Building a CNC Mill/Router - Part 4
Summary
TLDRIn this CNC build update, the creator discusses progress on assembling the Z and Y axes, 3D printing parts, and adding a thick aluminum plate as a cutting bed. They describe drilling mounting holes, wiring electronics, and configuring a Duet 3 6HC control board for motor control. The creator plans to build an enclosure to contain metal chips and improve safety. Despite challenges like cutting aluminum sheets with improper tools, they are pleased with the setup and demonstrate the machine’s movement using the web interface. Final wiring and enclosure work are still pending.
Takeaways
- 🔧 The Z-axis and part of the Y-axis for the CNC build were completed, with additional time spent 3D printing a base plate to catch cutting chips.
- 🛠️ A reprinted Z-axis motor mount using resin is stronger and more heat-resistant than the previous PETG part, with added mounting for a limit switch to home the Z-axis.
- 💡 The creator initially struggled to find a large, thick sheet for the cutting bed but later purchased a 20mm thick cast aluminum tooling plate for optimal flatness and durability.
- 🔩 After marking the mounting positions with tape and layout fluid, holes were drilled in the aluminum plate to align it with the Y-axis bearings, ensuring smooth movement.
- ⚙️ The electronics setup involves routing wires neatly behind the gantry, with only one drag chain required, simplifying the build by reducing moving parts.
- 🔌 The motors and power supply were wired up, using a Duet 3 6HC board capable of handling the Nema 34 motors without needing external drivers.
- 📱 The CNC machine can be controlled via a web interface using the Duet controller, allowing for easy motor control from any device, including a phone or tablet.
- 🔒 The creator plans to build an enclosure to contain metal cutting chips, with extrusions and aluminum sheets used for the walls and LED lights added to improve visibility inside.
- ⚡ The CNC build still requires final wiring checks, securing bolts with thread lock, and completing the spindle wiring before it can be fully operational.
- 💻 Preloaded G-code demonstrates the machine's functionality, although the spindle wiring and final setup still need to be completed for full operation.
Q & A
What purpose does the base plate being printed serve?
-The base plate will sit between the extrusions and is designed to catch cutting chips during the CNC process. It also creates a nice tabletop surface for the machine.
Why did the creator choose to reprint the Z-axis motor mount in resin?
-The creator reprinted the Z-axis motor mount in resin on the Form 4 because the resin part is stronger and more heat resistant than the original PETG part, which is important if the motor generates heat.
What decision was made regarding the cutting bed material?
-Initially, the creator considered using a smaller thick sheet in the center and a larger thinner sheet for the full cutting area but eventually decided to buy a large 20mm thick cast aluminum tooling plate for a flat surface finish.
How were the mounting holes for the aluminum tooling plate created?
-The creator marked the mounting holes' locations using tape and blue layout fluid. Then, they used a metal scribe to mark exact positions, center-punched them, drilled with 3mm and 6mm bits, and countersunk the holes to ensure the bolt heads sit flush.
What are the advantages of using a fixed gantry machine for the CNC build?
-In a fixed gantry machine, only one motor moves, and the X and Y motors are fixed in position, which simplifies wiring since it requires only one drag chain and reduces the complexity of the setup.
Which control board was chosen for the CNC machine and why?
-The creator chose the Duet 3 6HC board, recommended by YouTuber Ivan Miranda. This board is typically used for 3D printers but is capable of handling high enough current for the Nema 34 motors without requiring external stepper motor drivers, simplifying the build.
How does the Duet web interface help in controlling the CNC machine?
-The Duet web interface allows the creator to control the machine remotely from any computer, tablet, or phone, which makes operating and adjusting the settings far easier compared to older systems like Mach 3.
What challenge did the creator face when cutting the hole for the X-axis motor, and how was it resolved?
-The creator lacked the proper tools, such as a handheld jigsaw, and had to use tin snips and a file to cut the hole, which was time-consuming and didn’t provide the best finish. Despite this, the hole was correctly sized, but the creator plans to buy better tools for future tasks.
How did the creator ensure better lighting inside the CNC machine enclosure?
-After noticing the enclosure became dark inside, the creator installed small LED battery-powered lights inside the enclosure to brighten the workspace and make the machine visible during operation.
What is still left to complete on the CNC machine after the fourth video update?
-The creator still needs to finish the enclosure, secure all the wiring, add a clear PPC door to the front, and wire up the spindle. Additional checks will be made to ensure that all bolts are tightened and everything is working smoothly.
Outlines
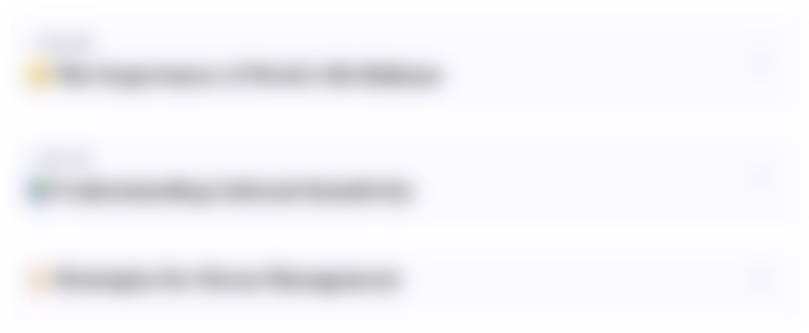
Этот раздел доступен только подписчикам платных тарифов. Пожалуйста, перейдите на платный тариф для доступа.
Перейти на платный тарифMindmap
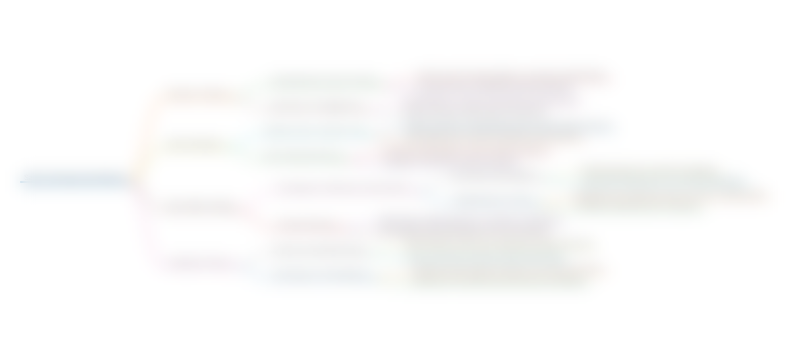
Этот раздел доступен только подписчикам платных тарифов. Пожалуйста, перейдите на платный тариф для доступа.
Перейти на платный тарифKeywords
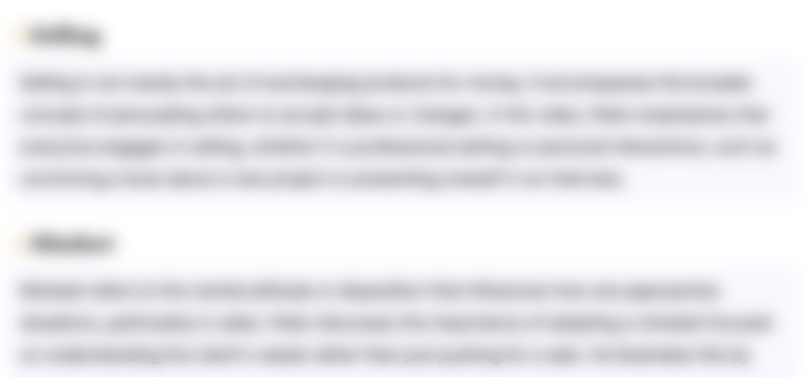
Этот раздел доступен только подписчикам платных тарифов. Пожалуйста, перейдите на платный тариф для доступа.
Перейти на платный тарифHighlights
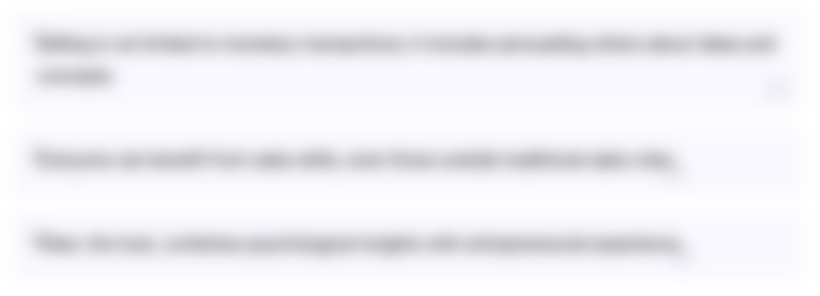
Этот раздел доступен только подписчикам платных тарифов. Пожалуйста, перейдите на платный тариф для доступа.
Перейти на платный тарифTranscripts
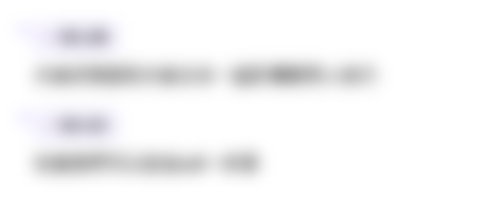
Этот раздел доступен только подписчикам платных тарифов. Пожалуйста, перейдите на платный тариф для доступа.
Перейти на платный тарифПосмотреть больше похожих видео

Cara membuat mesin CNC Router
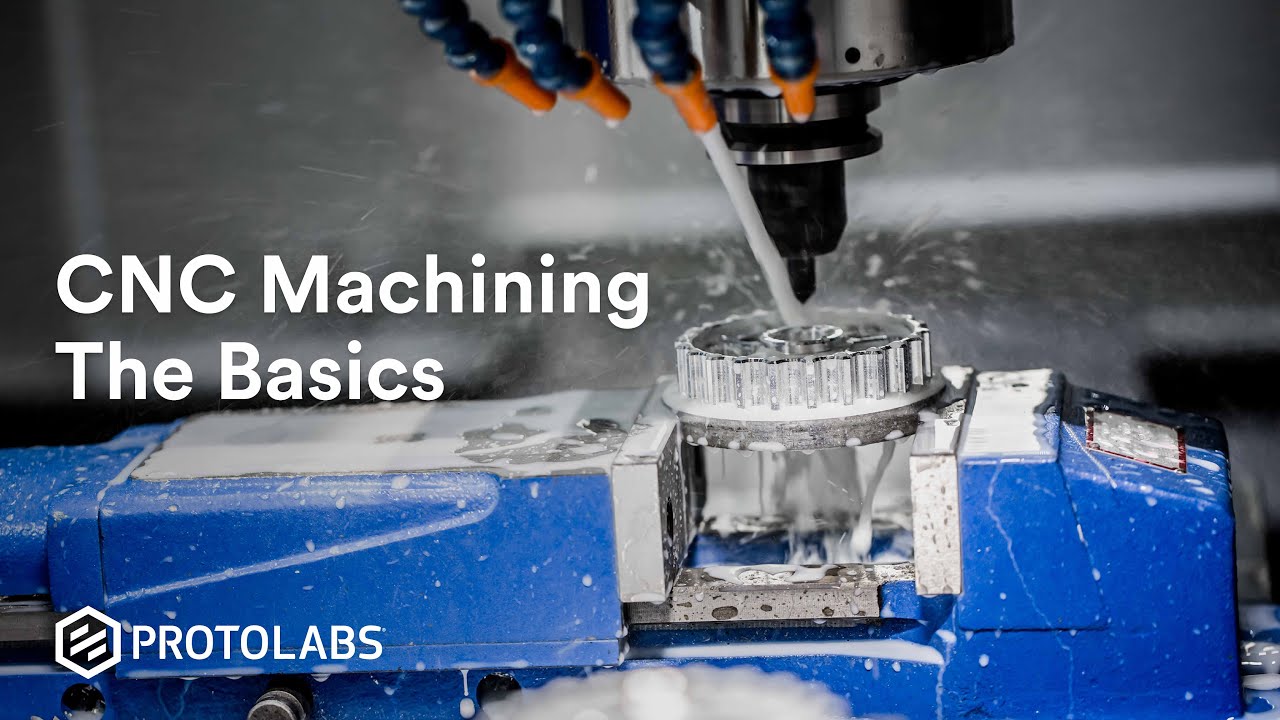
CNC machining - What is it and How Does it Work? (Must Know Basics)
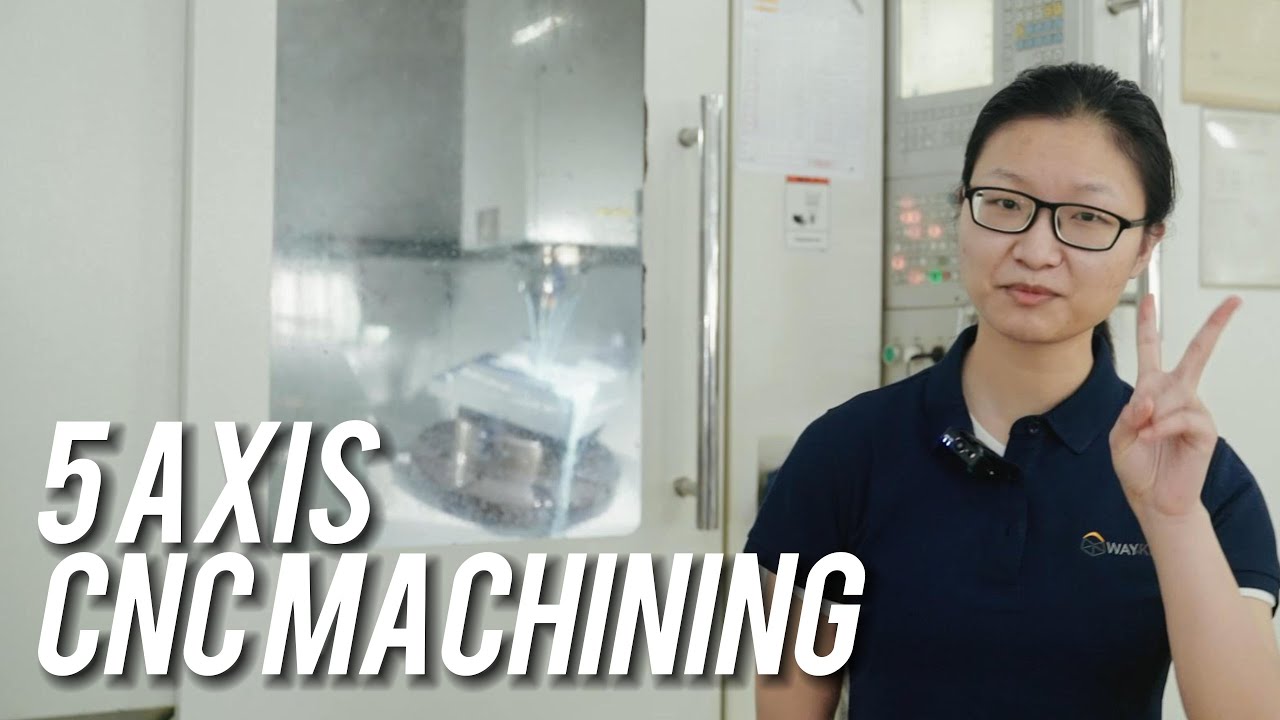
5 Axis CNC Machining For Your Parts | WayKen Rapid Manufacturing
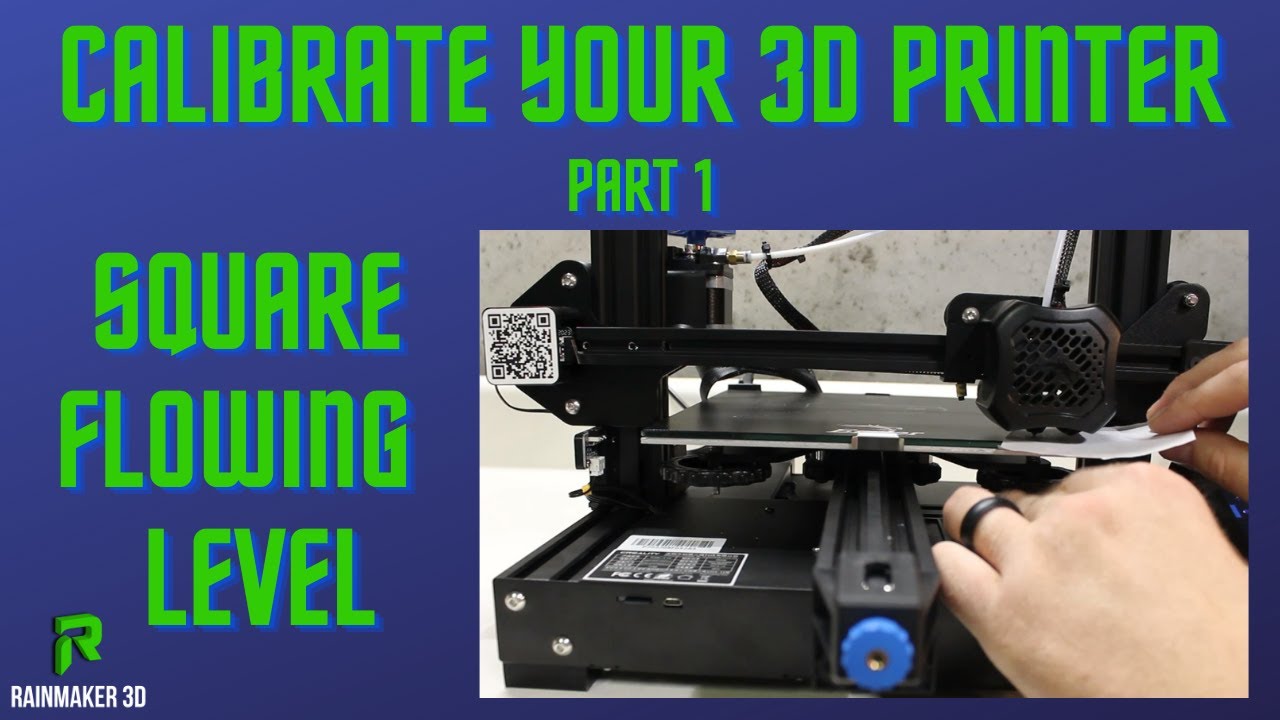
3D Printer Frame Check - Calibrating your 3D Printer Part 1 - Ender 3 V2

Computer Numerical Control

What is VAT Photopolymerization (SLA, DLP, CDLP)? | Dassault Systèmes
5.0 / 5 (0 votes)