Finite Element Analysis and Design of A Heavy Lift Padeye
Summary
TLDRThis video covers the structural finite element analysis (FEA) and design of a heavy lift pad-eye for an offshore platform. It details the modeling process, including dimensions, material properties, and load conditions, and emphasizes the importance of validating manual design calculations through FEA. The analysis focuses on bearing and shear stresses, comparing them to code requirements like API RP 2E. While the design met most requirements, the video highlights areas where stress exceeded allowable limits, suggesting plate thickness adjustments. It underscores the significance of FEA in ensuring the safety and compliance of large offshore structures.
Takeaways
- 😀 Manual calculations are used to verify the adequacy of a pad eye design for offshore platforms, focusing on bearing, shear, and combined principal stresses.
- 😀 Finite Element Analysis (FEA) is used to substantiate manual calculations, especially for extreme loads above 500 tons, as specified in MGP 220301.
- 😀 The total load on the pad eye is about 800 tons, a critical load that requires verification via FEA according to industry standards.
- 😀 The design must comply with the API RP2E code, ensuring that bearing stresses, shear stresses, and bending moments are within allowable limits.
- 😀 The pad eye's geometry, including dimensions like height, plate thicknesses, and hole diameters, must be modeled accurately to ensure proper analysis.
- 😀 Accurate load modeling, including the self-weight of the pad eye and lift weights, is essential for correct FEA results.
- 😀 The bearing stresses calculated by FEA show a range of 275–303 MPa, which is below the allowable limit of 310 MPa, indicating the design is satisfactory.
- 😀 Shear stresses in the pad eye are observed to increase significantly in certain regions, with a maximum stress of 156 MPa, which is higher than the allowable shear stress limit.
- 😀 To meet code requirements, adjustments may be necessary, such as increasing the thickness of the cheek plates or adding stiffener plates to reduce shear stresses.
- 😀 The primary benefit of FEA is its ability to show stress distribution across the entire pad eye, helping to optimize the design and ensure it meets safety standards.
Q & A
Why is finite element analysis (FEA) used to verify the manual calculations for the pad eye design?
-Finite element analysis (FEA) is used to verify the manual calculations because the load on the pad eye is extremely high, about 800 tons. The API RP 2E code specifies that loads exceeding 500 tons should be analyzed using FEA to ensure accuracy and compliance with safety standards.
What is the total load on the pad eye from the offshore winds?
-The total load on the pad eye from the offshore winds is approximately 800 tons, which is critical and requires thorough verification through FEA.
What are the key stresses that need to be verified in the pad eye design?
-The key stresses to be verified in the pad eye design are bearing stresses, shear stresses, and combined principal stresses, including those associated with axial and bending stresses.
What material specification is used for the pad eye plates according to the API RP 2E code?
-The material specification for the pad eye plates is API 2H grade 50. The allowable bearing stress is 0.9 times the yield stress of the material, which is 345 MPa.
What is the maximum allowable bearing stress for the pad eye, according to the code?
-The maximum allowable bearing stress for the pad eye is 310 MPa, which is 0.9 times the yield stress of the material (345 MPa).
How are the bearing stresses distributed throughout the pad eye?
-The bearing stresses on the pad eye vary across the structure, with values ranging from 303 MPa near the center, reducing to around 160 MPa at other regions, and this distribution is critical for determining the adequacy of the design.
What did the finite element analysis reveal about the shear stresses in the pad eye?
-The finite element analysis revealed that shear stresses are highest near the center of the pad eye, reaching up to 156 MPa, which exceeds the allowable shear stress of 110 MPa according to the code. This indicates that the design may need modifications, such as adding stiffener plates.
What does the design calculation for the pad eye's bearing stress suggest regarding its thickness?
-The design calculation suggests that the required thickness for the pad eye is 5.43 inches, and the modeled thickness of 5.5 inches exceeds this requirement, ensuring that the design is adequate for bearing stresses.
What action might be required based on the shear stress distribution in the pad eye?
-Based on the shear stress distribution, it may be necessary to increase the thickness of the cheek plates or add stiffener plates to reduce the shear stresses in regions where they exceed the allowable limits.
Why is it important to conduct a finite element analysis for heavy lift operations exceeding 500 tons?
-It is important to conduct a finite element analysis for heavy lift operations exceeding 500 tons to ensure that the pad eye can handle the extreme loads safely. FEA provides detailed insights into stress distributions, which are critical for verifying the integrity and safety of the design.
Outlines
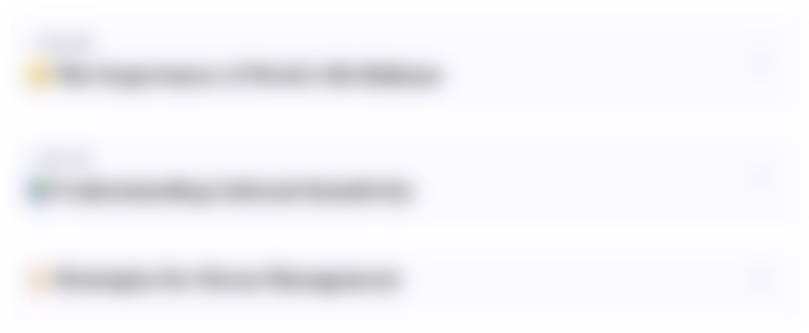
Esta sección está disponible solo para usuarios con suscripción. Por favor, mejora tu plan para acceder a esta parte.
Mejorar ahoraMindmap
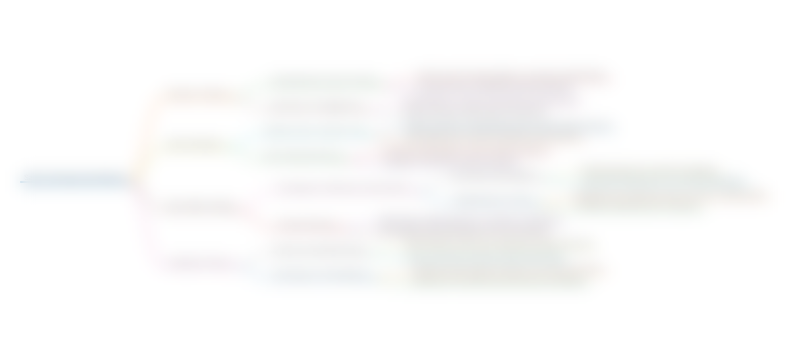
Esta sección está disponible solo para usuarios con suscripción. Por favor, mejora tu plan para acceder a esta parte.
Mejorar ahoraKeywords
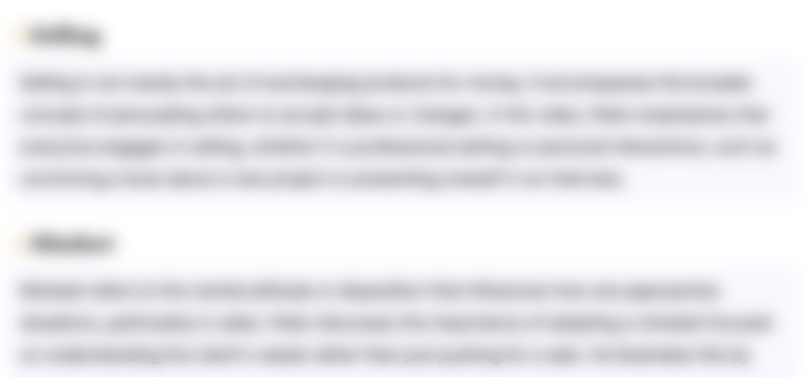
Esta sección está disponible solo para usuarios con suscripción. Por favor, mejora tu plan para acceder a esta parte.
Mejorar ahoraHighlights
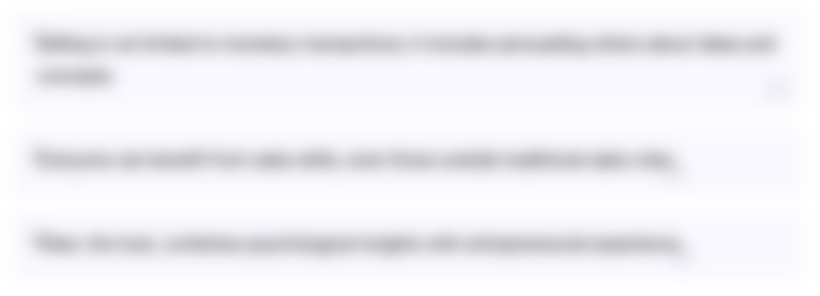
Esta sección está disponible solo para usuarios con suscripción. Por favor, mejora tu plan para acceder a esta parte.
Mejorar ahoraTranscripts
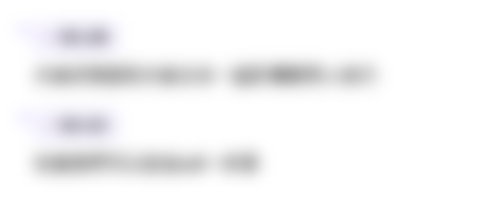
Esta sección está disponible solo para usuarios con suscripción. Por favor, mejora tu plan para acceder a esta parte.
Mejorar ahora5.0 / 5 (0 votes)