DX100 - Collision Detect (Code 4315)
Summary
TLDRThe video demonstrates the setup and implementation of the collision detection feature for the DX 100 controller, designed to safeguard the manipulator from unexpected collisions. Initially, the robot's collision detection is shown ineffective, with the robot not stopping during a crash. The tutorial then guides viewers through adjusting the maximum disturbance levels to activate the feature, ensuring the robot stops upon collision. After repairing damage and resetting the system, the video concludes with a successful demonstration of the collision detection in action.
Takeaways
- 🛠️ The script discusses the setup and implementation of collision detection for the DX 100 controller, which is crucial for protecting the manipulator from unexpected collisions.
- 🔍 Collision detection does not include tool or tool tip sensors; additional sensors are required for comprehensive protection.
- 📊 The script demonstrates the operation of the robot with factory-delivered collision detection settings, where valid values range from one to five hundred.
- 🚫 A mock-up scenario shows that the robot did not stop upon a collision, indicating the need to adjust the settings.
- 🔎 The 'maximum disturbers detected' can be found under the 'robot shock twister level', and it's necessary to be in 'management security' to access this feature.
- 🔑 The script highlights the importance of selecting a number smaller than the detected maximum (e.g., choosing 30 instead of 52) to ensure the collision detection engages.
- 🔧 After repairing any damage and adjusting the settings, the script shows a demonstration with the collision detection feature expected to be fully active.
- 💡 The script instructs on how to reset the alarm and move the machine out of a collision condition by using the 'teach reset' and 'job' functions.
- 🛑 The robot's shock sensor level can be adjusted by selecting any field and changing the feature to 'invalid', which stops the machine's operation.
- ✅ Once the machine is moved out of the collision area, the script emphasizes resetting the condition back to 'valid' to conclude the demonstration.
Q & A
What is the primary purpose of the collision detect feature in the DX 100 controller?
-The primary purpose of the collision detect feature is to protect the manipulator in the event of an unexpected collision.
Does the collision detect feature include protection for the tool or tool attachment?
-No, the collision detect feature does not include protection for the tool or tool attachment; a separate sensor would be required for that.
What is the range of valid values for the collision detect settings on the DX 100 controller?
-The valid values for the collision detect settings on the DX 100 controller range between one and five hundred.
What is the significance of the 'maximum disturbers detected' value in the collision detect feature?
-The 'maximum disturbers detected' value indicates the level of disturbance or shock that the robot can tolerate before the collision detect feature engages to protect the manipulator.
How can one access the 'robot shock twister level' setting on the DX 100 controller?
-To access the 'robot shock twister level' setting, one must be in management security mode for the button to appear, and then it can be adjusted accordingly.
What action was taken in the demo when the robot did not stop during the first attempt?
-When the robot did not stop during the first attempt, the maximum disturbers detected value was checked and adjusted to a number smaller than the largest number in the field to ensure the collision detect would engage on the next try.
What is the procedure to reset the robot after a collision has been detected?
-To reset the robot after a collision has been detected, one should perform a teach reset to clear the alarm, job the machine off, and then change the feature to invalid for any field, allowing the machine to move out of the collision condition.
Why is it important to reset the condition back to valid after moving the machine out of the collision condition?
-It is important to reset the condition back to valid after moving the machine out of the collision condition to ensure that the collision detect feature remains active and functional for future operations.
What is the role of the 'teach mode' in the collision detect feature demonstration?
-In the collision detect feature demonstration, 'teach mode' is used to safely operate and adjust the robot's settings without performing actual tasks, allowing for adjustments such as the maximum disturbers detected value.
How does the collision detect feature protect the robot during operation?
-The collision detect feature protects the robot by detecting unexpected collisions and stopping the robot's operation when the disturbance exceeds the set threshold, thus preventing damage to the manipulator.
Outlines
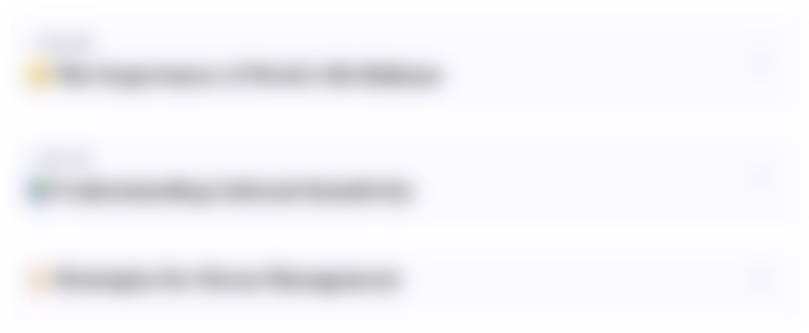
This section is available to paid users only. Please upgrade to access this part.
Upgrade NowMindmap
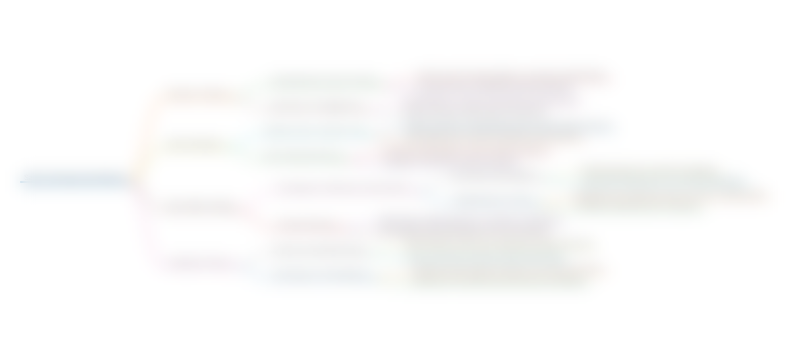
This section is available to paid users only. Please upgrade to access this part.
Upgrade NowKeywords
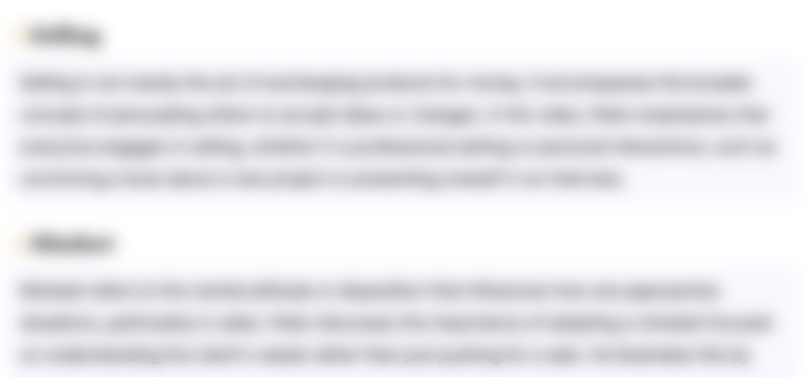
This section is available to paid users only. Please upgrade to access this part.
Upgrade NowHighlights
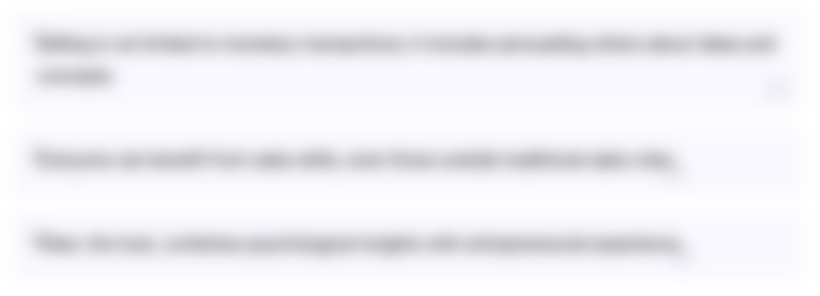
This section is available to paid users only. Please upgrade to access this part.
Upgrade NowTranscripts
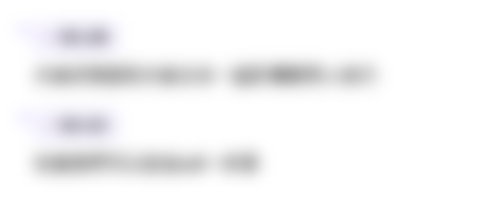
This section is available to paid users only. Please upgrade to access this part.
Upgrade NowBrowse More Related Video
5.0 / 5 (0 votes)