Penerapan Industri 4.0 di Indocement
Summary
TLDRPT Indocement, one of Indonesia's leading cement producers, has embarked on a comprehensive digital transformation since 1996. With three plant complexes and a production capacity of 25.5 million tons, the company has adopted Industry 4.0 technologies. Key initiatives include automation, smart systems for production prediction, real-time support, and advanced analytics. Additionally, the company has developed a unified digital ecosystem for supply chain management and internal efficiency. These innovations have improved productivity, reduced operational costs, and fostered a culture of collaboration. Indocement continues to adapt to digital trends, positioning itself for future success.
Takeaways
- 😀 Indocement is one of the leading cement producers in Indonesia, with three plant complexes in Citeureup, Cirebon, and Tarjun.
- 😀 Digital transformation at Indocement began in 1996 with the automation of the Central Control Panel at Plant 6, followed by further automation at Plant 11 in 1999.
- 😀 In 2010, Indocement upgraded the CCP at the Citeureup plant, and in 2016, a new fully digital Plant 14 was established at Citeureup.
- 😀 Indocement has implemented Industry 4.0 practices, focusing on three key digital pillars: service, automation, and analytics to enhance production efficiency.
- 😀 The service pillar provides real-time insights, remote support, and advanced analytics, helping improve operational efficiency across the company.
- 😀 Indocement operates a smart export system that predicts the quality of cement production, optimizing operations and ensuring consistency.
- 😀 Virtual inspections are carried out through CCTV, drop sensors, and automated sampling, further integrating and centralizing operational control.
- 😀 RFID technology is used to streamline processes, ensuring better connection and integration across operations and supply chains.
- 😀 Indocement has developed a Tiro digital ecosystem, facilitating collaboration between sales and supply chain teams, with integrated warehouse and sales force management systems.
- 😀 The company also uses robotic process automation, digital management reporting, and e-learning to improve internal workflows and ensure employee development.
- 😀 The implementation of Industry 4.0 has led to increased productivity, lower operational costs, and a culture of knowledge sharing and collaboration within the company.
Q & A
What is the main focus of Indocement's digital transformation?
-Indocement's digital transformation primarily focuses on the implementation of Industry 4.0 technologies to enhance operational efficiency, improve production quality, and foster better collaboration within the company.
When did Indocement begin its digital transformation?
-Indocement began its digital transformation in 1996 with the automation of the Central Control Panel at Plant 6.
What are the key pillars guiding Indocement's digital transformation?
-The three key pillars guiding Indocement's digital transformation are Service, Production, and Digital Ecosystem.
How has Indocement utilized automation in its production plants?
-Indocement has implemented automation in various production plants, including automating Central Control Panels at different plants and introducing full digital features in the newly built Plant 14 in 2016.
What specific digital technology does Indocement use to optimize production quality?
-Indocement uses an intelligent automatic export system that can predict the quality of cement production.
What role do virtual inspections play in Indocement's operations?
-Virtual inspections at Indocement involve the use of CCTV cameras and other technologies to monitor production processes remotely, ensuring quality control and operational efficiency.
What is the Tiro digital ecosystem at Indocement?
-The Tiro digital ecosystem is a unified digital platform that supports collaborative activities within the company, including sales, supply chain management, and warehouse management systems.
How does Indocement support its internal workforce through digital tools?
-Indocement uses digital tools like robotic process automation (RPA), digital management reports, and e-learning systems to ensure employees can work efficiently from anywhere, anytime, and access internal company resources.
What benefits has Indocement gained from applying Industry 4.0 technologies?
-By applying Industry 4.0 technologies, Indocement has seen improvements in productivity, cost reduction, enhanced knowledge sharing, and a collaborative working culture among its employees.
How does Indocement view the future role of digitalization in its success?
-Indocement believes that embracing digitalization is key to its future success, as it helps the company stay competitive and adaptable in a rapidly evolving technological landscape.
Outlines
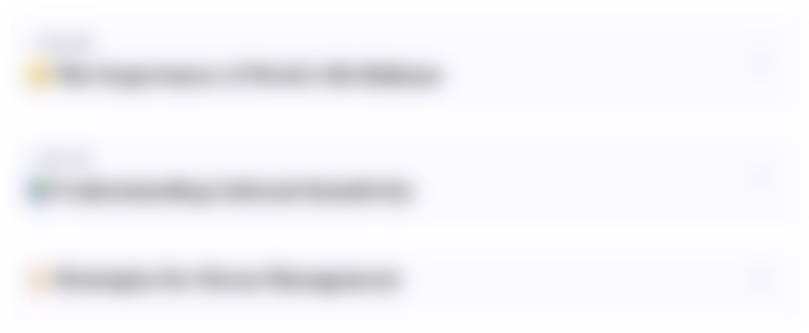
Cette section est réservée aux utilisateurs payants. Améliorez votre compte pour accéder à cette section.
Améliorer maintenantMindmap
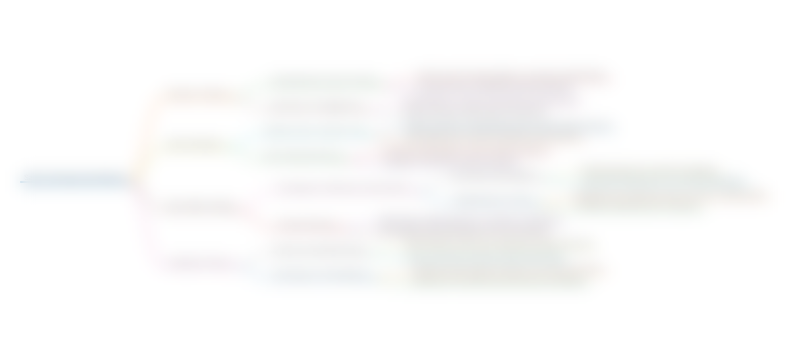
Cette section est réservée aux utilisateurs payants. Améliorez votre compte pour accéder à cette section.
Améliorer maintenantKeywords
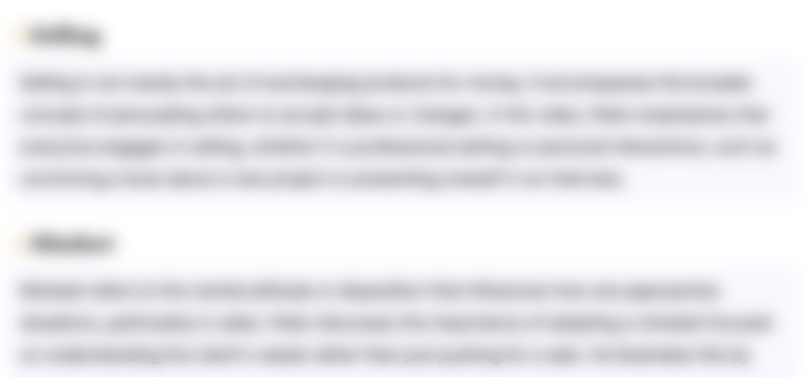
Cette section est réservée aux utilisateurs payants. Améliorez votre compte pour accéder à cette section.
Améliorer maintenantHighlights
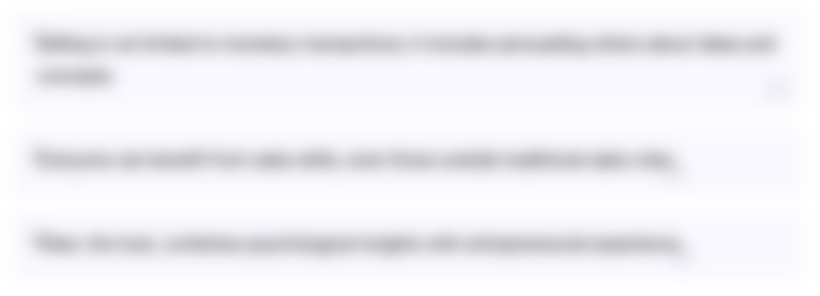
Cette section est réservée aux utilisateurs payants. Améliorez votre compte pour accéder à cette section.
Améliorer maintenantTranscripts
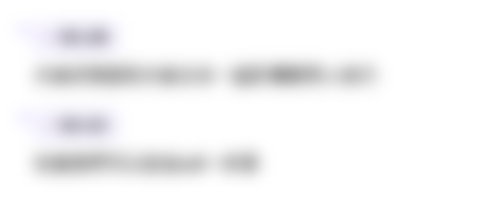
Cette section est réservée aux utilisateurs payants. Améliorez votre compte pour accéder à cette section.
Améliorer maintenantVoir Plus de Vidéos Connexes
5.0 / 5 (0 votes)