Wake Up Call: Refinery Disaster in Philadelphia
Summary
TLDROn June 21, 2019, a catastrophic incident occurred at the Philadelphia Energy Solutions refinery, caused by a corroded pipe elbow that ruptured, releasing toxic hydrofluoric acid (HF) and igniting a massive fire and explosions. The event resulted in significant damage, but fortunately, no major harm to the surrounding community. The CSB investigation identified key safety issues, including mechanical integrity, inadequate safeguards, and outdated equipment standards. The report calls for stronger regulations, safer technologies, and comprehensive inspections to prevent similar disasters in the future.
Takeaways
- 😀 A severely corroded pipe elbow ruptured at the Philadelphia Energy Solutions Refinery on June 21, 2019, leading to a massive fire, explosions, and the release of over 5,000 pounds of toxic hydrofluoric acid (HF).
- 😀 Despite the refinery's location in an urban area, the local community was fortunately not seriously harmed, although the potential for disaster was high.
- 😀 The fire caused an estimated $750 million in property damage, and the explosion resulted in a 38,000-pound vessel fragment being launched offsite.
- 😀 The CSB investigation revealed critical safety issues, including mechanical integrity failures, inadequate safety evaluations, and safeguard reliability in the HF alkylation unit.
- 😀 The pipe elbow that ruptured had corroded faster than other components due to high concentrations of nickel and copper, which are more susceptible to HF corrosion.
- 😀 Refineries did not inspect all piping components vulnerable to HF corrosion, which could have prevented the incident if identified and addressed in time.
- 😀 The API has since revised its standards to require refineries to develop special inspection programs for components at risk of accelerated corrosion due to HF exposure.
- 😀 Changes to industry standards, such as ASTM revisions, were not applied to older components in the PES refinery, highlighting the need for ongoing evaluations of equipment safety.
- 😀 Remotely operated emergency isolation valves, which could have stopped the release of hydrocarbons, were not installed at the refinery, exacerbating the severity of the explosion.
- 😀 The failure of the water spray mitigation system, designed to contain HF releases, was due to control system failures during the fire. Safeguards must be protected from fire and explosion risks to function properly.
- 😀 The CSB recommended replacing HF alkylation units with inherently safer alternatives, such as sulfuric acid or newer catalyst technologies, to reduce the risk of toxic HF releases and improve overall refinery safety.
Q & A
What caused the explosion and fire at the Philadelphia Energy Solutions Refinery?
-The explosion and fire were caused by a ruptured, severely corroded pipe elbow in the refinery's hydrofluoric acid alkylation unit. The rupture released process fluid, which ignited, leading to a massive fire and a series of explosions.
What is hydrofluoric acid (HF), and why is it so dangerous?
-Hydrofluoric acid is a highly toxic chemical used in the alkylation process to produce a gasoline component. It is particularly hazardous because it vaporizes when released into the air, which can cause severe lung damage and burns on contact with skin.
What was the role of the RAD drum during the incident?
-The RAD drum was designed to safely store hydrofluoric acid (HF) in the event of an emergency. In this case, it was used to quickly contain the HF and prevent further release during the fire, although it was only activated after the incident began.
How did the failure of the HF water mitigation system affect the response to the incident?
-The HF water mitigation system, which was designed to spray water to contain a HF release, failed because the control system and backup power were knocked out by the fire. This delayed the activation of the system, allowing more HF to escape before a manual intervention was made 40 minutes later.
What safety issue was related to the corrosion of the pipe elbow?
-The corrosion issue was linked to the high nickel and copper content in the steel of the pipe elbow, which accelerated corrosion when exposed to hydrofluoric acid. This led to the pipe elbow failing after 40 years of service, even though it was no longer appropriate for use in HF service.
Why did the CSB recommend updates to industry standards regarding inspections of piping components?
-The CSB recommended updates to industry standards after discovering that the PES Refinery did not inspect carbon steel piping for accelerated corrosion, despite the high-risk presence of hydrofluoric acid. This lack of inspection contributed to the incident, and the CSB advocated for a new program to detect and address such issues.
What were the mechanical integrity issues at the PES Refinery?
-The mechanical integrity issue was the use of a pipe elbow made of a material prone to rapid corrosion due to its high residual nickel and copper content. This material choice, combined with a lack of inspection for accelerated corrosion, led to the rupture of the elbow.
What was the impact of the explosions at the refinery, and how did it affect the local community?
-The explosions caused significant property damage, estimated at $750 million, and launched large fragments from vessels, but the local community was fortunate not to experience serious harm. Despite the potential for disaster, no major health impacts were reported from the HF release.
What safety measures were recommended by the CSB to prevent future incidents?
-The CSB recommended several measures, including updating API standards for refinery safety, implementing a special emphasis inspection program for carbon steel piping, ensuring the installation of remotely operated emergency isolation valves, and protecting critical safeguards from fire and explosion damage.
How does inherently safer design contribute to reducing risks in refinery operations?
-Inherently safer design focuses on using safer chemicals and technologies to reduce hazards. For example, replacing hydrofluoric acid with less hazardous alternatives, such as sulfuric acid or new catalytic technologies, can significantly lower the risk of catastrophic releases, thus protecting both workers and surrounding communities.
Outlines
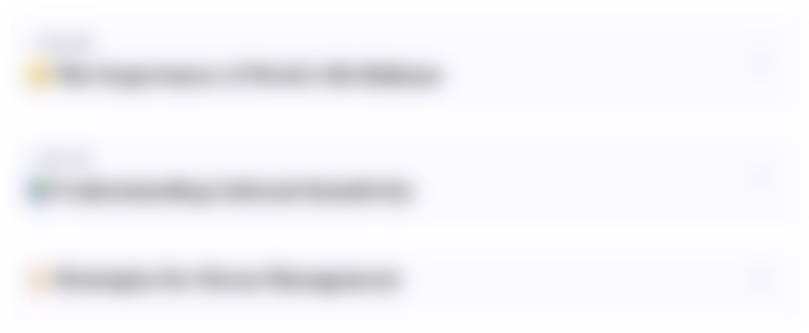
Esta sección está disponible solo para usuarios con suscripción. Por favor, mejora tu plan para acceder a esta parte.
Mejorar ahoraMindmap
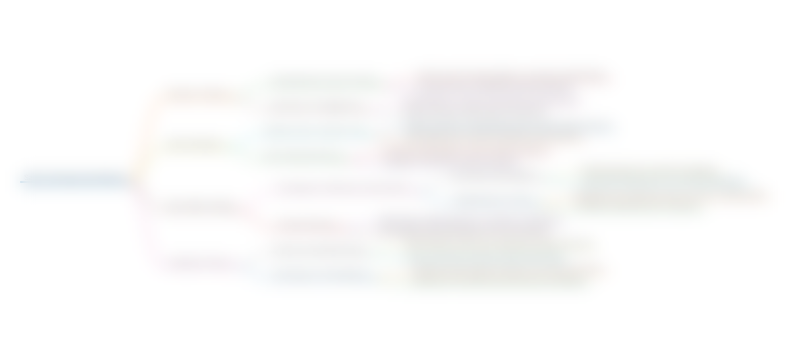
Esta sección está disponible solo para usuarios con suscripción. Por favor, mejora tu plan para acceder a esta parte.
Mejorar ahoraKeywords
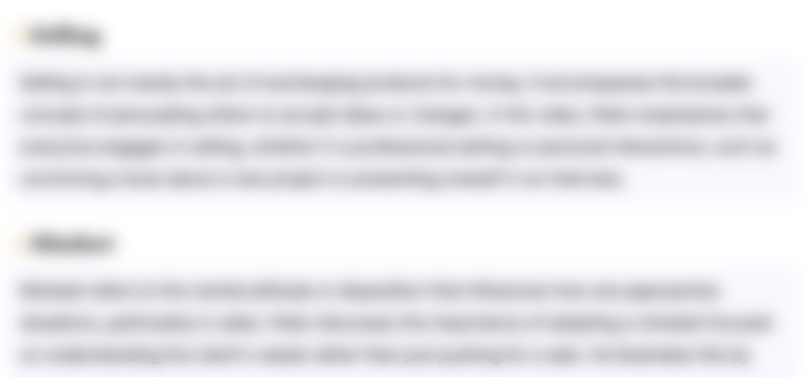
Esta sección está disponible solo para usuarios con suscripción. Por favor, mejora tu plan para acceder a esta parte.
Mejorar ahoraHighlights
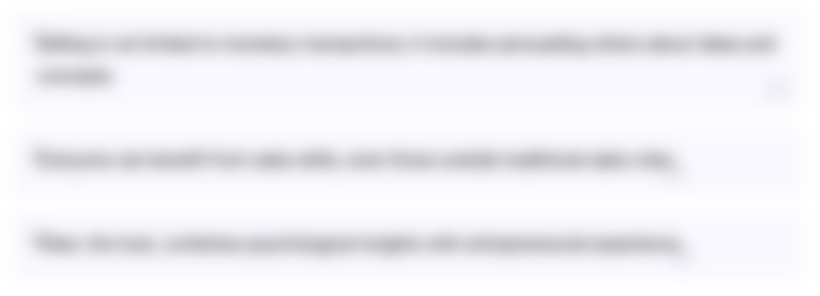
Esta sección está disponible solo para usuarios con suscripción. Por favor, mejora tu plan para acceder a esta parte.
Mejorar ahoraTranscripts
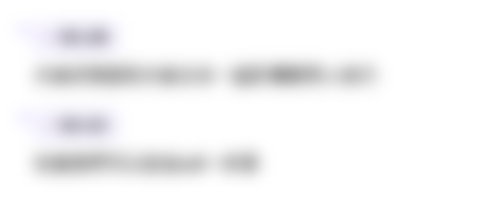
Esta sección está disponible solo para usuarios con suscripción. Por favor, mejora tu plan para acceder a esta parte.
Mejorar ahoraVer Más Videos Relacionados

Chemical Accident at an Ammonia Plant
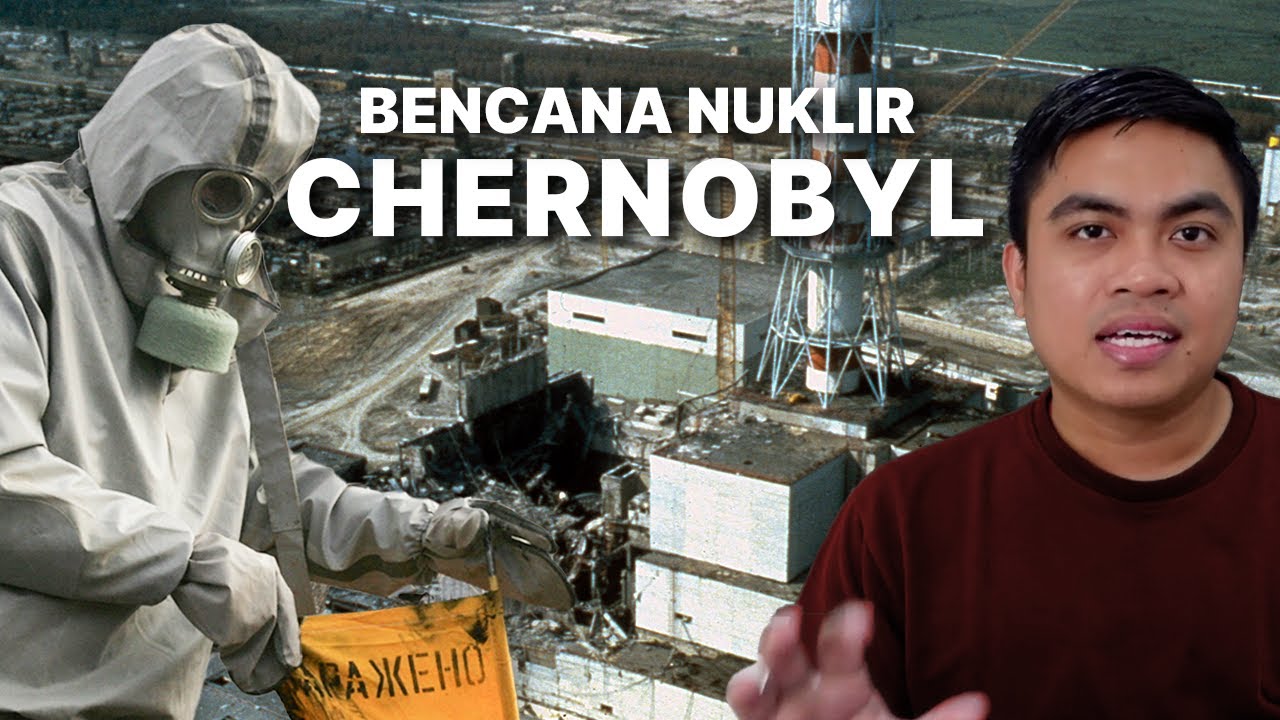
Bagaimana Kecelakaan Nuklir Terbesar di Dunia Terjadi (Chernobyl)

Mixed Connection, Toxic Result
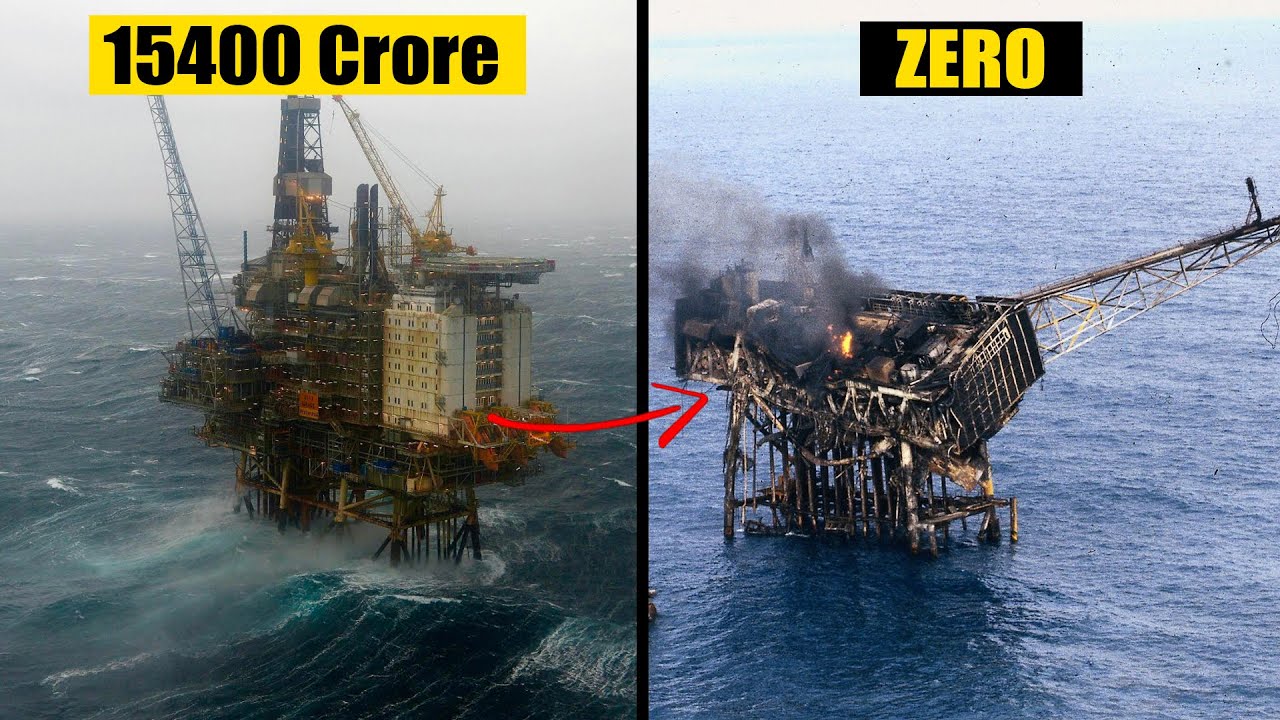
The Secret of Piper Alpha Oil Rig Disaster lies at the Bottom of the Sea
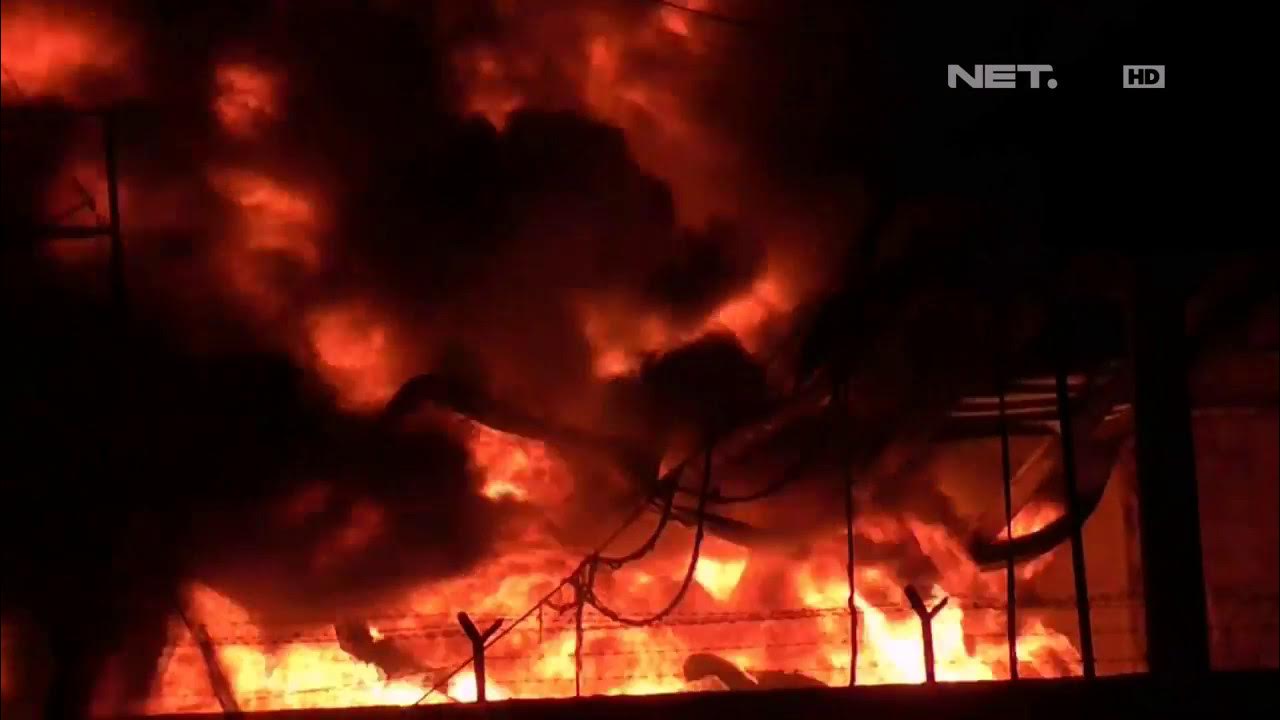
Kebakaran Pabrik Cat Menghanguskan Bangunan Dalam Waktu Singkat - NET5
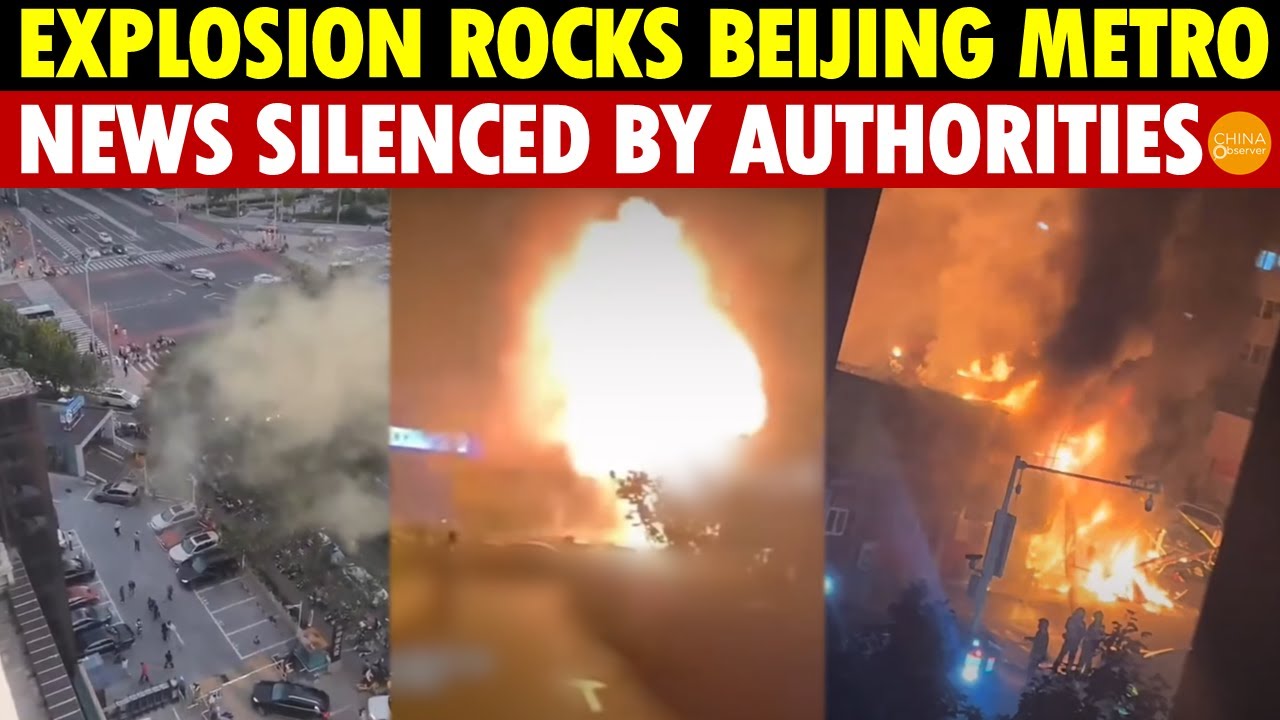
Explosion at Beijing Subway Station Causes Panic; Authorities Suppress the News
5.0 / 5 (0 votes)