What is Total Quality management (TQM)? | 7 Principles of Total Quality Management
Summary
TLDRThis video delves into Total Quality Management (TQM), a structured approach to enhance organizational outputs through continuous improvement. Originated in the 1950s by William Deming, TQM emphasizes seven core principles, including customer focus, employee involvement, and process-centered thinking. It advocates for an integrated system, fact-based decision-making, and strategic planning, fostering a culture of communication and quality. The video outlines TQM's benefits, such as defect reduction, increased productivity, cost savings, and heightened customer satisfaction, while also acknowledging potential challenges like the initial training period and resistance to change.
Takeaways
- 📚 Total Quality Management (TQM) is a structured approach for overall organizational management focused on improving the quality of outputs, including goods and services.
- 🌟 TQM originated in the 1950s and was developed by William Deming, a management consultant whose work significantly influenced Japanese manufacturing.
- 🔍 The term 'total' in TQM signifies the involvement of the entire organization, including all departments and functions in quality management.
- 🔑 TQM involves a continuous process of detecting and reducing errors, streamlining supply chain management, improving customer experience, and ensuring employee training.
- 👥 Principle 1: Customer Focus - Customer feedback is crucial in determining the level of quality and driving quality improvement efforts.
- 🤝 Principle 2: Total Employee Involvement - All employees must be engaged in working towards common goals, with an environment that fosters empowerment and continuous improvement.
- 🔄 Principle 3: Process Centered - TQM emphasizes process thinking, defining steps to transform inputs into outputs and monitoring performance to detect variations.
- 🛠️ Principle 4: Integrated System - An organization should have a system that provides effective TQM, possibly based on a quality standard like ISO 9001.
- 📊 Principle 5: Decision Making Based on Facts - TQM requires the collection and analysis of performance data to improve decision-making accuracy.
- 🎯 Principle 6: Strategic and Systematic Approach - TQM includes strategic planning that integrates quality as a core component to achieve organizational goals.
- 🗣️ Principle 7: Communication - Effective communication is vital during operations and organizational change to maintain morale and motivate employees.
- 💡 Advantage: Defect Reduction - TQM improves quality within processes, reducing the need for quality assurance personnel and time spent fixing errors.
- 📈 Advantage: Productivity Improvement - With fewer errors, employees spend less time correcting them, leading to increased output and often profits.
- 💰 Advantage: Cost Reduction - Consistent implementation of TQM can reduce costs due to fewer product defects, saving on customer support and product fixes.
- 👍 Advantage: Customer Satisfaction - Improved products and services with error-free interactions lead to higher customer satisfaction and potentially increased market share.
- 😊 Advantage: Improve Employee Morale - The success of TQM can enhance employee morale, reducing turnover and associated hiring and training costs.
- ⏳ Disadvantage: Training Period - TQM requires extensive training, which can temporarily affect costs as employees are taken away from their usual work.
- 😓 Disadvantage: Resistance to Change - TQM's incremental changes may face resistance from employees who prefer the current system or fear job loss.
Q & A
What is Total Quality Management (TQM)?
-Total Quality Management (TQM) is a structured approach to overall organizational management aimed at improving the quality of an organization's outputs, including goods and services, through the continual improvement of internal practices.
Who developed the concept of TQM?
-The concept of TQM was developed by William Deming, a management consultant whose work had a significant impact on Japanese manufacturing in the 1950s.
What does the term 'total' in TQM signify?
-The term 'total' in TQM signifies that all parties, departments, and functions within an organization are involved in quality management.
What are the seven principles of TQM?
-The seven principles of TQM are: 1) Customer-focused, 2) Total employee involvement, 3) Process-centered, 4) Integrated system, 5) Decision making based on facts, 6) Strategic and systematic approach, and 7) Communication.
How does TQM focus on the customer?
-TQM focuses on the customer by using their feedback to determine the level of quality and ensuring that customer satisfaction is at the forefront of all quality improvement efforts.
What is the role of employees in TQM?
-In TQM, all employees are involved in working towards common goals, and total employee engagement is achieved when they are empowered and when management creates a conducive environment for continuous improvement.
Why is process thinking important in TQM?
-Process thinking is important in TQM because it involves a series of steps that transform inputs from suppliers into outputs for customers. Continuously monitoring performance measures helps detect unexpected variation and improve the process.
What is an integrated system in the context of TQM?
-An integrated system in TQM is a cohesive framework that provides effective total quality management across all functions and divisions of an organization, which may be based on a quality standard such as ISO 9001.
How does TQM approach decision making?
-TQM approaches decision making by requiring organizations to frequently collect and analyze data on performance measures to improve the accuracy and effectiveness of decision-making.
What are some advantages of implementing TQM?
-Advantages of TQM include defect reduction, productivity improvement, cost reduction, increased customer satisfaction, and improved employee morale.
What challenges might organizations face when implementing TQM?
-Challenges in implementing TQM include the need for considerable employee training, potential negative reactions from employees who prefer the current system or fear job loss due to incremental changes.
How does TQM contribute to employee morale and turnover?
-TQM contributes to improved employee morale through ongoing success and involvement in quality improvement, which in turn can reduce employee turnover and associated hiring and training costs.
What is the significance of communication in TQM?
-Communication is significant in TQM as it plays a crucial role in maintaining morale and motivating employees during day-to-day operations and times of organizational change, involving strategies, practice, and timeliness.
Outlines
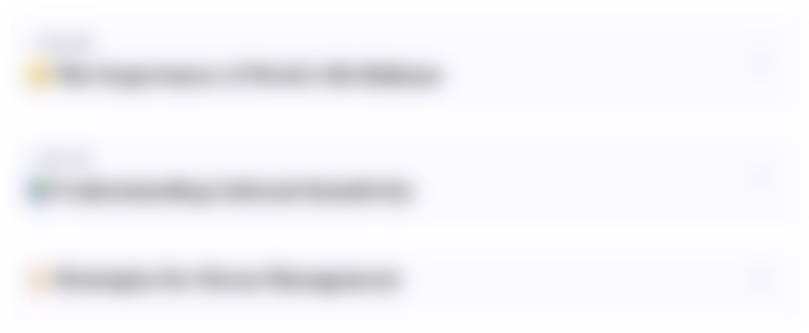
Этот раздел доступен только подписчикам платных тарифов. Пожалуйста, перейдите на платный тариф для доступа.
Перейти на платный тарифMindmap
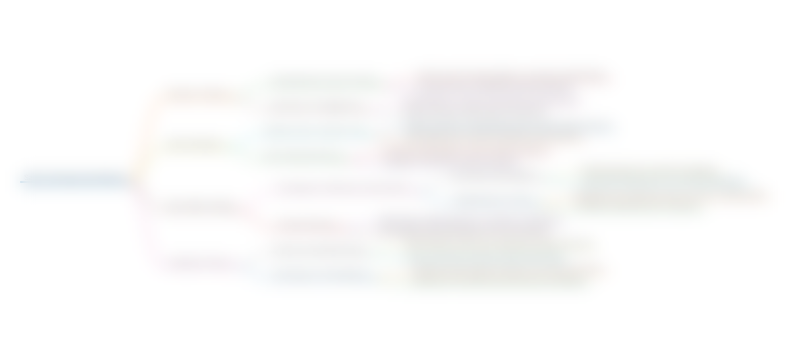
Этот раздел доступен только подписчикам платных тарифов. Пожалуйста, перейдите на платный тариф для доступа.
Перейти на платный тарифKeywords
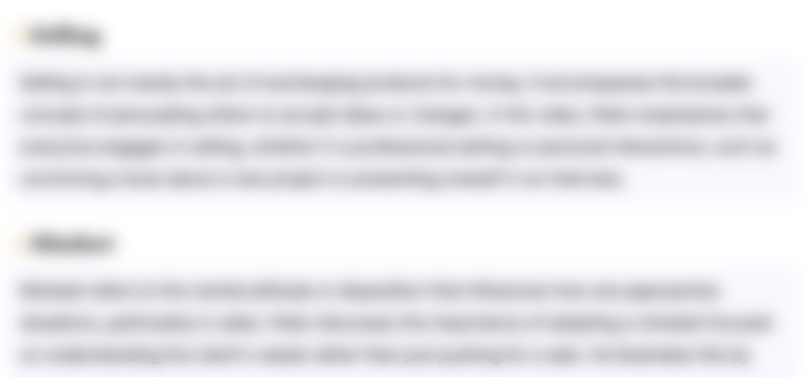
Этот раздел доступен только подписчикам платных тарифов. Пожалуйста, перейдите на платный тариф для доступа.
Перейти на платный тарифHighlights
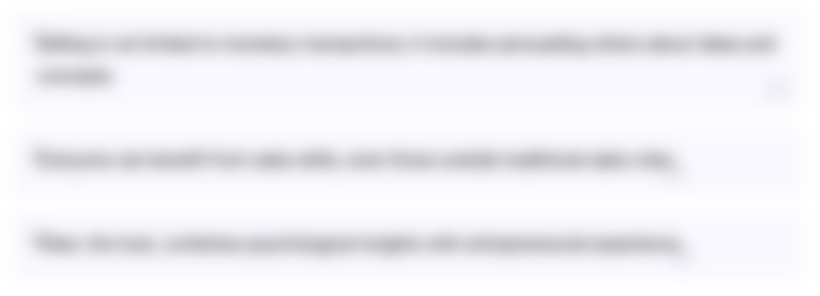
Этот раздел доступен только подписчикам платных тарифов. Пожалуйста, перейдите на платный тариф для доступа.
Перейти на платный тарифTranscripts
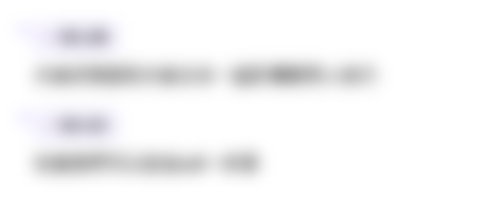
Этот раздел доступен только подписчикам платных тарифов. Пожалуйста, перейдите на платный тариф для доступа.
Перейти на платный тариф5.0 / 5 (0 votes)