Flow Control - Hydraulics - Airframes & Aircraft Systems #11
Summary
TLDRThis lesson delves into hydraulic control devices used in aircraft systems. It explains the non-return valve, akin to a diode, allowing fluid flow in one direction only. The restrictor valve, or choke, limits flow in one direction while permitting full flow in the other, crucial for controlling service speeds. Selector valves direct fluid to actuators and provide return paths. Shuttle valves enable alternate systems to operate the same actuators. Sequence valves ensure proper gear and door operation sequence. Hydraulic fuses prevent leaks in critical areas, and modulators work with anti-skid units in brake systems, controlling fluid flow for optimal performance.
Takeaways
- 🔧 The non-return valve, also known as a check or non-reversible valve, allows fluid to flow in one direction but blocks it in the opposite, similar to a diode in electrical circuits.
- 🚧 A restrictor valve, or choke, permits limited fluid flow in one direction and full flow in the other, useful for controlling the speed of hydraulically operated services.
- 📍 Selector valves are used to direct fluid to the correct side of an actuator and provide a return path for displaced fluid, ensuring proper operation of hydraulic systems.
- 🔄 Shuttle valves enable an alternate hydraulic system to operate the same actuators as the normal system, crucial for redundancy in aircraft systems.
- 🛫 Sequence valves in landing gear hydraulic circuits ensure the correct sequence of door opening and closing, which is vital for safe aircraft operation.
- 💧 Hydraulic fuses are safety devices that block lines in vulnerable areas to prevent serious fluid leaks, enhancing the reliability of aircraft hydraulic systems.
- 🛑 A modulator, used with the anti-skid unit in brake systems, allows full flow to brake units on initial application and restricts flow thereafter for effective braking.
- ✈️ Modern jet aircraft rely heavily on hydraulic systems for various services including flight controls, landing gear operation, and wheel brakes.
- 🔗 The placement of restrictor valves is critical; they should be placed to restrict the flow of returned fluid to prevent pressure drop and potential damage to actuators.
- 🔐 Mechanically operated sequence valves use a piston and plunger mechanism to control the sequence of operations, such as landing gear and door operations.
Q & A
What is the primary function of a non-return valve in hydraulic systems?
-A non-return valve permits full flow in one direction but blocks flow in the opposite direction, similar to a diode in electrical circuits.
What is another name for a non-return valve?
-A non-return valve is also known as a check valve or a non-reversible valve.
How does a restrictor valve or choke differ from a non-return valve?
-A restrictor valve is designed to permit limited fluid flow in one direction and full flow in the other, unlike a non-return valve which only allows flow in one direction.
Why is it important to place a restrictor valve correctly in a hydraulic system?
-The valve should be placed to restrict the flow of returned fluid. If placed on the inlet side of an actuator, it could cause a pressure drop leading to cavitation and potential damage to the actuator.
What is the purpose of a selector valve in a hydraulic system?
-A selector valve directs fluid to the appropriate side of an actuator and provides a return path for the fluid displaced from the opposite side.
How can a shuttle valve be used in landing gear and brake systems?
-Shuttle valves enable an alternate hydraulic system to operate the same actuators as the normal system, switching over when normal system pressure is lost.
What sequence do sequence valves ensure in the landing gear hydraulic circuit?
-Sequence valves ensure that the gear and doors open and close in the correct sequence, which is crucial for proper operation and safety.
What is the role of hydraulic fuses in aircraft hydraulic systems?
-Hydraulic fuses block lines in vulnerable areas if a serious fluid leak occurs, preventing further loss of fluid and potential system failure.
How does a modulator work in conjunction with the anti-skid unit in a brake system?
-A modulator allows full flow to the brake units on initial brake application and thereafter restricts the flow, which is controlled by the anti-skid unit to prevent wheel lockup.
Why are multiple hydraulic systems used in modern jet aircraft?
-Modern jet aircraft rely on hydraulic systems for various critical functions like flight controls and landing gear operation, hence multiple systems are used for redundancy and safety.
Outlines
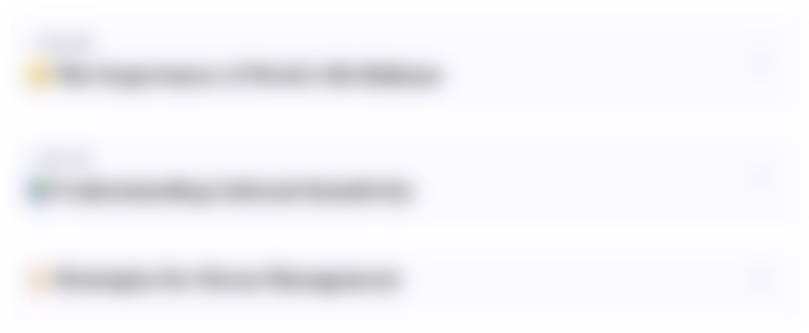
This section is available to paid users only. Please upgrade to access this part.
Upgrade NowMindmap
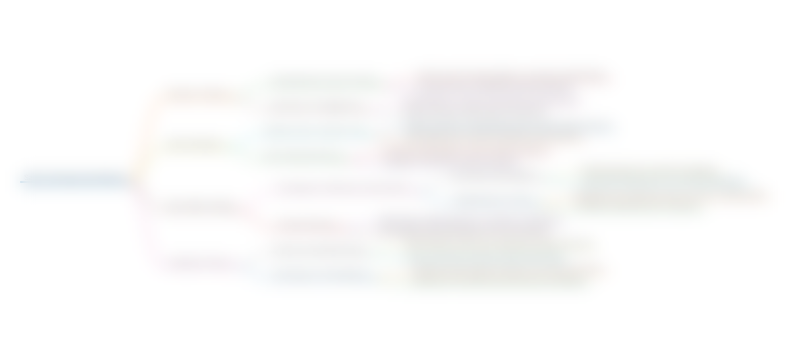
This section is available to paid users only. Please upgrade to access this part.
Upgrade NowKeywords
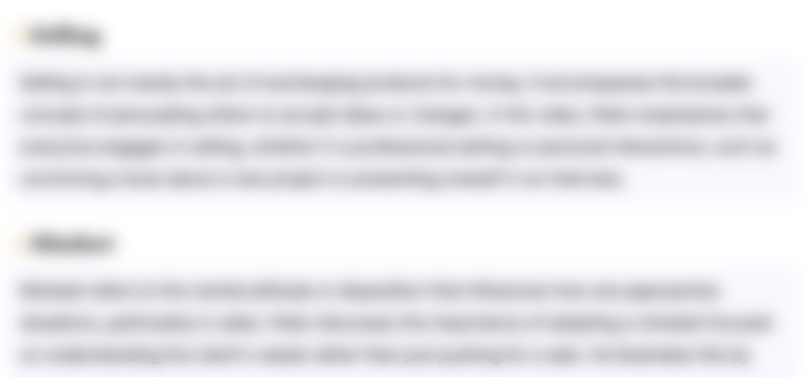
This section is available to paid users only. Please upgrade to access this part.
Upgrade NowHighlights
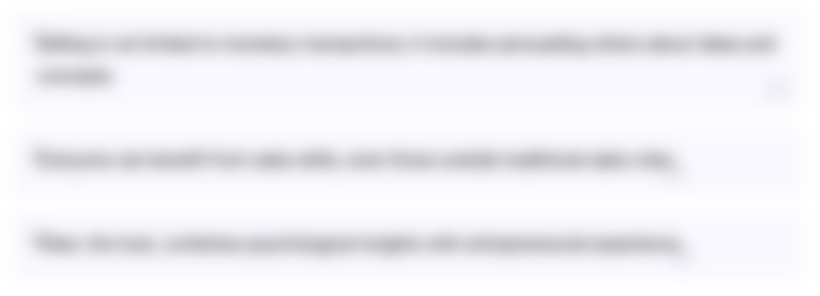
This section is available to paid users only. Please upgrade to access this part.
Upgrade NowTranscripts
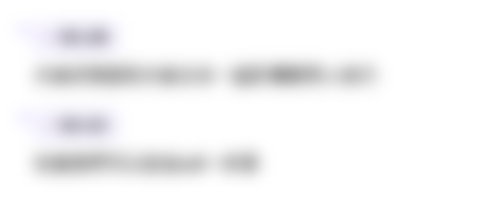
This section is available to paid users only. Please upgrade to access this part.
Upgrade NowBrowse More Related Video
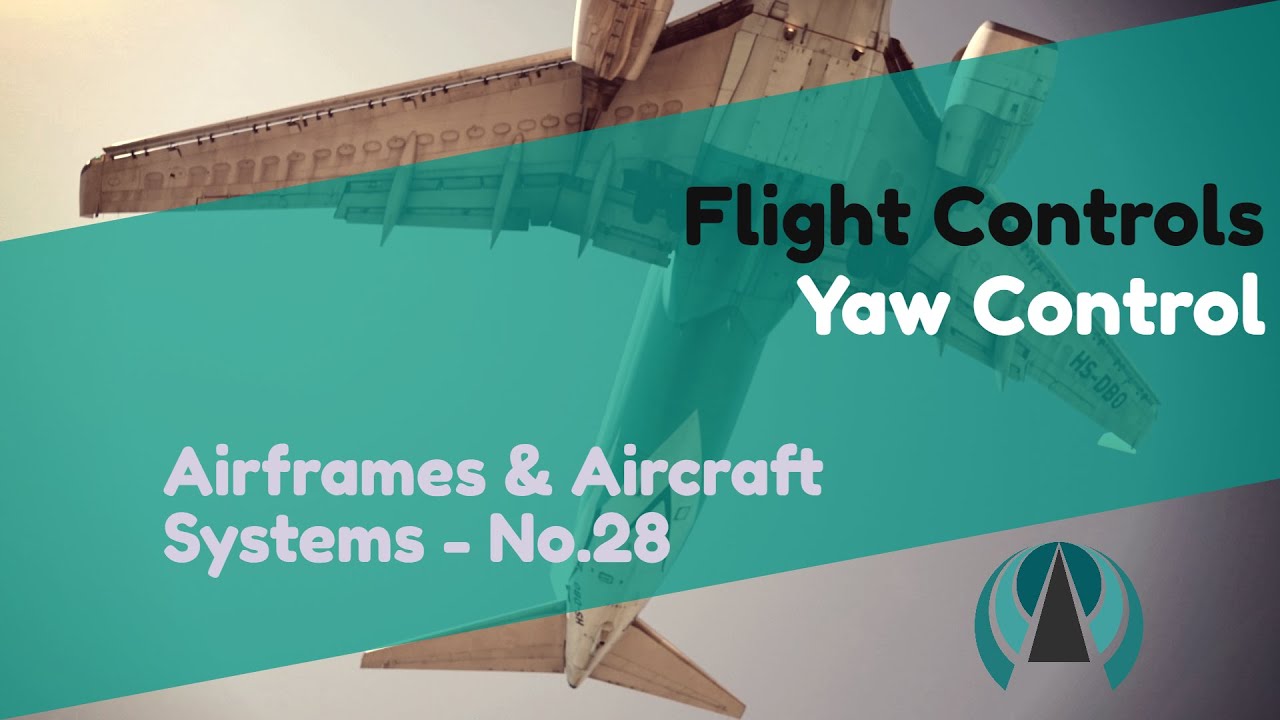
Yaw Control - Flight Controls - Airframes & Aircraft Systems #28
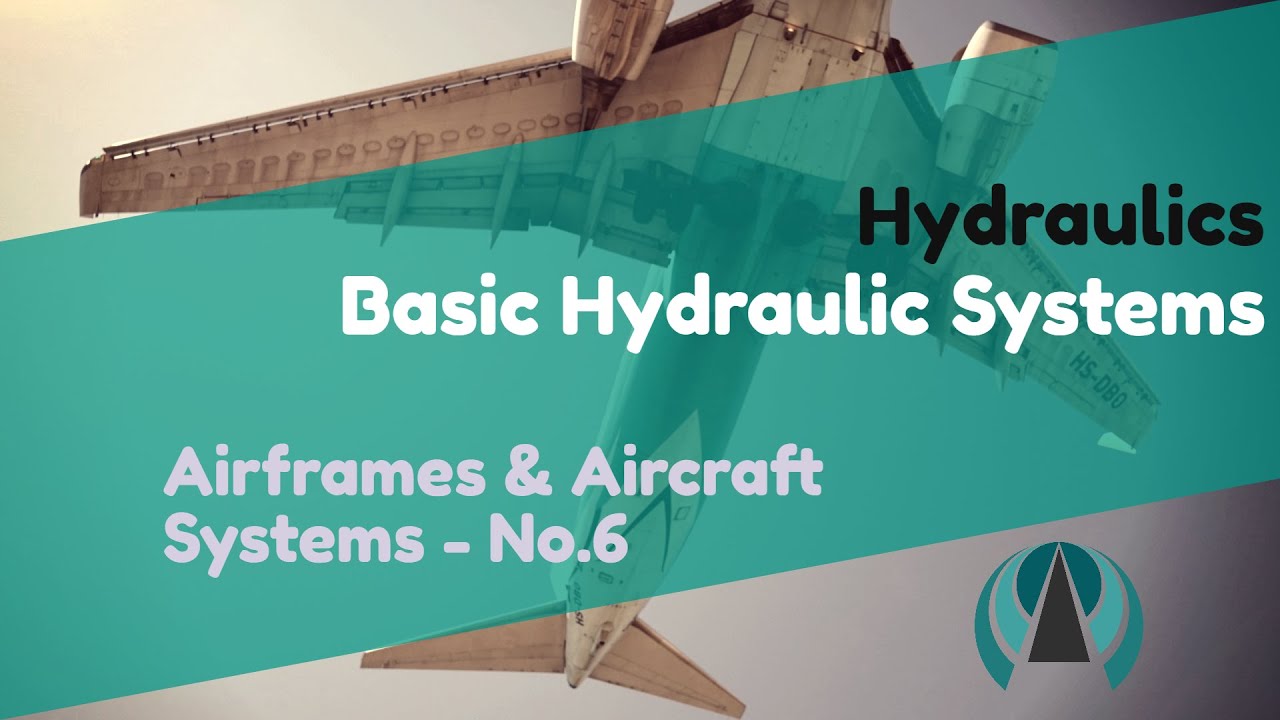
Basic Hydraulic Systems - Hydraulics - Airframes & Aircraft Systems #6
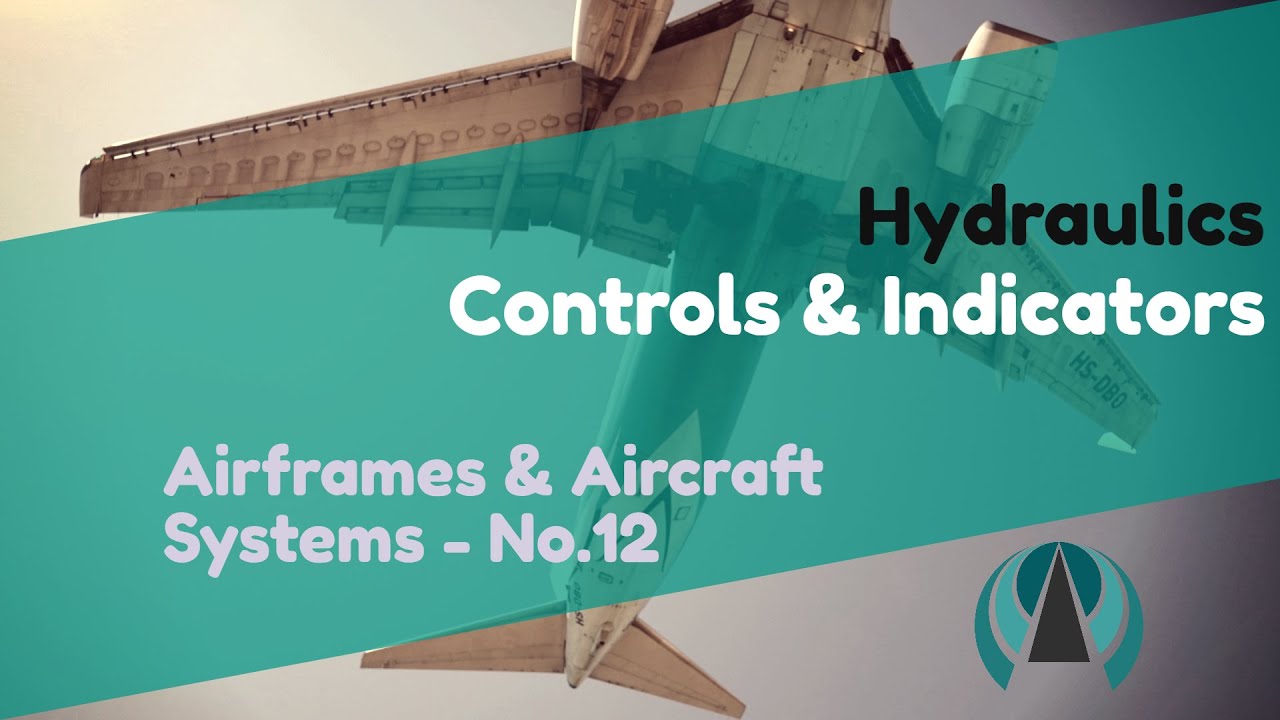
Controls & Indicators - Hydraulics - Airframes & Aircraft Systems #12

Pressure Control - Hydraulics - Airframes & Aircraft Systems #10
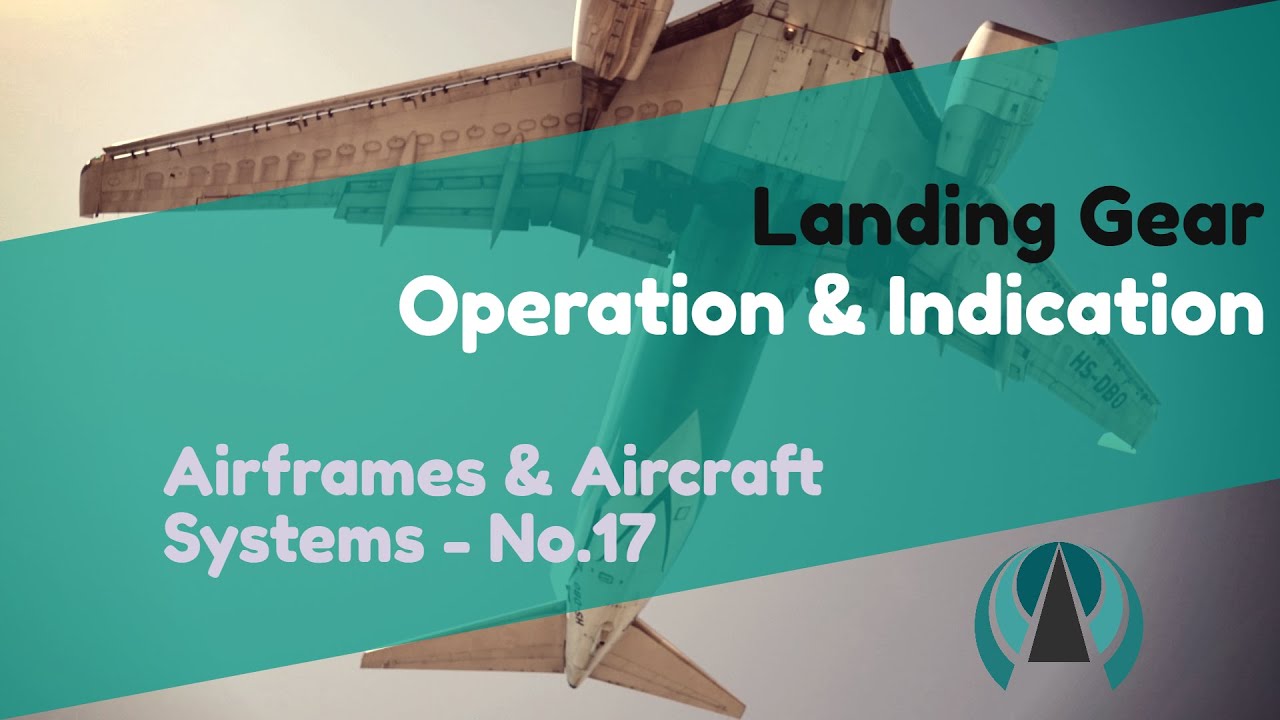
Operation & Indication - Landing Gear - Airframes & Aircraft Systems #17

Hydraulic Actuators & Motors - Hydraulics - Airframes & Aircraft Systems #9
5.0 / 5 (0 votes)