What is Quality Management? | Quality Management Tutorial | Invensis Learning
Summary
TLDRThis video covers the essentials of quality management, explaining its importance in ensuring consistent products, satisfying customer needs, and improving organizational performance. It highlights key principles, such as customer focus and continuous improvement, and explores popular tools like Six Sigma, Pareto charts, and the Fishbone diagram. Real-world examples from companies like Coca-Cola, Boeing, and Nokia demonstrate how these strategies lead to significant business improvements, from reducing defects to enhancing productivity. The video emphasizes that quality management is crucial for staying competitive and responsive to customer demands.
Takeaways
- 😀 Quality management (QM) ensures the consistency and reliability of products and services, aiming to meet or exceed customer expectations.
- 😀 Businesses often claim to offer 'high quality' without clearly defining what quality actually means or ensuring it through their processes.
- 😀 Quality management is essential for improving both products and services and the processes that produce them, aiming for consistent, higher quality.
- 😀 QM has its roots in the 1920s, with statistical methods first used to control product quality and ensure products met specific standards.
- 😀 Total Quality Management (TQM) gained momentum in Japan in the 1940s, using principles from Western experts like Deming and Juran to improve product quality.
- 😀 Quality management is crucial today for businesses to stay competitive, with factors like customer satisfaction, consistency, and cost efficiency playing key roles.
- 😀 Key benefits of quality management include improved customer satisfaction, long-term efficiency, risk reduction, increased profits, and maintaining a competitive edge.
- 😀 A Quality Management System (QMS) coordinates all activities necessary to meet customer and regulatory requirements while ensuring continuous improvement.
- 😀 The basic phases of quality management include quality planning, quality assurance, and quality control, each with distinct inputs, tools, and outputs.
- 😀 Six Sigma, Kaizen, Pareto charts, and Fishbone diagrams are essential tools used in quality management to identify defects, improve processes, and make data-driven decisions.
Q & A
What is quality management, and why is it important?
-Quality management involves managing the activities and tasks that ensure products and services meet a specific standard of quality. It is important because it helps organizations deliver consistent and high-quality products, enhances customer satisfaction, and improves overall efficiency in processes.
What is the history of quality management?
-Quality management has roots dating back to the 1920s when statistical theory was first used to control product quality. It gained significant traction in the 1940s in Japan, particularly through Total Quality Management (TQM), and by the 1980s, Western companies began adopting these practices.
Why is customer satisfaction critical in quality management?
-Customer satisfaction is crucial because, in a competitive market, businesses need to meet or exceed customer expectations to retain their market position. Quality management helps ensure products and services consistently satisfy customer needs, which drives loyalty and long-term success.
What are the main reasons why quality management is necessary for organizations?
-Quality management is necessary because it ensures customer satisfaction, maintains product consistency, improves operational efficiency, reduces risks, increases profitability, and helps maintain a competitive advantage.
What is a Quality Management System (QMS)?
-A Quality Management System (QMS) is a structured system that documents processes, methods, and responsibilities for achieving quality objectives. It helps organizations meet customer and regulatory requirements while improving their processes and efficiency. An example of a QMS is ISO 9001.
What are the key phases in the quality management process?
-The key phases in the quality management process are quality planning, quality assurance, and quality control. Each phase involves specific activities to ensure that the deliverables meet the required standards.
What are some of the essential tools used in quality management?
-Some essential tools used in quality management include Six Sigma, Pareto charts, Fishbone diagrams, Kaizen, flowcharts, histograms, and Total Quality Management (TQM). These tools help businesses identify, analyze, and address quality issues in their processes.
How did Coca-Cola implement quality management techniques?
-Coca-Cola improved its food safety and quality management by creating a Six Sigma team. They applied various quality management tools like process mapping and cost-benefit analysis, leading to a 75% reduction in customer complaints and improved quality metrics.
How did Boeing benefit from implementing quality management strategies?
-Boeing improved efficiency by introducing Lean Manufacturing and later combining it with Six Sigma techniques. This integration helped increase resource productivity from 30% to 70%, reduce costs, and improve customer response times.
What is Kaizen, and how does it relate to quality management?
-Kaizen is a Japanese term meaning continuous improvement. It focuses on making small, incremental changes in processes to achieve large-scale improvements over time. In quality management, Kaizen encourages a culture of ongoing improvement, involving employees in problem-solving and process refinement.
Outlines
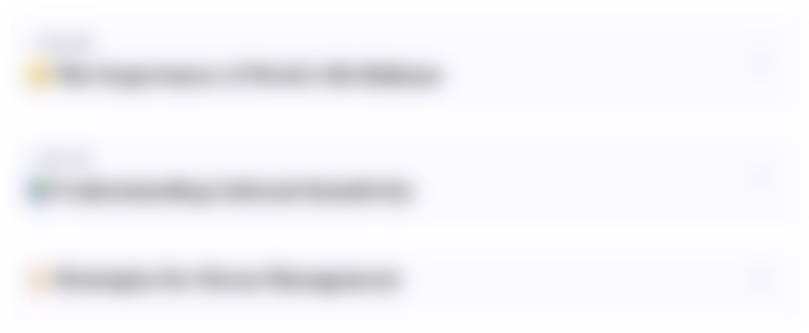
このセクションは有料ユーザー限定です。 アクセスするには、アップグレードをお願いします。
今すぐアップグレードMindmap
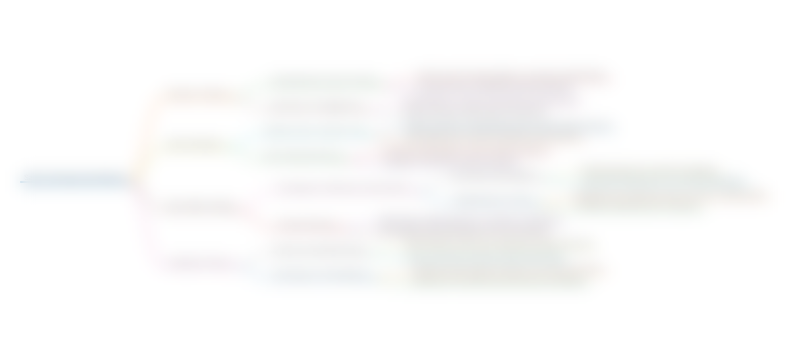
このセクションは有料ユーザー限定です。 アクセスするには、アップグレードをお願いします。
今すぐアップグレードKeywords
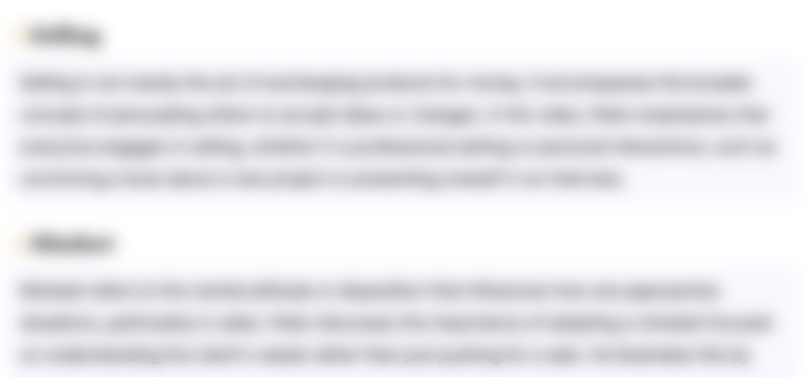
このセクションは有料ユーザー限定です。 アクセスするには、アップグレードをお願いします。
今すぐアップグレードHighlights
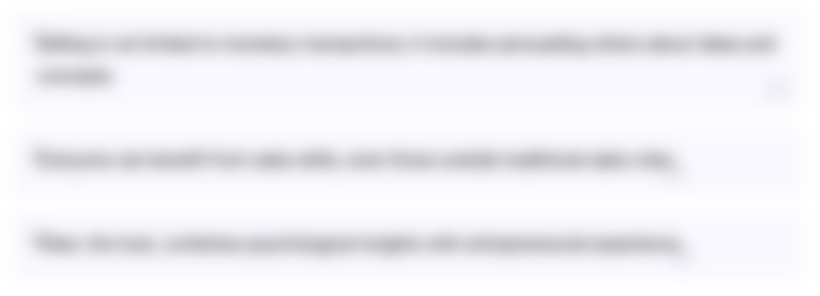
このセクションは有料ユーザー限定です。 アクセスするには、アップグレードをお願いします。
今すぐアップグレードTranscripts
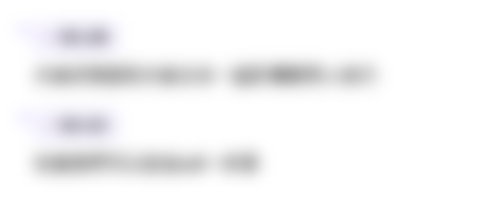
このセクションは有料ユーザー限定です。 アクセスするには、アップグレードをお願いします。
今すぐアップグレード5.0 / 5 (0 votes)