OEE Plus Die Casting Process Part #1 Pengantar HPDC
Summary
TLDRIn this video, the process of manufacturing automotive parts through high-pressure die casting (HPDC) is explored. The journey begins with the storage of aluminum ingots, which are melted in a furnace and then molded into precise automotive parts using specialized HPDC machines. The molten aluminum is injected into molds, forming strong, smooth-surfaced parts. The process is highly efficient and controlled, ensuring the production of high-quality components. The video also highlights the role of smart manufacturing technologies in optimizing the HPDC process, making it more precise and automated. The video provides a deep dive into the innovative world of aluminum manufacturing.
Takeaways
- π The video introduces the topic of smart manufacturing, focusing on the process of aluminum casting using high-pressure die casting machines.
- π It begins by explaining the raw materials used in the process, specifically aluminum ingots stored in a warehouse.
- π The aluminum ingots are melted in a furnace, reaching a temperature of 700Β°C, using various heat sources like LNG.
- π Once melted, the liquid aluminum is prepared for casting into automotive parts, including blocks, calipers, wheels, and shock absorbers.
- π The liquid aluminum is transferred to machines through a launder system and enters high-pressure die casting chambers.
- π The high-pressure die casting machine applies pressure to force the liquid aluminum into precisely shaped molds, creating accurate and durable parts.
- π The machine uses steel molds that form the aluminum into the desired automotive components.
- π After casting, the part is cooled, removed from the mold, and trimmed from the aluminum runners (excess material).
- π Additional finishing steps, such as painting, may be performed on the parts if needed to meet quality standards.
- π Quality control checks are done to ensure the aluminum parts meet required specifications and standards for automotive use.
- π The video concludes with a connection to the concept of smart manufacturing, emphasizing its application in high-pressure die casting machines.
Q & A
What is the main focus of the video?
-The video focuses on the high-pressure die-casting (HPDC) process used in aluminum processing, specifically for creating precise automotive parts. It also connects this process to smart manufacturing technologies.
What is the role of aluminum ingots in the manufacturing process?
-Aluminum ingots are the raw material used in the die-casting process. They are stored in the warehouse and then melted to create liquid aluminum, which is subsequently used to form automotive parts.
At what temperature is the aluminum melted during the process?
-The aluminum is melted at a temperature of 700Β°C in a furnace, using various heat sources like LNG to achieve the required temperature for the aluminum to become liquid.
How does the aluminum move through the production process?
-Once melted, the aluminum is transferred via a launder system to the die-casting machines, where it is injected into steel molds under high pressure to form the desired automotive parts.
What is the significance of the high-pressure die-casting (HPDC) machine?
-The HPDC machine applies high pressure to the molten aluminum, ensuring it fills the mold completely and forms a precise part. This process helps in achieving high-quality, smooth-surfaced automotive parts.
What types of parts are produced using the die-casting process?
-The die-casting process produces a variety of automotive parts, including brake calipers, wheels, shock absorbers, and other precision components used in vehicles.
How is the aluminum cooled and separated from the mold?
-After the aluminum solidifies, the mold is opened, and the part is removed. It is then cooled and separated from the runner, the aluminum channel used in the molding process.
What happens to the parts after they are removed from the mold?
-The parts undergo finishing processes, such as painting, if required, and are then subjected to quality control to ensure they meet the desired standards before being used in automotive manufacturing.
How does smart manufacturing play a role in the die-casting process?
-Smart manufacturing technologies help optimize the die-casting process by automating tasks, ensuring precision, improving efficiency, and providing real-time data for better decision-making and quality control.
What is the importance of quality control in the manufacturing process?
-Quality control ensures that the finished parts meet the required specifications and standards for strength, precision, and surface quality, which are essential for their use in automotive applications.
Outlines
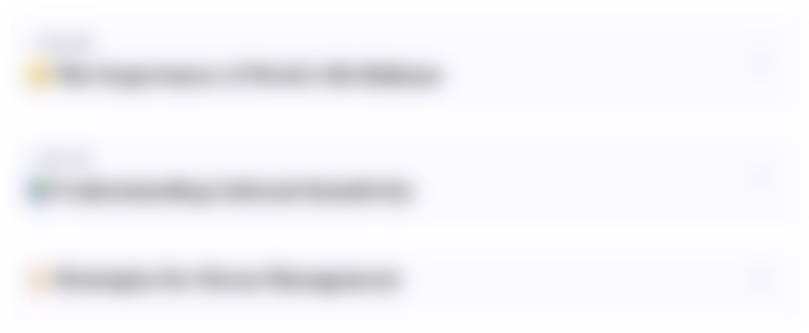
This section is available to paid users only. Please upgrade to access this part.
Upgrade NowMindmap
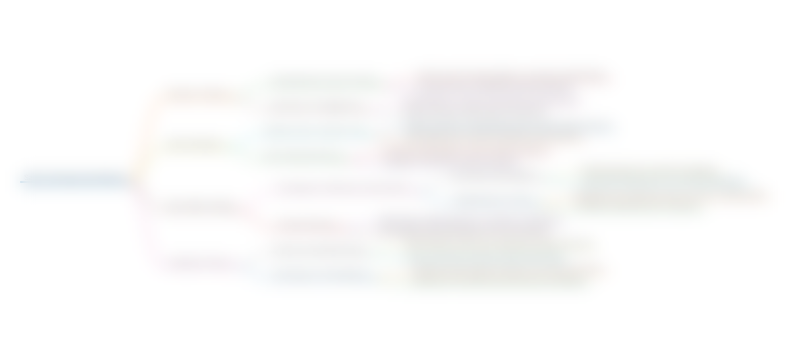
This section is available to paid users only. Please upgrade to access this part.
Upgrade NowKeywords
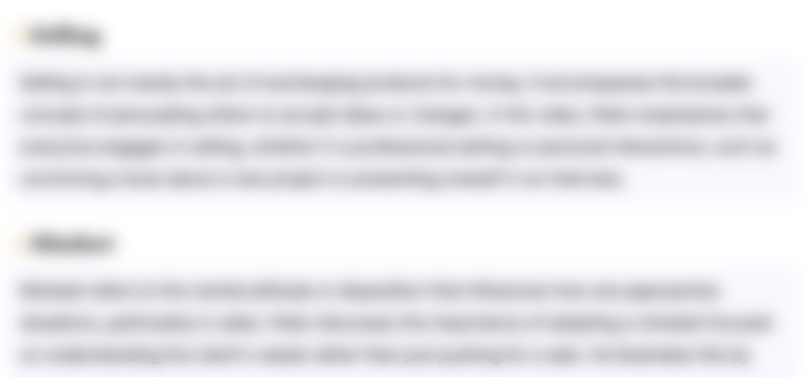
This section is available to paid users only. Please upgrade to access this part.
Upgrade NowHighlights
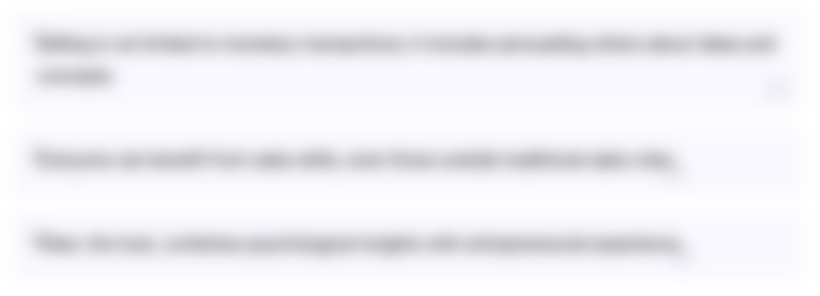
This section is available to paid users only. Please upgrade to access this part.
Upgrade NowTranscripts
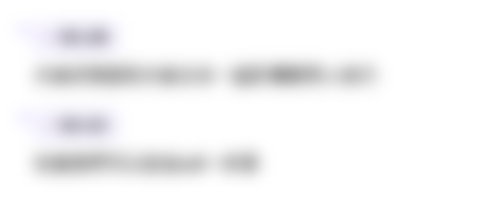
This section is available to paid users only. Please upgrade to access this part.
Upgrade NowBrowse More Related Video

How Die Casting Aluminum Works - How It's Made

What Is Casting? 11 Types of Casting Processes Explanation

5 Tips for Working With Aluminium HIGH PRESSURE DIE CASTING | Explained - Serious Engineering: Ep 28
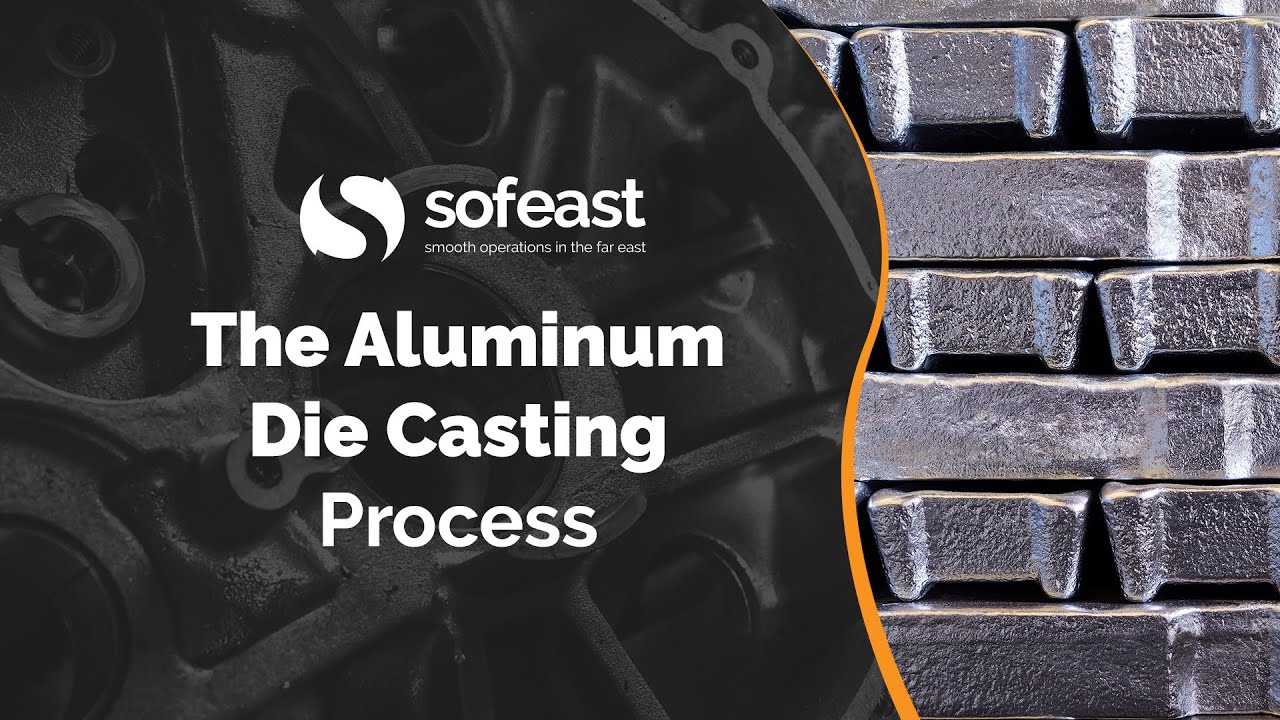
The Aluminum Die Casting Process
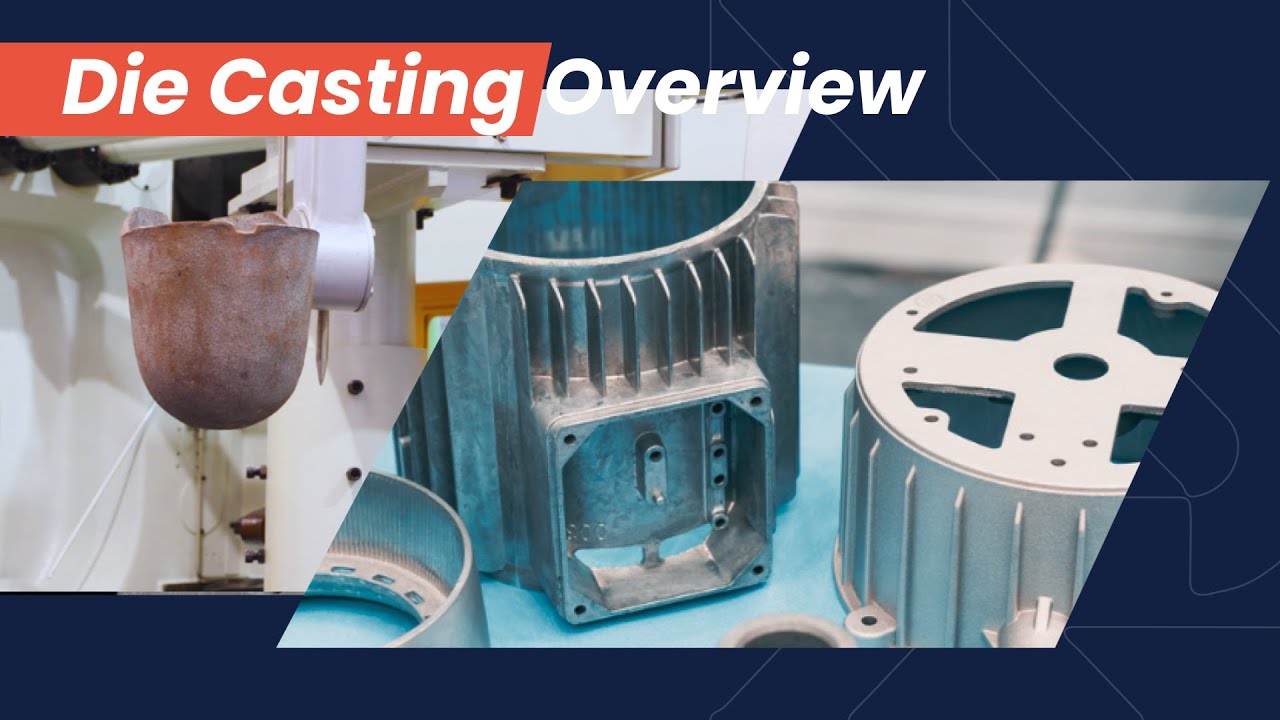
What Is Die Casting? Understand the Most Efficiency Metal Casting Process

Die Casting
5.0 / 5 (0 votes)