Philosophies of Quality Management new
Summary
TLDRThis lecture introduces key philosophies and strategies in quality management, highlighting the contributions of experts like Armand Feigenbaum, Kaoru Ishikawa, and Shigeo Shingo. It covers the importance of Six Sigma, TQM, and the Japanese 5S principle. The lecture emphasizes the role of quality circles and continuous improvement in achieving organizational success, with a focus on reducing costs and enhancing customer satisfaction.
Takeaways
- 📚 The lecture introduces philosophies of quality management, emphasizing the importance of quality in effective management and leadership.
- 🔍 Six Sigma, developed by Motorola, is a business management strategy aimed at improving the quality of process outputs by minimizing defects and variability.
- 🏆 Dr. W. Edwards Deming's philosophies on quality management have been influential, particularly in Japan, where his teachings led to significant success for companies like Toyota, Fuji, and Sony.
- 🏭 Armand Feigenbaum is recognized for his concept of Total Quality Control (TQM), which integrates quality development, maintenance, and improvement efforts across an organization.
- 🌐 Dr. Kaoru Ishikawa is known for developing quality circles and the cause-and-effect diagram, tools that have been instrumental in workplace transformation and continuous improvement.
- 🏗️ Shigeshi Shingo contributed to the field with his SMED system, aiming to reduce equipment changeover times significantly, thereby increasing efficiency.
- 📊 Walter A. Shewhart is considered the father of modern quality control, introducing statistical process control (SPC) techniques that are widely used in manufacturing.
- 🔄 The concept of Quality Circles (QC) involves employees at all levels working together to solve problems and improve processes within an organization.
- 🛠️ The 5S methodology (Sort, Set in order, Shine, Standardize, Sustain) is a foundational principle in workplace organization and efficiency, originating from Japan.
- 🌟 Quality is now seen as a critical factor for organizational success and growth, with a focus on customer satisfaction, cost reduction, and continuous improvement.
Q & A
What is the primary goal of Six Sigma?
-The primary goal of Six Sigma is to improve the quality of process outputs by identifying and removing the causes of defects and errors, and minimizing variability in manufacturing and business processes.
What is the significance of the term 'six sigma' in the context of manufacturing?
-In the context of manufacturing, 'six sigma' refers to a process that statistically expects 99.99966% of the products manufactured to be free of defects, which equates to 3.4 defects per million.
What potential problem can arise when companies focus on Six Sigma strategy?
-A potential problem with companies adopting a Six Sigma strategy is that they can become so focused internally on process improvements and operational cost savings that they lose focus on growing top-line sales.
Who is Dr. W. Edwards Deming and what is his contribution to quality management?
-Dr. W. Edwards Deming was a statistician who taught statistical process control to leaders of prominent Japanese businesses, leading to significant success for companies like Toyota, Fuji, and Sony. His philosophies of quality management, including the 14 points, have been influential in the field.
What is the concept of Total Quality Management (TQM) and who is credited with its development?
-Total Quality Management (TQM) is an effective system for integrating quality development, maintenance, and improvement efforts across an organization to ensure customer satisfaction and economical costs. It was developed by Armand Feigenbaum.
What is the concept of a 'hidden plant' in quality control?
-The concept of a 'hidden plant' refers to the extra work performed in correcting mistakes, implying that there is effectively an additional plant within any factory dedicated to fixing errors.
Who is Kaoru Ishikawa and what is his contribution to quality management?
-Kaoru Ishikawa was a developer of the concepts of quality circles and the cause and effect diagram, also known as the fishbone diagram or Ishikawa diagram. His philosophy focused on transforming the workplace and encouraging continuous improvement.
What is Shige Shingo's contribution to the field of quality management?
-Shige Shingo contributed the SMED (Single Minute Exchange of Die) system, which aims to reduce changeover times in manufacturing processes, with the belief that every changeover can be reduced by 5/6.
What is the significance of Walter A. Shewhart in the history of quality control?
-Walter A. Shewhart is known as the true father of modern quality control. He introduced the concept of statistical process control (SPC) in manufacturing and developed control chart techniques that have been widely adopted.
What is a Quality Circle and what are its main objectives?
-A Quality Circle (QC) is a small group of employees from various levels within an organization, voluntarily involved in identifying, analyzing, and solving work-related problems. Its main objectives include improving and developing the organization, fostering open exchange of ideas, and enhancing individual abilities and potentials.
What are the 5S principles in quality management?
-The 5S principles are a method of work organization involving Sort (Seiri), Set in order (Seiton), Shine (Seiso), Standardize (Seiketsu), and Sustain (Shitsuke). These principles aim to create and maintain a workplace that is clean, organized, efficient, and standardized.
Outlines
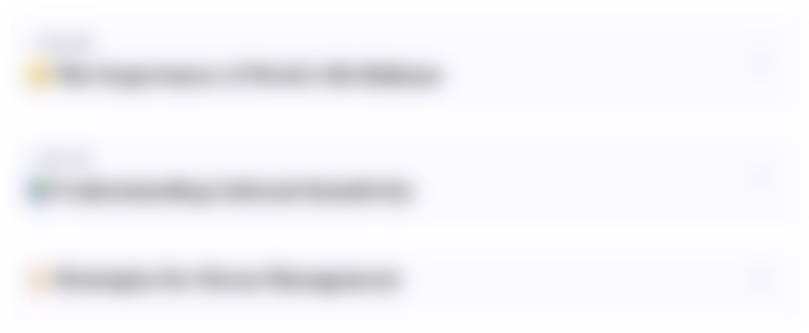
This section is available to paid users only. Please upgrade to access this part.
Upgrade NowMindmap
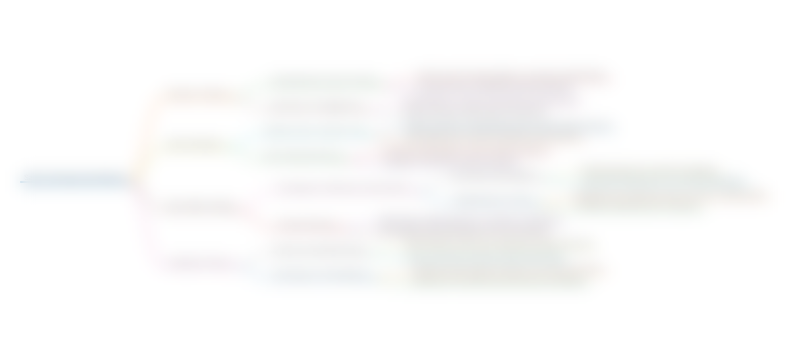
This section is available to paid users only. Please upgrade to access this part.
Upgrade NowKeywords
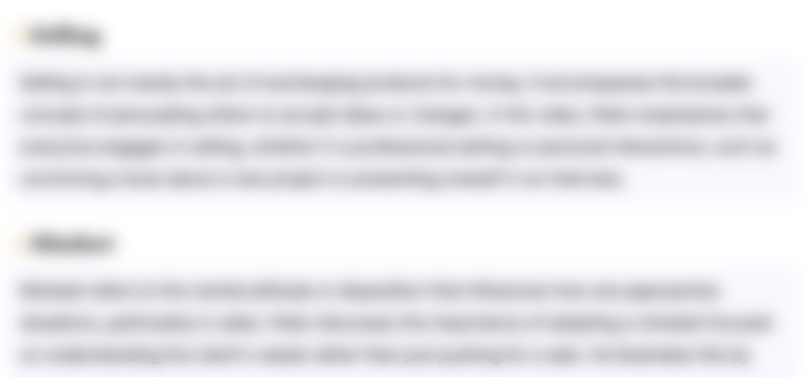
This section is available to paid users only. Please upgrade to access this part.
Upgrade NowHighlights
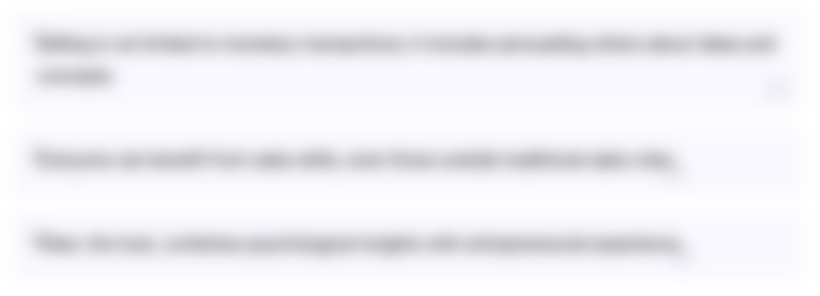
This section is available to paid users only. Please upgrade to access this part.
Upgrade NowTranscripts
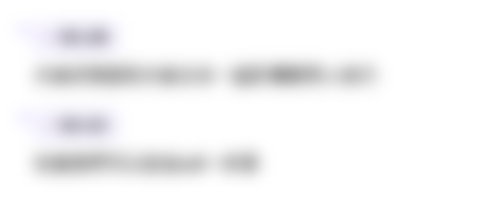
This section is available to paid users only. Please upgrade to access this part.
Upgrade NowBrowse More Related Video
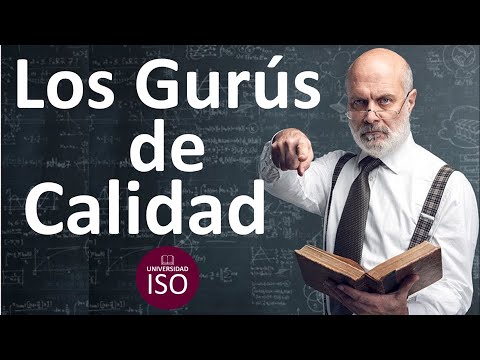
¿Quienes son los Gurús de Calidad? Edwards Deming | Philip B. Crosby | Kaoru Ishikawa Joseph Juran
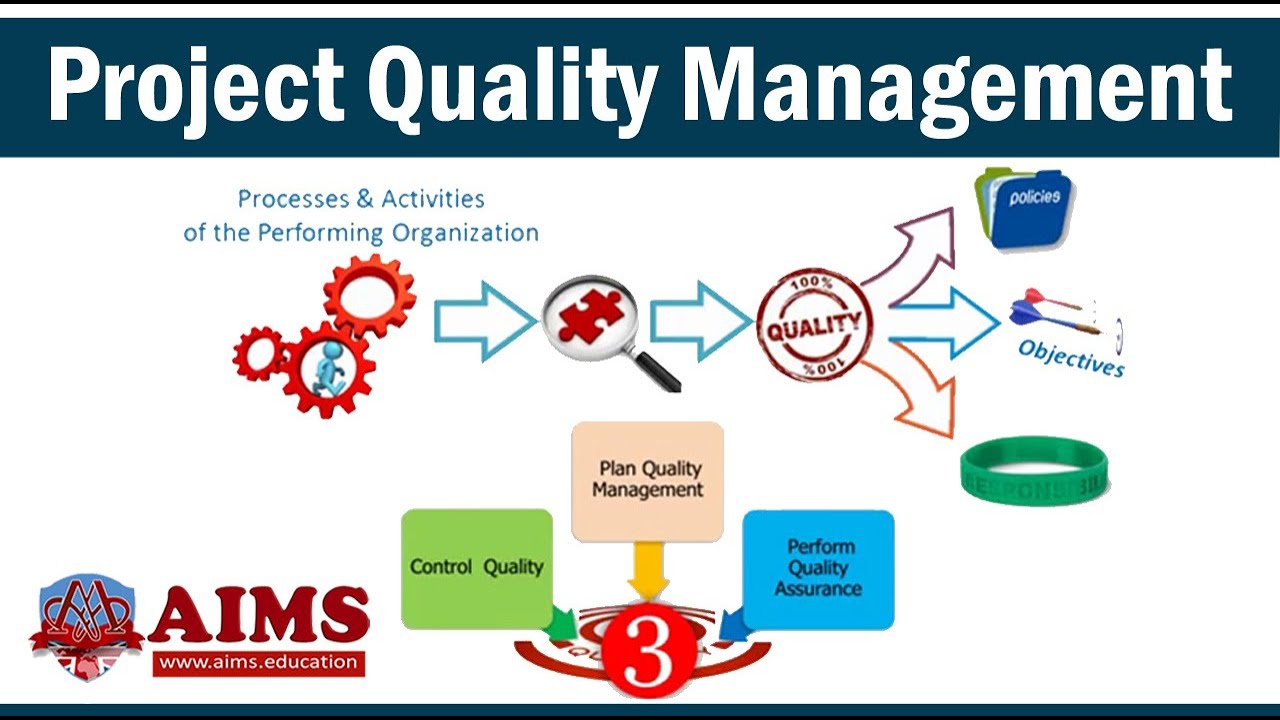
Project Quality Management - Processes and Seven Basic Quality Management Tools - AIMS UK

Los Gurús de la calidad y las 7 herramientas de la calidad para una ISO 9001 2008 Parte 1
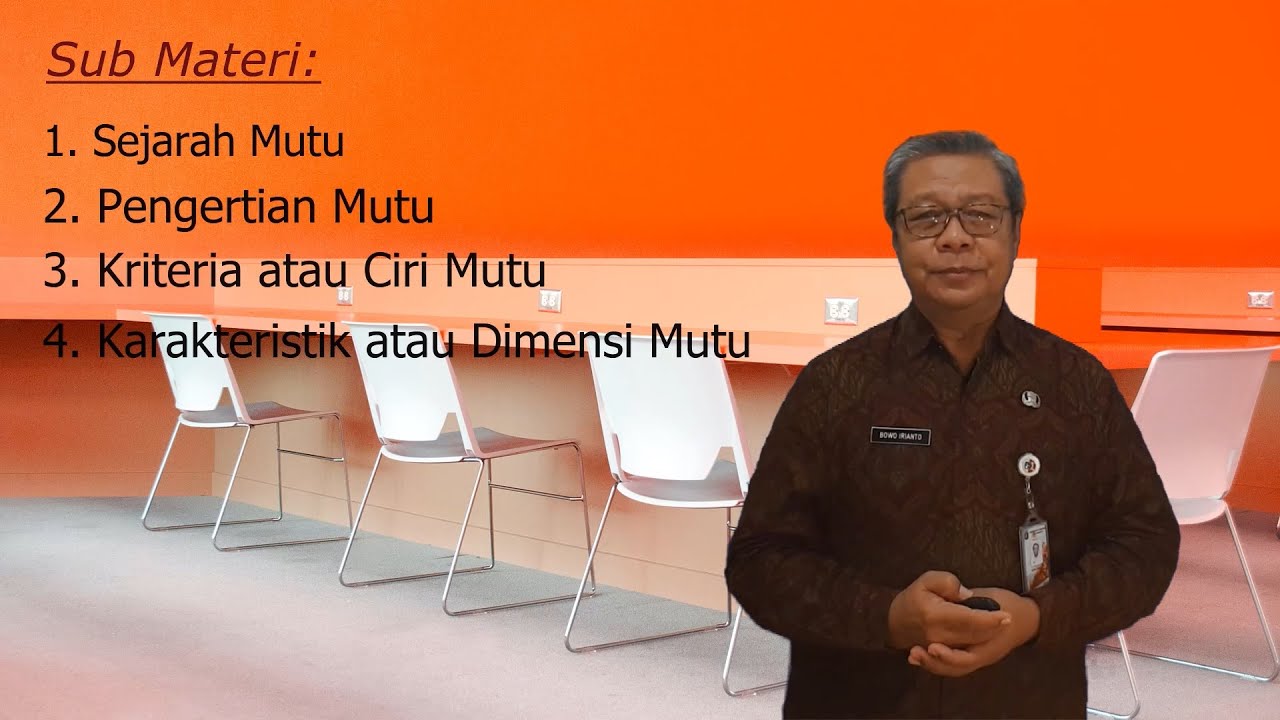
MANAJEMEN MUTU 01 - Sejarah, Pengertian, Kriteria dan Karakteristik Mutu - Bowo Irianto
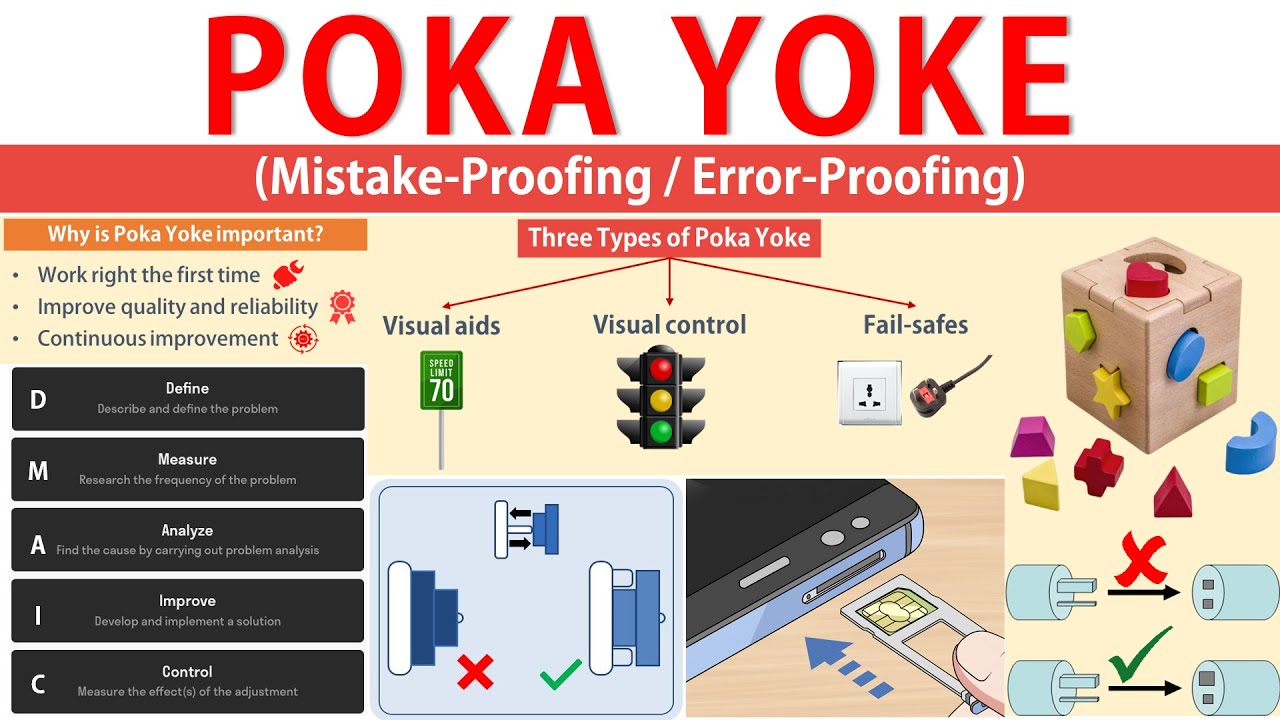
Poka Yoke (Error Proofing) - Meaning, Concept, Types, Stages, & Implementation Explained.

Quality Service Management in Tourism and Hospitality_Chapter 1_Introduction to Quality Management
5.0 / 5 (0 votes)