Fuel Distribution - Fuel Systems - Airframes & Aircraft Systems #66
Summary
TLDRThis lesson delves into aircraft fuel systems, highlighting their critical role in storing and delivering fuel to engines. It discusses the systems' ability to prevent engine starvation, especially during high-demand phases like takeoff. The video covers various components, including tanks, pumps, filters, and valves, and their functions in both single and multi-engine aircraft. It also touches on advanced features like vent systems, cross-feed capabilities, and fuel dump systems, essential for maintaining aircraft performance and safety.
Takeaways
- 🛩 The aircraft fuel system's primary function is to store and deliver fuel to the engine, ensuring it never runs out, even during critical flight phases.
- ✈️ Large aircraft like the Boeing 747 can consume up to 10,000 kg of fuel per engine per hour during takeoff.
- 💧 Fuel tanks in light aircraft are typically rigid and located in the wings, filled through a filler cap and refueling pipe.
- 🔧 Mechanical or electrical pumps draw fuel from the tanks, while a hand-operated selector allows the pilot to choose the fuel source or cut off the supply.
- 🚫 A strainer in the system filters out debris before fuel reaches the engine to prevent damage.
- 🔋 Piston engines may require priming with fuel before starting, which is done through a hand-operated priming pump.
- 📊 Multi-engine aircraft have more complex fuel systems with features like integral wing tanks, center tanks, and sometimes tanks in the fin or stabilizer.
- 💨 A vent system in fuel tanks equalizes air pressure above the fuel with ambient pressure, preventing issues during altitude changes.
- 🔁 Boost pumps in each tank are crucial for high-altitude operations, preventing cavitation and low-pressure boiling that could lead to vapor locks.
- 🔄 Cross-feed valves and pipes allow fuel to be fed from any tank to any engine, enhancing flexibility and safety in fuel management.
- ♻️ Some aircraft are equipped with fuel dump systems for emergency weight reduction, ensuring the plane can land safely within structural limits.
Q & A
What is the primary function of an aircraft's fuel system?
-The primary function of an aircraft's fuel system is to store and deliver fuel to the engine, ensuring it can deliver more fuel than the engine can use during its most critical phase of flight.
How much fuel can a Boeing 747 burn during take-off?
-A Boeing 747 can burn as much as 10,000 kilograms per engine per hour during the take-off phase.
What are the different types of fuel tanks used in aircraft?
-Aircraft use rigid tanks in wings, integral tanks, center tanks, and sometimes tanks in the fin or stabilizer. These tanks can be used to increase fuel capacity and adjust the aircraft's center of gravity.
What is the purpose of the vent system in aircraft fuel tanks?
-The vent system allows air pressure above the fuel in the tank to equalize with ambient pressure, preventing excessive vaporization at altitude and ensuring the fuel system operates correctly.
Why are fuel booster pumps necessary in high-altitude aircraft?
-Fuel booster pumps are necessary to prevent bubbles forming due to cavitation or low-pressure boiling at the inlet of the engine-driven fuel pump, which could lead to vapor locks.
How do cross-feed valves work in a multi-engine aircraft's fuel system?
-Cross-feed valves allow fuel to be fed from any tank to any engine, ensuring that in case of a pump failure in one tank, fuel can still be supplied to all engines.
What is the purpose of the fuel dump or jettison system in aircraft?
-The fuel dump or jettison system is used to reduce the mass of the airplane to its required landing mass when necessary, such as in emergencies or to meet regulatory requirements.
How does the fuel system prevent fuel starvation during flight?
-The fuel system prevents fuel starvation by using booster pumps, cross-feed valves, and ensuring the tanks are vented properly to maintain pressure and prevent cavitation.
What is the role of the high-level float switch in the fuel system?
-The high-level float switch shuts off fuel to the tank during refueling when the tank is full, preventing overfilling and ensuring the vent system can operate correctly.
How does the aircraft manage fuel imbalance between tanks during flight?
-Aircraft manage fuel imbalance by using the cross-feed valve to supply both engines from the tank with more fuel, then adjusting the booster pumps to restore the correct balance.
What is the purpose of the collector tank or surge box in the fuel system?
-The collector tank or surge box ensures that the booster pumps are continually submerged in fuel, preventing them from being starved of fuel and keeping them cool.
Outlines
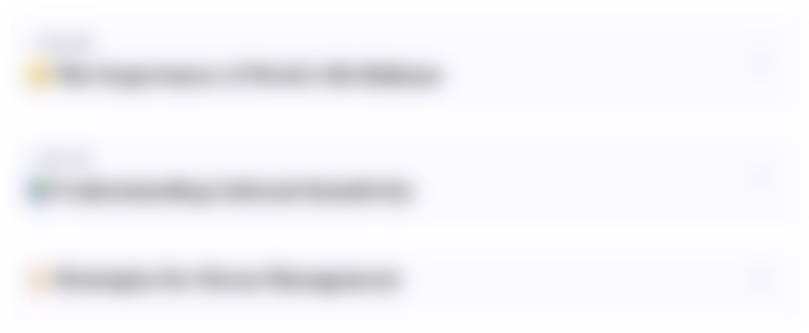
Cette section est réservée aux utilisateurs payants. Améliorez votre compte pour accéder à cette section.
Améliorer maintenantMindmap
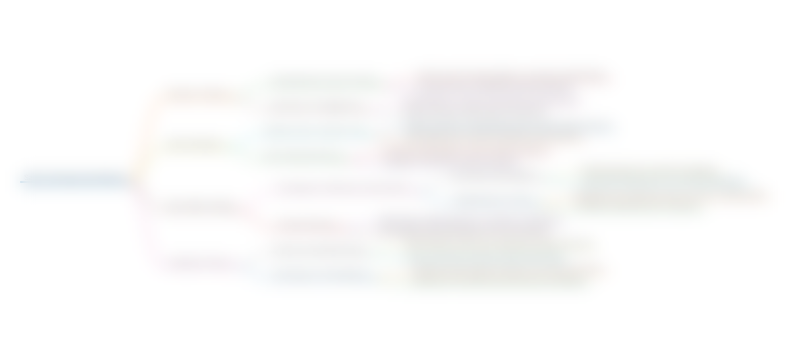
Cette section est réservée aux utilisateurs payants. Améliorez votre compte pour accéder à cette section.
Améliorer maintenantKeywords
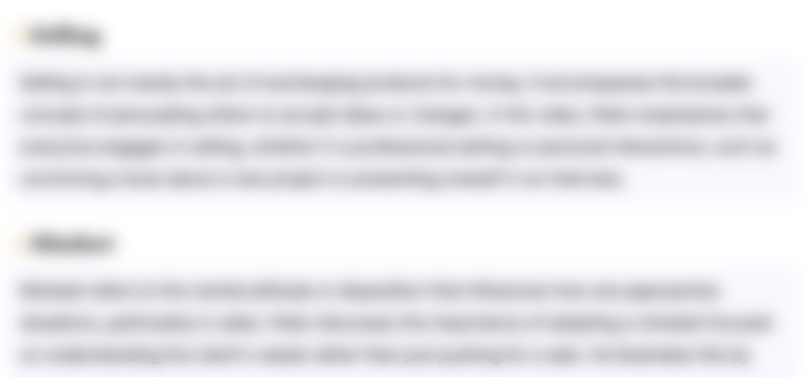
Cette section est réservée aux utilisateurs payants. Améliorez votre compte pour accéder à cette section.
Améliorer maintenantHighlights
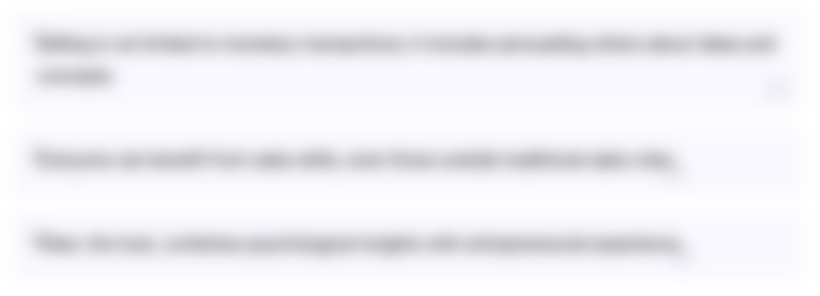
Cette section est réservée aux utilisateurs payants. Améliorez votre compte pour accéder à cette section.
Améliorer maintenantTranscripts
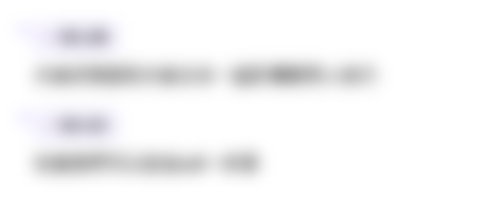
Cette section est réservée aux utilisateurs payants. Améliorez votre compte pour accéder à cette section.
Améliorer maintenantVoir Plus de Vidéos Connexes
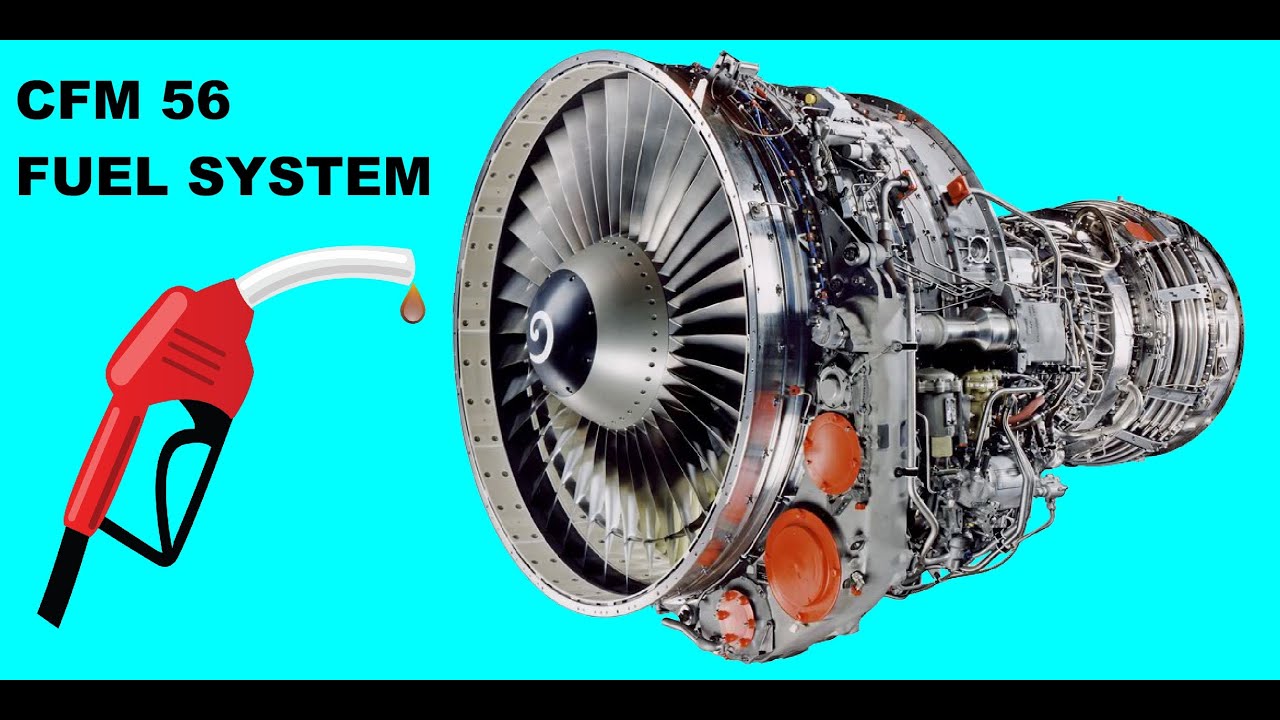
JET ENGINE FUEL SYSTEM

Fuel Types - Fuel Systems - Airframes & Aircraft Systems #64
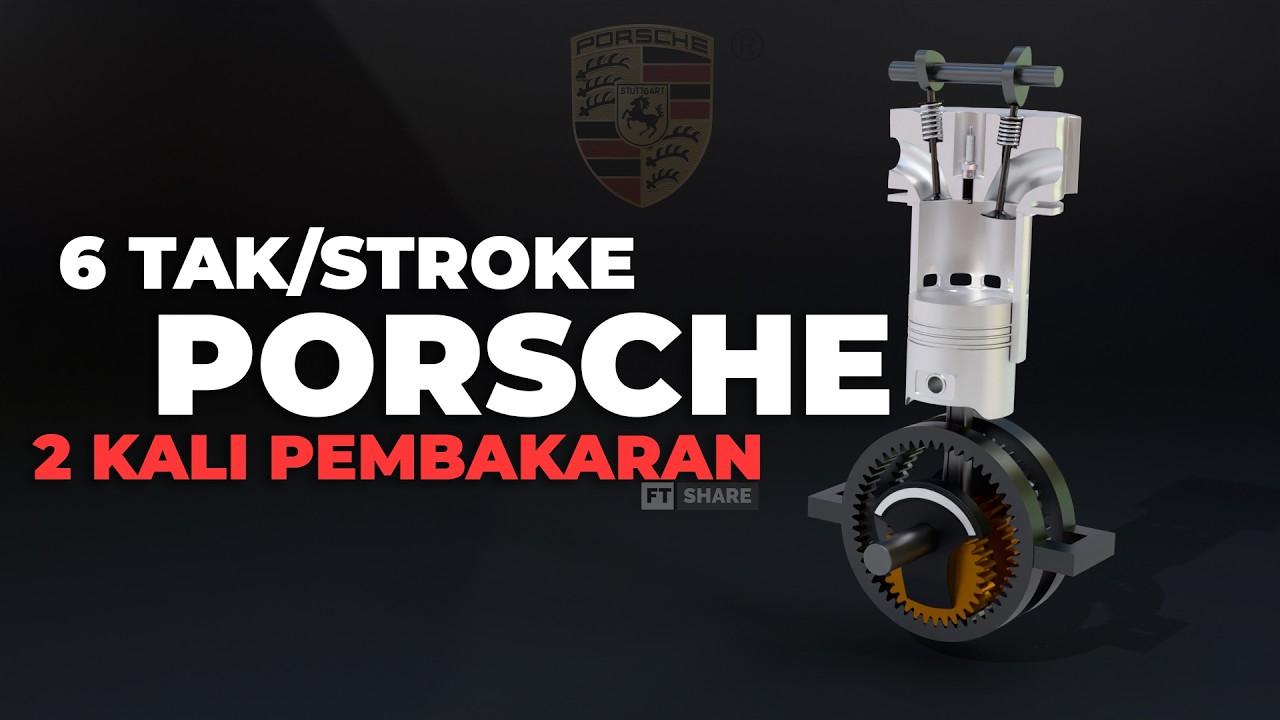
6-Stroke Dari Porsche?? Inovasi & Revolusi Mesin Bensin! Cara Kerja Mesin 6-Tak Porsche Dengan 3D
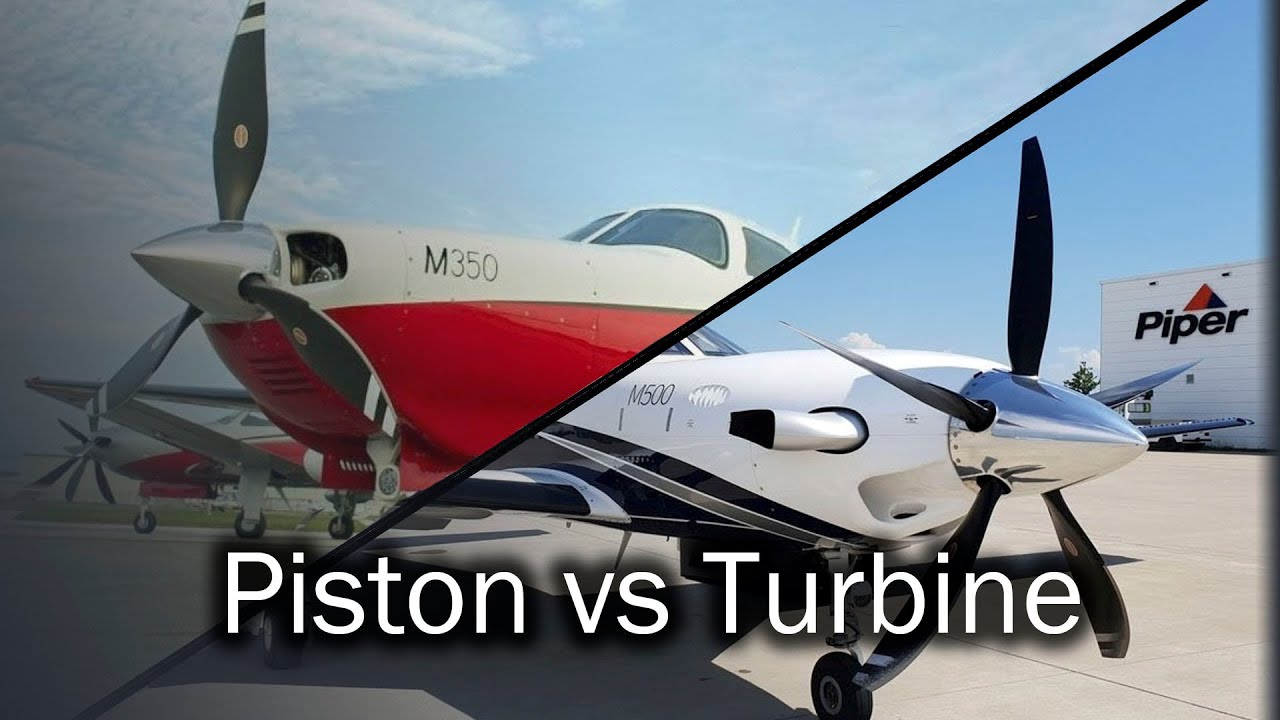
Piston and Turboprop engines | What is the difference?
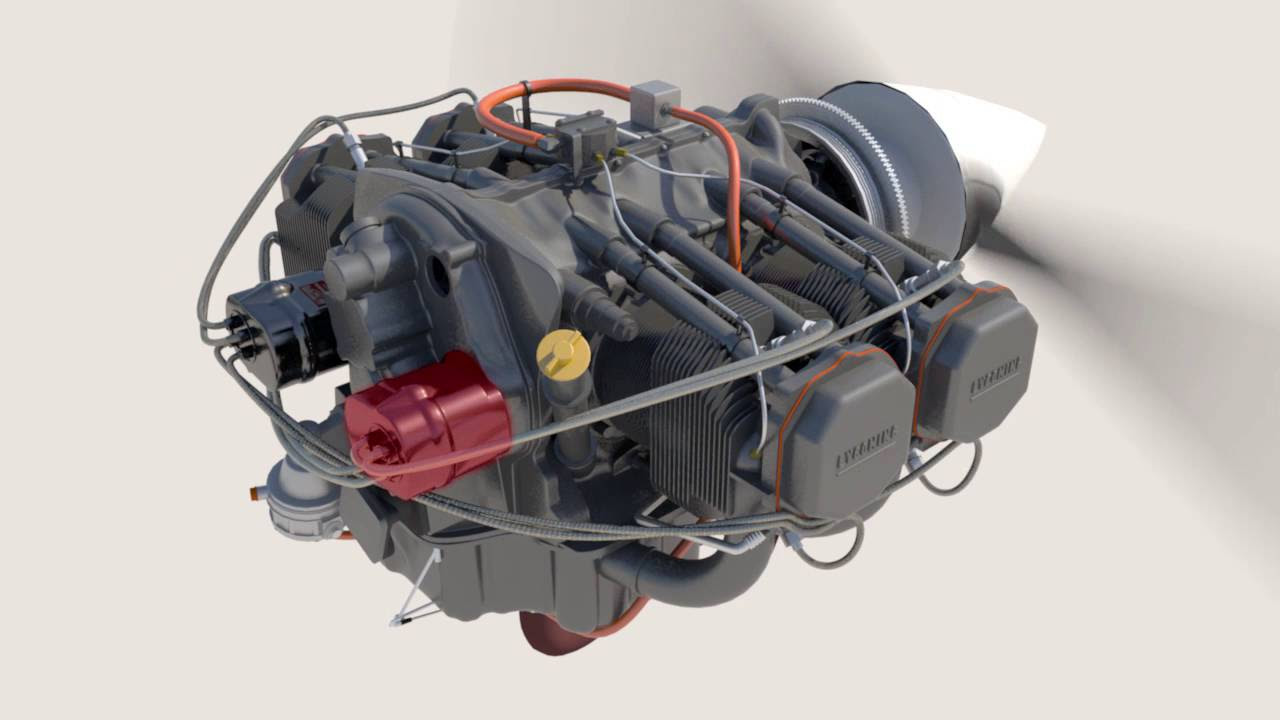
Aircraft Systems - 03 - Engine

Combustion Chambers Part 2 - Aircraft Gas Turbine Engines #09
5.0 / 5 (0 votes)