Materials Science Mechanical Engineering - Part 4 Heat Treatment Explained
Summary
TLDRThis tutorial explains the forging process, highlighting how heated metal billets are shaped under pressure to align grain structure, improving strength and fatigue resistance. It contrasts forged parts with machined parts, showing how grain alignment in forging prevents cracks at critical points. The video also provides a tip for identifying forged parts by examining the flashing and grinding marks, which are wider and more pronounced than those on cast parts. The tutorial offers practical insights for distinguishing between forged and cast vehicle components.
Takeaways
- 😀 Heat treatments and hardening processes control the microstructure of materials, improving strength, durability, and resistance to fatigue.
- 😀 The crystal structure of metals, such as Body-Centered Cubic (BCC) and Face-Centered Cubic (FCC), significantly impacts material properties like ductility and toughness.
- 😀 Increasing carbon content in ferrous materials boosts hardness, but can decrease ductility, which is crucial for balancing material properties.
- 😀 Various heat treatment techniques such as tempering, normalizing, and annealing are used to refine material properties, such as reducing brittleness or increasing toughness.
- 😀 Advanced hardening processes like induction hardening, carburizing, and nitriding selectively harden materials to improve wear resistance while maintaining a tough core.
- 😀 Cryogenic hardening is used to convert retained austenite into martensite, enhancing the material's overall strength and stability.
- 😀 Hardness tests, such as Rockwell, Vickers, and Brinell, are used to measure the material's resistance to deformation, giving insight into its overall strength and durability.
- 😀 Forged parts, like connecting rods, exhibit aligned grain structures that increase their fatigue resistance, unlike cast or machined parts with weaker spots.
- 😀 The cooling rate during heat treatment significantly affects the material’s final structure and properties; slow cooling tends to result in softer, more ductile materials.
- 😀 Materials with smaller grain sizes are typically stronger because their crystal structures resist movement, while larger grains offer increased ductility and flexibility.
Q & A
What is the purpose of heat treatment in materials, specifically metals?
-Heat treatment is used to modify the crystal structure of metals, improving their hardness, strength, and other mechanical properties. By heating and cooling metals in specific ways, we can influence the size and orientation of the crystalline grains, resulting in different material properties such as increased hardness or enhanced ductility.
How do different crystal structures (FCC, BCC, and HCP) affect the material's properties?
-Different crystal structures affect a material's ductility, toughness, and response to temperature. Face-Centered Cubic (FCC) structures are generally more ductile and resistant to brittle fracture at low temperatures, while Body-Centered Cubic (BCC) structures can become brittle at lower temperatures. Hexagonal Close-Packed (HCP) structures are typically less ductile than FCC but stronger in some cases.
What is the relationship between grain size and material strength?
-Smaller grains in a material lead to higher strength because they create barriers that hinder the movement of dislocations within the crystal lattice. This makes the material more resistant to deformation. Conversely, larger grains tend to make the material more ductile but less strong.
How does carbon content influence the hardening of steel?
-Carbon content significantly affects the hardness of steel. As the carbon content increases, the steel's ability to harden improves, leading to a higher Rockwell C hardness. Carbon interacts with the crystal structure, increasing strength by making it more difficult for the material to deform.
What are quenching and tempering in the heat treatment process?
-Quenching involves rapidly cooling a heated material, typically in water, oil, or other media, to lock in a specific crystal structure like martensite. Tempering follows quenching and involves reheating the material to a lower temperature to reduce brittleness and increase toughness while maintaining strength.
What role does cooling rate play in the hardening process?
-The cooling rate is crucial in determining the final crystal structure. A rapid cooling rate, such as quenching, forms hard structures like martensite. Slower cooling rates can result in more ductile phases like pearlite or bainite, which are typically used to balance strength and toughness.
What are localized hardening methods like induction hardening, and what are their advantages?
-Localized hardening methods, such as induction hardening, focus heat treatment on the surface of the material, creating a hard, wear-resistant outer layer while maintaining a tough, ductile core. This is ideal for parts that need high surface strength, like shafts or gears, to resist wear and fatigue without compromising internal strength.
What is the difference between a forged part and a cast part in terms of grain structure?
-Forged parts typically have a grain structure that follows the shape of the part, providing superior strength and fatigue resistance. In contrast, cast parts have grains that are oriented in a less controlled manner, which can lead to weaker points where cracks may form, especially at the surface.
What is the significance of austenite in the heat treatment of steel?
-Austenite is a high-temperature phase of steel that plays a key role in heat treatment. When steel is heated to the austenitizing temperature, the carbon atoms dissolve into the iron, creating a structure that can be rapidly cooled to form martensite, a very hard and strong phase. The transformation from austenite to martensite is crucial for creating high-strength steels.
How does cold working affect a material's properties?
-Cold working involves deforming a material at temperatures below its recrystallization point. This process increases strength by introducing dislocations and work hardening but decreases ductility. Cold-rolled materials, for example, tend to have tighter tolerances but may develop residual stresses that cause dimensional changes during machining.
Outlines
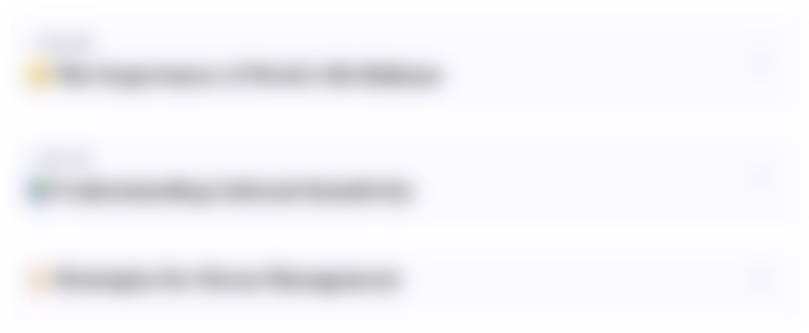
Этот раздел доступен только подписчикам платных тарифов. Пожалуйста, перейдите на платный тариф для доступа.
Перейти на платный тарифMindmap
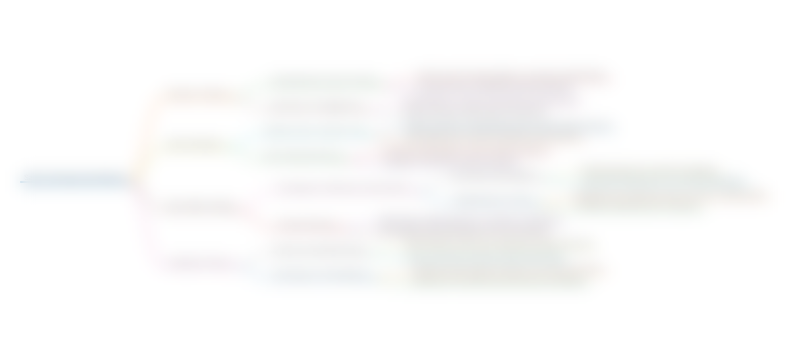
Этот раздел доступен только подписчикам платных тарифов. Пожалуйста, перейдите на платный тариф для доступа.
Перейти на платный тарифKeywords
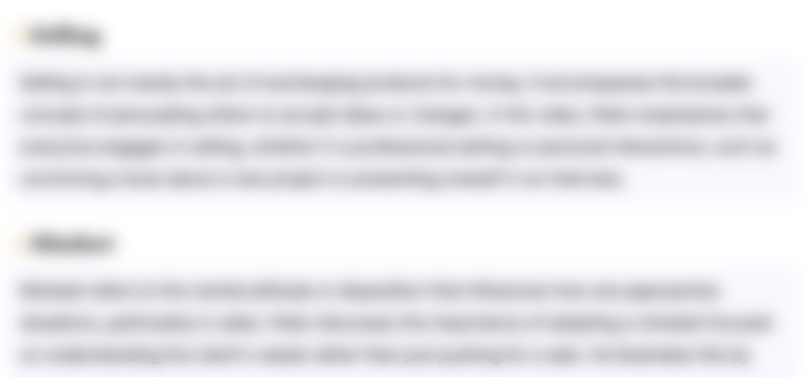
Этот раздел доступен только подписчикам платных тарифов. Пожалуйста, перейдите на платный тариф для доступа.
Перейти на платный тарифHighlights
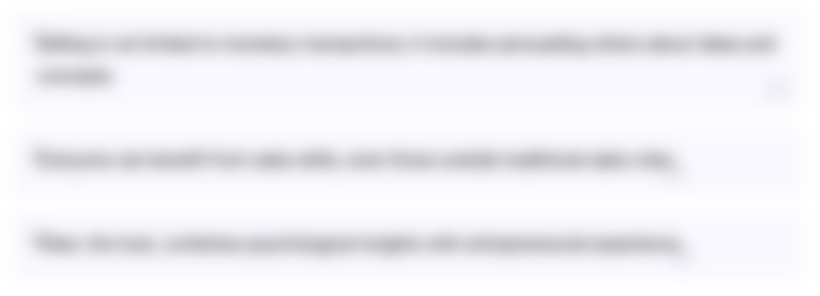
Этот раздел доступен только подписчикам платных тарифов. Пожалуйста, перейдите на платный тариф для доступа.
Перейти на платный тарифTranscripts
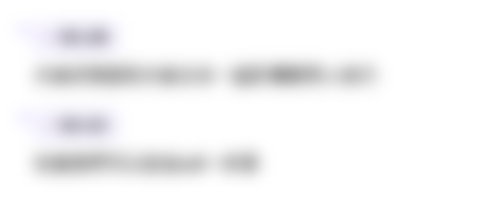
Этот раздел доступен только подписчикам платных тарифов. Пожалуйста, перейдите на платный тариф для доступа.
Перейти на платный тарифПосмотреть больше похожих видео
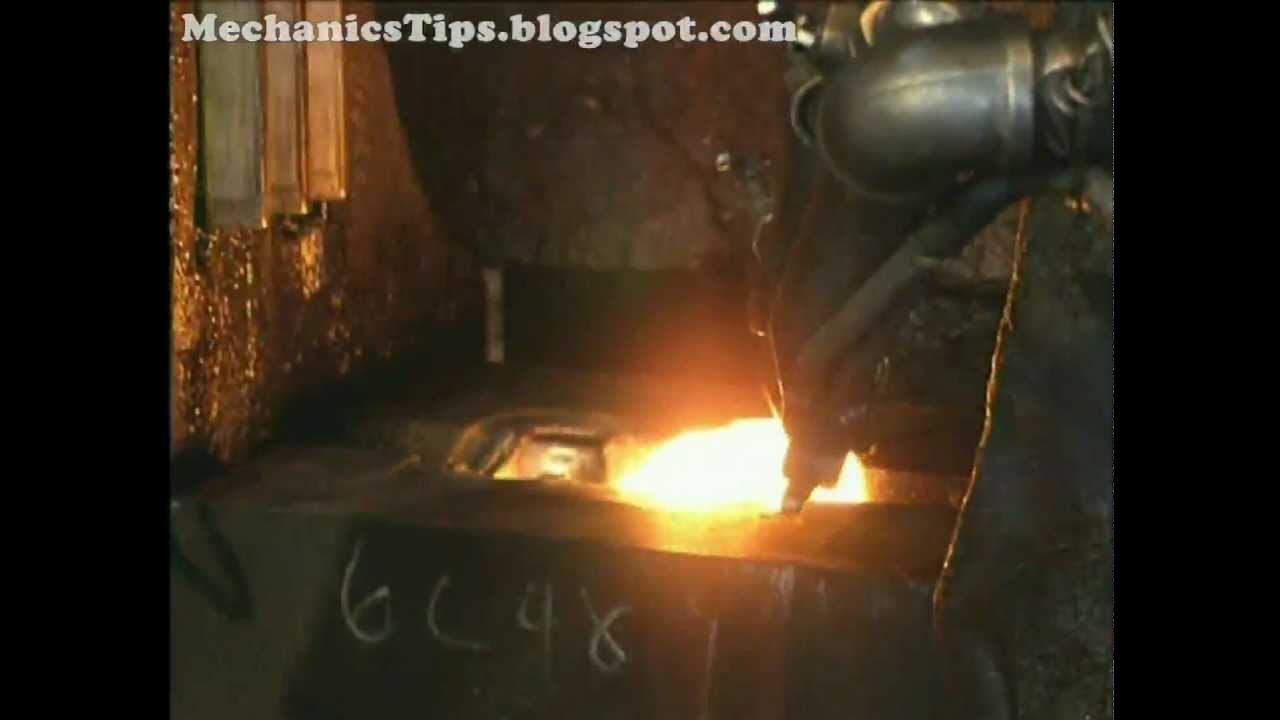
Die forging process(open and closed die)

Open die forging
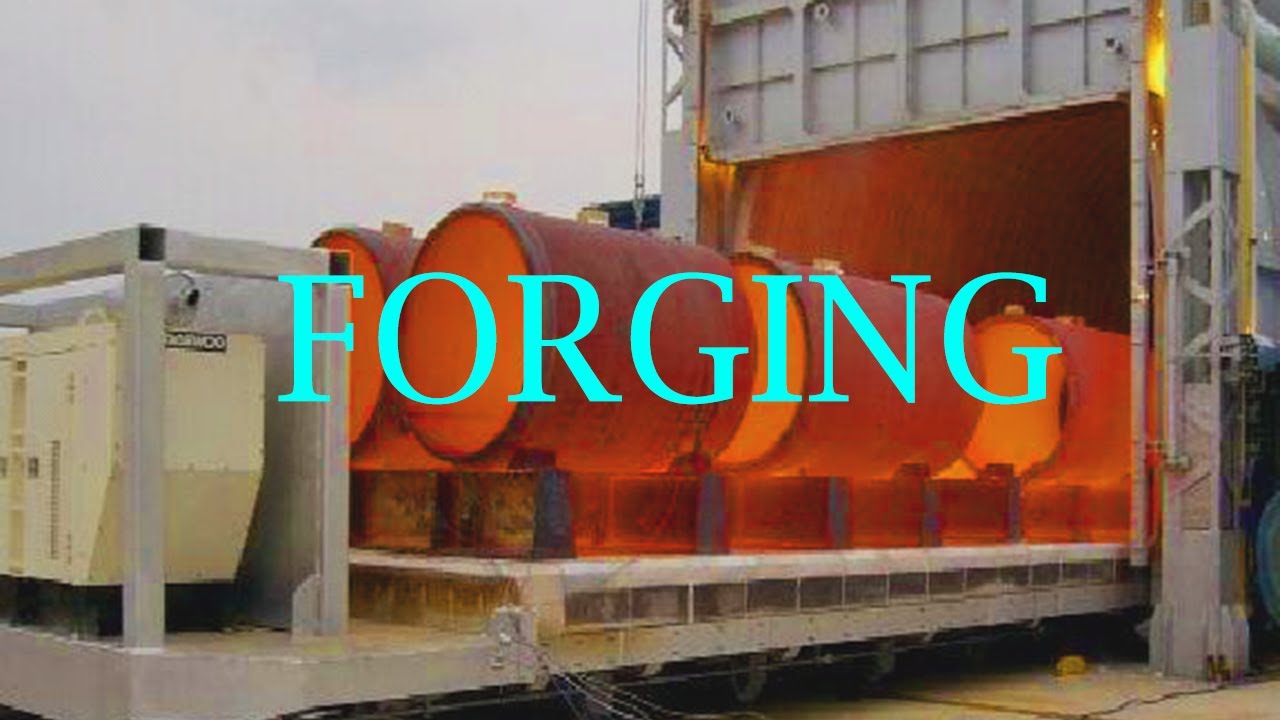
Teknik Pembentukan Logam (Forging)

HUBUNGAN PERHITUNGAN TEKANAN HIDROSTATIS TERHADAP DESAIN BENDUNGAN

Telecurso 2000 - Processos de Fabricação - 09 Casa de ferreiro, espeto de aço
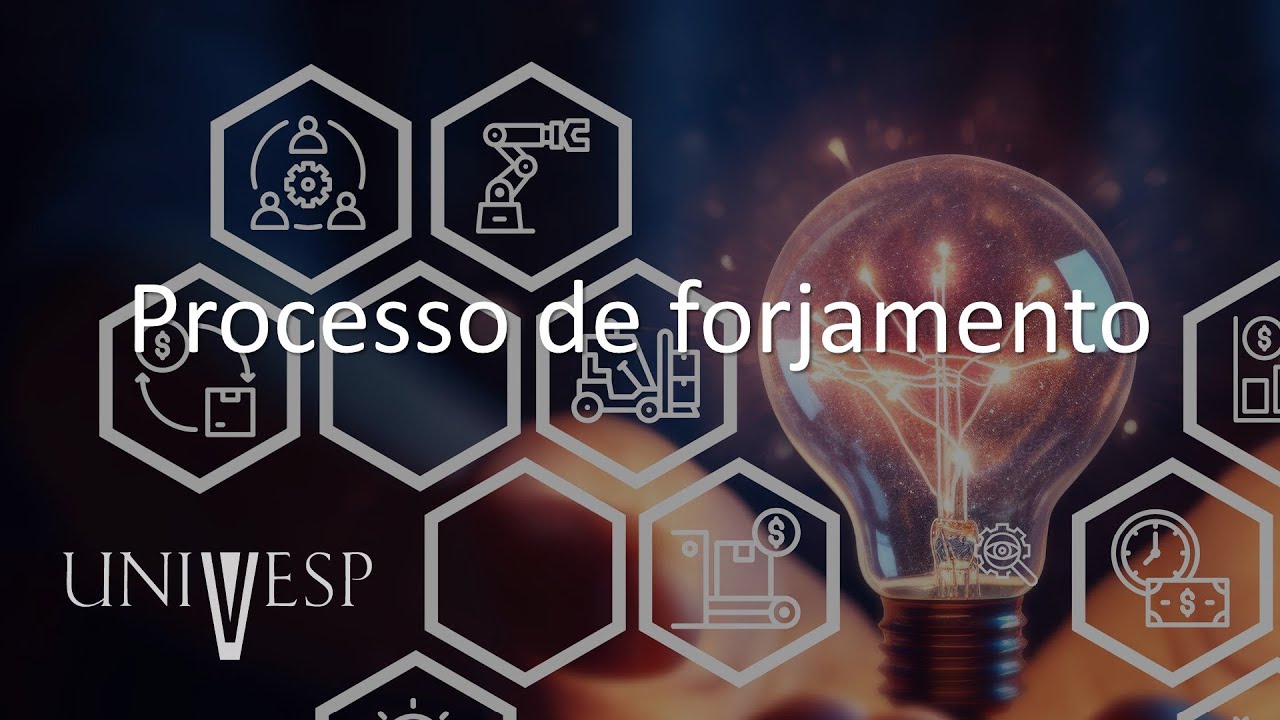
Materiais e Processos de Fabricação para Engenharia de Produção - Processo de forjamento
5.0 / 5 (0 votes)