05 The Tensile Test
Summary
TLDR本视频展示了如何通过实验确定材料的应力-应变曲线,特别是在弹性区域。使用黄铜样品进行拉伸试验,样品呈特定的“狗骨”形状,中间部分较窄,两端较宽,以确保在拉伸过程中中间部分承受最大应力。实验中,通过在样品上安装应变片来测量应变,同时使用便携式拉伸试验机施加应力。视频详细记录了从弹性阶段到塑性变形的整个过程,并展示了材料在达到弹性极限后如何继续增强,直至最终断裂。
Takeaways
- 📏 拉伸样品通常是狗骨头形状,中间较窄,末端较宽,以便于夹持。
- 🔧 中间较窄的区域被称为“减小截面”,这是材料变形和失效的主要区域。
- 🎯 应变计安装在减小截面区域,用于精确测量应变。
- 📊 通过拉伸试验可以生成应力-应变曲线,其中弹性变形部分表现为直线。
- ⚙️ 拉伸试验中,初始加载曲线可能有“曲线尾巴”,是由设备的机械特性引起的。
- 🧠 在应力-应变曲线的弹性区域末端,材料开始发生塑性变形,通常在400兆帕附近。
- 🔄 卸载时,材料会发生弹性恢复,曲线的斜率仍然等于杨氏模量。
- 🏋️ 通过塑性变形,材料的强度增加,但杨氏模量保持不变。
- 🔄 拉伸试验还展示了材料的滞后现象,这是一种实验伪影。
- 💥 最终,在持续施加应力下,材料断裂,显示出延展性和弹性恢复。
Q & A
什么是应力-应变曲线?
-应力-应变曲线描述了材料在受到拉伸或压缩时的应力和应变之间的关系,特别是在弹性区和塑性区的表现。
为什么样品的中间部分被设计成较窄的截面?
-样品的中间部分被设计为较窄是为了集中应力,并确保材料的塑性变形和断裂发生在这一区域,从而便于研究和获取数据。
什么是‘狗骨样品’?
-‘狗骨样品’是一种用于拉伸测试的样品,它因形状类似于狗骨头而得名,通常在中间部分变窄,两端较宽,方便夹紧。
应力和应变是如何被测量的?
-应力是通过测量样品所承受的载荷来计算的,应变则通过附着在样品上的应变片精确测量。
什么是弹性恢复?
-弹性恢复指的是当材料在应力解除后恢复到原来形状的能力,通常发生在材料的弹性区域。
拉伸测试中的‘塑性变形’是什么意思?
-塑性变形是指材料在超出其弹性极限后发生的永久变形,即材料不会完全恢复到原来的形状。
‘屈服点’是什么?
-屈服点是指材料从弹性变形转变为塑性变形的应力水平,通常在应力-应变曲线上表现为曲线开始偏离线性部分的地方。
拉伸测试中的‘断裂’意味着什么?
-断裂是指材料在拉伸测试中承受的应力达到极限后发生的断裂或破坏,测试结束时材料通常会变得比原来更长。
应力-应变曲线中出现的‘滞后现象’是什么?
-滞后现象是指在加载和卸载过程中,材料应力-应变曲线之间形成的闭环,通常由于材料的内部摩擦或实验过程中的误差引起。
如何通过塑性变形增强材料的强度?
-通过对材料施加塑性变形,材料的强度会增加,这是由于材料内部结构发生了变化,如黑smith锻打金属时通过反复敲打增强强度的原理。
Outlines
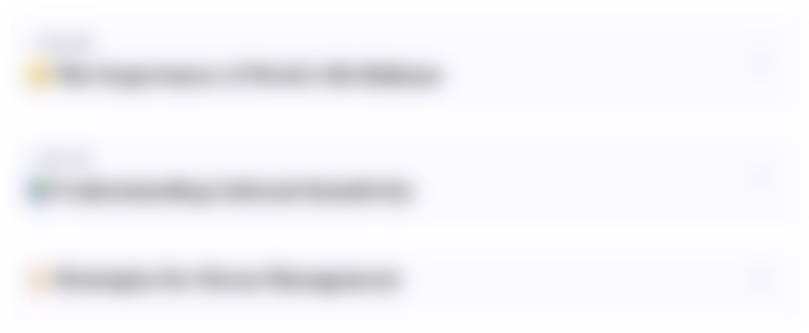
This section is available to paid users only. Please upgrade to access this part.
Upgrade NowMindmap
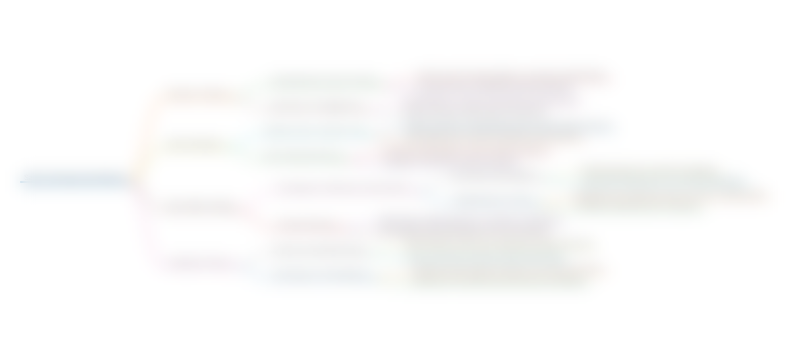
This section is available to paid users only. Please upgrade to access this part.
Upgrade NowKeywords
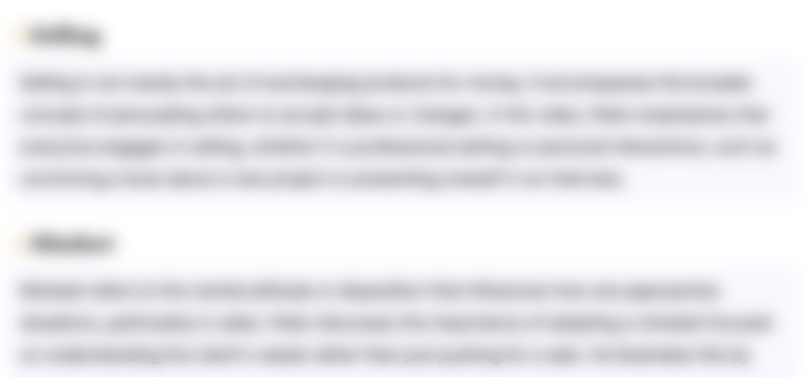
This section is available to paid users only. Please upgrade to access this part.
Upgrade NowHighlights
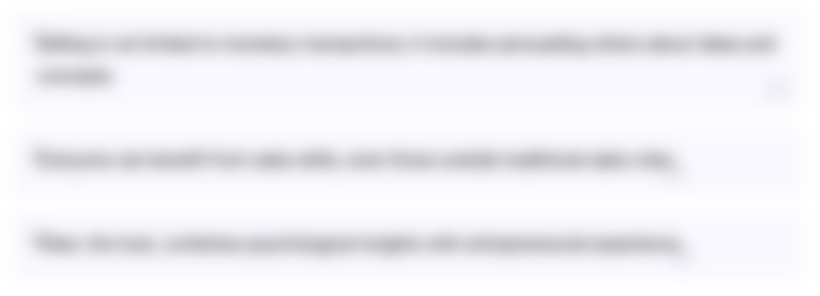
This section is available to paid users only. Please upgrade to access this part.
Upgrade NowTranscripts
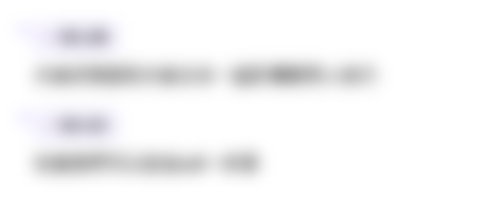
This section is available to paid users only. Please upgrade to access this part.
Upgrade NowBrowse More Related Video
5.0 / 5 (0 votes)