NE499/515 - Lecture 10: Safety Culture and the Boeing 737 MAX Airplane Crashes
Summary
TLDRThis lecture addresses the importance of a healthy safety culture in preventing criticality accidents. It uses case studies, including the Space Shuttle Challenger disaster and the Boeing 737 Max crashes, to illustrate how poor safety culture and management pressures can lead to fatal outcomes. The talk emphasizes the need for operators to feel empowered to raise safety concerns and for management to support a culture that prioritizes safety over production pressures.
Takeaways
- 🚨 Safety culture is crucial in preventing accidents and is influenced by shared attitudes, values, goals, and practices within an organization.
- 📈 The probability of failure can escalate rapidly, as illustrated by the hypothetical reactor test scenario, underscoring the importance of vigilance.
- 👥 A healthy safety culture is not mandated or enforced but is cultivated through operators' attitudes and questioning of unsafe conditions.
- 🛠 The Space Shuttle Challenger disaster was a result of poor safety culture, where management pressures overrode an engineer's critical safety warning.
- ✈️ The Boeing 737 MAX crashes were a consequence of a flawed safety culture, where cost-cutting measures and inadequate training led to tragic outcomes.
- 🔍 A single point of failure, like the MCAS system in the Boeing 737 MAX, can have deadly consequences if not properly managed.
- 👩🏫 Training is vital; inadequate training on the MCAS system contributed to the Boeing crashes, highlighting the need for comprehensive safety education.
- 🔄 Economic pressures can compromise safety, as seen in the Deep Water Horizon accident, where cost-saving decisions increased the risk of a blowout.
- 🤝 Operator involvement and management buy-in are essential for a strong safety culture, ensuring that rules are understood and followed.
- 🔄 Routine self-assessments and audits can identify weaknesses in safety controls and are necessary for continuous improvement.
- 🌟 Setting the right example and fostering a team mentality can encourage a proactive approach to safety and prevent accidents.
Q & A
What is the main focus of the lecture series?
-The lecture series focuses on nuclear criticality safety, discussing how an unhealthy safety culture can lead to criticality accidents.
What is the significance of the hypothetical case study presented in the lecture?
-The hypothetical case study illustrates the dilemma of proceeding with a high-risk test under pressure, drawing parallels to real-world disasters like the Space Shuttle Challenger accident.
What does the term 'safety culture' refer to in the context of the lecture?
-Safety culture refers to a set of shared attitudes, values, goals, and practices within an organization that prioritize safety in day-to-day operations.
Why is it crucial for operators to be comfortable raising safety concerns?
-Operators must feel comfortable raising safety concerns to prevent accidents, as they are often the first to notice potential hazards in their work environment.
What role did a poor safety culture play in the Boeing 737 Max crashes?
-A poor safety culture at Boeing led to the design of the Maneuvering Characteristics Augmentation System (MCAS) with a single point of failure, inadequate pilot training, and a failure to address warning signs, contributing to the crashes.
How did management pressures contribute to the Space Shuttle Challenger disaster?
-Management pressures led to the decision to launch the Challenger despite safety concerns raised by an engineer about the cold temperatures affecting the shuttle's O-rings.
What are some ways to cultivate a healthy safety culture in an organization?
-Cultivating a healthy safety culture involves getting operator involvement, management buy-in, routine self-assessments, audit closeout meetings, tracking corrective actions, and promoting a questioning attitude.
Why is it important for criticality safety engineers to network with each other?
-Networking allows criticality safety engineers to share experiences, learn from mistakes, and find better ways to ensure safety, as illustrated by the case of an expert noticing an abnormal condition at Y-12.
What is the significance of the ANS standards mentioned in the lecture?
-The ANS standards, specifically ANS 819 and 820, provide guidelines for developing and maintaining a healthy safety culture in nuclear and other high-risk industries.
How can operators be encouraged to follow safety rules?
-Operators are more likely to follow safety rules if they understand their purpose and see the rules as making everyone safer, rather than as inconvenient restrictions.
Outlines
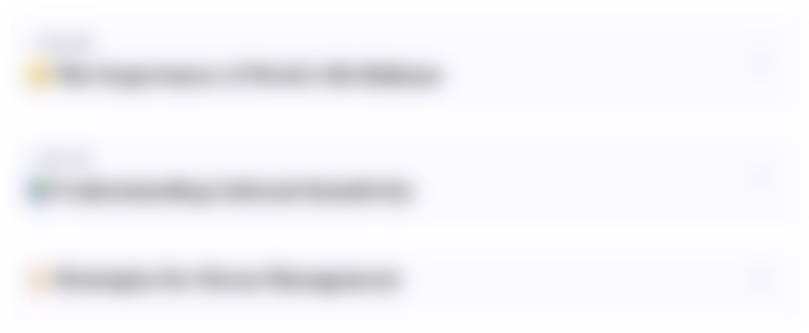
Cette section est réservée aux utilisateurs payants. Améliorez votre compte pour accéder à cette section.
Améliorer maintenantMindmap
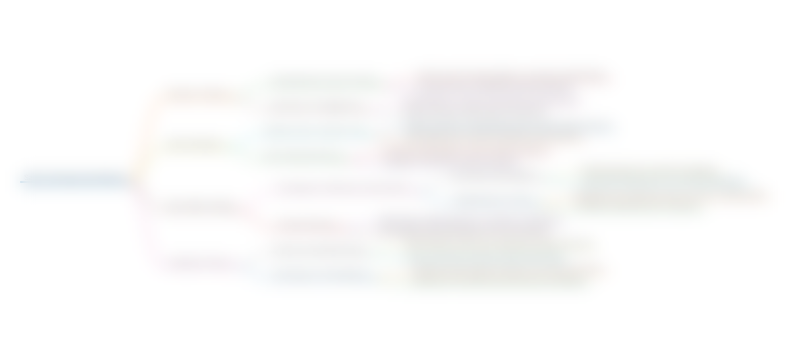
Cette section est réservée aux utilisateurs payants. Améliorez votre compte pour accéder à cette section.
Améliorer maintenantKeywords
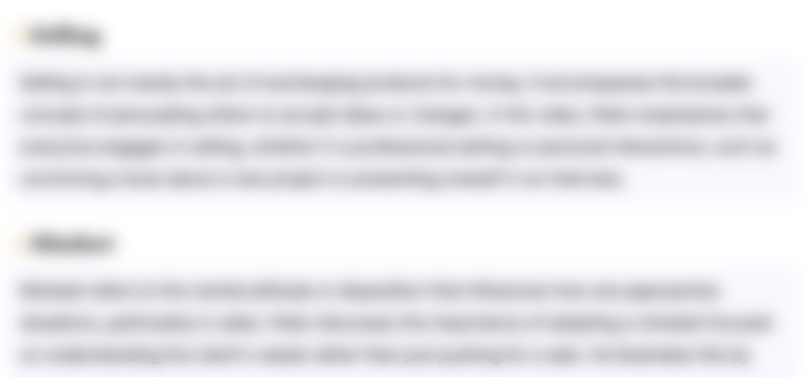
Cette section est réservée aux utilisateurs payants. Améliorez votre compte pour accéder à cette section.
Améliorer maintenantHighlights
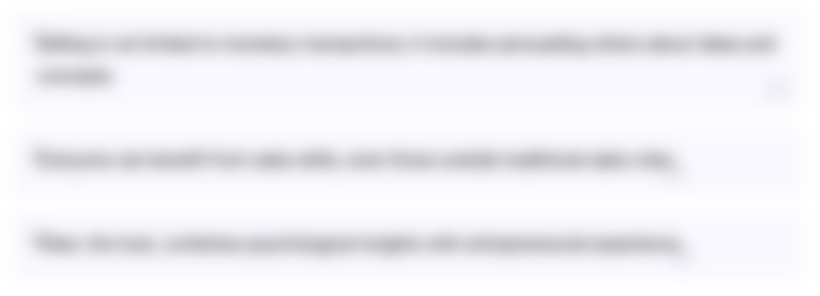
Cette section est réservée aux utilisateurs payants. Améliorez votre compte pour accéder à cette section.
Améliorer maintenantTranscripts
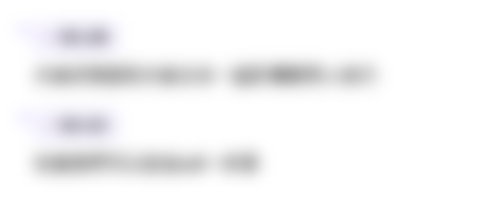
Cette section est réservée aux utilisateurs payants. Améliorez votre compte pour accéder à cette section.
Améliorer maintenant5.0 / 5 (0 votes)