3D Printing a Lamborghini Aventador!
Summary
TLDRIn this remarkable journey, Sterling and his son embarked on building a 3D printed Lamborghini Aventador, showcasing innovation, resourcefulness, and craftsmanship. Starting with a small CR-10s printer and PLA material, they overcame challenges like the heat resistance of PLA by laminating carbon fiber for durability. The project, involving custom parts, a Corvette engine, and Porsche transmission, is a testament to their dedication. With support from the 3D printing community and even Lamborghini itself, the duo created a unique car that blends cutting-edge technology with classic automotive design. The project continues, with plans for a car show debut in August.
Takeaways
- 😀 Sterling and his son began the 3D-printed Lamborghini Aventador SV project five years ago with a CR-10 3D printer.
- 😀 The car's body panels were 3D printed in PLA and reinforced with carbon fiber for added strength and durability.
- 😀 The PLA also provided an unexpected benefit of sound dampening, making the car's body feel more solid.
- 😀 The CR-10s printer was used for over a year before being replaced with a larger Equity X-Max printer for more advanced printing.
- 😀 ASA material was used for interior and exterior parts exposed to the sun, as it’s UV stable and has a higher glass transition temperature than PLA.
- 😀 Lamborghini donated authentic headlights to the project after being impressed by Sterling’s efforts and passion.
- 😀 The windshield of the car was sourced from a Pacifica minivan, modified with the help of Chip Pros for a custom fit.
- 😀 Sterling and his son designed a custom door hinge mechanism after failing to replicate the original Lamborghini hinge, with guidance from a friend in Texas.
- 😀 The engine is an LS1 V8 from a 2005 Corvette, paired with a Porsche 911 transaxle, with help from the 3D printing community to connect the parts.
- 😀 The completed 3D-printed Lamborghini is lighter than the real Aventador SV, weighing around 2,700 pounds, compared to the original's 4,000 pounds.
- 😀 The car will be showcased at a car show at Bandimere Speedway near Denver in August 2025, marking a significant milestone for the project.
Q & A
How long ago did Sterling and his son start the 3D printed Lamborghini project?
-Sterling and his son started the 3D printed Lamborghini project about five years ago.
What was the first step they took in learning how to 3D print a car?
-They began by going to 'YouTube University' and watching videos, including one from the interviewer’s channel, to learn about 3D printing and gather information on how to start the project.
What material did Sterling and his son initially use for the 3D printing?
-They initially used PLA material for the 3D printing, which is commonly used for smaller, less structurally demanding prints.
Why did they choose to laminate the 3D printed parts with carbon fiber?
-They laminated the 3D printed parts with carbon fiber to improve their structural integrity, making them more durable and able to withstand Colorado's hot summers, as well as providing sound-dampening properties.
What is the benefit of using PLA material in the 3D printed panels?
-PLA provides sound-dampening benefits inside the 3D printed panels, helping to reduce the 'tinny' sound that is common with carbon fiber panels, creating a more solid feel.
What type of 3D printer did Sterling and his son use for the initial phase of the project?
-They used a small CR-10s 3D printer, which was a consumer-level machine but capable of producing large-format prints.
How did Sterling upgrade the 3D printing process once the CR-10s failed?
-Sterling upgraded to an Equity X Max 3D printer, which was provided to him after a Lamborghini commercial was made featuring his project.
What material did Sterling switch to for more durable parts?
-Sterling switched to ASA material for more durable parts, as it has a higher glass transition temperature and is UV stable, making it more suitable for Colorado's harsh sun and outdoor exposure.
What are the main custom parts in the car’s frame?
-The custom parts in the frame include the main support for the occupants, made from 2x4 steel tubing with a 120-wall thickness, making it sturdy yet lighter than the real Lamborghini.
How does the door hinge mechanism on the 3D printed Lamborghini differ from the original design?
-The custom door hinge design allows the door to move both up and outward at a 30-degree angle. Although the original Lamborghini hinge costs around $1,000, Sterling created a more affordable custom solution with help from a friend in Texas.
Outlines
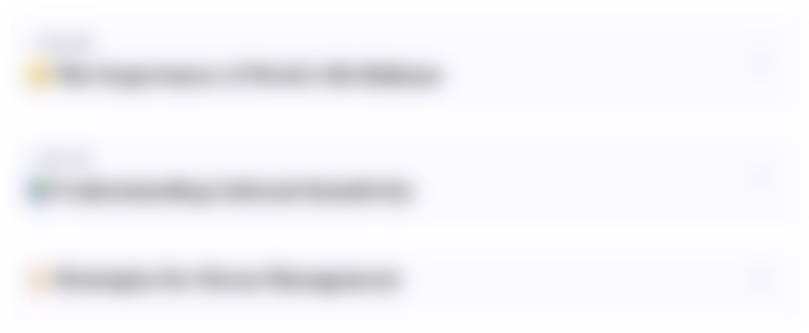
Esta sección está disponible solo para usuarios con suscripción. Por favor, mejora tu plan para acceder a esta parte.
Mejorar ahoraMindmap
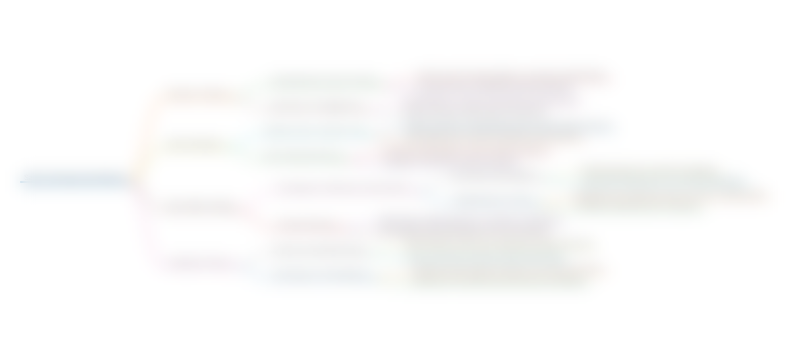
Esta sección está disponible solo para usuarios con suscripción. Por favor, mejora tu plan para acceder a esta parte.
Mejorar ahoraKeywords
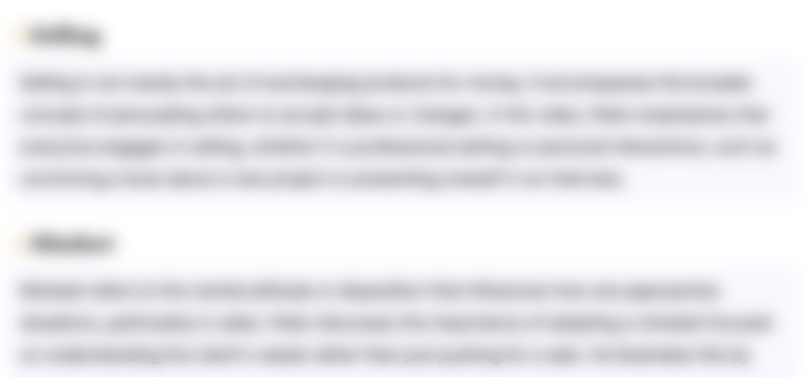
Esta sección está disponible solo para usuarios con suscripción. Por favor, mejora tu plan para acceder a esta parte.
Mejorar ahoraHighlights
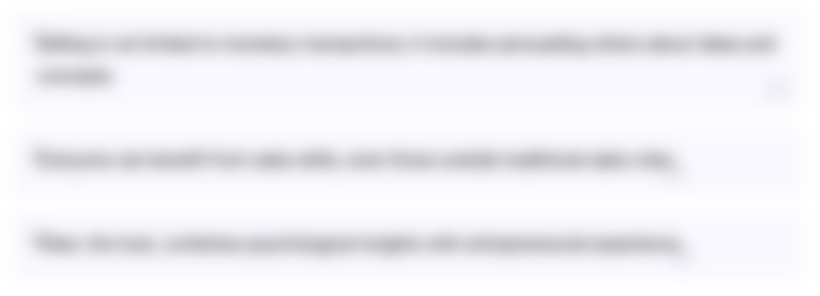
Esta sección está disponible solo para usuarios con suscripción. Por favor, mejora tu plan para acceder a esta parte.
Mejorar ahoraTranscripts
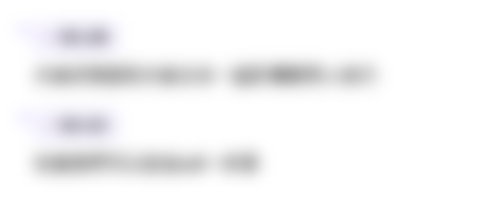
Esta sección está disponible solo para usuarios con suscripción. Por favor, mejora tu plan para acceder a esta parte.
Mejorar ahoraVer Más Videos Relacionados

爆音F1サウンドww 笑いが止まらなさすぎたwランボルギーニ アヴェンタドールSV パワクラ
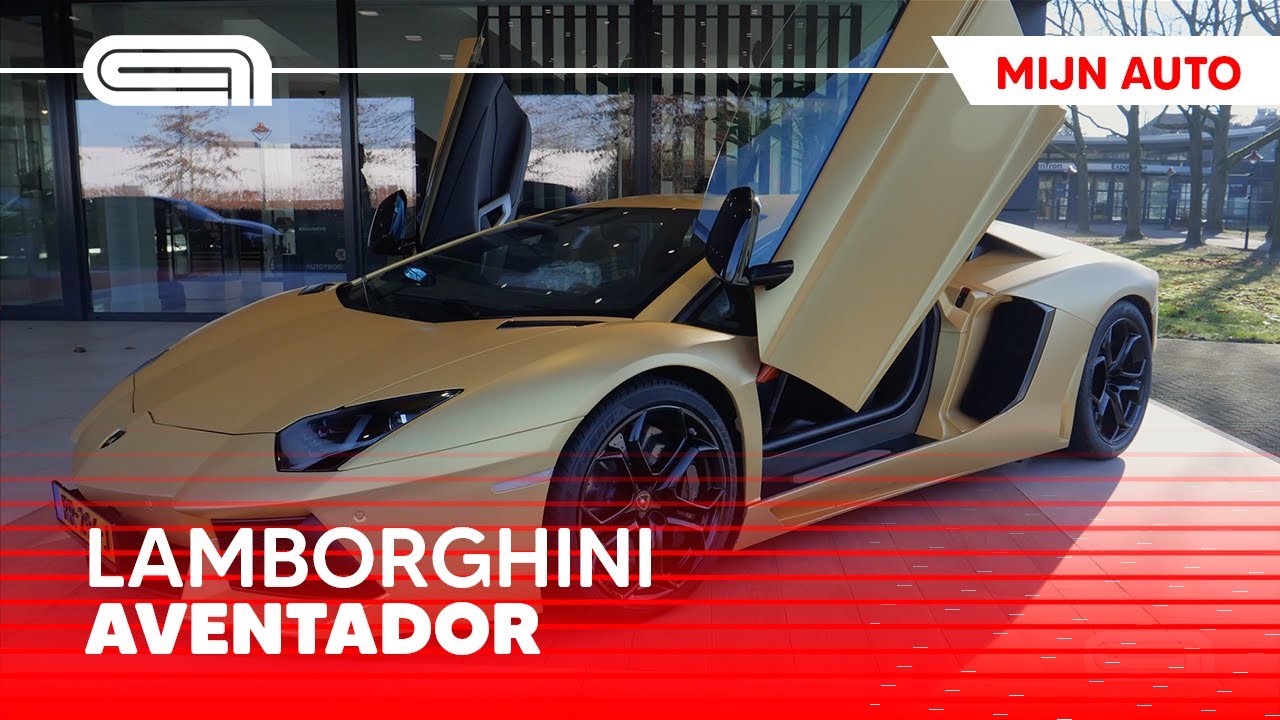
Mijn Auto: Lamborghini Aventador van Richard
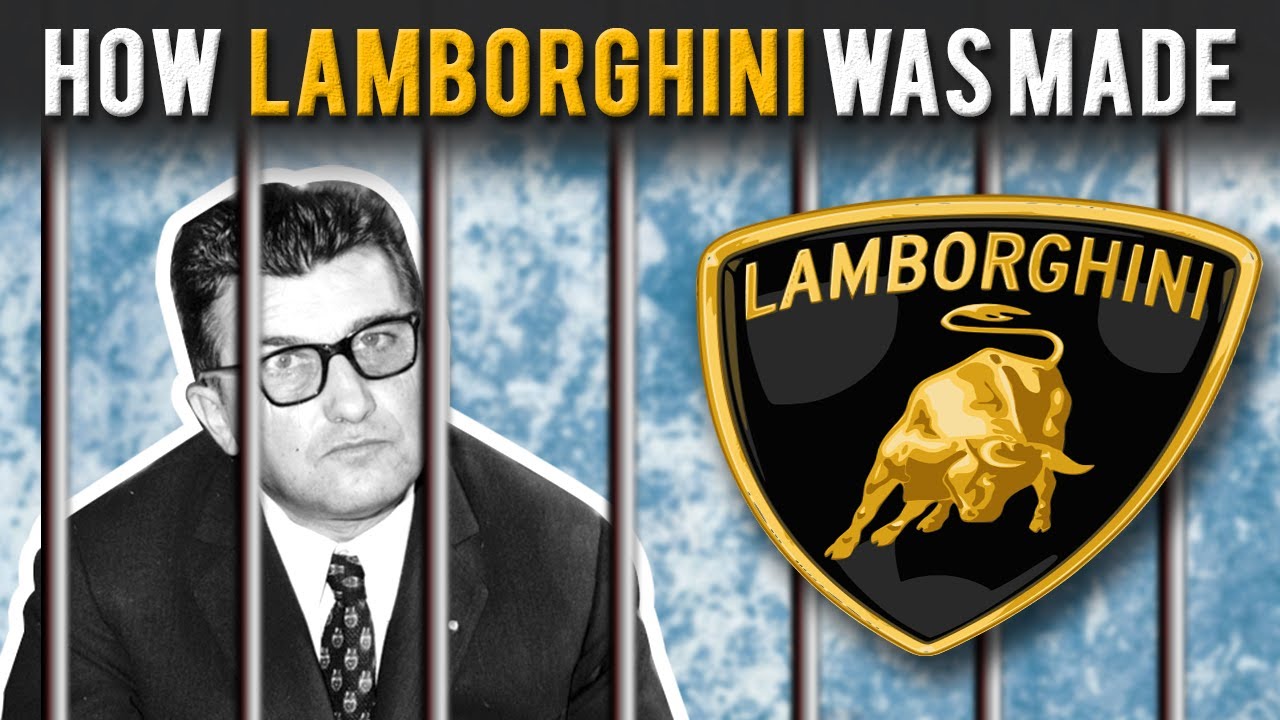
How Ferrari Motivated This Former Prisoner To Invent Lamborghini
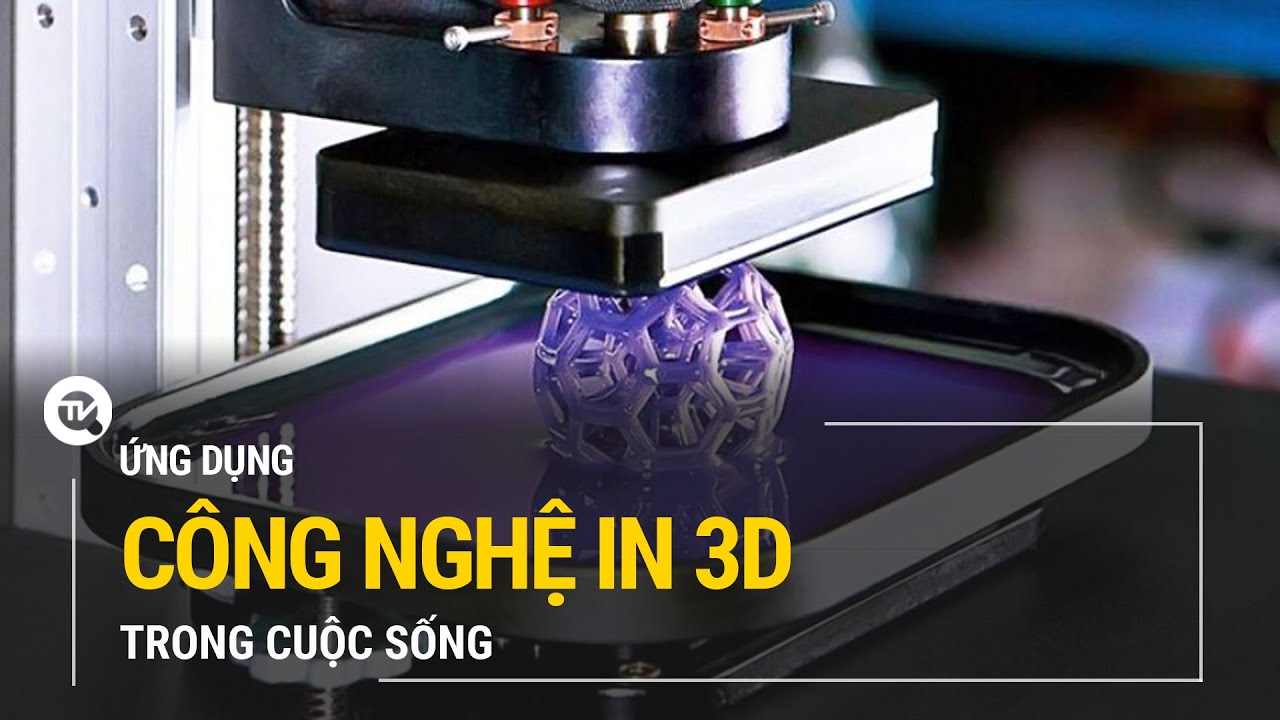
Nhìn ra thế giới: Ứng dụng công nghệ in 3D trong cuộc sống | Truyền hình Quốc hội Việt Nam

From Welfare to a BILLION Dollar Empire - How I Afford My $30 Million Car Collection!

Deswegen hat er den Aventador gekauft…😳🦇
5.0 / 5 (0 votes)