Lean Six Sigma Project Example - Using DMAIC - Yellow Belt Training
Summary
TLDRThis video provides a comprehensive guide to applying the Lean Six Sigma methodology, focusing on improving customer satisfaction in a European call center. It follows the MEIC framework (Define, Measure, Improve, Analyze, Control), outlining each phase with specific tools such as SIPOC diagrams, FMEA, and control charts. The project aims to enhance service quality by reducing inefficiencies, addressing root causes, and implementing sustainable improvements. With measurable data and strategic analysis, the project seeks to deliver significant benefits, including a 20% improvement in customer satisfaction and a substantial return on investment.
Takeaways
- 😀 The Lean Six Sigma framework follows five phases: Define, Measure, Analyze, Improve, and Control (MEIC), which helps in organizing and managing improvement projects.
- 😀 The Define phase involves identifying the problem, creating a project charter, setting goals, defining the project scope, and outlining the timeline and team composition.
- 😀 The Measure phase focuses on data collection, identifying key performance metrics (e.g., customer satisfaction scores), and using tools like the SIPOC diagram to understand the process.
- 😀 Cost of Poor Quality (COPQ) helps quantify the financial impact of poor service, demonstrating the potential benefits of process improvements.
- 😀 The Analyze phase is about using tools like Fishbone diagrams, the 5 Whys, and multivar charts to identify the root causes of problems and the sources of dissatisfaction.
- 😀 Root cause analysis goes beyond symptoms and looks deeper into underlying causes of problems, such as over-processing and defects in service delivery.
- 😀 The Improve phase involves eliminating non-value-added steps, improving process efficiency, and brainstorming ideas for improvements, such as agent training or reducing call transfers.
- 😀 Tools like FMEA (Failure Mode and Effects Analysis) and Pokayoke help in anticipating potential issues before changes are made and designing solutions to prevent errors.
- 😀 The Control phase involves establishing systems to monitor process performance over time, using control charts to track metrics like customer satisfaction and ensuring the improvements remain consistent.
- 😀 Lean Six Sigma projects require continuous monitoring and control to avoid performance deterioration, ensuring that improvements are sustained and the process remains stable.
- 😀 A key focus of Lean Six Sigma is using data to drive decisions, avoiding ambiguous conclusions and ensuring improvements are quantifiable and measurable.
Q & A
What is the primary challenge when starting a Lean Six Sigma project?
-The primary challenge is determining the first step to take, the sequence of actions, and the appropriate tools to use at each phase, as each situation may differ.
What framework is recommended for organizing a Lean Six Sigma project?
-The MEIC framework (Define, Measure, Analyze, Improve, Control) is advised as it provides a structured approach for managing Lean Six Sigma projects.
What is the problem statement in the Travis project, and what does it focus on?
-The problem statement is: 'How can customer satisfaction be improved?' It specifically focuses on improving customer satisfaction related to call center issues, not vehicle pricing or quality.
What does a project charter include in a Lean Six Sigma project?
-A project charter includes the project's goal, scope, timeline, and team composition. In the Travis case, the goal is a 20% improvement in customer satisfaction, with a 3-month timeline and an interdisciplinary team of three staff members.
How is the Cost of Poor Quality (COPQ) calculated in the Travis project?
-COPQ is calculated based on the costs incurred by the call center due to poor customer service. For example, the loss of 200 customers a month, with an estimated $1,000 profit loss per customer, leads to an annual COPQ of $2.4 million, with an estimated $1.2 million potential savings if customer satisfaction is improved.
What tools are used during the Measure phase of a Lean Six Sigma project?
-In the Measure phase, tools such as the CYPo diagram, data collection (e.g., customer satisfaction scores), and process mapping (e.g., value stream map) are used to measure and understand the process.
What role does root cause analysis play in the Analyze phase?
-Root cause analysis aims to identify the real cause(s) of a problem by examining underlying factors rather than just symptoms. Tools like Fishbone diagrams, the 5 Whys technique, and statistical analysis, such as Multivar charts, are used to uncover these root causes.
What are the main types of waste that are analyzed in the Analyze phase?
-The main types of waste analyzed are transportation, inventory, motion, waiting, over-processing, over-production, and defects. In the Travis project, over-processing (calls being transferred between agents) and defects (invoice errors) were particularly relevant.
What improvements were suggested in the Improve phase to enhance customer satisfaction?
-In the Improve phase, suggestions included eliminating unnecessary call transfers, learning from high-performing centers (like Milan), and providing better training for agents to reduce errors and rework.
How is the Control phase important in maintaining improvements?
-The Control phase is critical for ensuring that improvements are maintained over time. Control charts are used to monitor performance, ensuring customer satisfaction remains within the desired range. If scores deviate from the set limits, corrective action can be taken.
Outlines
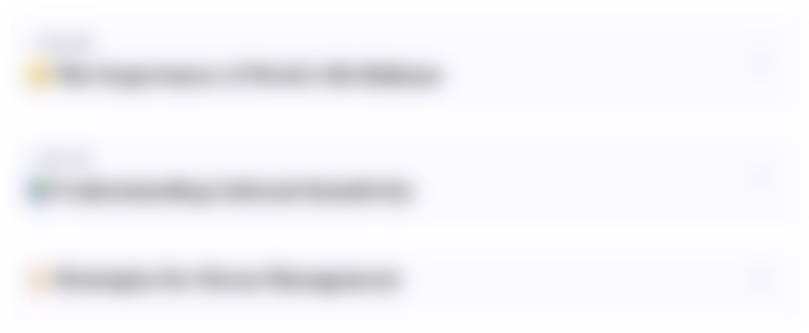
Cette section est réservée aux utilisateurs payants. Améliorez votre compte pour accéder à cette section.
Améliorer maintenantMindmap
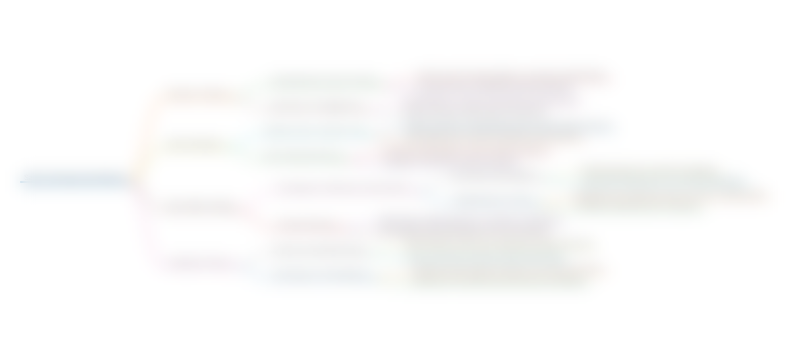
Cette section est réservée aux utilisateurs payants. Améliorez votre compte pour accéder à cette section.
Améliorer maintenantKeywords
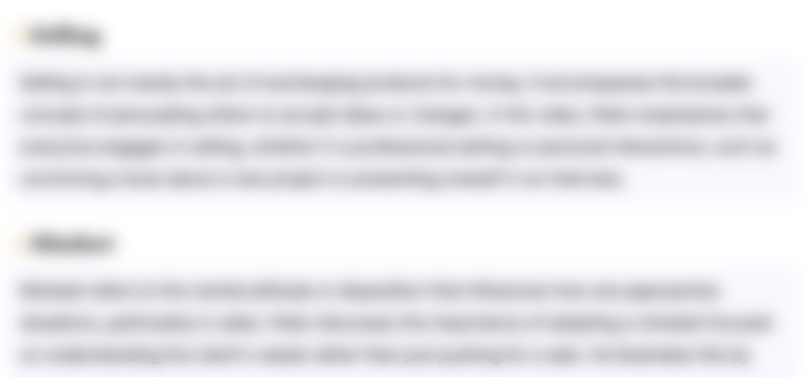
Cette section est réservée aux utilisateurs payants. Améliorez votre compte pour accéder à cette section.
Améliorer maintenantHighlights
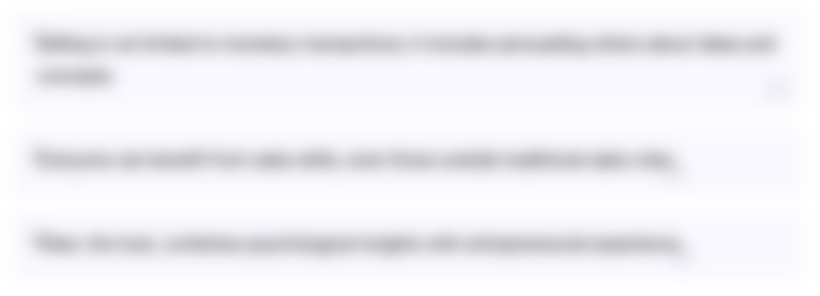
Cette section est réservée aux utilisateurs payants. Améliorez votre compte pour accéder à cette section.
Améliorer maintenantTranscripts
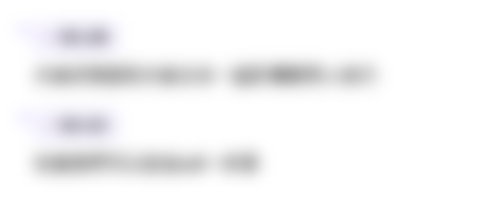
Cette section est réservée aux utilisateurs payants. Améliorez votre compte pour accéder à cette section.
Améliorer maintenantVoir Plus de Vidéos Connexes

DMAIC Call center example DMAIC Case Study

What is Six Sigma?

Introduction Best Lean Six Sigma Black Belt Tutorial For Beginners | @Six Sigma by Henry Harvin
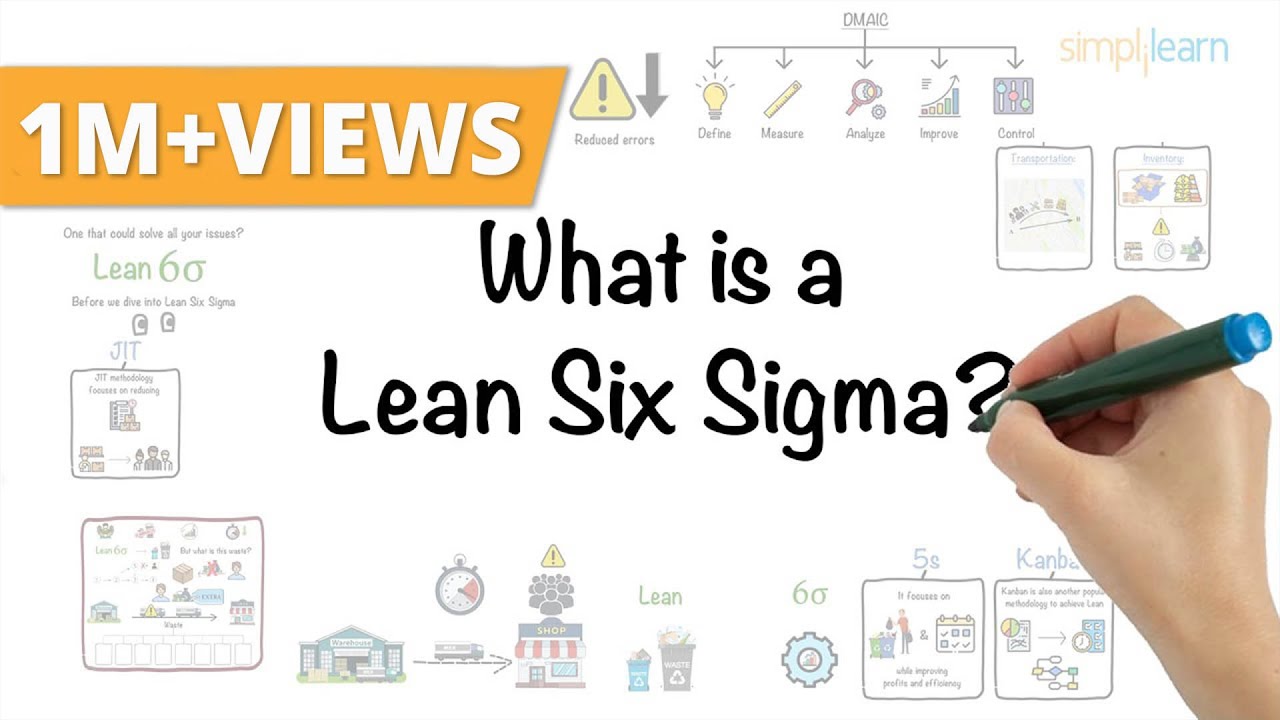
Lean Six Sigma In 8 Minutes | What Is Lean Six Sigma? | Lean Six Sigma Explained | Simplilearn
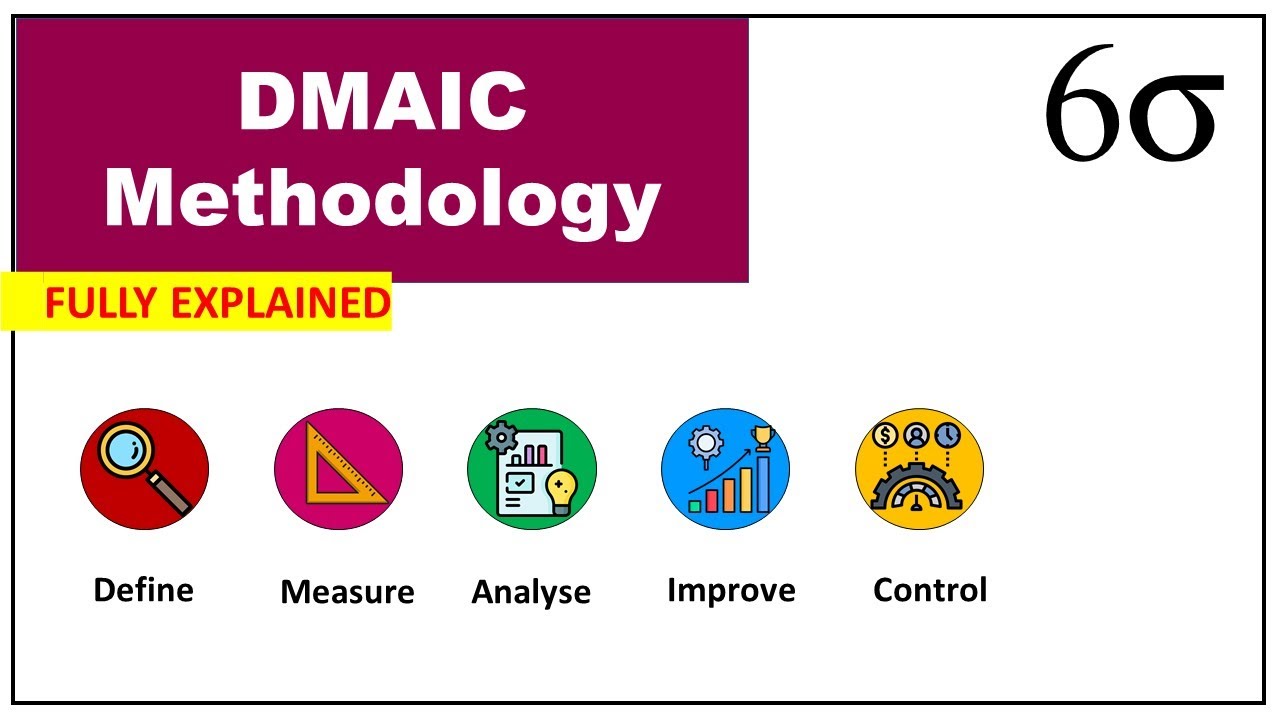
DMAIC Methodology in Six Sigma | Improve Your Processes
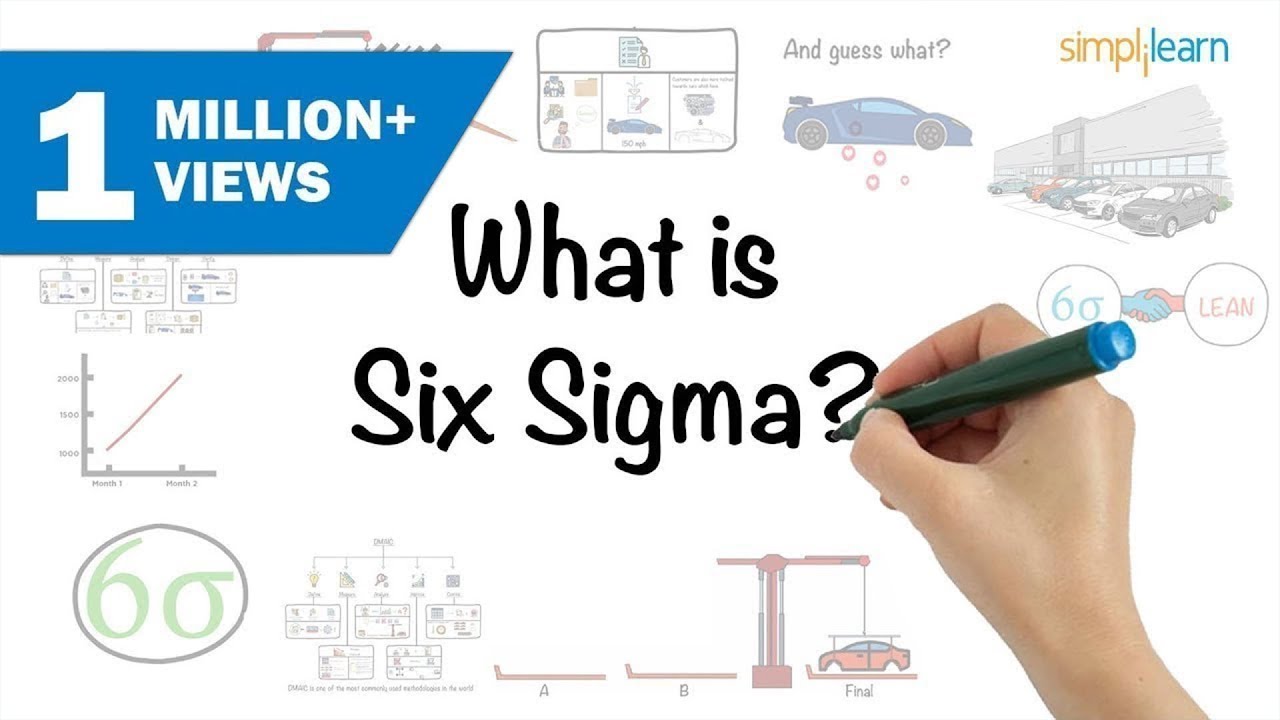
Six Sigma In 9 Minutes | What Is Six Sigma? | Six Sigma Explained | Six Sigma Training | Simplilearn
5.0 / 5 (0 votes)