Hazard Analysis Framework
Summary
TLDRThe video script emphasizes the critical role of hazard analysis in workplace safety. It outlines how employers can prevent injuries and accidents by examining operations, establishing safe processes, and training employees. Hazard analysis is a key component of a comprehensive Safety and Health Management program, offering benefits like reduced job-related incidents, lower compensation costs, and improved productivity. Employers should conduct analyses when creating new positions, introducing new equipment, or after incidents occur, ensuring proactive risk management and maintaining employee trust.
Takeaways
- 🚨 **Workplace Safety**: Employers are responsible for preventing workplace injuries and fatalities by examining operations and establishing safe work processes.
- 🔍 **Hazard Analysis**: A crucial step for employers to protect employees is conducting a hazard analysis to identify potential harm or hazards in the workplace.
- 🛠️ **Equipment and Processes**: Hazard analysis considers not only employee actions but also equipment failures and existing controls.
- 🛑 **Proactive Measures**: Once hazards are identified, employers can proactively minimize risks to ensure employee safety.
- 🔑 **Component of Safety Program**: Hazard analysis is a key component of a comprehensive Safety and Health Management program.
- 🚀 **Preventive Benefits**: Early identification and control of hazards can prevent many injuries and accidents in the workplace.
- 💰 **Financial and Morale Benefits**: Organizations benefit from reduced costs, increased productivity, and improved morale through effective hazard analysis.
- 👥 **Training New Employees**: Hazard analysis helps in training new employees in safe work practices from the start.
- 🔄 **Continuous Improvement**: Employers must act on findings from hazard analysis to maintain credibility and ensure ongoing safety.
- ⏰ **Timeliness**: While OSHA does not mandate a specific timeline, hazard analysis should be performed regularly, especially with changes in the workplace.
Q & A
What is a hazard analysis?
-A hazard analysis is a process that examines potential harm or hazards employees face while performing their work, as well as possible equipment failures and controls. It forms the basis for determining safe work procedures.
Why is conducting a hazard analysis important for employers?
-Conducting a hazard analysis is important because it helps employers to identify and minimize potential workplace hazards, thereby protecting employees and keeping them safe.
How does a hazard analysis contribute to a Safety and Health Management program?
-A hazard analysis is a key component of a robust Safety and Health Management program. It helps in identifying hazards early in work operations and eliminating or controlling them to prevent injuries and accidents.
What are the benefits of implementing a hazard analysis program?
-The benefits include fewer job-related injuries, illnesses, and deaths, reduced worker compensation costs, increased worker productivity and morale, and more efficient work practices.
How does a hazard analysis help in training new employees?
-A hazard analysis can be a helpful tool for training new employees in safe work practices from the first day, creating a workforce that only knows one way to do their job—the safe way.
What is the obligation of management when hazards are identified during a hazard analysis?
-When risks and hazards are found to exist, management has the obligation to address them as soon as possible and incorporate these findings into trainings to maintain credibility with employees.
Does OSHA establish a firm timeline for conducting a hazard analysis?
-OSHA does not establish a firm timeline for conducting a hazard analysis. However, it is generally recommended to perform one whenever a new position is created, new equipment is purchased, a work-related injury, illness, or fatality occurs, or when management feels it is appropriate.
How can a hazard analysis improve worker productivity and morale?
-A hazard analysis can lead to improved worker productivity and morale by creating a safer work environment, reducing the fear of accidents, and showing employees that their safety is a priority.
What are some triggers for conducting a hazard analysis according to the script?
-Some triggers include the creation of a new position within the organization, the purchase of new equipment for certain work operations, a work-related injury, illness, or fatality, or any other time when management feels it is necessary.
How does a hazard analysis help in preventing workplace accidents?
-A hazard analysis helps in preventing workplace accidents by proactively identifying potential hazards and establishing safe and effective work processes to minimize or eliminate these risks.
What is the role of proper employee training in the context of a hazard analysis?
-Proper employee training is crucial as it ensures that all employees are equipped with the knowledge and skills to perform their jobs safely, which is a key outcome of a hazard analysis.
Outlines
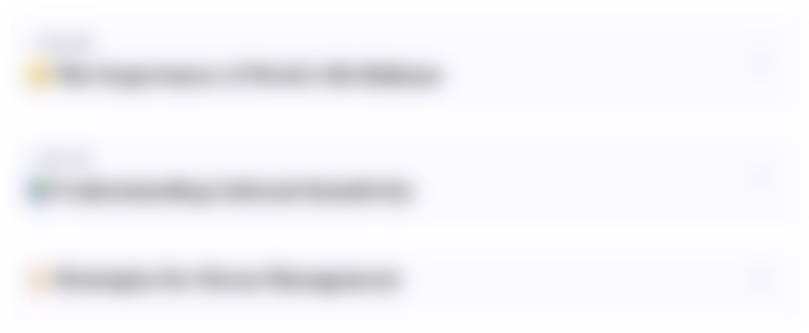
Cette section est réservée aux utilisateurs payants. Améliorez votre compte pour accéder à cette section.
Améliorer maintenantMindmap
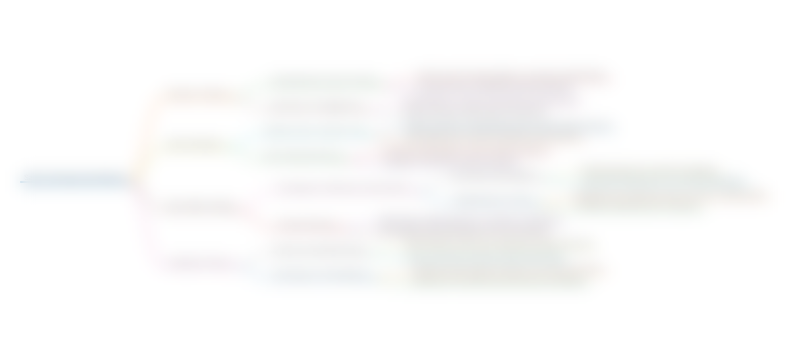
Cette section est réservée aux utilisateurs payants. Améliorez votre compte pour accéder à cette section.
Améliorer maintenantKeywords
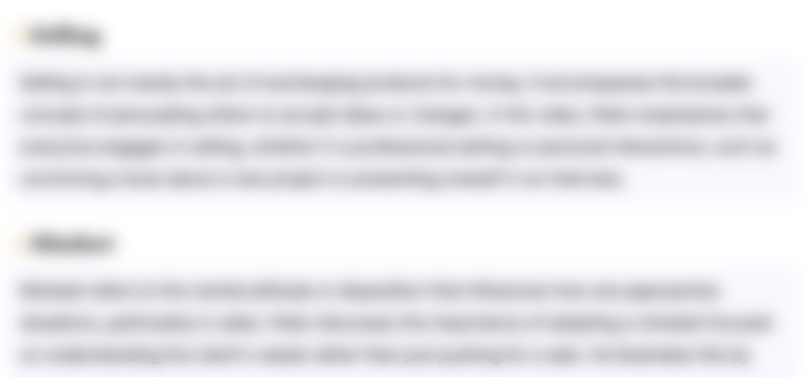
Cette section est réservée aux utilisateurs payants. Améliorez votre compte pour accéder à cette section.
Améliorer maintenantHighlights
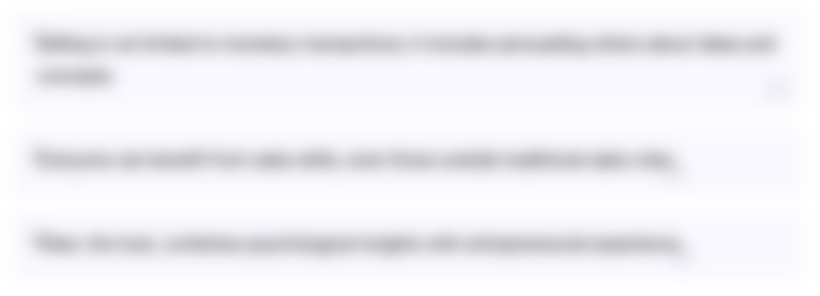
Cette section est réservée aux utilisateurs payants. Améliorez votre compte pour accéder à cette section.
Améliorer maintenantTranscripts
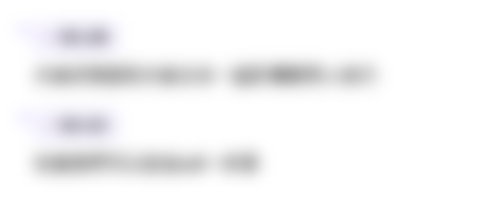
Cette section est réservée aux utilisateurs payants. Améliorez votre compte pour accéder à cette section.
Améliorer maintenantVoir Plus de Vidéos Connexes
5.0 / 5 (0 votes)