Hydraulic System Components - Hydraulics - Airframes & Aircraft Systems #8
Summary
TLDRThis lesson delves into the intricacies of an aircraft's hydraulic system, focusing on the reservoir's role in storing fluid and preventing leaks. It discusses the necessity of reservoirs despite the system's sealed nature, due to fluid expansion and contraction, and the presence of small, controlled leaks for actuator lubrication. The lesson also covers accumulators, their types, and functions, including pressure stabilization and emergency fluid supply. Additionally, it touches on the importance of filters for protecting system components from debris, and the automatic cutout valve's role in controlling system pressure and reducing pump wear.
Takeaways
- 💧 A reservoir is essential for an aircraft's hydraulic system, even though the system is designed to be leak-free, as it compensates for fluid expansion and contraction, and lubricates actuators.
- 🔄 Accumulators store variable amounts of fluid in hydraulic systems, which is crucial for the system's operation and is detailed further in the lesson.
- 💨 The hydraulic pump's operation involves both supplying pressure and creating suction, which can lead to cavitation if not managed properly by the reservoir.
- 🛑 Cavitation occurs when bubbles in the fluid implode with force, potentially causing severe pump damage, and it can be identified by specific sounds.
- 📡 Reservoirs help prevent cavitation by maintaining a positive pressure at the pump inlet, often achieved by being located higher than the pump or by pressurization with air.
- 🔗 The reservoir includes various connections for the hydraulic system, such as suction pipes to pumps, return pipes, and a quantity transmitter unit for monitoring.
- 🚫 To prevent debris from entering the reservoir, a strainer is used in the filling inlet, which is crucial for maintaining fluid cleanliness.
- 🛠️ Filters are used throughout the hydraulic system to protect components from damage caused by foreign particles and to ensure system efficiency.
- 🔄 An accumulator's function includes dampening pressure fluctuations and providing an emergency fluid supply in case of pump failure, highlighting its importance in system reliability.
- 🔩 The automatic cutout valve (ACOV) manages system pressure in constant delivery fixed volume pump systems, reducing pump wear by controlling the pump's operation.
Q & A
Why is a reservoir necessary in an aircraft's hydraulic system even though it is a sealed system?
-A reservoir is necessary because no system can be completely leak-free. It allows for small amounts of fluid to leak across the seals of actuators for lubrication, accommodates fluid expansion and contraction due to temperature changes, and stores extra fluid needed by actuators depending on their extension.
What is the role of an accumulator in a hydraulic system?
-An accumulator stores hydraulic fluid under pressure and serves to dampen pressure fluctuations, provide a small emergency supply of fluid in case of pump failure, and allow for thermal expansion and contraction of fluid.
How does a reservoir help prevent cavitation in a hydraulic system?
-A reservoir helps prevent cavitation by providing a head of fluid to the pump, ensuring a positive pressure at the pump inlet. It is often located higher in the system than the pump, and in some installations, it is also pressurized with air from the engine compressor.
What is the purpose of the baffles and fins in a reservoir?
-Baffles and fins in a reservoir are fitted to prevent sloshing and foaming of the fluid during in-flight maneuvers, ensuring the stability of the fluid within the reservoir.
What is the function of a suction filter in a hydraulic system?
-A suction filter protects the pump and other system components by removing foreign particles from the fluid before it enters the pump, preventing damage that could be caused by debris.
How does the bootstrap method work in pressurizing a reservoir?
-In the bootstrap method, a piston sits on top of the fluid in the reservoir and is pushed down by an actuator powered from its own hydraulic system, pressurizing the fluid. When the system is not operating, the pressure is held by a non-return valve.
What is the purpose of a filling inlet and strainer in a reservoir?
-A filling inlet, normally sealed with a filler cap, allows for the addition of fluid to the reservoir. The strainer in the filling inlet prevents debris from entering the reservoir, helping to keep the hydraulic fluid clean.
What is the role of an automatic cutout valve (ACOV) in a hydraulic system?
-An automatic cutout valve (ACOV) controls system pressure and provides the pump with an idling circuit when no services have been selected. It operates in two modes, cut in and cut out, to regulate the flow of fluid and reduce pump wear.
How does an accumulator provide the initial fluid when a selection is made and the pump is cut out?
-When a service is selected and the pump is cut out, the accumulator provides the initial fluid under pressure until the system pressure drops efficiently, signaling the pump to come online.
What can be inferred about the condition of a hydraulic system based on the time between cut out and cut in of the ACOV?
-The time between cut out and cut in of the ACOV can indicate the condition of the system. External leakage may cause frequent loading and unloading of the pump, while internal leakage, often caused by piston seal failure, can also lead to increased pump activity and potentially higher fluid temperatures.
Outlines
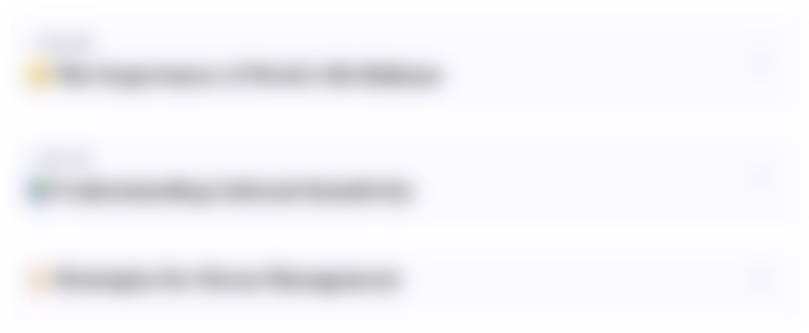
This section is available to paid users only. Please upgrade to access this part.
Upgrade NowMindmap
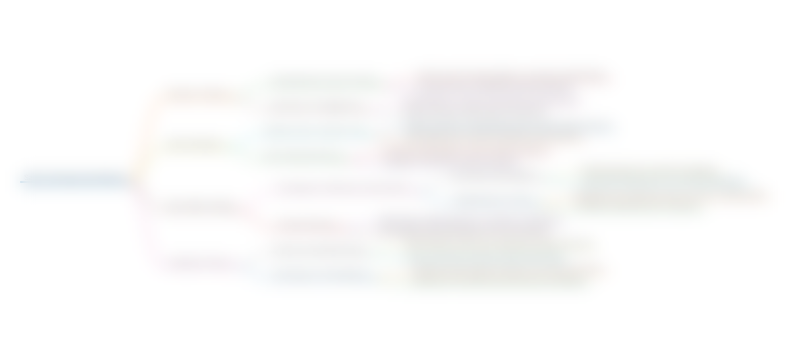
This section is available to paid users only. Please upgrade to access this part.
Upgrade NowKeywords
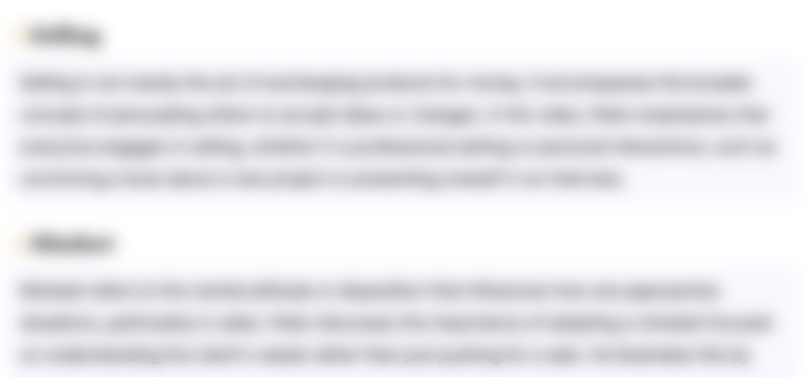
This section is available to paid users only. Please upgrade to access this part.
Upgrade NowHighlights
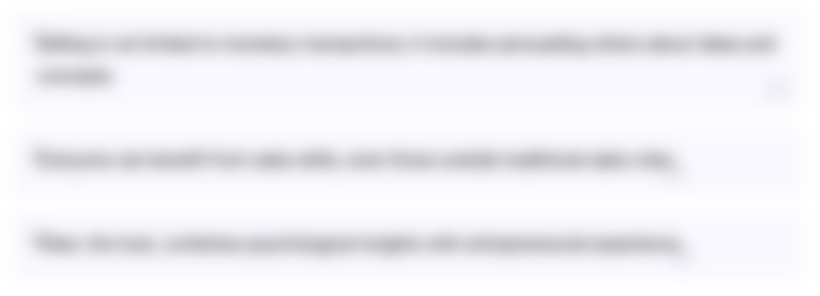
This section is available to paid users only. Please upgrade to access this part.
Upgrade NowTranscripts
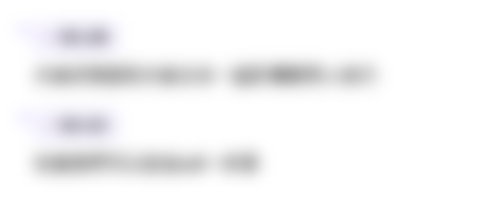
This section is available to paid users only. Please upgrade to access this part.
Upgrade NowBrowse More Related Video
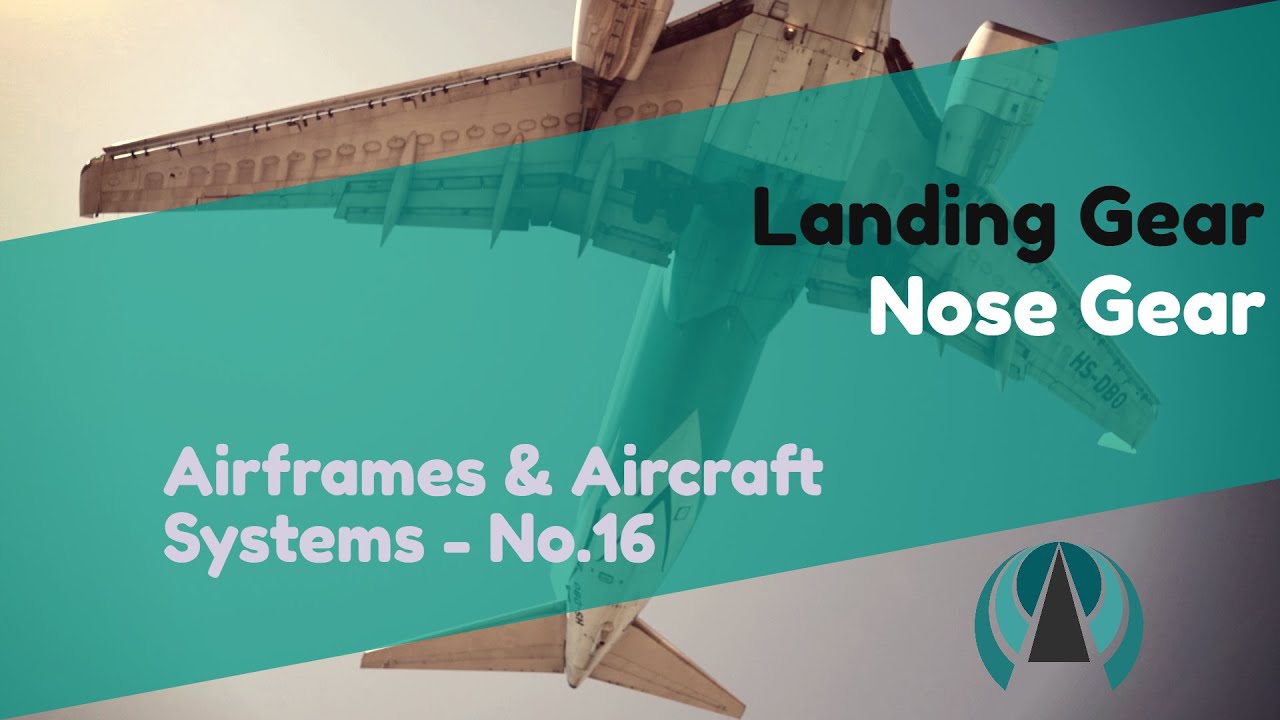
Nose Gear - Landing Gear - Airframes & Aircraft Systems #16
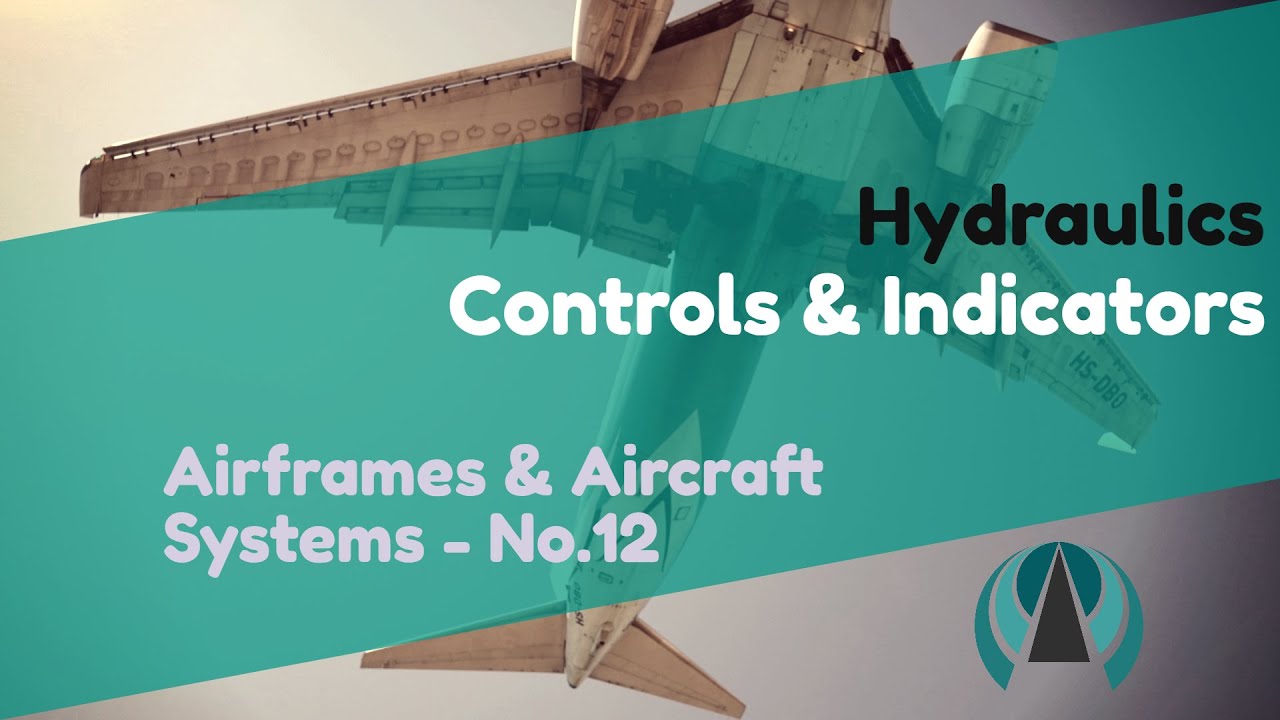
Controls & Indicators - Hydraulics - Airframes & Aircraft Systems #12
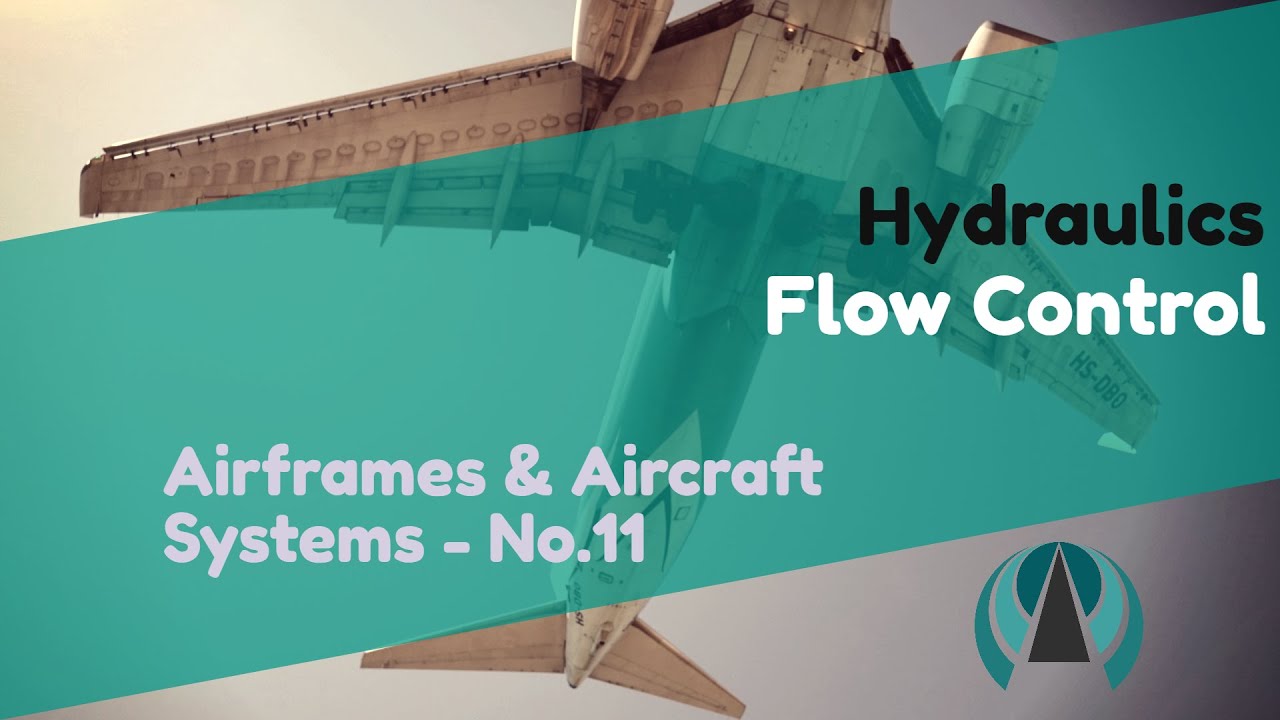
Flow Control - Hydraulics - Airframes & Aircraft Systems #11

Pressure Control - Hydraulics - Airframes & Aircraft Systems #10
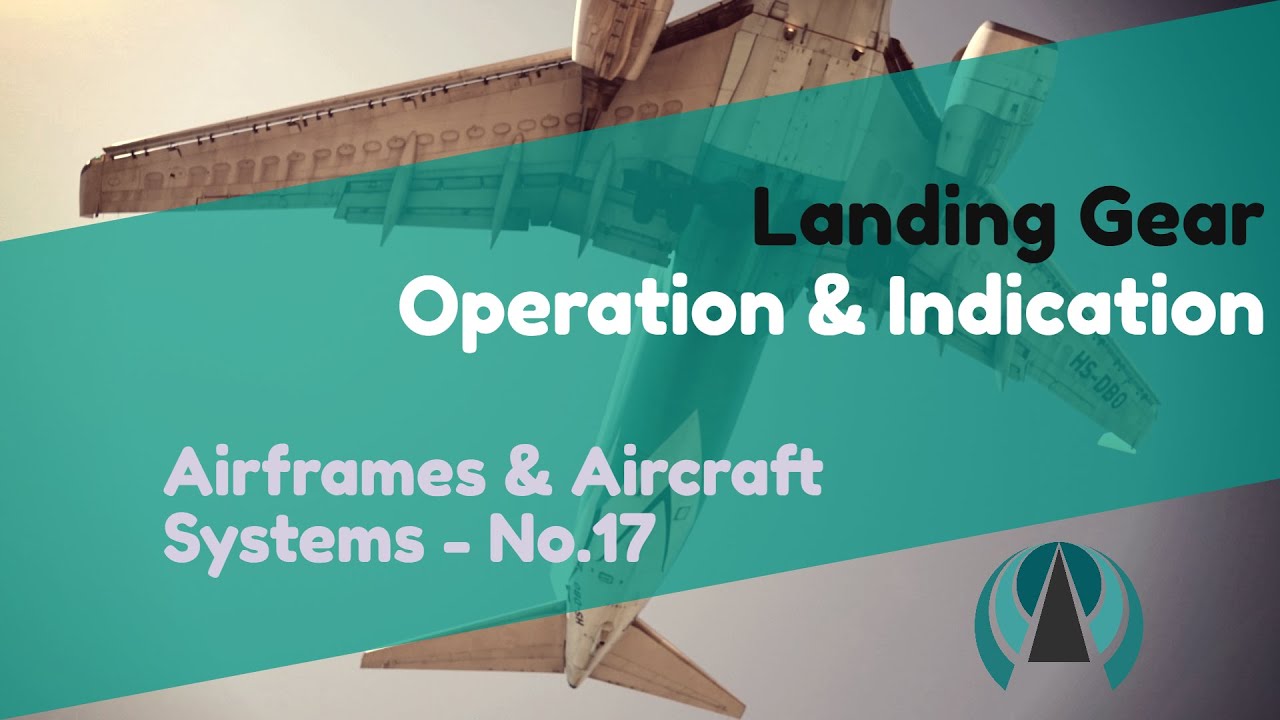
Operation & Indication - Landing Gear - Airframes & Aircraft Systems #17

Air Conditioning Part 2 - Pneumatics - Airframes & Aircraft Systems #40
5.0 / 5 (0 votes)