Combustion Chambers Part 2 - Aircraft Gas Turbine Engines #09
Summary
TLDRThis script discusses methods for eliminating excess fuel in gas turbine engines, including fuel drain systems and evaporation techniques. It explores the annular combustion chamber system, highlighting its advantages over multiple chamber systems. The script also covers the importance of the correct air-fuel ratio for efficient combustion, the concept of self-sustaining speed, and the challenges of relight after a flameout. Additionally, it delves into combustion efficiency, the role of fuel spray nozzles, and various fuel atomization methods, such as air spray systems and vaporizing tubes, crucial for engine start and operation.
Takeaways
- π§ Two primary methods are used to eliminate excess fuel in gas turbine engines: the fuel drain system and evaporation via a blowout cycle.
- π§ The fuel drain system works by utilizing drain tubes that connect the lowest part of each combustion chamber to the next chamber below, allowing excess fuel to exit the engine.
- π A blowout cycle involves motoring the engine with the starter motor, without fuel and ignition, to evaporate any remaining fuel traces within the engine.
- π₯ The turbo-annular combustion chamber system is more compact than the multiple combustion chamber system and does not have individual air casings for each flame tube.
- π The annular combustion chamber system is shorter and more efficient than the tubo-annular system, with no flame propagation issues and less cooling air required.
- π‘οΈ Combustion in gas turbine engines occurs at a nearly constant pressure, with a slight pressure loss due to turbulence and mixing within the combustion chamber.
- π₯ The chemically correct air-fuel ratio of 15:1 is used in gas turbine engines without causing detonation or dissociation, unlike in piston engines.
- π Combustion stability is maintained over a wide range of air/fuel ratios and air mass flows, with the stability range narrowing as air mass flow increases.
- βοΈ Relight, or restarting the engine in flight after a flameout, may require slowing down or descending to achieve the right conditions for successful ignition.
- π― Modern gas turbine engines achieve very high combustion efficiency, nearing 99% at high power and maintaining around 95% at idle, thanks to effective fuel spray nozzles.
Q & A
What are the two methods mentioned for getting rid of excess fuel in a gas turbine engine?
-The two methods are the fuel drain system and a method of evaporating the remaining traces of fuel from the combustion chambers, the turbine, and the jet pipe.
How does the fuel drain system work in a gas turbine engine?
-The fuel drain system utilizes drain tubes that connect the lowest part of each combustion chamber with the next chamber below. After a wet start, excess fuel flows from the top of the engine to the bottom chamber and exits the engine.
What is a blowout cycle in the context of gas turbine engines?
-A blowout cycle is when the engine is turned over by the starter motor without high-pressure fuel and the ignition system deselected, allowing air to flow through the engine to assist in evaporating any remaining fuel.
What is the difference between a tuber annular combustion chamber system and a multiple combustion chamber system?
-The tuber annular combustion chamber system is more compact as it does not have individual air casings for each flame tube. Instead, a number of flame tubes are fitted within an inner and an outer air casing.
What are the advantages of the annular combustion chamber system over the multiple combustion chamber system?
-The annular system has a shorter length, no flame propagation problems, requires less cooling air, has higher combustion efficiency, and provides a more even load on the turbine.
What is the chemically correct air-fuel ratio for maximum heat release in a gas turbine engine?
-The chemically correct air-fuel ratio for maximum heat release in a gas turbine engine is 15 units of air to one unit of fuel by weight.
What is the self-sustaining speed of a gas turbine engine?
-The self-sustaining speed is the speed at which the engine can accelerate without the assistance of the starter motor after start.
What is a flameout in a gas turbine engine, and how can it be caused?
-A flameout is the extinction of the flame due to various unusual occurrences, such as the ingestion of large quantities of water into the engine intakes during takeoff.
What is the significance of combustion stability in a gas turbine engine?
-Combustion stability refers to the engine's ability to maintain smooth burning over a large range of air/fuel ratios and air mass flows, which is crucial for reliable engine performance.
How does the combustion efficiency of a modern gas turbine engine compare at high power and idle conditions?
-At high power operating conditions, combustion efficiencies as great as 99% are achievable, while at idle, the system can still provide up to 95% efficiency.
What challenges do fuel spray nozzles face in gas turbine engines, and how are they addressed?
-Fuel spray nozzles face challenges such as the high velocity of the air stream and the short distance for combustion. They address this by atomizing or vaporizing the fuel. At low engine speeds and pressures, the spray pattern may form a 'bubble', which is insufficient for ignition. As the engine accelerates, the pump builds up pressure to form a 'tulip' shape, which is still not optimal. Eventually, the pump produces a spray that is finely atomized enough to ensure rapid burning.
Outlines
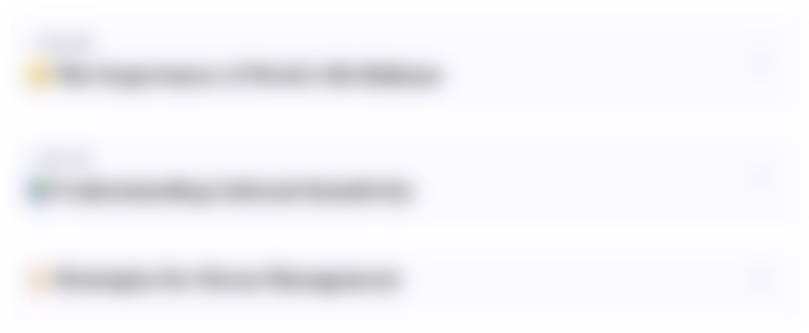
This section is available to paid users only. Please upgrade to access this part.
Upgrade NowMindmap
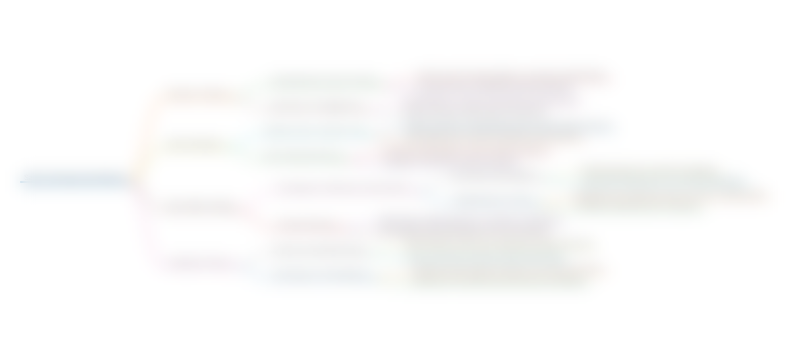
This section is available to paid users only. Please upgrade to access this part.
Upgrade NowKeywords
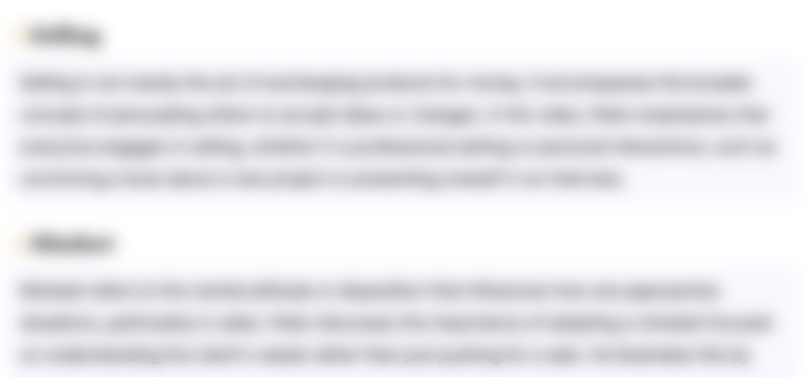
This section is available to paid users only. Please upgrade to access this part.
Upgrade NowHighlights
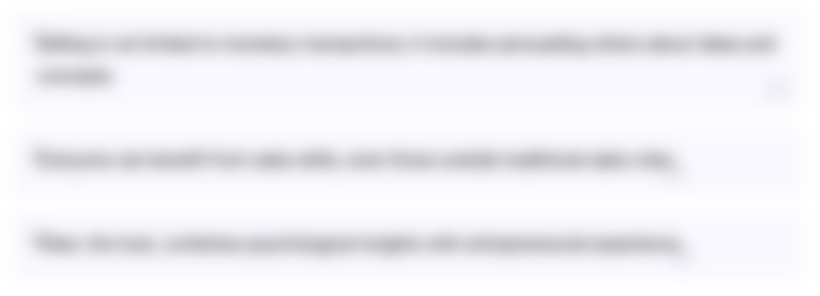
This section is available to paid users only. Please upgrade to access this part.
Upgrade NowTranscripts
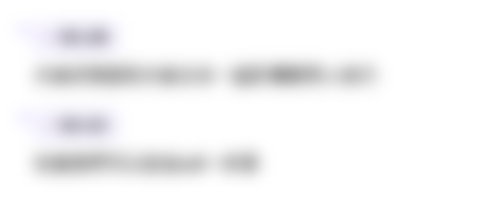
This section is available to paid users only. Please upgrade to access this part.
Upgrade NowBrowse More Related Video
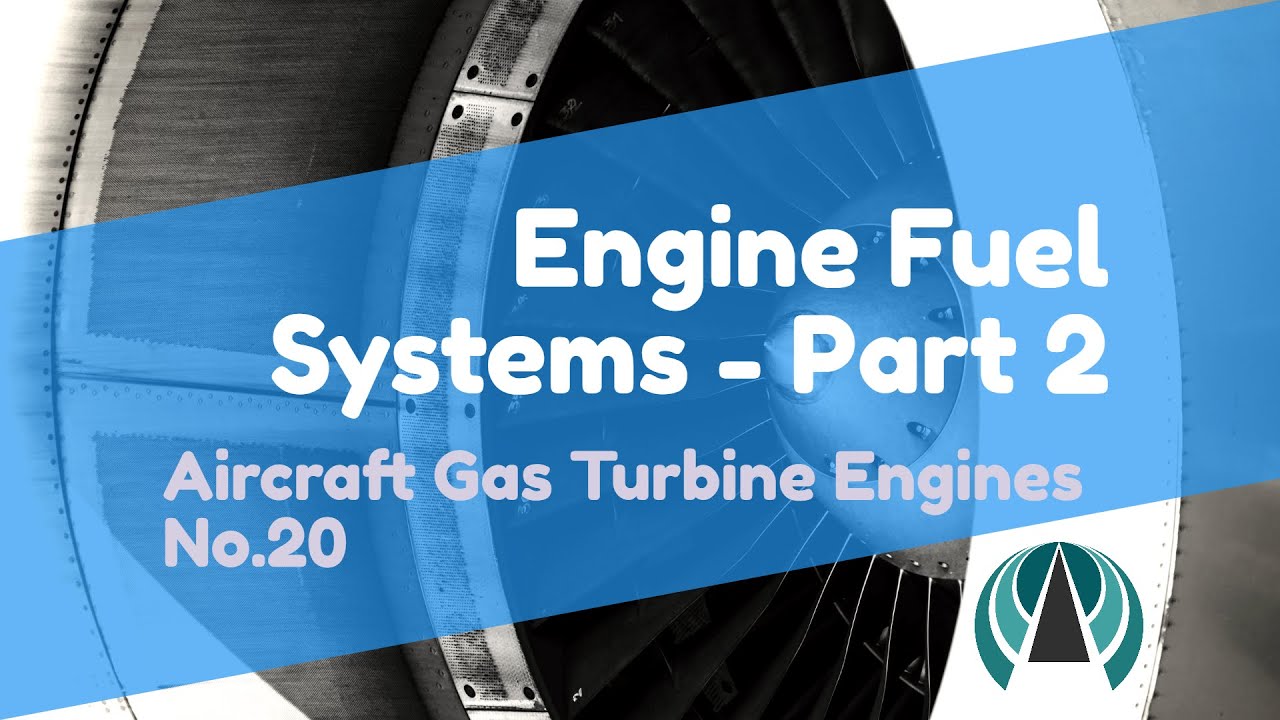
Engine Fuel Systems Part 2 - Aircraft Gas Turbine Engines #20
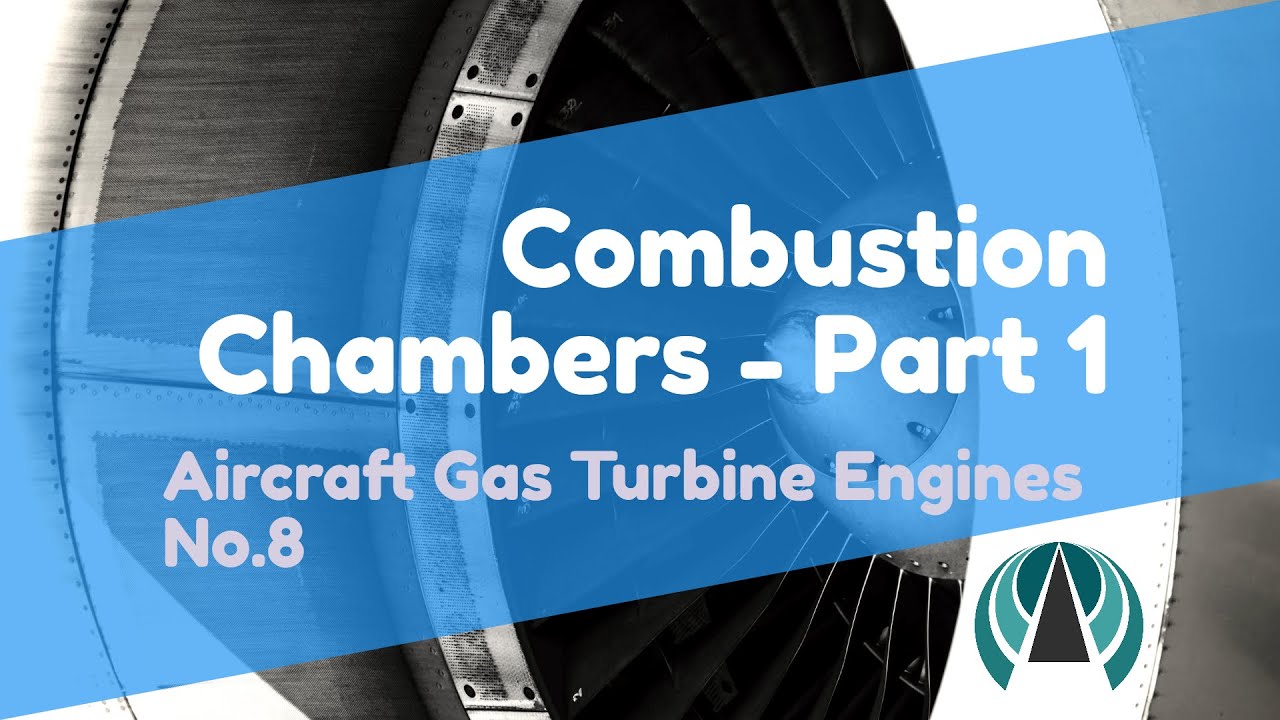
Combustion Chambers Part 1 - Aircraft Gas Turbine Engines #08
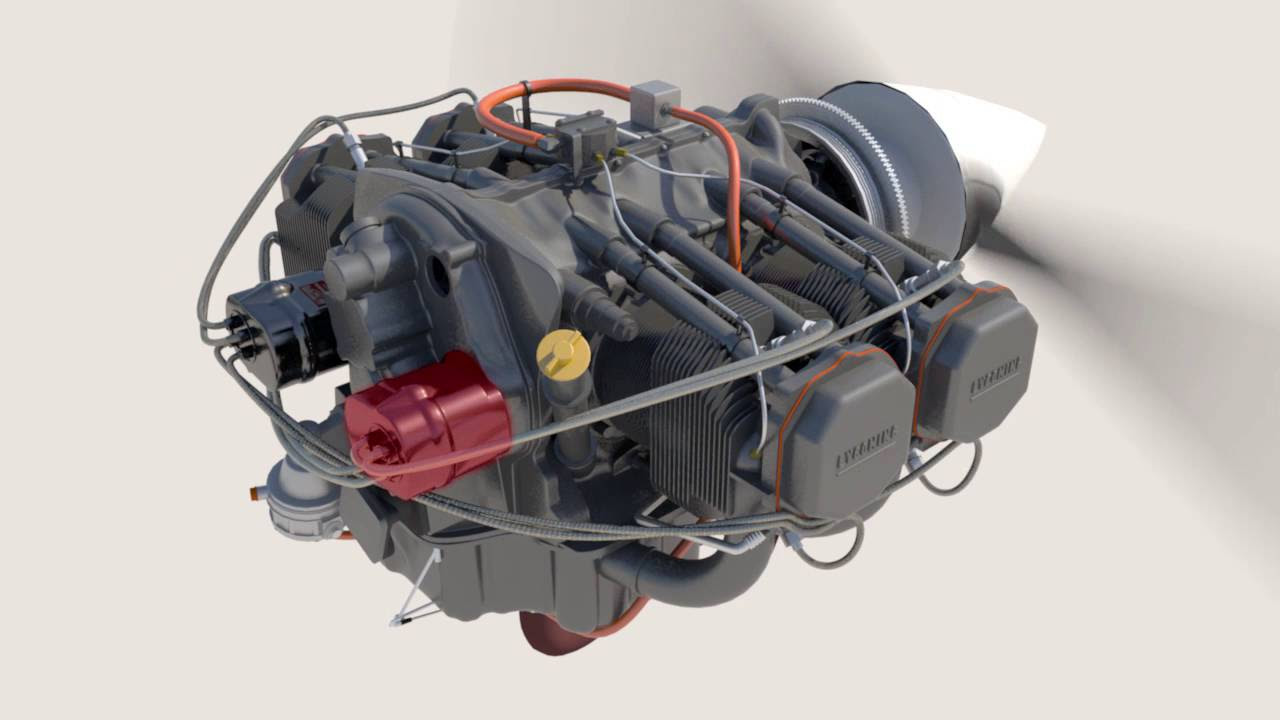
Aircraft Systems - 03 - Engine
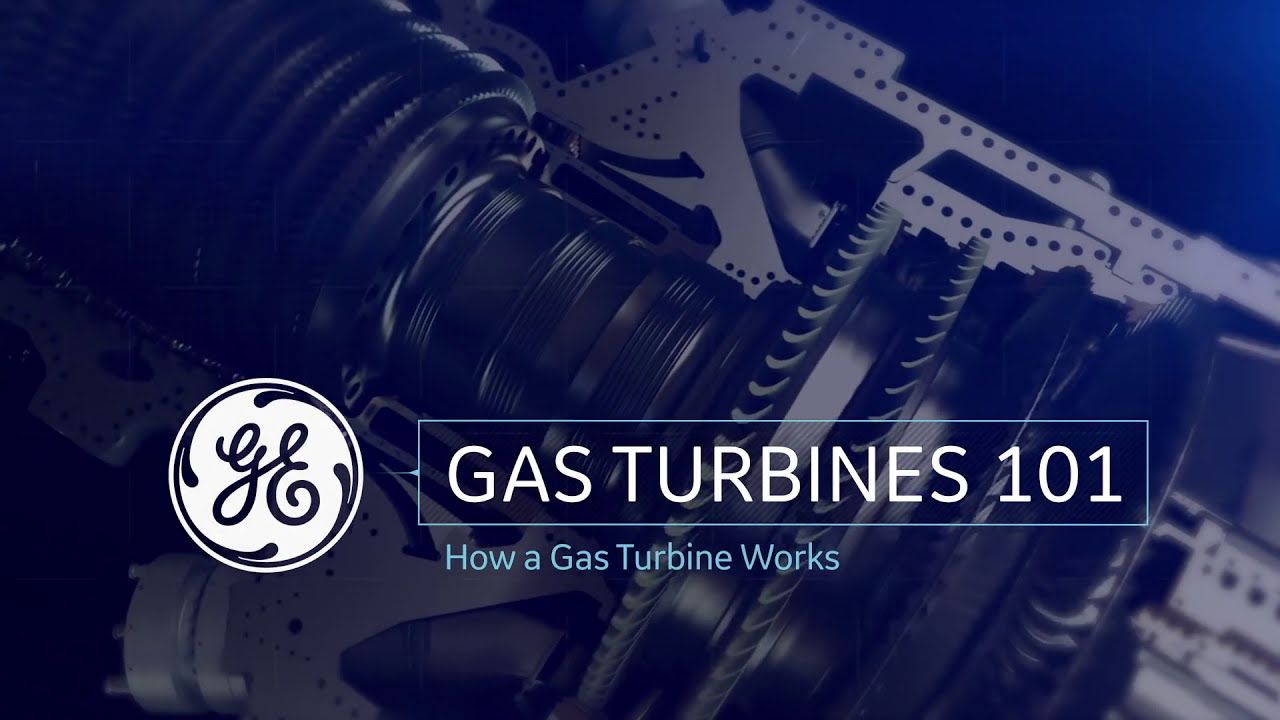
How a Gas Turbine Works | Gas Power Generation | GE Power

13 ATPL Training Gas Turbine Engines #13 Performance

DUAL FUEL ENGINES PART 5 - DOUBLE WALL PIPE VENTILATION SYSTEM
5.0 / 5 (0 votes)