Lessons learnt while inspecting steam turbine blades
Summary
TLDRThe speaker discusses their group's experiences inspecting turbine blades over the past two years, highlighting challenges and insights gained. They found numerous blade defects, exceeding initial expectations, and compared various non-destructive testing (NDT) techniques. The main methods explored include fluorescent magnetic particle inspection (MPI), penetrant inspection, eddy current inspection, and phased array ultrasound. While eddy current inspection proved most sensitive, phased array is the only in-situ method, useful for quick assessments. The summary compares the effectiveness of each technique, emphasizing the importance of risk management and inspector competency in detecting blade defects.
Takeaways
- 🔍 Significant increase in defective blades found during inspections over the last two years.
- 🛠 Various NDT (Non-Destructive Testing) techniques were evaluated, including fluorescent magnetic particle inspection, fluorescent penetrant inspection, eddy current inspection, and phased array inspection.
- 💡 High-stress concentrations on blades tend to be located in specific areas depending on whether it's the pressure or suction side.
- 📉 Cracks and defects are primarily found where the highest stress concentrations exist, but their specific characteristics vary based on the mechanism causing the cracking.
- 🚁 Phased array inspection is the most commonly used in-situ inspection technique for last-stage blades, offering the ability to inspect without rotor removal.
- 📈 Eddy current inspections, particularly with modern arrays, are becoming more effective than traditional MPI and dye penetrant inspections.
- 🔧 Different stations and case studies showed varying effectiveness of NDT techniques in identifying blade defects, with some missing significant cracks.
- ⚙ Improvements in NDT techniques, especially with MPI, are needed, including better inspector training and equipment modifications to detect smaller defects.
- 🧪 Shot peening of blade surfaces can close surface cracks, making them harder to detect with traditional MPI and dye penetrant methods.
- 📊 Eddy current inspection has proven to find more defects than other methods, especially on older, corroded blades, while phased array remains the only viable in-situ technique despite being the least sensitive.
Q & A
What were the main challenges faced by the group during the inspections?
-The main challenges included finding a higher number of defective blades than originally expected, determining where the stress concentrations and cracks occurred on the blades, and evaluating the effectiveness of different NDT techniques.
What are the common areas where high stress concentrations were found on the blades?
-High stress concentrations were found on the suction side of the blade root, typically in the center, and on the pressure side toward the extreme ends of the blade root.
Which NDT techniques were most commonly used by the group during inspections?
-The group commonly used fluorescent magnetic particle inspection (MPI), fluorescent penetrant inspection, eddy current inspection, and phased array ultrasound inspection.
Why is phased array ultrasound used, and what are its benefits?
-Phased array ultrasound is used because it is the only NDT technique that can inspect blades in situ. It provides a practical solution for quick inspections during outages, helping manage the risk of defects without removing the blades.
What were the limitations of MPI and dye penetrant inspection in detecting defects?
-MPI and dye penetrant inspections require cracks to be fairly open at the surface. Factors like shot peening by manufacturers can close surface cracks, making them harder to detect with these methods.
How did the group evaluate the effectiveness of the NDT techniques?
-The group compared the performance of four NDT techniques by analyzing how well each one detected defects. They looked at defect size, location, and the overall sensitivity of each method across different stations and blade conditions.
What was the performance of eddy current inspection in comparison to other techniques?
-Eddy current inspection was found to be the most sensitive technique, detecting even very small defects, some less than 1 millimeter in length. However, it requires specific probes and surface preparation.
What was the performance of phased array inspection compared to other methods?
-Phased array inspection detected fewer defects compared to other techniques, but it is the only method that can be used in situ. Despite finding fewer defects, it was effective for managing risk during inspections.
What were some of the improvements suggested for MPI techniques?
-Improvements for MPI included better surface preparation, improved inspector training and competence, and enhanced awareness of what defects to look for, which improved the detection of small defects.
What conclusions did the group draw from their experience with NDT techniques for blade inspection?
-The group concluded that no single NDT technique guarantees defect-free blades. However, eddy current proved to be the most sensitive, while phased array is valuable for in-situ inspections. The key is understanding each technique's limitations and using them based on the condition of the blades.
Outlines
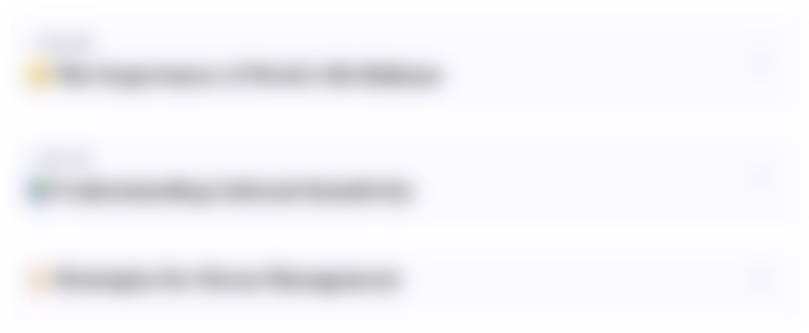
Этот раздел доступен только подписчикам платных тарифов. Пожалуйста, перейдите на платный тариф для доступа.
Перейти на платный тарифMindmap
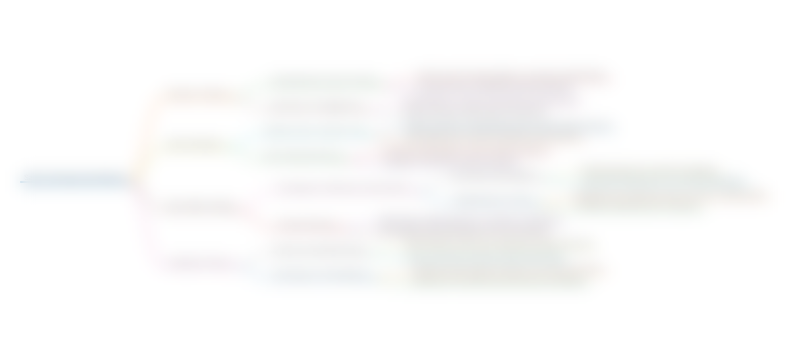
Этот раздел доступен только подписчикам платных тарифов. Пожалуйста, перейдите на платный тариф для доступа.
Перейти на платный тарифKeywords
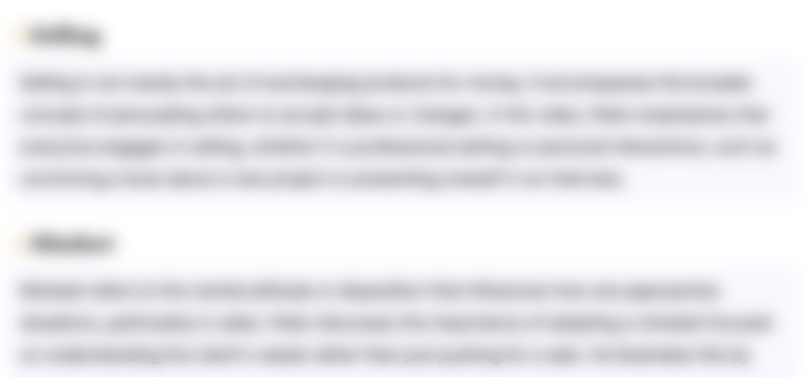
Этот раздел доступен только подписчикам платных тарифов. Пожалуйста, перейдите на платный тариф для доступа.
Перейти на платный тарифHighlights
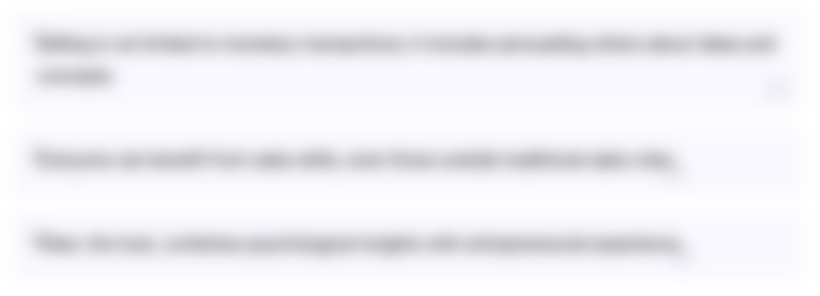
Этот раздел доступен только подписчикам платных тарифов. Пожалуйста, перейдите на платный тариф для доступа.
Перейти на платный тарифTranscripts
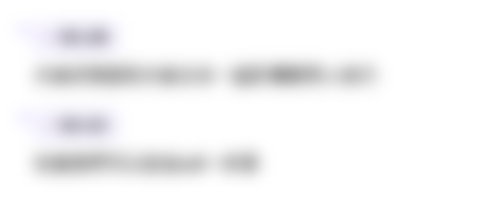
Этот раздел доступен только подписчикам платных тарифов. Пожалуйста, перейдите на платный тариф для доступа.
Перейти на платный тарифПосмотреть больше похожих видео
5.0 / 5 (0 votes)