Using a Button Cutter to High Feed Ramp a Mold Core, then Plunge Finishing for Shortest Cycle Time
Summary
TLDRThis video from Des Prés Tech Center explores different milling techniques for roughing and finishing core shapes in machining. It compares high feed ramping with a button cutter versus a high feed cutter, highlighting productivity and surface quality. The video also demonstrates three finishing methods: waterline profile milling with a bull nose cutter, the same with a ball nose cutter for faster cycle times, and plunge finishing with a bull nose for accessing tight corners and reduced tool pressure. The discussion covers the pros and cons of each method, providing insights for choosing the right tool and technique.
Takeaways
- 🛠️ The video discusses two machining approaches: roughing and finishing, using different types of cutters.
- ⏱️ Roughing with a button cutter is compared to high feed cutters, showing productivity and practical considerations.
- 🔩 Button cutters leave smaller scallops on sloped surfaces compared to high feed cutters, which is beneficial for semi-finishing and finishing.
- 💰 Economically, button cutters with double sides provide 12 usable indexes per insert, making them a strong option over high feed cutters.
- 📉 The roughing process with a button cutter took 8 minutes and 47 seconds, which is longer than high feed but results in a smoother surface.
- 🛠️ Three different finishing approaches are demonstrated: bull nose cutter with water line profile milling, ball nose cutter, and bull nose cutter with plunge finishing.
- ⏲️ Using a ball nose cutter significantly reduced the cycle time to 43 minutes and 30 seconds compared to the bull nose cutter.
- 🔍 The ball nose cutter provides a good finish but may require a secondary tool for smaller radii in corners.
- 🔩 The bull nose cutter in plunge finishing approach reduced cycle time by 75% compared to the profile milling approach.
- 🏁 The video concludes by summarizing the advantages of button cutters for roughing and bull nose cutters for finishing tapered walls over ball nose or barrel type cutters.
Q & A
What are the two main machining approaches discussed in the script?
-The two main machining approaches discussed are roughing and finishing.
What type of cutter is suggested as an alternative to high feed cutters for roughing?
-A button cutter is suggested as an alternative to high feed cutters for roughing.
How does the button cutter compare to a high feed cutter in terms of productivity?
-The button cutter provides a smoother surface with smaller scallops and has more usable cutting edges, which can be more economical and efficient for certain applications.
What are the three different finishing approaches demonstrated in the script?
-The three different finishing approaches demonstrated are using a bull nose cutter with a water line profile milling approach, using a ball nose cutter, and using a bull nose cutter with a plunge finishing approach.
Why might a bull nose cutter be preferred over a ball nose cutter for finishing?
-A bull nose cutter allows for better access to tight corners and intersections, and it generates less tool pressure, which can result in fewer issues with tool deflection and the need for recutting.
What is the cycle time for roughing with a button cutter as mentioned in the script?
-The cycle time for roughing with a button cutter is 8 minutes and 47 seconds.
What is the advantage of using a ball nose cutter over a bull nose cutter in terms of cycle time?
-The ball nose cutter significantly reduces the cycle time compared to a bull nose cutter, as demonstrated by the 43 minutes and 30 seconds cycle time versus the longer time taken by the bull nose cutter.
What is the potential downside of using a ball nose cutter for finishing?
-The potential downside of using a ball nose cutter is that it may not be able to access tight corners as effectively as a bull nose cutter, requiring a secondary tool to finish those areas.
How does the plunge finishing approach with a bull nose cutter compare to the water line profile milling approach in terms of cycle time?
-The plunge finishing approach with a bull nose cutter is about four times faster than the water line profile milling approach, reducing the cycle time by 75%.
What are the economic considerations when choosing between a button cutter and a high feed cutter?
-Economic considerations include the number of usable cutting edges, the depth of cut the tool can take, and the smoother surface left by the button cutter, which may require less finishing work.
Outlines
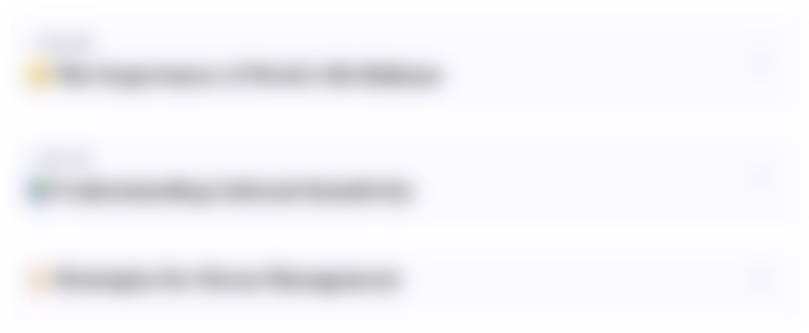
Этот раздел доступен только подписчикам платных тарифов. Пожалуйста, перейдите на платный тариф для доступа.
Перейти на платный тарифMindmap
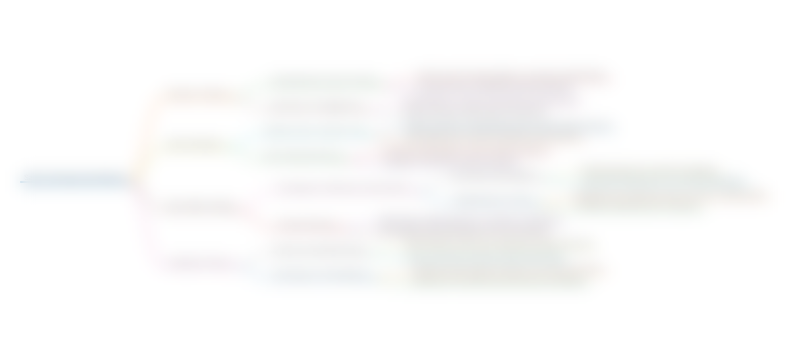
Этот раздел доступен только подписчикам платных тарифов. Пожалуйста, перейдите на платный тариф для доступа.
Перейти на платный тарифKeywords
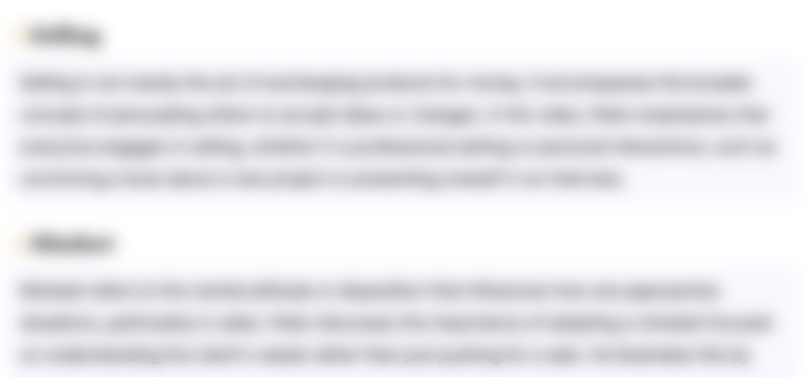
Этот раздел доступен только подписчикам платных тарифов. Пожалуйста, перейдите на платный тариф для доступа.
Перейти на платный тарифHighlights
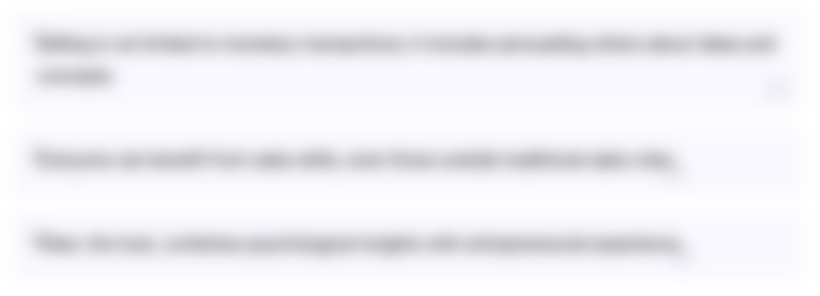
Этот раздел доступен только подписчикам платных тарифов. Пожалуйста, перейдите на платный тариф для доступа.
Перейти на платный тарифTranscripts
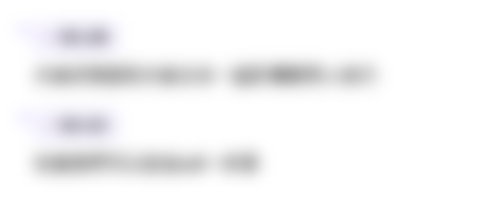
Этот раздел доступен только подписчикам платных тарифов. Пожалуйста, перейдите на платный тариф для доступа.
Перейти на платный тарифПосмотреть больше похожих видео

HEAVY DUTY LATHES. Most Mesmerizing Collection of CNC Machine Processes.
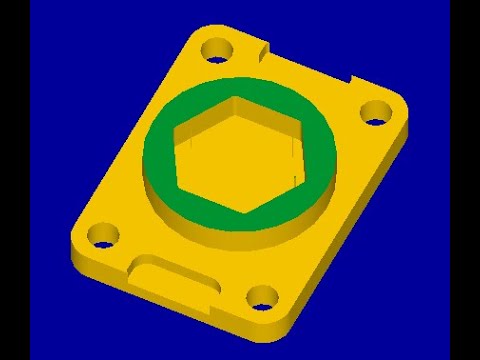
Tutorial Mastercam X5 CNC Mill / Fraish

Cara Pengefraisan Balok Rata Bersama Gick Sugiyarna
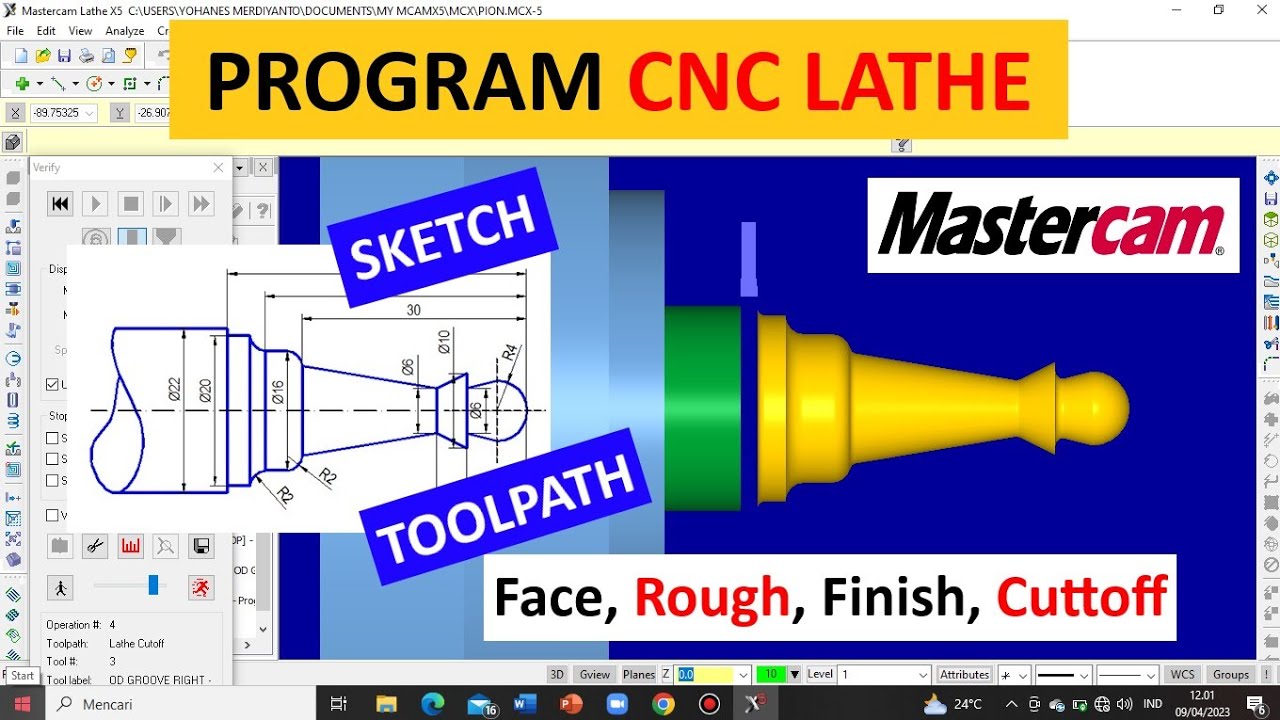
TUTORIAL MASTERCAM X5 MEMBUAT PION || CNC Turning (Lathe) || Simpel & Mudah dipahami !!

Milling machine tutorial - cutter selection, speeds and feeds, coolant, high speed machining
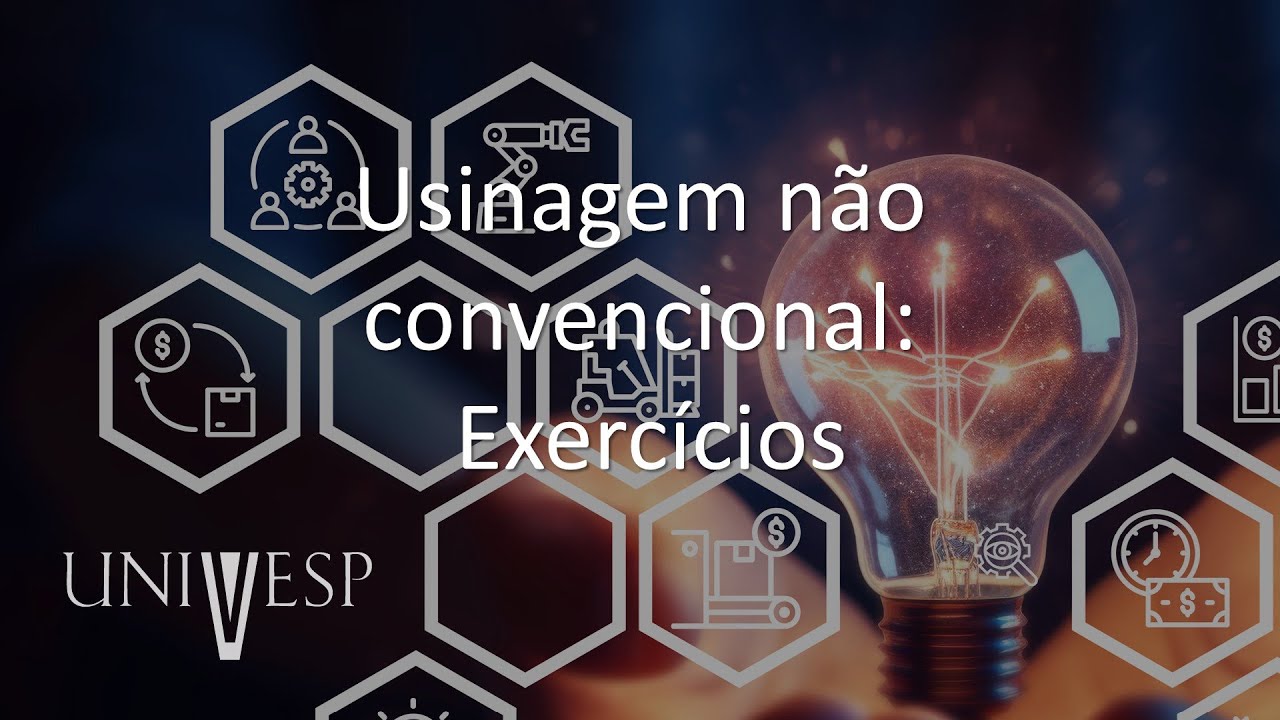
Materiais e Processos de Fabricação para Engenharia de Produção - Usinagem não convencional...
5.0 / 5 (0 votes)