Studi Kasus Manajemen Risiko Mutu untuk aplikasi Kualifikasi Pemasok sesuai CPOB
Summary
TLDRThis video script focuses on risk management in the pharmaceutical industry, particularly in the qualification of raw materials (Active Pharmaceutical Ingredients) to meet JPOB standards. It outlines a risk analysis process using the APERMIA method to evaluate potential failure points in raw material qualification. The process involves assessing risks based on severity, occurrence likelihood, and detectability, with the goal of identifying corrective actions to mitigate high-risk issues. The video encourages viewers to complete tasks related to identifying failures, determining their causes, and assessing their risks to ensure product quality and regulatory compliance.
Takeaways
- 😀 PT. Farmasi Z produces various pharmaceutical products and focuses on maintaining product quality and regulatory compliance with Good Pharmaceutical Manufacturing Practices (JPOB).
- 😀 The case study focuses on the qualification of raw materials, particularly Active Pharmaceutical Ingredients (APIs), to ensure quality and adherence to standards.
- 😀 The goal of the case study is to identify potential failure modes in the raw material qualification process and analyze their impact on product quality and compliance.
- 😀 The analysis involves assessing the severity, occurrence, and detectability of each failure mode to determine the risk associated with it.
- 😀 The risk assessment follows the Apemia method, which uses a formula to calculate risk: Severity × Likelihood + Detectability.
- 😀 Risks are evaluated on a scale from 1 to 10, with higher values representing more severe, frequent, or undetectable issues that pose a significant threat to product quality or safety.
- 😀 Severity refers to the impact of a failure on product quality or safety, with a score of 10 indicating major safety concerns.
- 😀 Occurrence probability is the likelihood of a failure happening, with a score of 10 indicating a very frequent occurrence.
- 😀 Detectability measures how easily a failure can be detected, with a score of 1 indicating easy detection and a score of 10 indicating no ability to detect the failure.
- 😀 Based on the risk evaluation, corrective actions are determined to mitigate high-risk issues and improve the qualification process to ensure product quality and regulatory compliance.
Q & A
What is the main goal of the case study?
-The main goal of the case study is to identify potential failure points in the supplier qualification process for active pharmaceutical ingredients (API), analyze the impact of each failure on product quality, and assess compliance with Good Pharmaceutical Manufacturing Practice (JPOB) regulations.
What methodology is used to analyze the risks in the case study?
-The APERMIA (Analysis, Probability, and Evaluation Method for Impact Analysis) method is used to analyze the risks. This method involves identifying potential failures, assessing their severity, probability, and detectability, and calculating a risk score to determine appropriate corrective actions.
What are the key factors assessed in the APERMIA risk analysis method?
-The APERMIA risk analysis method assesses three key factors for each potential failure: Severity (S), Occurrence (O), and Detectability (D). These factors are rated on a scale from 1 to 10 and used to calculate the overall risk score.
How is the risk score calculated in the APERMIA method?
-The risk score is calculated by multiplying the three factors: Severity (S), Occurrence (O), and Detectability (D). The formula is: Risk Score = S × O × D.
What is the scale for each factor (Severity, Occurrence, and Detectability)?
-Each factor is rated on a scale of 1 to 10. Severity (S) ranges from 1 (minor impact) to 10 (severe impact), Occurrence (O) ranges from 1 (rare occurrence) to 10 (frequent occurrence), and Detectability (D) ranges from 1 (easy to detect) to 10 (difficult to detect).
What is the significance of the risk score in the APERMIA method?
-The risk score helps determine the level of risk associated with each failure. A high risk score (128-200) indicates the need for immediate corrective action, while a lower score (2-7) indicates a lower risk that may require less immediate attention.
What is the purpose of identifying failure points in the raw material qualification process?
-Identifying failure points helps the company anticipate potential risks that could compromise product quality or regulatory compliance, allowing for proactive measures to mitigate these risks.
How does the case study assess the impact of potential failures?
-The case study assesses the impact of potential failures by analyzing how each failure could affect product quality and compliance with JPOB regulations. This impact is quantified through the Severity factor in the risk analysis.
What are the main tasks assigned to participants in this case study?
-Participants are tasked with identifying potential failure points in the supplier qualification process, determining the causes and effects of these failures, and performing a risk evaluation by assessing Severity, Occurrence, and Detectability.
What is the significance of performing a risk evaluation in this case study?
-Performing a risk evaluation is crucial for prioritizing risks and determining appropriate corrective actions. It helps ensure that high-risk issues are addressed promptly to protect product quality and regulatory compliance.
Outlines
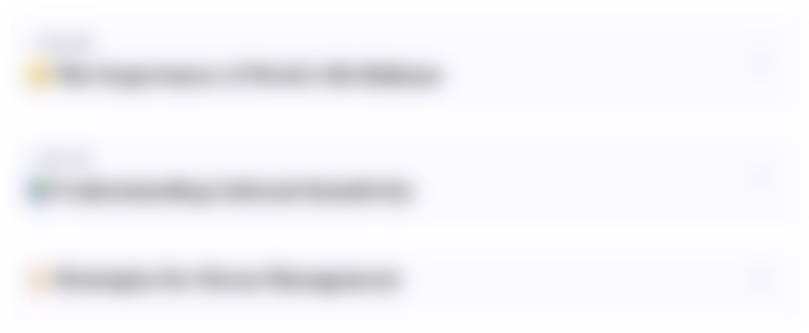
Esta sección está disponible solo para usuarios con suscripción. Por favor, mejora tu plan para acceder a esta parte.
Mejorar ahoraMindmap
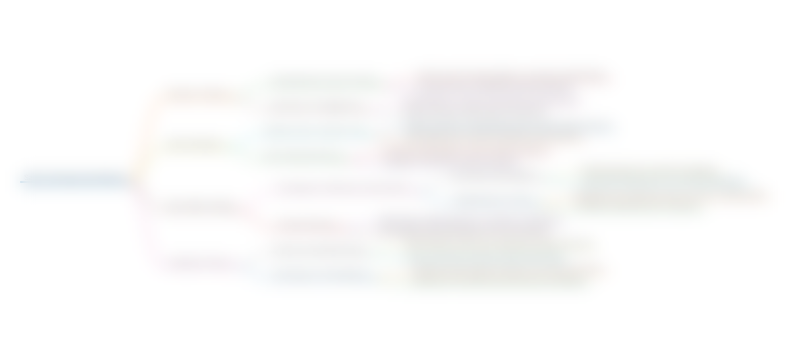
Esta sección está disponible solo para usuarios con suscripción. Por favor, mejora tu plan para acceder a esta parte.
Mejorar ahoraKeywords
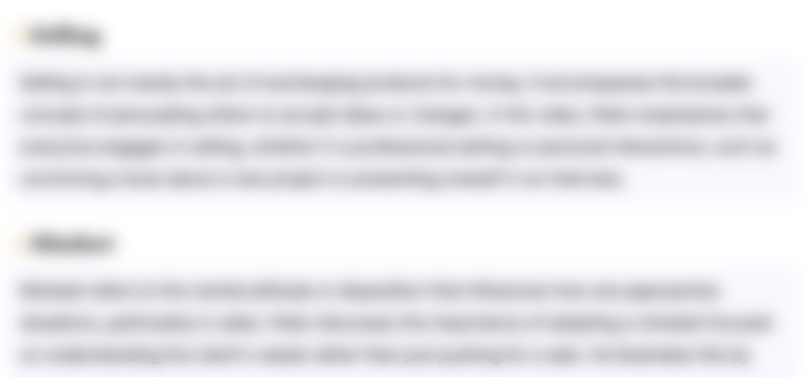
Esta sección está disponible solo para usuarios con suscripción. Por favor, mejora tu plan para acceder a esta parte.
Mejorar ahoraHighlights
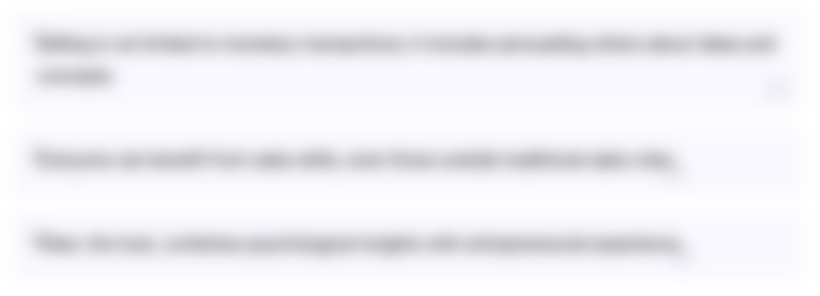
Esta sección está disponible solo para usuarios con suscripción. Por favor, mejora tu plan para acceder a esta parte.
Mejorar ahoraTranscripts
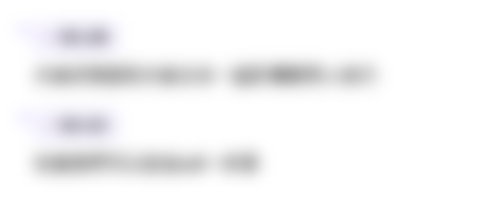
Esta sección está disponible solo para usuarios con suscripción. Por favor, mejora tu plan para acceder a esta parte.
Mejorar ahora5.0 / 5 (0 votes)