quality.
What is the significance of reducing 'work in progress' (WIP) in a production process?
-Reducing WIP can lead to a significant decrease in lead times and improve the responsiveness of a production system. By minimizing the inventory between production steps, the system can become more agile and efficient, leading to faster delivery times and reduced waste.
How can the script's discussion on production metrics help a business improve its operations?
-The script provides a comprehensive overview of key production metrics that can be used to assess and improve operational efficiency. By understanding and applying these metrics, businesses can identify areas for improvement, reduce waste, and optimize their production processes.
Outlines
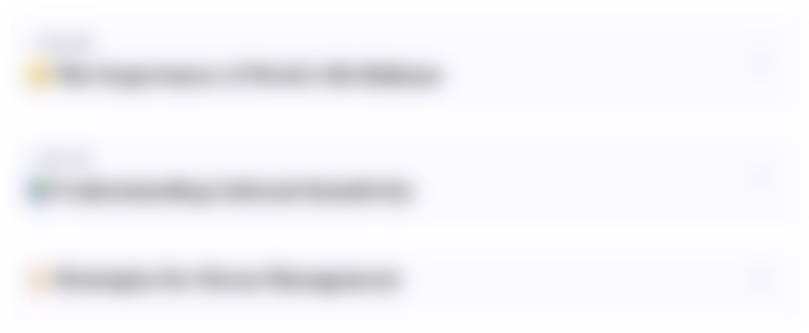
This section is available to paid users only. Please upgrade to access this part.
Upgrade NowMindmap
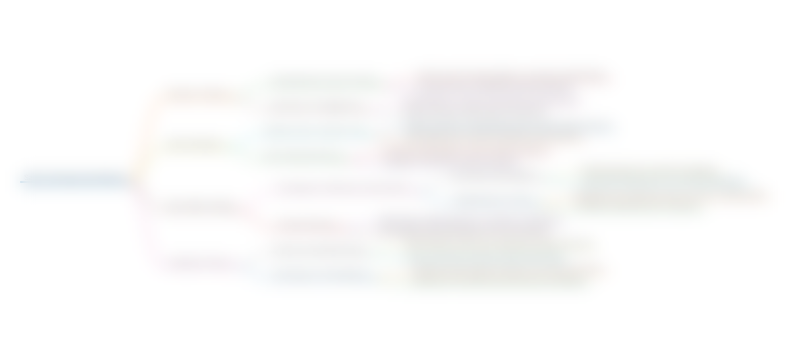
This section is available to paid users only. Please upgrade to access this part.
Upgrade NowKeywords
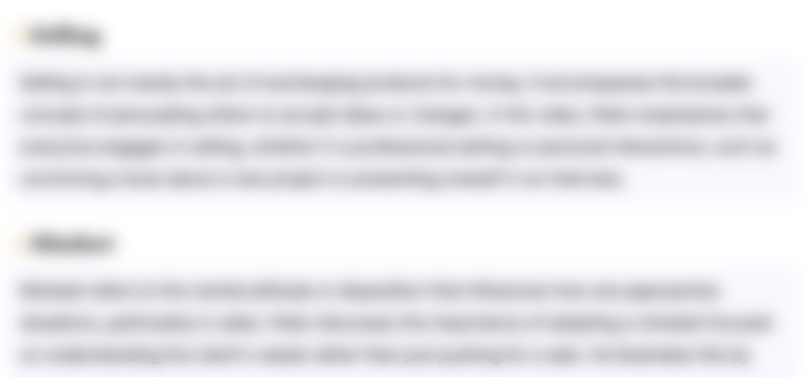
This section is available to paid users only. Please upgrade to access this part.
Upgrade NowHighlights
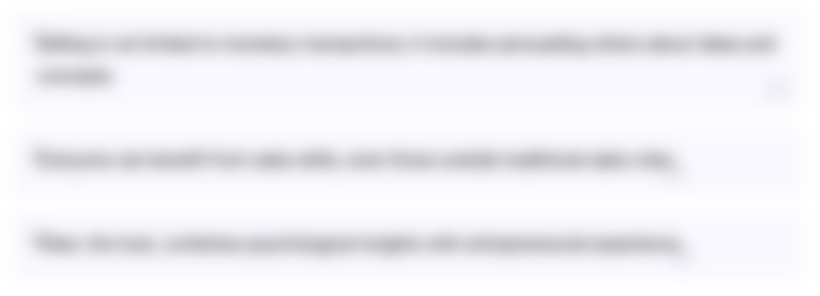
This section is available to paid users only. Please upgrade to access this part.
Upgrade NowTranscripts
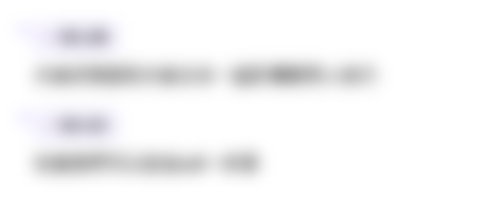
This section is available to paid users only. Please upgrade to access this part.
Upgrade NowBrowse More Related Video

mengenal indikator evaluasi kinerja lingkungan

How to Write an Operational Plan in Business Plan - Part 8 - Business plan writing course
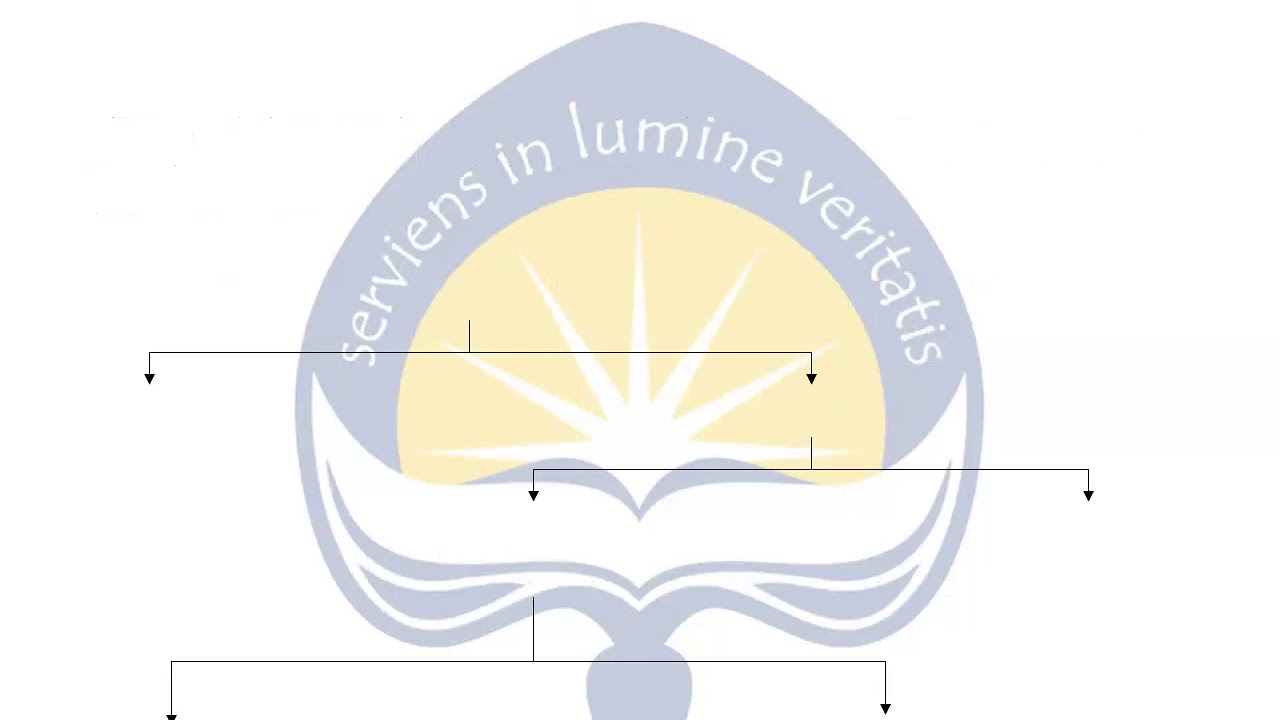
Sistem Pengendalian Manajemen Pengukuran kinerja tradisional 3

Teori Produksi - PART 1
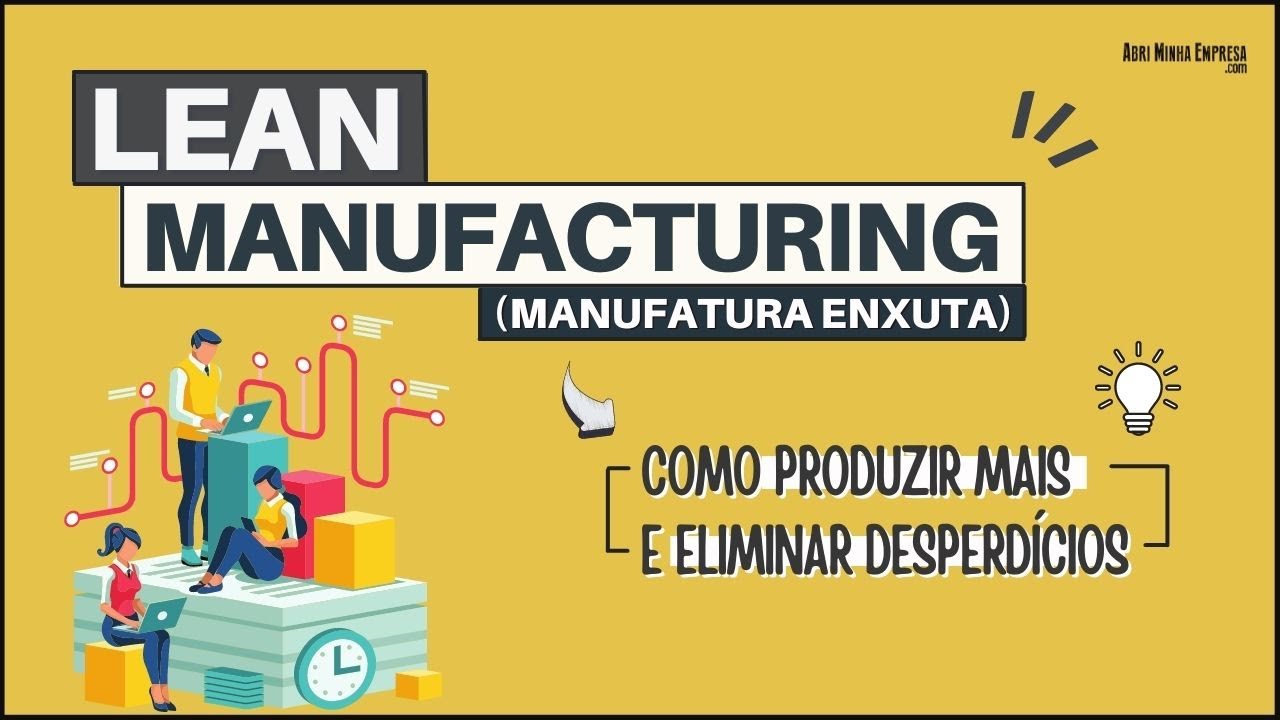
LEAN MANUFACTURING (Manufatura Enxuta) | Conheça os 8 Principais Tipos de Desperdícios

4.1 Production of goods and services IGCSE Business Part 1
5.0 / 5 (0 votes)