Internal Threading On The Lathe!
Summary
TLDRIn this instructional video, Quinn from Blindix demonstrates the art of single point cutting for internal threads, a skill that intimidates many machinists. Quinn dispels the fear by showing that with the right technique and patience, anyone can master it. The video covers the basics of grinding the threading tool, setting up the lathe, and cutting both through and blind internal threads. It also highlights the importance of using the compound for better control and safety, especially when dealing with blind holes. Quinn's step-by-step guidance, from preparing the tool to making test fits, makes this complex process accessible and satisfying to learn.
Takeaways
- ๐ ๏ธ The video discusses the process of single point cutting for internal threads, which is considered challenging for many home machinists.
- ๐ฉ Quinn, the presenter, suggests starting with learning external thread cutting before attempting internal threads due to the increased complexity.
- โ๏ธ An internal threading tool is required, and the video demonstrates how to grind one if you don't have access to a pre-made tool.
- ๐ The importance of using a fishtail gauge and proper grinding techniques to achieve the correct angles and clearances for the threading tool is emphasized.
- ๐ Magnification and good lighting are crucial for precision when grinding small threading tools.
- ๐จ Respirator use is recommended during grinding operations to protect against dust inhalation.
- ๐ฉ The video explains how to prepare the stock, including enlarging the hole to the appropriate size for threading.
- โ๏ธ The setup of the lathe, including the compound angle and tool height, is crucial for accurate threading.
- ๐ง A scratch pass is performed to ensure the threading gears are set correctly, and the threading depth is accurately measured.
- ๐ฉ Lighter cuts and more passes are recommended when cutting internal threads due to the less rigid nature of the tools.
- ๐ Measuring internal threads can be tricky, and the video suggests using Machinery's Handbook for dimensions or performing test fits.
Q & A
What is the main difference between cutting internal and external threads?
-The main difference is that internal thread cutting involves cutting into a hole, which requires a left-hand tool, and each step has a little twist on it, making the process more challenging and terrifying compared to external thread cutting.
Why does the video suggest starting with external thread cutting before attempting internal threads?
-External thread cutting is fundamental and less complex, so mastering it first provides a solid basis and confidence before moving on to the more intricate process of internal thread cutting.
What is a left-hand tool as mentioned in the script?
-A left-hand tool is one designed for cutting internal threads, which typically require a left-hand rotation to engage properly, as opposed to right-hand tools used for external threads.
What is the purpose of the clearances underneath and on the ends of the threading tool?
-The clearances underneath and on the ends of the threading tool are necessary to avoid interference with the workpiece, allowing the tool to cut close to the bottom of a hole or internal shoulders without rubbing against the material.
Why is it recommended to grind a threading tool from a split blank?
-Using a split blank for grinding a threading tool is recommended because it has been pre-split at the ends from the factory, which saves time and effort by reducing the amount of grinding dust and material that needs to be removed.
What is the role of the D-bit grinder in the process described?
-The D-bit grinder is used for fine-tuning the threading tool, specifically for plunge grinding the area behind the thread cutting point to clean up rough grinder marks and establish the necessary clearance angles.
Why is it important to use magnification and lots of light when grinding threading tools?
-Magnification and ample lighting are crucial for precision during the grinding of threading tools, as they allow the machinist to see the fine lines and grind accurately up to the desired specifications.
What is the significance of the compound angle in internal threading?
-The compound angle in internal threading is significant because it determines the direction of the tool's feed, which should align with the cutting edge of the threading tool to ensure proper thread formation and reduce tool pressure.
How does the process of cutting internal threads differ when moving from a through hole to a blind hole?
-Cutting internal threads in a blind hole is more challenging because it requires a special left-hand tool and a different approach, often involving starting in the middle and feeding outwards, which reduces the risk of crashing into the chuck or other obstructions.
What is a 'spring pass' in the context of thread cutting?
-A 'spring pass' is an additional pass made without adjusting the depth of cut, intended to remove any spring or deformation from the thread cutting tool, resulting in a more accurate and precise thread.
Why is single point internal thread cutting considered valuable despite being nerve-wracking?
-Single point internal thread cutting is valuable because it allows for the creation of threads in tight or blind holes that would be difficult or impossible with other methods, such as taps, and it can be done with a simple tool, offering precision and control over the thread formation process.
Outlines
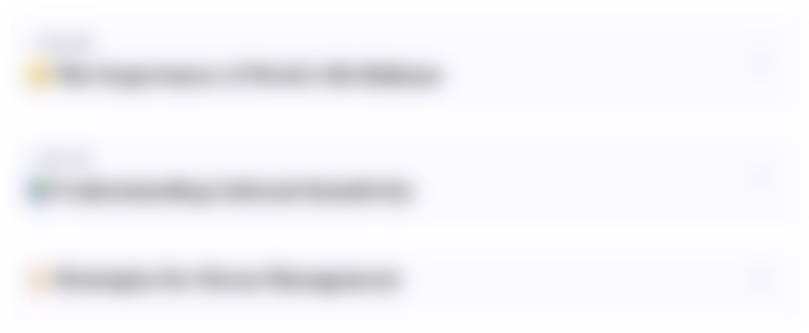
This section is available to paid users only. Please upgrade to access this part.
Upgrade NowMindmap
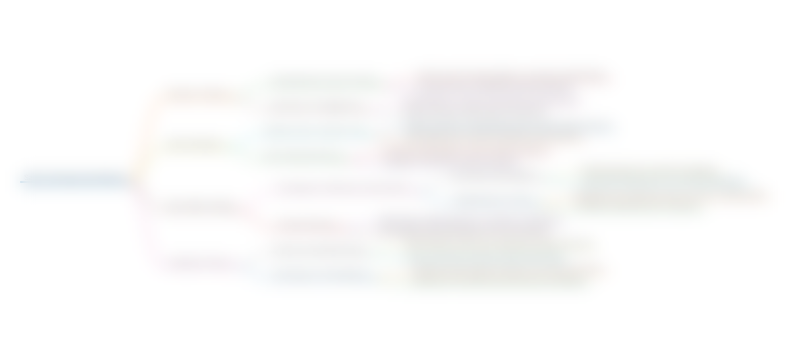
This section is available to paid users only. Please upgrade to access this part.
Upgrade NowKeywords
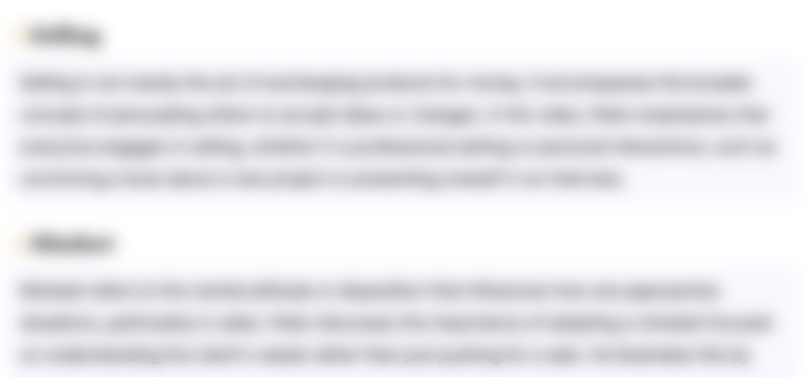
This section is available to paid users only. Please upgrade to access this part.
Upgrade NowHighlights
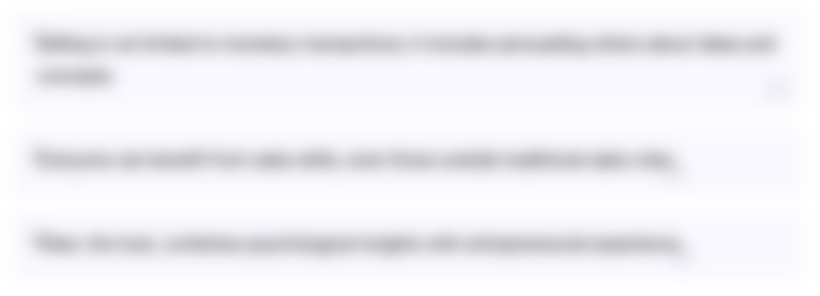
This section is available to paid users only. Please upgrade to access this part.
Upgrade NowTranscripts
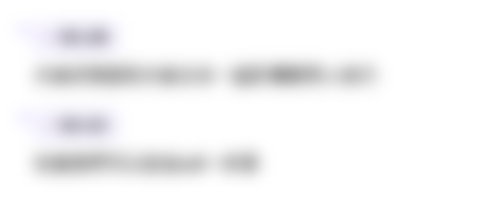
This section is available to paid users only. Please upgrade to access this part.
Upgrade NowBrowse More Related Video
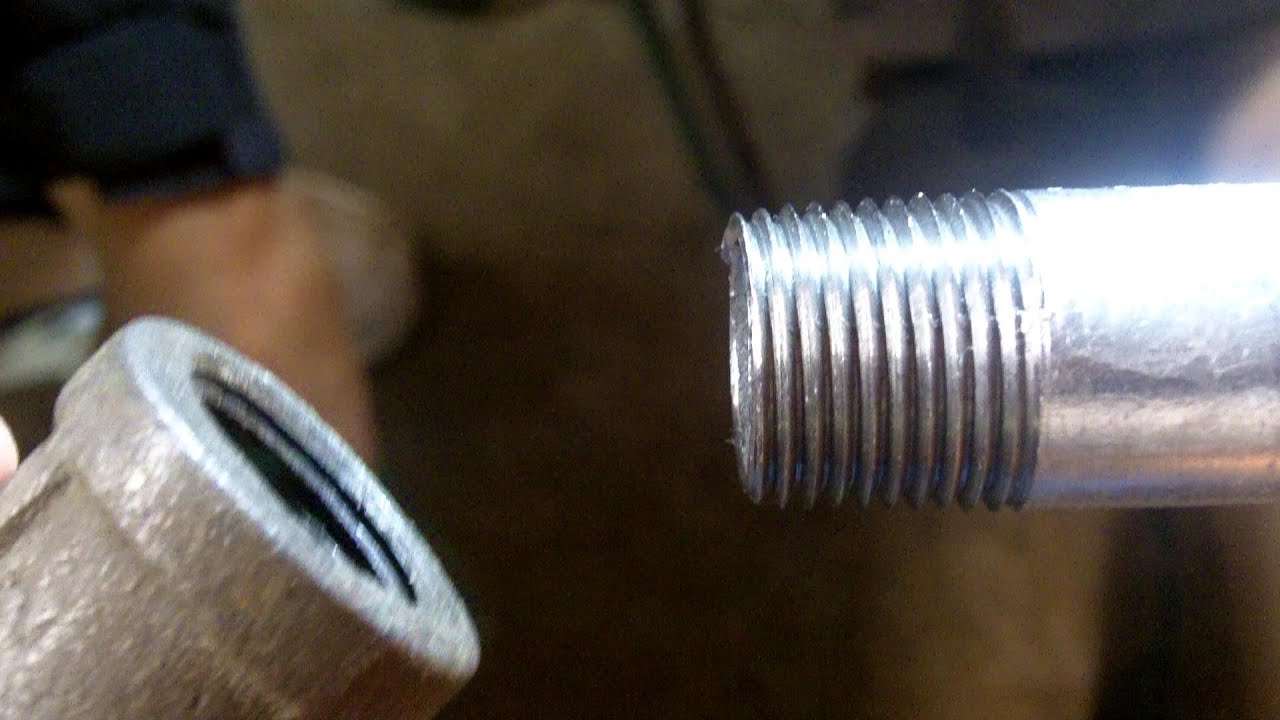
How to Thread Pipe; A Beginner's Tutorial

Multithreading Models & Hyperthreading

๐tutorial membuat keset kaki dari kain perca๐

CNC External thread cutting programming using code G76

Metal Lathe Tutorial 21 : Speeds & Feeds
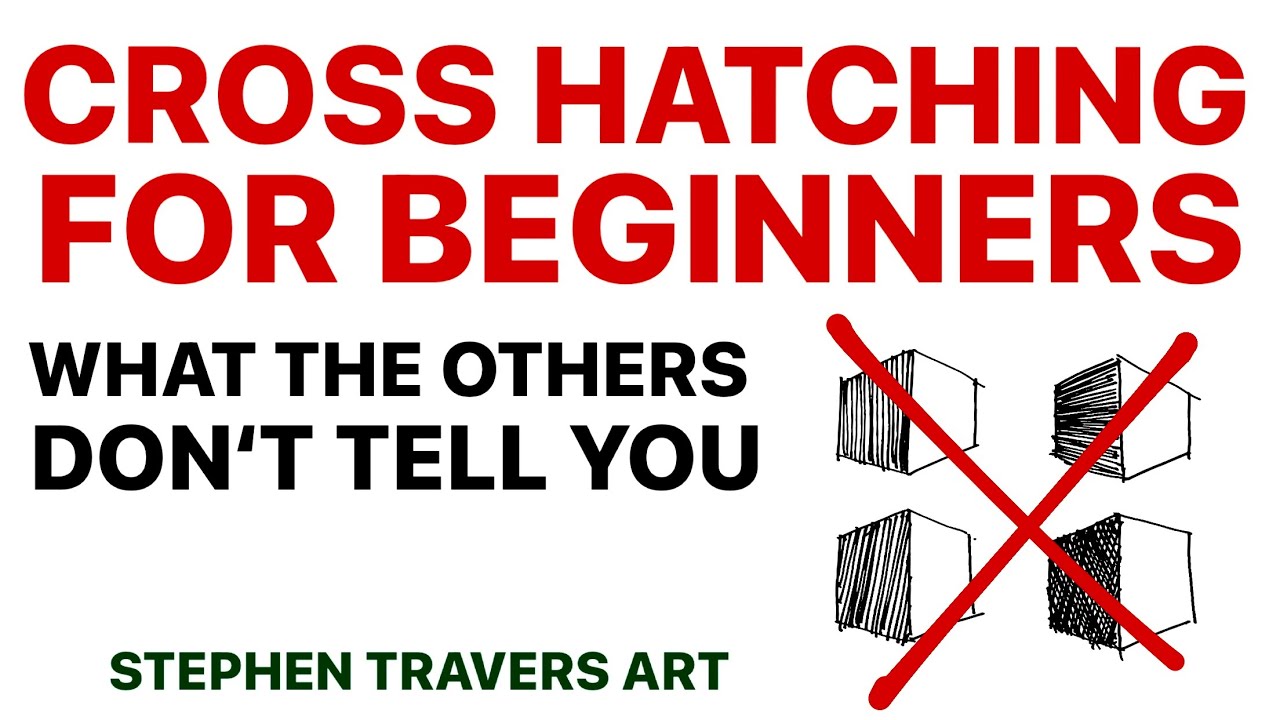
Beginners Need to Know This About Cross Hatching - And No One Else is Telling You!
5.0 / 5 (0 votes)