Telecurso 2000 - Processos de Fabricação - 65 Metalurgia do pó
Summary
TLDRThis educational video covers the process of powder metallurgy, also known as sintering, highlighting its significance in producing complex parts efficiently. It explains the three key stages: powder production, compaction, and sintering, and the techniques used, such as atomization and electrolysis. The video emphasizes the advantages of powder metallurgy, including cost-effectiveness, precision, and automation. Applications range from filters and cutting tools to bearings in industries like automotive and aerospace. However, limitations like the size of parts and tooling costs are also discussed. Overall, the process is portrayed as essential for modern industrial production.
Takeaways
- 😀 The script introduces the powder metallurgy process, also known as sintering, which is widely used in mechanical engineering.
- 😀 Powder metallurgy offers a competitive alternative to traditional metallurgy due to its technological and economic advantages.
- 😀 This technique allows for the mass production of complex-shaped parts with minimal material waste using a single press and operator.
- 😀 The process involves three main stages: powder production, compaction, and sintering.
- 😀 Powder can be produced using various methods such as atomization, electrolysis, and mechanical grinding.
- 😀 The compaction step involves pressing powders into molds, where the particles bond through cold welding to form a 'green' compact.
- 😀 Sintering is the final stage where the 'green' compact is heated to a temperature just below the melting point to fuse the particles together.
- 😀 The sintering process reduces porosity and results in a dense, coherent product with controlled mechanical properties.
- 😀 Metal parts produced by powder metallurgy can be used immediately or undergo further operations such as heat treatment, machining, or surface finishing.
- 😀 Powder metallurgy is applied in industries such as automotive, aerospace, electronics, and agriculture, offering efficient solutions for mass production of durable parts.
Q & A
What is powder metallurgy, and why is it important?
-Powder metallurgy, also known as sintering, is a technique used to produce metal parts by pressing metal powders into molds and then heating them to form solid pieces. It is important because it allows for the production of complex shapes with high precision, reducing waste and improving material utilization.
How does powder metallurgy compare to conventional metallurgy?
-Powder metallurgy is more competitive than conventional metallurgy due to its technical and economic advantages, such as the ability to produce large quantities of parts with complex shapes using less material and energy.
What are the three main stages in powder metallurgy?
-The three main stages in powder metallurgy are: 1) obtaining the metal powder, 2) compacting the powder into a mold, and 3) sintering, where the compacted powder is heated to form a solid piece.
What methods are commonly used to obtain metal powder?
-Common methods for obtaining metal powder include atomization (where molten metal is sprayed with gas, air, or water to form powder), electrolysis (where metal is dissolved and deposited as powder), and mechanical methods like ball milling.
What is the role of compacting in the powder metallurgy process?
-Compacting involves placing a certain amount of metal powder into a mold and applying pressure to it, causing the powder particles to bond together into a compacted shape. This stage forms the 'green compact' that will later be sintered.
What happens during the sintering stage of powder metallurgy?
-During sintering, the compacted powder is heated to a temperature below its melting point, causing the particles to fuse together. This process reduces porosity and strengthens the material, making it suitable for further use or processing.
How does sintering affect the size and shape of the compacted powder?
-Sintering causes the compacted powder to shrink, which can lead to a volume reduction of up to 40%. The material becomes more coherent and solid, with reduced porosity and improved mechanical properties.
What are some advantages of powder metallurgy over traditional manufacturing processes?
-Powder metallurgy offers several advantages, such as minimal material waste, the ability to produce complex parts without machining, and the control over material composition and properties. It also allows for easier automation and is cost-effective for mass production.
What are some applications of powder metallurgy in industry?
-Powder metallurgy is used in the production of various parts such as filters, bearings, and tools. It is especially valuable in industries like automotive, aerospace, and electronics, where components require high precision and resistance to heat and wear.
What are the limitations of powder metallurgy?
-Some limitations of powder metallurgy include the need for specialized molds, which may limit the production of certain shapes like parts with cross holes. Additionally, the process can be costly for small-scale production due to the high cost of tooling and equipment.
Outlines
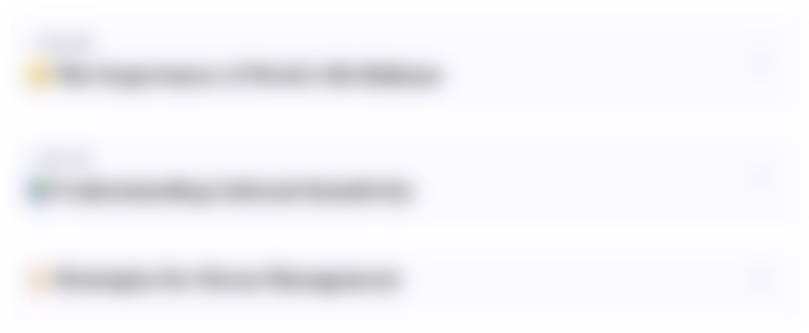
Cette section est réservée aux utilisateurs payants. Améliorez votre compte pour accéder à cette section.
Améliorer maintenantMindmap
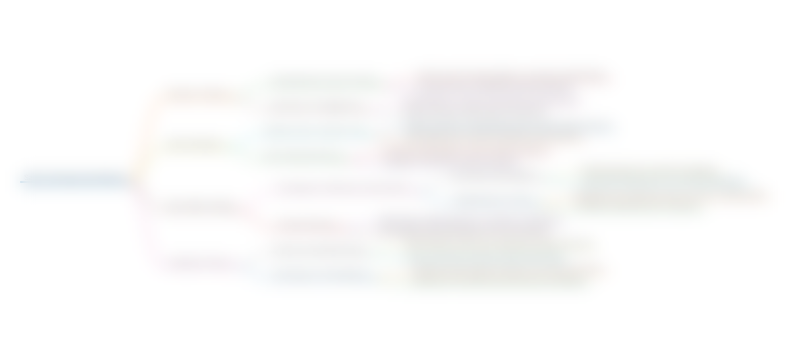
Cette section est réservée aux utilisateurs payants. Améliorez votre compte pour accéder à cette section.
Améliorer maintenantKeywords
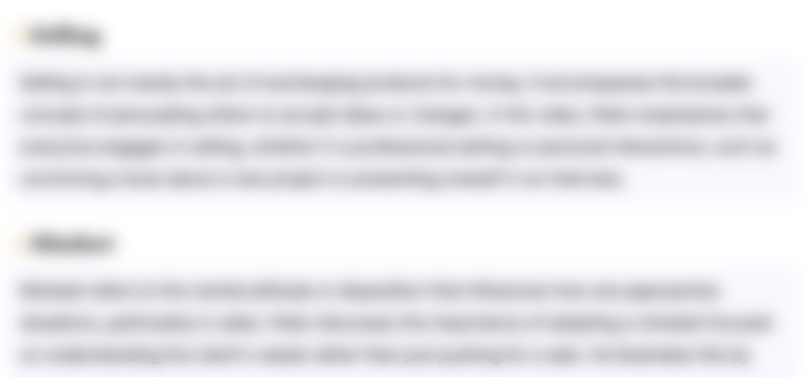
Cette section est réservée aux utilisateurs payants. Améliorez votre compte pour accéder à cette section.
Améliorer maintenantHighlights
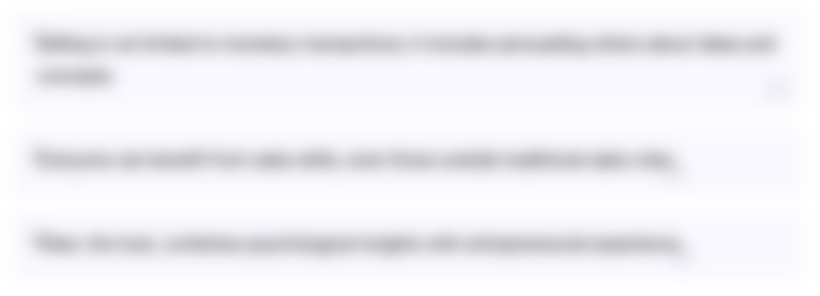
Cette section est réservée aux utilisateurs payants. Améliorez votre compte pour accéder à cette section.
Améliorer maintenantTranscripts
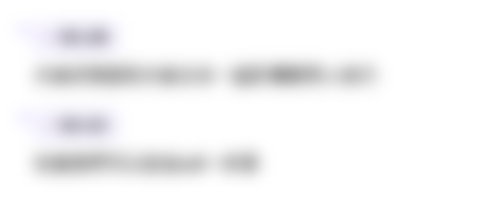
Cette section est réservée aux utilisateurs payants. Améliorez votre compte pour accéder à cette section.
Améliorer maintenantVoir Plus de Vidéos Connexes
5.0 / 5 (0 votes)