5 Tips for Working With Aluminium HIGH PRESSURE DIE CASTING | Explained - Serious Engineering: Ep 28
Summary
TLDRThis video provides an in-depth look at high pressure die casting (HPDC), detailing the process of injecting molten metals like aluminum into a die under intense pressure. Host Gordon Stiles emphasizes the speed and precision required for successful die casting, offering five essential tips for optimizing the process. These include using quality steel for tooling, avoiding prototype dies, maintaining consistent draft angles, ensuring proper post-machining support, and choosing common aluminum alloys. The video is a comprehensive guide for engineers, blending technical insight with practical advice for maximizing casting efficiency.
Takeaways
- 😀 High-pressure die casting (HPDC) is a process for producing large volumes of components from metals like aluminum, zinc, tin, magnesium, copper, and brass, and PVC.
- 😀 The HPDC process involves four key stages: slow closure of the chamber, forming a wavefront to remove air, rapid injection of molten metal, and high-pressure holding to ensure material fills all parts of the die.
- 😀 The injection speed in HPDC is extremely fast and violent, often taking mere milliseconds for molten metal to fill the die cavity.
- 😀 Proper die design is crucial in HPDC to avoid issues such as air entrapment, short shots, and porosity. If accumulators are malfunctioning or turned off, these problems are more likely.
- 😀 Prototype tooling in HPDC is not effective, as soft steel dies don’t last long. Instead, hardened tool steel, such as H13, should be used to withstand the high pressures and temperatures involved.
- 😀 Avoid designing parts with large holes or openings in the die that obstruct the flow of molten metal. These should be filled in the die and cut during post-machining.
- 😀 Maintain consistent wall thicknesses across the part in HPDC, with typical thicknesses ranging from 2mm to 8mm, but avoiding extremes is recommended.
- 😀 Always incorporate generous draft angles in die design. A minimum of 2 degrees of draft angle is recommended, but 5 degrees is ideal for easier part removal.
- 😀 Never ask your die maker to add draft angles after the product design has been completed. The part should be designed with draft angles from the outset, especially in modern CAD systems.
- 😀 For post-machining, include three leveling pads in the design for proper part clamping. These pads ensure the part is held efficiently during machining and respects Geometric Dimensioning and Tolerancing (GD&T).
- 😀 Use common aluminum alloys like ADC10 (A380) or ADC12 (A383) for HPDC, as these alloys offer optimal strength and filling characteristics, with reduced porosity and hot cracking.
- 😀 Always insist on using a trimming die to remove overflows from the part after casting, or alternatively, use CNC machining for low-quantity runs to prevent damage to the part.
Q & A
What is High Pressure Die Casting (HPDC)?
-High Pressure Die Casting (HPDC), also known as PDC, is a manufacturing process used to produce metal parts in high volumes. It involves injecting molten metal, such as aluminum, zinc, tin, magnesium, copper, or brass, into a die under high pressure.
Why is the PDC process often misunderstood?
-The PDC process is often misunderstood because people may oversimplify it, thinking it is just about pouring molten metal into a die, waiting for it to cool, and then removing the finished part. In reality, it is a complex and fast process that requires careful design and precise control.
What are the four stages of the PDC injection process?
-The four stages of PDC injection are: 1) Closing off the chamber opening with the plunger. 2) The plunger moves slowly to create a wavefront that removes air from the shot chamber. 3) The plunger violently pushes the shot into the cavity. 4) The high-pressure hold ensures the material fills the die and compacts air trapped in the molten metal.
Why is the fill time in PDC so short?
-The fill time is short because when molten metal, such as aluminum, comes into contact with the relatively cold die, it quickly solidifies. The die walls can reach temperatures up to 400-450°C in just one second due to the heat transfer from the molten metal.
What problems can arise if the accumulators in the PDC machine are not functioning correctly?
-If the accumulators, which provide pressurized gas assistance, are not working or are turned off to save costs, issues like porosity (air bubbles) and short shots (incomplete castings) may occur, affecting the quality of the casting.
Why is prototype tooling not recommended for die casting?
-Prototype tooling, such as soft steel dies, does not withstand the harsh conditions of the PDC process. Though it may work for a few shots, it's more cost-effective to use proper production-grade tooling made from high-quality materials like H13 tool steel, which can handle around 100,000 cycles.
What should be considered when designing die castings with large holes or openings?
-For large holes or openings in die castings, it's recommended to fill them in the die and machine them later during post-production. This avoids flow obstructions that can cause air entrapment and other quality issues during casting.
What is the ideal draft angle for die casting designs?
-The ideal draft angle for die casting is between 2 to 5 degrees on both sides of cavities and cores. While 2 degrees is the minimum, a larger angle (around 5 degrees) is often recommended for better part release and ease of manufacturing.
Why should leveling pads be included in die casting designs?
-Leveling pads are essential for holding the casting in place during post-machining. They prevent the part from twisting during clamping and ensure precise machining by providing stable and consistent referencing for the fixture.
What aluminum alloys are commonly used in PDC, and why?
-The most commonly used aluminum alloys in PDC are ADC10 (A380) and ADC12 (A383). These alloys contain between 7.5% to 11.5% silicon, offering an optimal balance of strength and resistance to porosity, as well as excellent filling characteristics and resistance to hot cracking.
Outlines
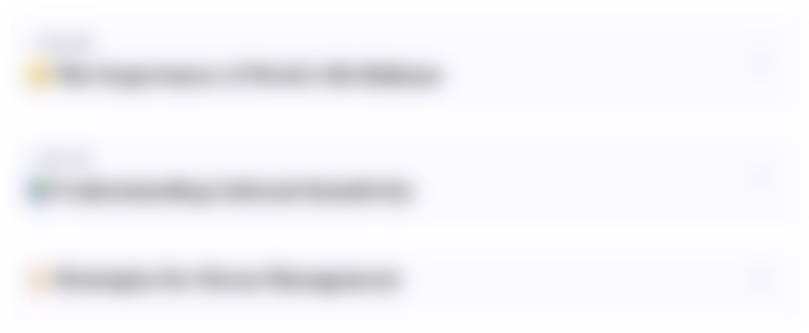
このセクションは有料ユーザー限定です。 アクセスするには、アップグレードをお願いします。
今すぐアップグレードMindmap
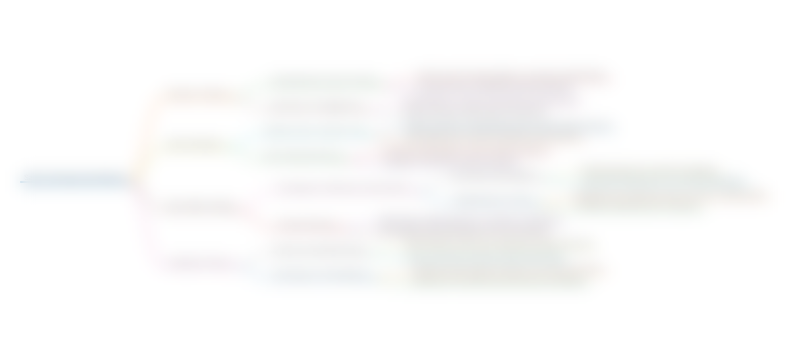
このセクションは有料ユーザー限定です。 アクセスするには、アップグレードをお願いします。
今すぐアップグレードKeywords
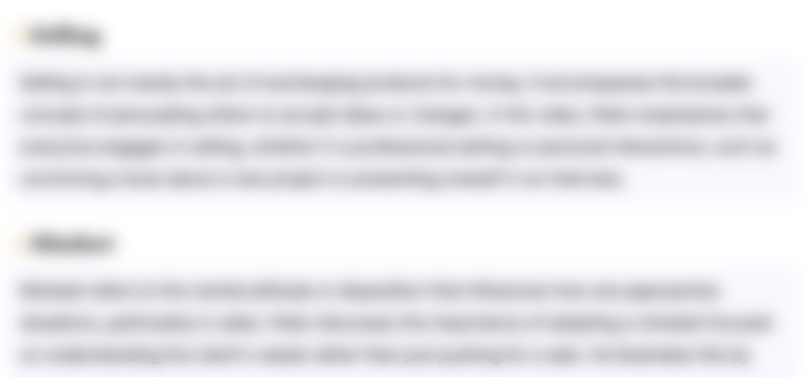
このセクションは有料ユーザー限定です。 アクセスするには、アップグレードをお願いします。
今すぐアップグレードHighlights
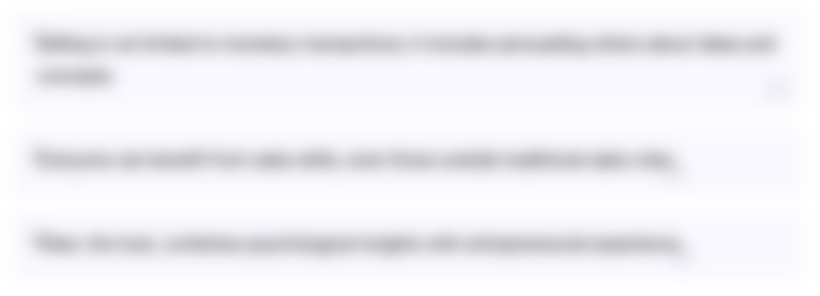
このセクションは有料ユーザー限定です。 アクセスするには、アップグレードをお願いします。
今すぐアップグレードTranscripts
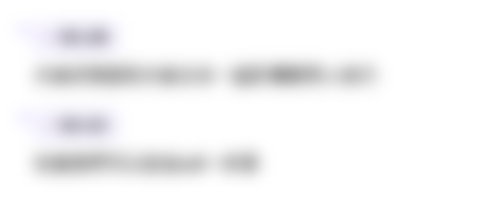
このセクションは有料ユーザー限定です。 アクセスするには、アップグレードをお願いします。
今すぐアップグレード5.0 / 5 (0 votes)