QFD (Quality Function Deployment): With Practical Example (PART-1)
Summary
TLDRThis video explains Quality Function Deployment (QFD), a methodology that transforms customer needs into technical specifications. Developed in the 1960s in Japan, QFD is used globally across industries like manufacturing, healthcare, and services. The process involves four phases: Product Definition, Product Development, Process Development, and Process Quality Control. The 'House of Quality' matrix is a central tool that aligns customer desires with design features. QFD enhances communication, reduces development time, and ensures that products meet customer expectations, ultimately boosting competitiveness and efficiency in product development.
Takeaways
- 📊 QFD, or Quality Function Deployment, was developed in Japan in the late 1960s and is used to translate customer requirements into engineering specifications.
- 🚗 Initially adopted by automotive companies in the US, QFD is now utilized across various industries, including healthcare and services.
- 🔍 QFD focuses on the Voice of the Customer (VOC), ensuring that customer needs and expectations are at the forefront of product development.
- 🏠 The House of Quality is a key tool in QFD that connects customer wants ('Whats') with design features ('Hows').
- 🗣️ Effective communication of customer needs throughout an organization is essential for creating products with high perceived value.
- ⏳ Implementing QFD can lead to shorter development times and lower costs by preventing late design changes and focusing on value-added features.
- 📈 The QFD process includes four phases: Product Definition, Product Development, Process Development, and Process Quality Control.
- 🔗 The QFD methodology promotes teamwork and discipline, creating a collaborative environment for product development.
- 📋 The House of Quality matrix captures customer requirements, importance factors, design features, and competitor comparisons in one place.
- 🔄 After completing the House of Quality, the derived technical requirements are deployed to relevant teams for further analysis in Level 2 QFD.
Q & A
What is Quality Function Deployment (QFD)?
-Quality Function Deployment (QFD) is a methodology used to translate the Voice of the Customer (VOC) into measurable design specifications, ensuring that the product meets customer requirements. It focuses on aligning product features with customer needs throughout the product development process.
Who developed QFD and when?
-QFD was developed by Yoji Akao in Japan in the late 1960s while he was working for Mitsubishi's shipyard. It was later adopted by other companies, including Toyota, and eventually spread to industries outside of Japan, such as the U.S. automotive sector in the 1980s.
What industries currently use QFD?
-QFD is used in a wide range of industries including manufacturing, healthcare, automotive, electronics, and service organizations. It helps companies design products that meet customer needs effectively.
What are the main benefits of implementing QFD?
-The main benefits of QFD include a stronger focus on customer needs, reduced development time and costs, enhanced communication between departments, improved product quality, and the ability to compare your product with competitors to gain a competitive advantage.
How does QFD improve communication within an organization?
-QFD improves communication by providing a structured framework for sharing customer requirements across multiple business functions, including design, marketing, manufacturing, and production. This ensures that every department is aligned with the same customer-focused goals.
What are the four phases of QFD?
-The four phases of QFD are: 1) Product Definition, where customer needs are translated into product specifications; 2) Product Development, where critical parts and assemblies are identified; 3) Process Development, where manufacturing processes are designed; and 4) Process Quality Control, which ensures that processes meet customer requirements before full-scale production.
What is the 'House of Quality' in QFD?
-The 'House of Quality' is a matrix used in QFD to translate customer requirements (Whats) into design features (Hows). It visually represents the relationships between customer needs and design parameters, helping teams focus on fulfilling customer expectations.
How do you determine the importance of each customer requirement in QFD?
-Customer requirements are typically ranked on a scale of 1 to 5, with 5 representing the highest importance. These ratings help prioritize design features and guide resource allocation during product development.
What is the correlation matrix in the House of Quality used for?
-The correlation matrix in the House of Quality is used to show how each design feature (How) correlates with customer requirements (What). It helps identify strong, moderate, or weak relationships between them and guides the development of technical specifications.
How does QFD help reduce development time and costs?
-QFD reduces development time and costs by ensuring that the product design is directly aligned with customer needs from the beginning. This reduces the likelihood of costly late-stage design changes and prevents wasted resources on non-value-added features.
Outlines
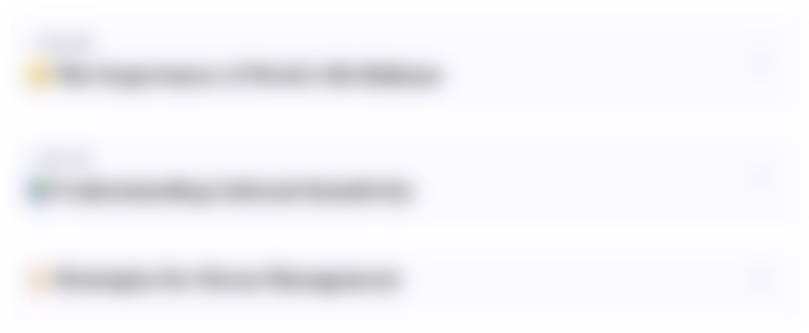
Esta sección está disponible solo para usuarios con suscripción. Por favor, mejora tu plan para acceder a esta parte.
Mejorar ahoraMindmap
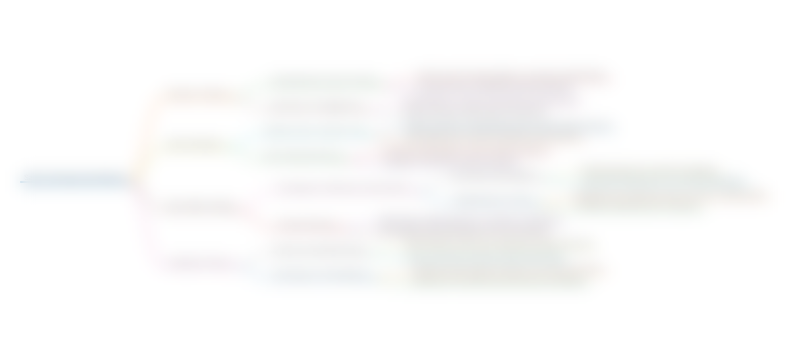
Esta sección está disponible solo para usuarios con suscripción. Por favor, mejora tu plan para acceder a esta parte.
Mejorar ahoraKeywords
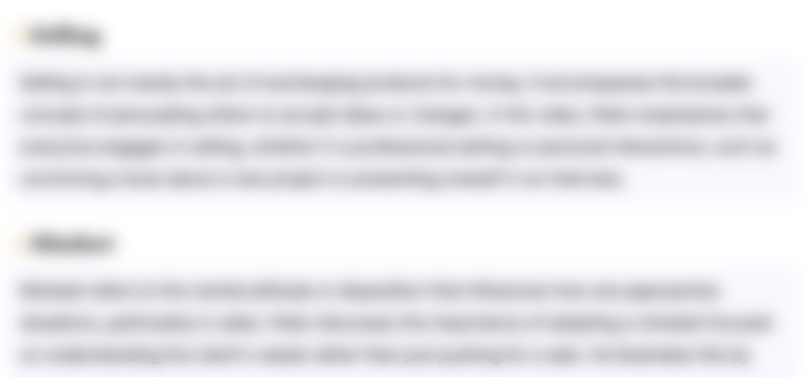
Esta sección está disponible solo para usuarios con suscripción. Por favor, mejora tu plan para acceder a esta parte.
Mejorar ahoraHighlights
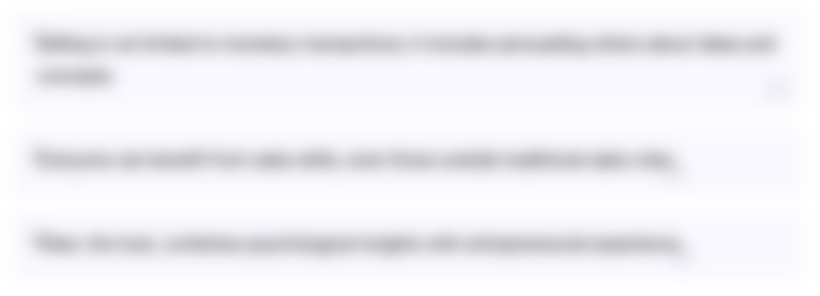
Esta sección está disponible solo para usuarios con suscripción. Por favor, mejora tu plan para acceder a esta parte.
Mejorar ahoraTranscripts
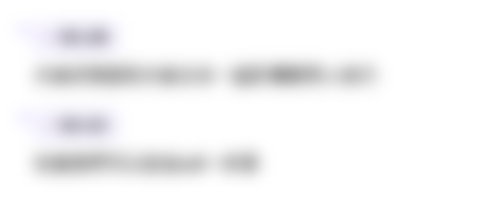
Esta sección está disponible solo para usuarios con suscripción. Por favor, mejora tu plan para acceder a esta parte.
Mejorar ahoraVer Más Videos Relacionados

QUALITY FUNCTION DEPLOYMENT QFD
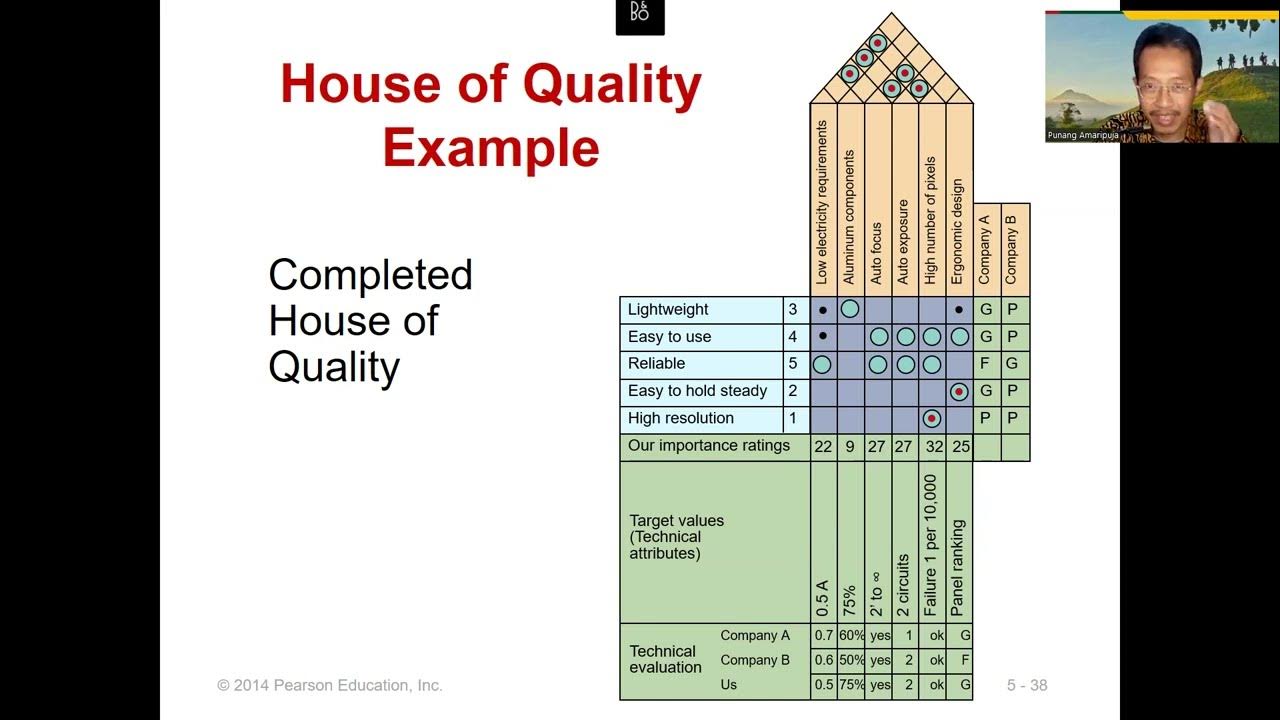
House of Quality (QFD) || Dr Punang Amaripuja Serial Operasi dan Teknologi - MOT 05B
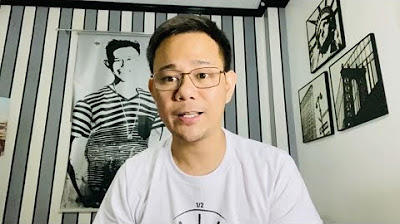
CBME 1 | Lesson 2 | Part 1/3

Penetapan Produk Unggul dan Manajemen Inovasi

Manage quality customer service

SOAL DAN PEMBAHASAN SKB PENGELOLA PENGADAAN BARANG/JASA MATERI PENYUSUNAN SPESIFIKASI TEKNIS PART 1
5.0 / 5 (0 votes)