How to Achieve Operational Excellence in Manufacturing
Summary
TLDRThe video discusses achieving operational excellence in manufacturing, emphasizing that success comes through continuous improvement in product design, processes, and productivity. Operational excellence is a journey, not a destination, and it leads to sustainable market leadership and customer satisfaction. Key strategies include empowering employees, CEO commitment, and leveraging training resources. By focusing on ongoing improvement and aligning objectives with resources, businesses can lower costs, boost employee morale, and enhance customer service. In today's competitive marketplace, operational excellence is essential for manufacturing companies to thrive.
Takeaways
- 🏭 Operational excellence is crucial for long-term growth and market leadership in manufacturing.
- 📈 It focuses on continuous improvement rather than being a fixed destination, leading to sustainable success.
- 💡 Manufacturers need to invest in product design, production processes, and productivity to enhance customer satisfaction.
- 🎯 The three main strategic objectives for manufacturers are ensuring product quality, improving responsiveness to customer demands, and increasing production capacity.
- 🚀 Operational excellence helps businesses stand out by reducing operating costs, boosting employee morale, and improving customer satisfaction.
- 👷 Empowering shop floor employees to make decisions is a key step in achieving operational excellence.
- 👩💼 Leadership support, particularly from the CEO, is crucial to fostering a company-wide commitment to excellence.
- 📚 Continuous training, hiring experts, and focusing on ongoing improvement and problem-solving are essential elements of operational excellence.
- 😊 Happy and well-supported employees lead to satisfied customers, which drives better business results.
- 🌍 In today's global marketplace, operational excellence is not optional—it is a necessity for maintaining competitiveness, productivity, and profitability.
Q & A
What is operational excellence in the context of manufacturing?
-Operational excellence in manufacturing is a strategy focused on continuous improvement of product design, production processes, and productivity. It leads to enhanced customer satisfaction and helps businesses achieve sustainable market leadership.
Why is operational excellence considered a journey rather than a destination?
-Operational excellence is seen as a journey because it involves continuous improvement over time. It's not a one-time achievement, but an ongoing process aimed at positioning the organization for long-term growth and market leadership.
What are the three strategic objectives of manufacturers according to the script?
-The three strategic objectives for manufacturers are: ensuring consistent product quality, improving responsiveness to customer orders, and increasing production capacity and capability.
How does operational excellence benefit employee morale and retention?
-Operational excellence benefits employee morale and retention by streamlining processes, which creates a more efficient work environment. This leads to reduced stress, greater empowerment, and higher job satisfaction among employees.
What role do shop floor employees play in achieving operational excellence?
-Shop floor employees play a crucial role by being empowered to make decisions that drive operational efficiency. Their involvement in decision-making helps ensure that processes are continuously improved and optimized.
Why is it important for the CEO to support the cultural commitment to operational excellence?
-CEO support is critical because it signals a top-down commitment to operational excellence. Leadership support fosters a company-wide initiative and creates a culture where continuous improvement and excellence are prioritized.
How does operational excellence give businesses a competitive advantage?
-Operational excellence gives businesses a competitive edge by lowering operating costs, improving employee morale, reducing defect rates, and shortening industry lead times. This results in better customer satisfaction and market leadership.
What are the three key actions a company can take to achieve operational excellence?
-The three key actions to achieve operational excellence are: empowering shop floor employees to make decisions, ensuring CEO support for cultural commitment, and leveraging training resources and experts for continuous improvement.
Why is focusing on customer satisfaction important for operational excellence?
-Focusing on customer satisfaction is important because operational excellence not only improves internal processes but also leads to better customer care and solutions. Satisfied customers are key to business success and long-term growth.
What role does continuous improvement play in operational excellence?
-Continuous improvement is the foundation of operational excellence. After a strategy is established, the focus shifts to ongoing problem-solving, leadership development, and optimizing processes to achieve sustainable growth and competitive advantage.
Outlines
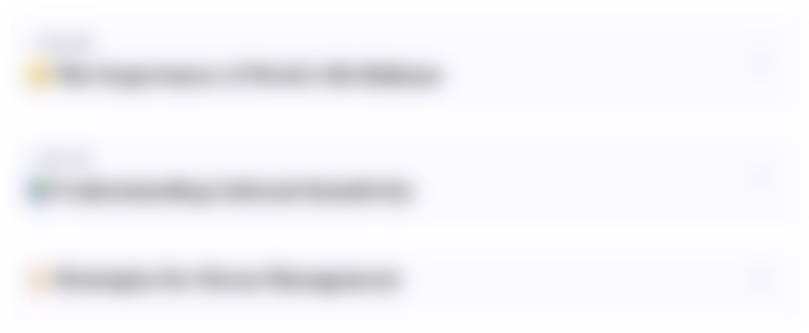
Cette section est réservée aux utilisateurs payants. Améliorez votre compte pour accéder à cette section.
Améliorer maintenantMindmap
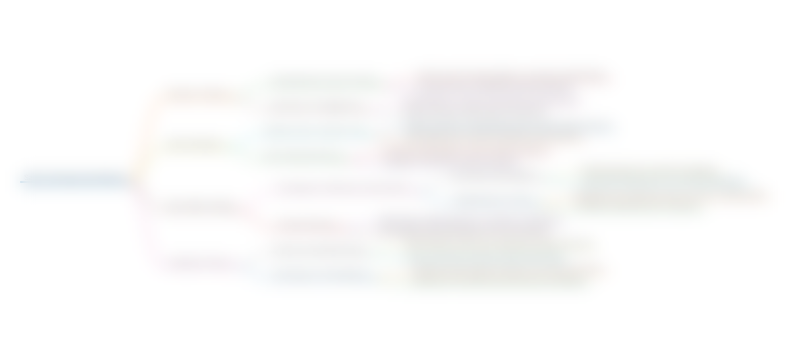
Cette section est réservée aux utilisateurs payants. Améliorez votre compte pour accéder à cette section.
Améliorer maintenantKeywords
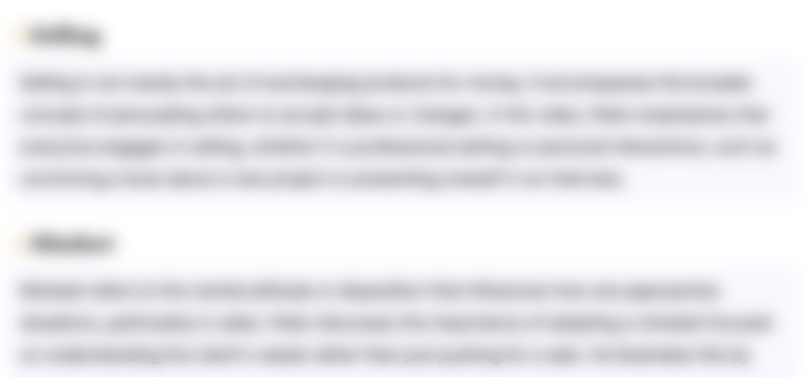
Cette section est réservée aux utilisateurs payants. Améliorez votre compte pour accéder à cette section.
Améliorer maintenantHighlights
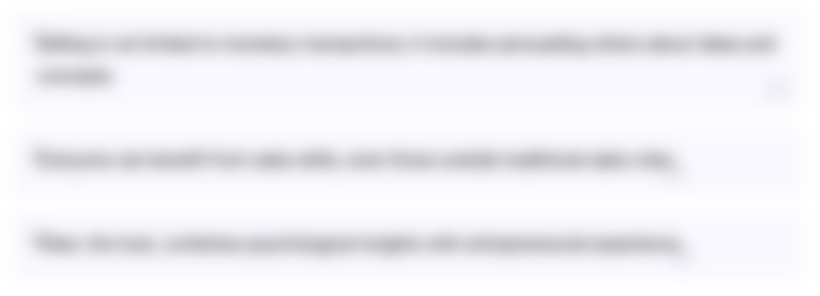
Cette section est réservée aux utilisateurs payants. Améliorez votre compte pour accéder à cette section.
Améliorer maintenantTranscripts
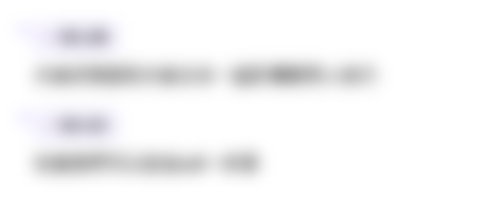
Cette section est réservée aux utilisateurs payants. Améliorez votre compte pour accéder à cette section.
Améliorer maintenantVoir Plus de Vidéos Connexes
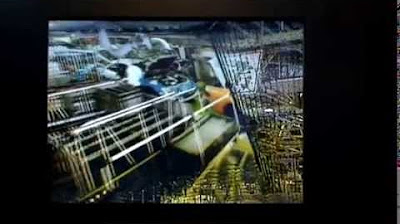
History of the Toyota Production System (TPS)

Business Process Modeling (BPM): Definisi, Manfaat dan Teknik

M3 L8 Communication for Operational Excellence
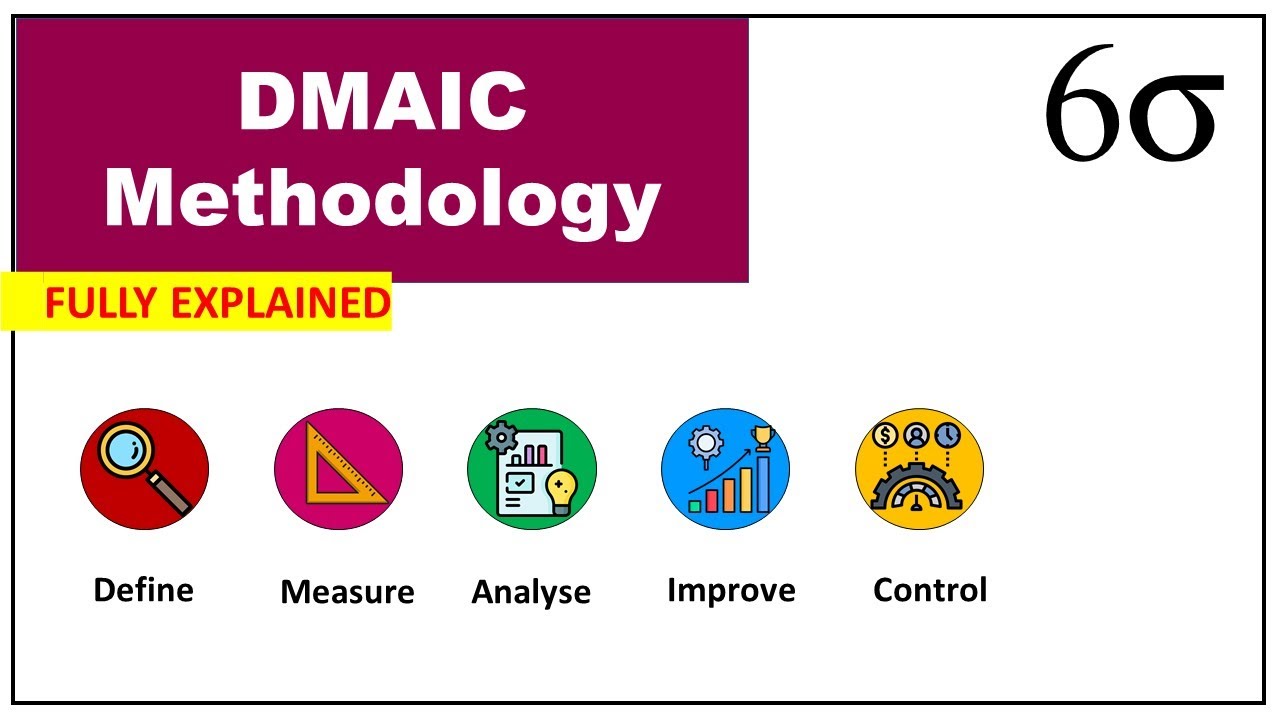
DMAIC Methodology in Six Sigma | Improve Your Processes

Essential Strategies for Increasing Production Efficiency

M3 L6 Lean Principles for Continuous Improvement
5.0 / 5 (0 votes)