Pitch sobre Critérios de Escoamento de Metais Dúcteis
Summary
TLDRThis video delves into the concept of flow criteria for ductile metals, focusing on the transition between elastic and plastic deformation. It explains how the ductility of a material allows for plastic deformation without failure and highlights key mechanical properties like elasticity modulus, yield stress, and Poisson's ratio. The video also touches on failure mechanisms, including fatigue and ductile fracture. It discusses the use of finite element analysis (FEA) to predict material behavior, reduce prototyping costs, and enhance safety. Through practical examples, it showcases how FEA helps in material selection and design optimization in engineering applications.
Takeaways
- 😀 Ductility refers to a material's ability to undergo significant plastic deformation before failure, which is crucial in metal forming processes.
- 😀 Flow criteria for ductile metals define the transition from elastic deformation (reversible) to plastic deformation (irreversible).
- 😀 Yield stress is the critical stress point where deformation transitions from elastic to plastic, and it is key in determining material performance.
- 😀 The modulus of elasticity measures a material’s rigidity and is an important factor in understanding flow criteria.
- 😀 Poisson's ratio relates axial strain to lateral strain and is used in evaluating material behavior under stress.
- 😀 Fatigue refers to the weakening of materials due to repeated cyclic loading, which can cause failure even if the individual loads are below the yield stress.
- 😀 Ductile fracture occurs when a material undergoes significant plastic deformation (necking) followed by rupture.
- 😀 Failure criteria like the Von Mises and Tresca criteria help predict material failure under stress, with Von Mises being more common in FEA due to its simplicity.
- 😀 Finite Element Analysis (FEA) is used to simulate and predict material behavior under various loading conditions, helping optimize designs and reduce failure risk.
- 😀 Real-world applications of FEA include assessing the integrity of components with discontinuities (e.g., lead-tin alloy devices) and identifying stress concentrations in metal structures to prevent failure.
Q & A
What is flow stress, and how is it related to elastic and plastic deformation?
-Flow stress refers to the transition between elastic deformation, which is reversible, and plastic deformation, which is irreversible. It marks the point where the material starts to deform plastically, and beyond this point, the deformation is permanent.
What does ductility mean in materials?
-Ductility is the ability of a material to undergo significant plastic deformation before failure. It allows the material to be formed without breaking.
What are the key mechanical properties involved in the flow stress process?
-The key mechanical properties include the elasticity modulus (which indicates the material's rigidity), the yield stress (which is the stress at which material starts transitioning from elastic to plastic deformation), and the Poisson's ratio (which relates the strain in the material's transverse direction to the strain in its longitudinal direction).
What is the significance of the yield stress in ductile materials?
-The yield stress is the point where elastic deformation transitions into plastic deformation. It is critical because, above this stress, all further deformation is permanent and irrecoverable.
What are fatigue and fracture in the context of ductile metals?
-Fatigue in ductile metals refers to the weakening of a material due to cyclic loading over time, where the stress is below the yield stress. Fracture occurs when plastic deformation is followed by rupture, often involving necking, which is a localized reduction in cross-sectional area before failure.
What are the two main failure criteria for ductile metals discussed?
-The two main failure criteria are the von Mises criterion, which predicts failure when the second variant of stress exceeds a critical value, and the Tresca criterion, which applies when the maximum shear stress reaches a critical value.
How do finite element analysis (FEA) and failure criteria help in testing metal materials?
-FEA, combined with failure criteria, allows for virtual testing of different failure conditions under various loads and geometries. This helps predict potential failures, reduces the need for costly physical prototypes, and enhances the reliability and safety of the material.
What are the three types of variables considered in finite element analysis for material testing?
-The three variables are material properties (mechanical and thermal), geometry (including 3D coordinates and shape), and boundary conditions (which include forces, pressures, degrees of freedom, and temperature).
How does finite element analysis contribute to cost reduction and safety in product design?
-By simulating various stress scenarios and failure points, FEA helps identify potential issues before physical testing, reducing trial-and-error costs, enhancing product safety, and optimizing designs, such as creating lighter aircraft that consume less fuel.
Can you provide an example where finite element analysis was used to improve material choice and safety?
-In one case, FEA analysis revealed that a lead-tin alloy used in a device had a von Mises stress higher than the material's yield stress, indicating a risk of failure. As a result, the material was switched to A36 steel, which had a lower stress, ensuring the device was both safe and reliable.
Outlines
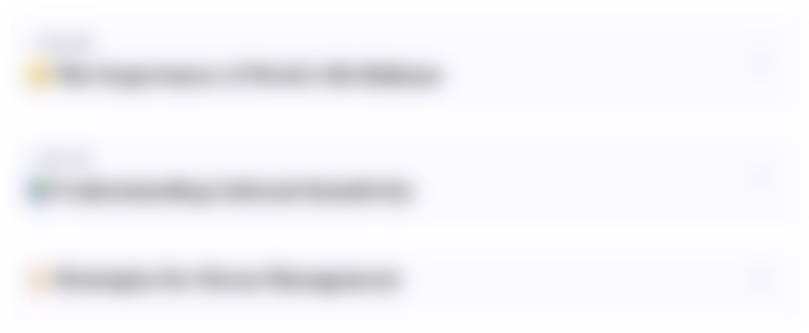
This section is available to paid users only. Please upgrade to access this part.
Upgrade NowMindmap
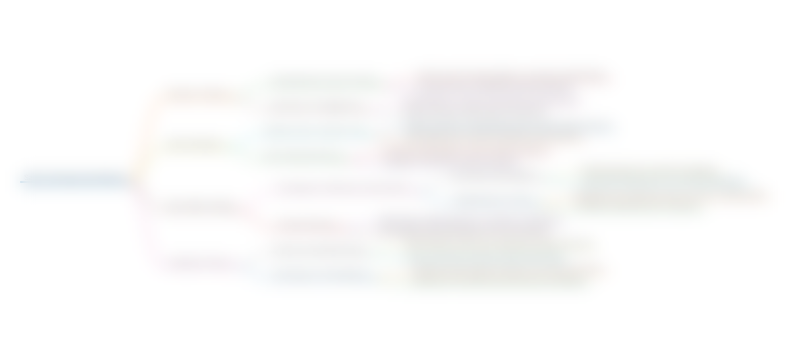
This section is available to paid users only. Please upgrade to access this part.
Upgrade NowKeywords
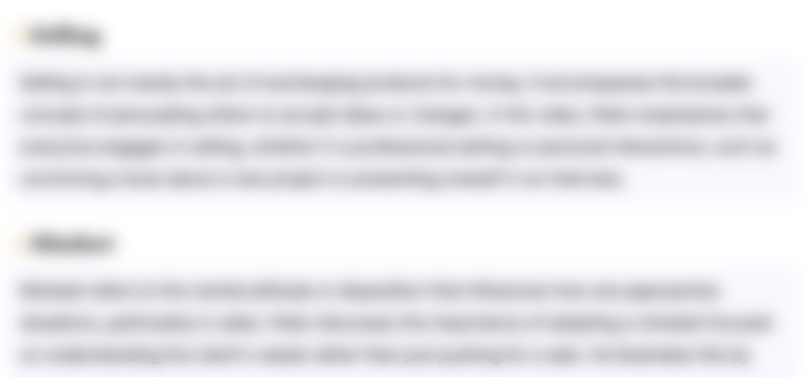
This section is available to paid users only. Please upgrade to access this part.
Upgrade NowHighlights
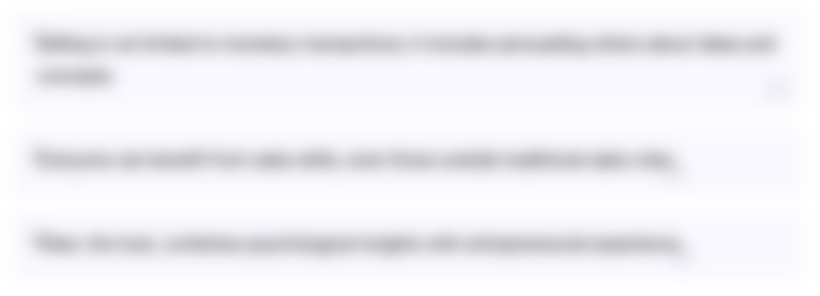
This section is available to paid users only. Please upgrade to access this part.
Upgrade NowTranscripts
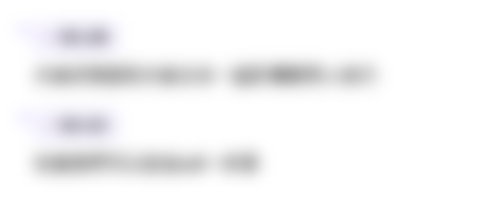
This section is available to paid users only. Please upgrade to access this part.
Upgrade NowBrowse More Related Video
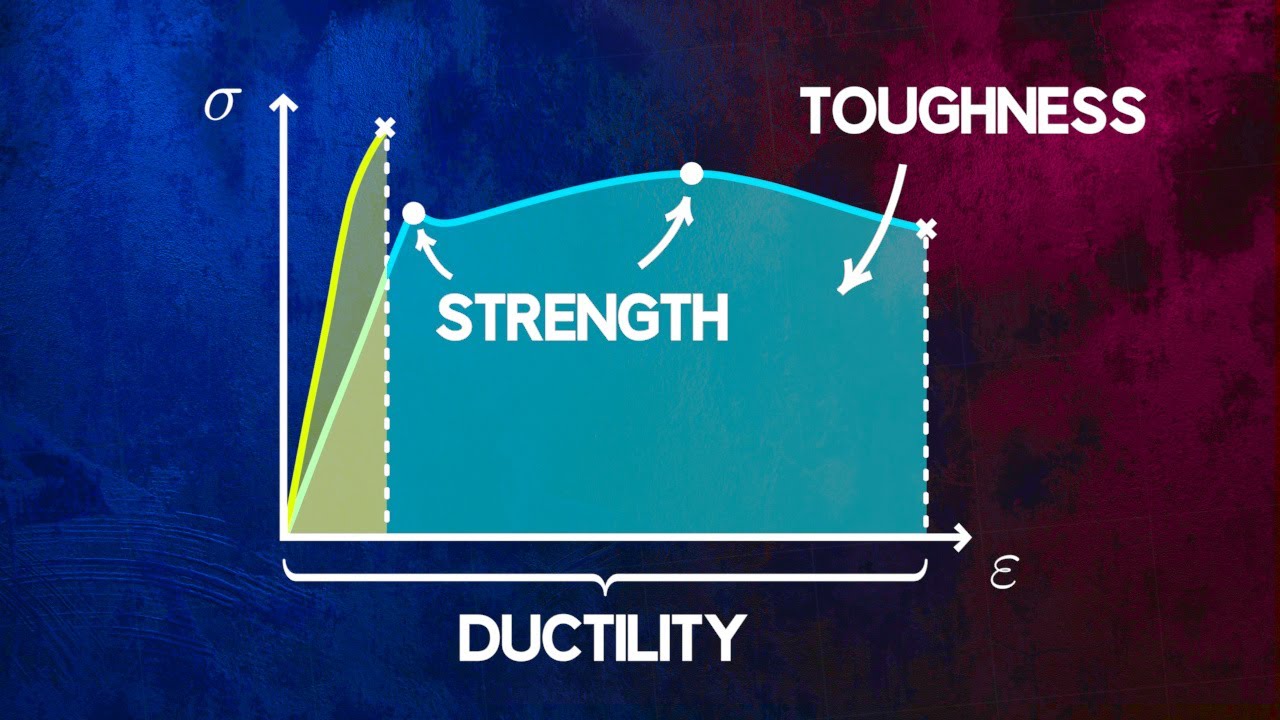
Understanding Material Strength, Ductility and Toughness

Yield Strength and Resilience of Materials | Basic Concepts | Materials Science And Engineering

#AghamUnite: Deformation of the Crust
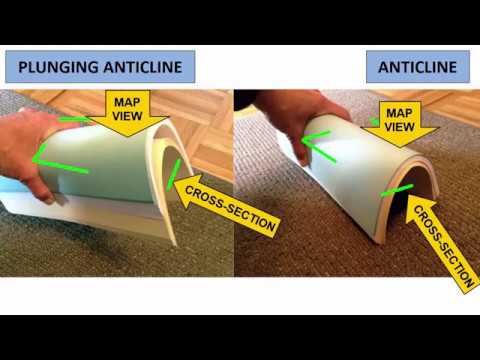
Folds and Faults

Materiais e Processos de Fabricação para Engenharia de Produção - Processos de Laminação
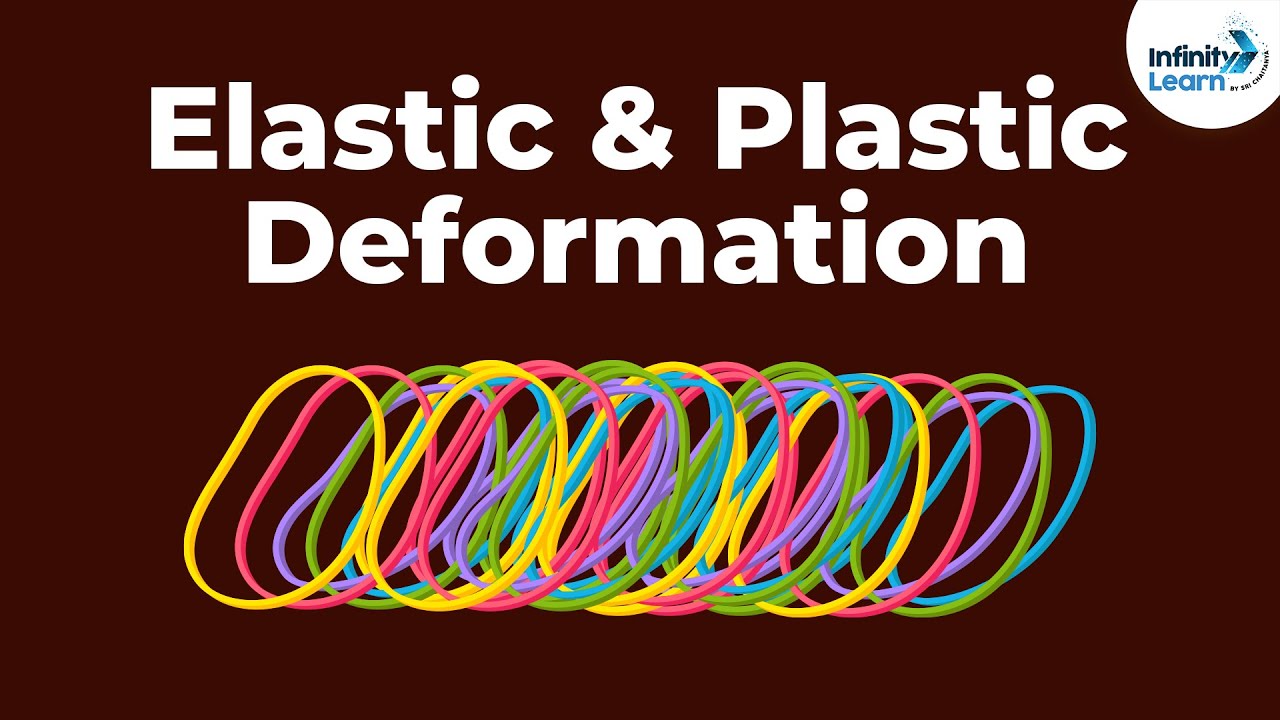
Elastic Deformation and Plastic Deformation | Mechanical Properties of Solids | Don't Memorise
5.0 / 5 (0 votes)