tugas
Summary
TLDRThis video introduces Total Quality Management (TQM), a management philosophy aimed at consistently meeting customer expectations through organizational-wide involvement. It outlines the eight principles of TQM, including customer focus, leadership, employee participation, and continuous improvement. While TQM can be costly and challenging to implement due to the time and resources required, it can lead to long-term success, as demonstrated by companies like Toyota. By fostering a culture of quality and continuous improvement, TQM helps organizations achieve growth, enhance customer satisfaction, and improve internal processes.
Takeaways
- 😀 TQM (Total Quality Management) focuses on integrating all functions of an organization to meet customer needs and organizational goals.
- 😀 TQM emphasizes the involvement of everyone in the organization, from top management to employees, to ensure quality at every level.
- 😀 The core of TQM is to meet or exceed customer expectations by delivering consistent, high-quality products and services.
- 😀 The eight principles of TQM are: Customer Focus, Leadership, Employee Involvement, Process Approach, Strategic Approach, Continuous Improvement, Factual Decision-Making, and Mutually Beneficial Supplier Relationships.
- 😀 Customer Focus ensures that the company understands and meets customer needs at all times, placing the customer at the center of operations.
- 😀 Leadership in TQM means aligning the organization with a common goal or direction and fostering a sense of shared purpose.
- 😀 Employee Involvement encourages a collaborative environment where every team member contributes to achieving organizational objectives.
- 😀 Continuous Improvement, or Kaizen, encourages a culture of ongoing refinement in processes, aiming for zero defects and errors.
- 😀 The strategic approach in TQM emphasizes quality as a core component of the company's strategic plan to ensure long-term success.
- 😀 Despite its benefits, TQM has limitations, including the high costs and time investment required to implement it, and resistance to change due to uncertainty or fear.
- 😀 Toyota Motor Company exemplifies successful TQM implementation through customer-first strategies, continuous improvement (Kaizen), and total employee participation.
Q & A
What is Total Quality Management (TQM)?
-Total Quality Management (TQM) is a management philosophy focused on improving the quality of products and services by involving all employees in the organization. It aims to meet or exceed customer expectations consistently.
What are the key principles of TQM?
-The eight key principles of TQM are customer focus, leadership, employee involvement, process approach, strategic and systematic approach, continual improvement, factual decision-making, and mutually beneficial supplier relationships.
Why is customer focus important in TQM?
-Customer focus is crucial in TQM because it ensures that an organization continuously meets or exceeds the needs and expectations of its customers, which is key to long-term success.
How does leadership play a role in TQM?
-Leadership in TQM is about establishing a unified purpose and organizational direction. Strong leadership ensures that everyone in the organization shares a common goal and works towards achieving it.
What is meant by employee involvement in TQM?
-Employee involvement in TQM refers to creating a work environment where all employees are encouraged to participate in decision-making and continuous improvement efforts, helping the organization achieve its quality goals.
Why is the process approach important in TQM?
-The process approach in TQM emphasizes understanding and optimizing the processes that produce outcomes. By improving these processes, organizations can ensure consistent quality in their products and services.
What is meant by a strategic and systematic approach in TQM?
-A strategic and systematic approach in TQM means integrating quality as a core component of the organization’s strategic plan, ensuring that quality is consistently prioritized across all operations.
What does continual improvement mean in the context of TQM?
-Continual improvement in TQM refers to the ongoing efforts to enhance processes, products, and services to eliminate defects, errors, and accidents, aiming for zero defects and perfection.
What are the limitations of TQM?
-The limitations of TQM include the high cost and time required for implementation, which involves training employees and integrating quality systems, and resistance to change from employees due to uncertainty and fear of rapid global competition.
Can you provide an example of a company successfully implementing TQM?
-An example of a company that successfully implemented TQM is Toyota. Toyota has focused on customer satisfaction, continual improvement (Kaizen), and employee participation to maintain high quality and long-term success.
Outlines
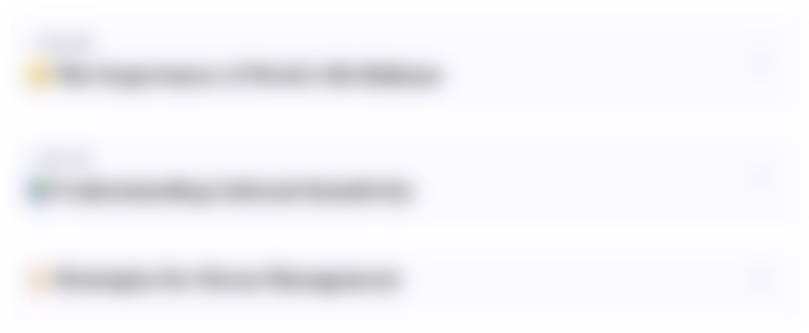
Esta sección está disponible solo para usuarios con suscripción. Por favor, mejora tu plan para acceder a esta parte.
Mejorar ahoraMindmap
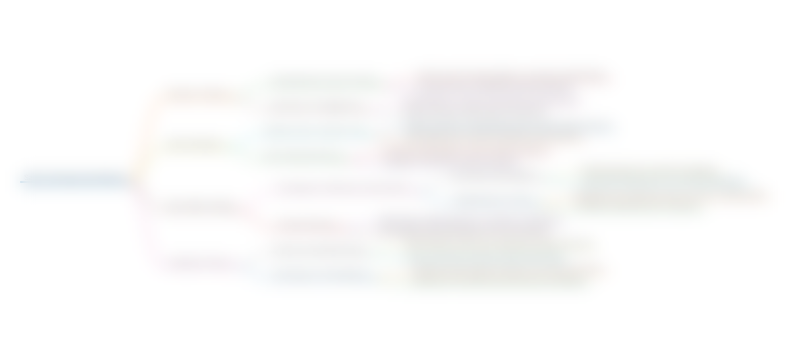
Esta sección está disponible solo para usuarios con suscripción. Por favor, mejora tu plan para acceder a esta parte.
Mejorar ahoraKeywords
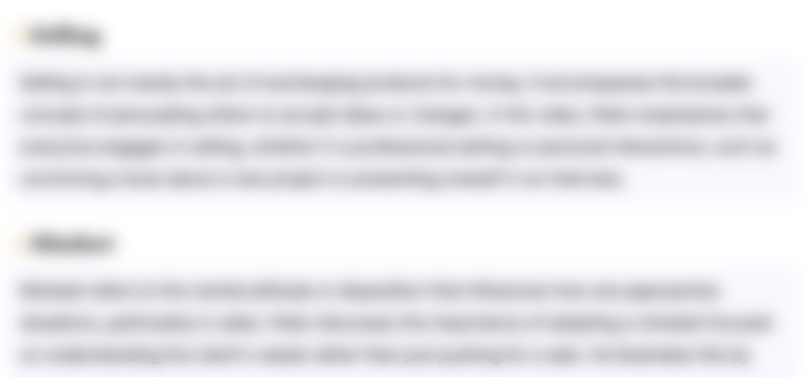
Esta sección está disponible solo para usuarios con suscripción. Por favor, mejora tu plan para acceder a esta parte.
Mejorar ahoraHighlights
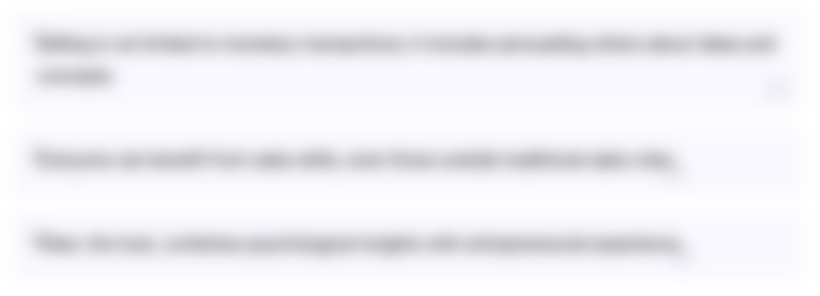
Esta sección está disponible solo para usuarios con suscripción. Por favor, mejora tu plan para acceder a esta parte.
Mejorar ahoraTranscripts
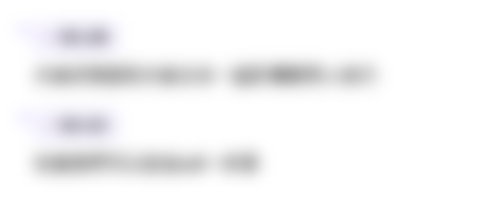
Esta sección está disponible solo para usuarios con suscripción. Por favor, mejora tu plan para acceder a esta parte.
Mejorar ahora5.0 / 5 (0 votes)