SLA 3D Printing - What Is It And How Does It Work?
Summary
TLDRIn this video, Ben Redwood introduces SLA (Stereolithography), the original 3D printing technology, explaining how it works using ultraviolet light to solidify photopolymer resin layer by layer. SLA is ideal for producing intricate, smooth parts, making it perfect for visual models and prototyping. However, its parts are brittle and require post-processing, including support removal and UV curing. While SLA excels in accuracy and detail, it’s not suited for load-bearing parts. Ben also compares SLA to other technologies like DLP and introduces industrial applications, such as the production of hearing aids. Finally, he advises on design considerations like part orientation and hollow sections for optimal results.
Takeaways
- 😀 SLA (Stereolithography) is a 3D printing technology that uses lasers and photopolymer resin to build highly detailed parts layer by layer.
- 😀 SLA is ideal for creating intricate designs and parts that require a smooth surface finish, making it great for visual models and prototyping.
- 😀 SLA prints are highly accurate due to the small laser spot size and low layer height, typically 100 microns but can go as low as 25 microns.
- 😀 Parts produced using SLA are brittle and sensitive to UV light, which can degrade the material over time, making it unsuitable for load-bearing functional parts.
- 😀 Post-processing is required to achieve optimal mechanical properties, including curing the parts under UV light to harden them fully.
- 😀 Support material is always necessary for SLA printing to hold overhangs and prevent curling, but it can leave marks on the part's surface.
- 😀 The part orientation is critical for reducing the amount of support material required and avoiding surface contact with it, ensuring better cosmetic finishes.
- 😀 Hollow sections in SLA parts reduce material use, making them lighter, faster to print, and more cost-effective, but escape holes must be at least 4mm in diameter.
- 😀 SLA printers can be divided into desktop and industrial categories, with desktop printers being more cost-effective for small parts and industrial printers used for high precision or specialized materials.
- 😀 SLA technology is widely used in industries like medical, dental, and jewelry, with applications including custom hearing aids and investment casting resins.
- 😀 Emerging SLA technologies, such as Carbon's resin-based printer, promise up to 100 times faster printing by continuously pulling the part out of resin rather than printing one layer at a time.
Q & A
What is SLA in 3D printing?
-SLA (Stereolithography) is a 3D printing technology that uses UV light to cure photopolymer resin layer by layer to create precise and detailed parts. It is known for its high accuracy and smooth surface finish.
How does SLA 3D printing work?
-SLA works by positioning a build plate inside a tank of photopolymer resin. A UV light source then scans the surface, curing the resin layer by layer. The process repeats, with the platform lowering after each layer is completed to build up the part.
What are the key differences between SLA and DLP printing?
-While both SLA and DLP use light to cure resin, the key difference is the light source. SLA uses a laser and mirrors (galvanometers) to focus on a specific area, whereas DLP uses a digital light projector to flash an image of the entire layer at once. This makes DLP generally faster than SLA, but SLA is often more accurate.
What are the advantages of using SLA for 3D printing?
-SLA is ideal for producing parts with fine details, intricate features, and smooth surface finishes. It's also scalable, able to produce large parts, and offers a wide range of material options for specialized applications.
What are the limitations of SLA printing?
-SLA prints are brittle due to the use of photopolymers, making them unsuitable for functional or load-bearing parts. Additionally, the materials are UV-sensitive and degrade over time, especially with exposure to direct sunlight. SLA also requires support structures and post-processing, which adds to the cost and time.
Why are support structures necessary in SLA printing?
-Support structures are necessary in SLA to anchor the part to the build plate, prevent warping, and support overhangs during the printing process. They must be removed after printing, and their contact points can leave marks on the part surface.
What design considerations should be kept in mind when preparing parts for SLA printing?
-Key design considerations for SLA include optimizing part orientation to minimize support contact on visible surfaces, using hollow sections to reduce material usage, and ensuring escape holes are present to prevent resin from being trapped inside the part.
What is the role of part orientation in SLA printing?
-Part orientation in SLA printing determines how much support material is required and where it will contact the part. Proper orientation can help minimize support marks on cosmetic surfaces and improve the overall surface finish of the part.
What are the benefits of using hollow sections in SLA parts?
-Hollow sections reduce the amount of resin used, making parts lighter, faster, and cheaper to produce. However, designers must ensure there are sufficient escape holes (at least 4mm in diameter) to allow uncured resin to drain out.
What are the two main categories of SLA printers?
-The two main categories of SLA printers are desktop printers, which are suitable for general-purpose prototyping and smaller parts, and industrial printers, which are used for high-precision applications or specialized materials, such as in the medical or dental industries.
What is the significance of post-processing in SLA printing?
-Post-processing is important in SLA printing to fully cure the part under UV light, improving its mechanical properties. Additionally, support structures must be removed, and sometimes additional smoothing or finishing is required to achieve the desired surface quality.
How does SLA compare to other 3D printing technologies like SLS or FDM?
-SLA is best for producing small, detailed parts with smooth surfaces but is not suitable for functional or load-bearing applications due to the brittleness of photopolymers. For stronger and more durable parts, technologies like SLS (Selective Laser Sintering) or FDM (Fused Deposition Modeling) are more appropriate.
Outlines
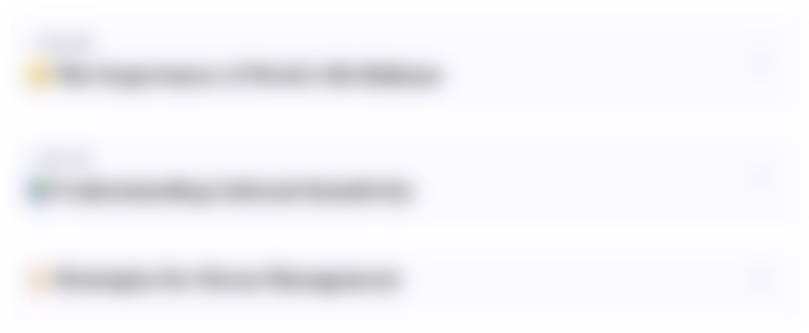
Esta sección está disponible solo para usuarios con suscripción. Por favor, mejora tu plan para acceder a esta parte.
Mejorar ahoraMindmap
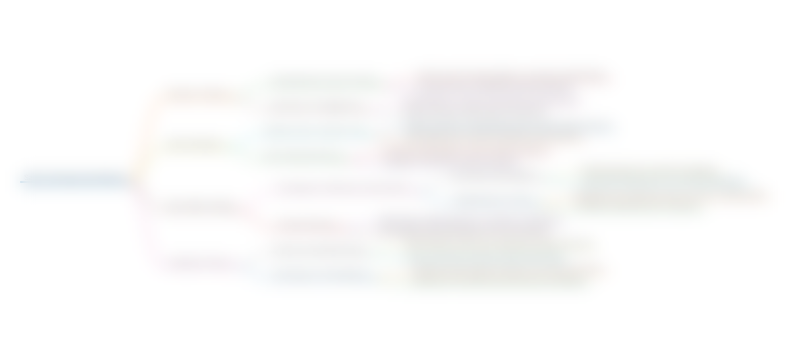
Esta sección está disponible solo para usuarios con suscripción. Por favor, mejora tu plan para acceder a esta parte.
Mejorar ahoraKeywords
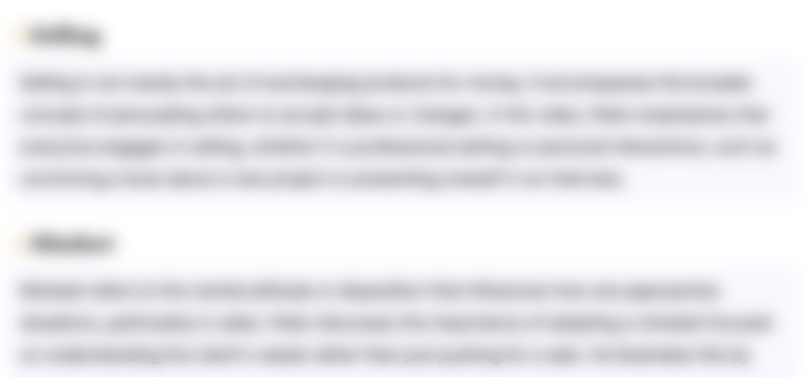
Esta sección está disponible solo para usuarios con suscripción. Por favor, mejora tu plan para acceder a esta parte.
Mejorar ahoraHighlights
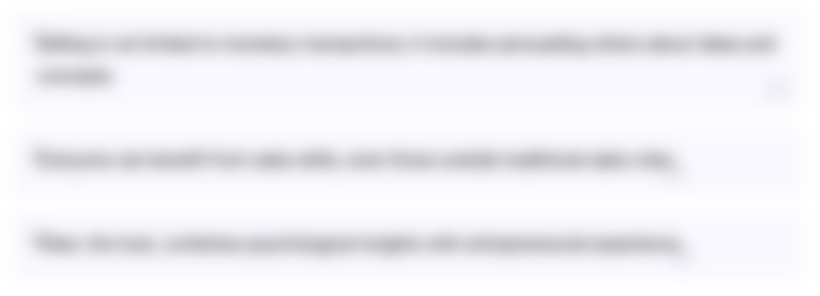
Esta sección está disponible solo para usuarios con suscripción. Por favor, mejora tu plan para acceder a esta parte.
Mejorar ahoraTranscripts
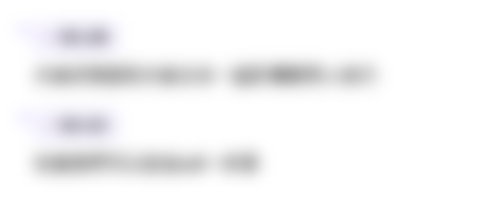
Esta sección está disponible solo para usuarios con suscripción. Por favor, mejora tu plan para acceder a esta parte.
Mejorar ahoraVer Más Videos Relacionados

3D Printers - CompTIA A+ 220-1101 - 3.7

Digital Light Processing DLP 3D Printing Process

What is VAT Photopolymerization (SLA, DLP, CDLP)? | Dassault Systèmes
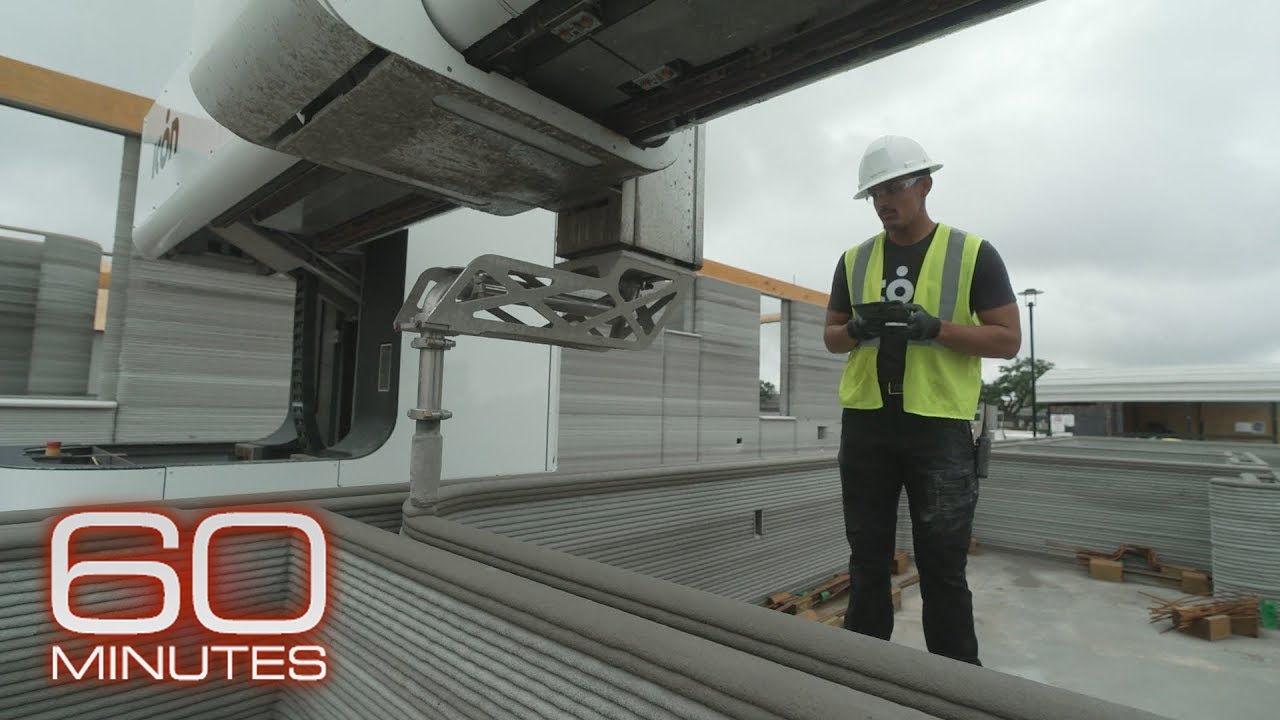
3D printing homes on Earth, someday the moon | 60 Minutes
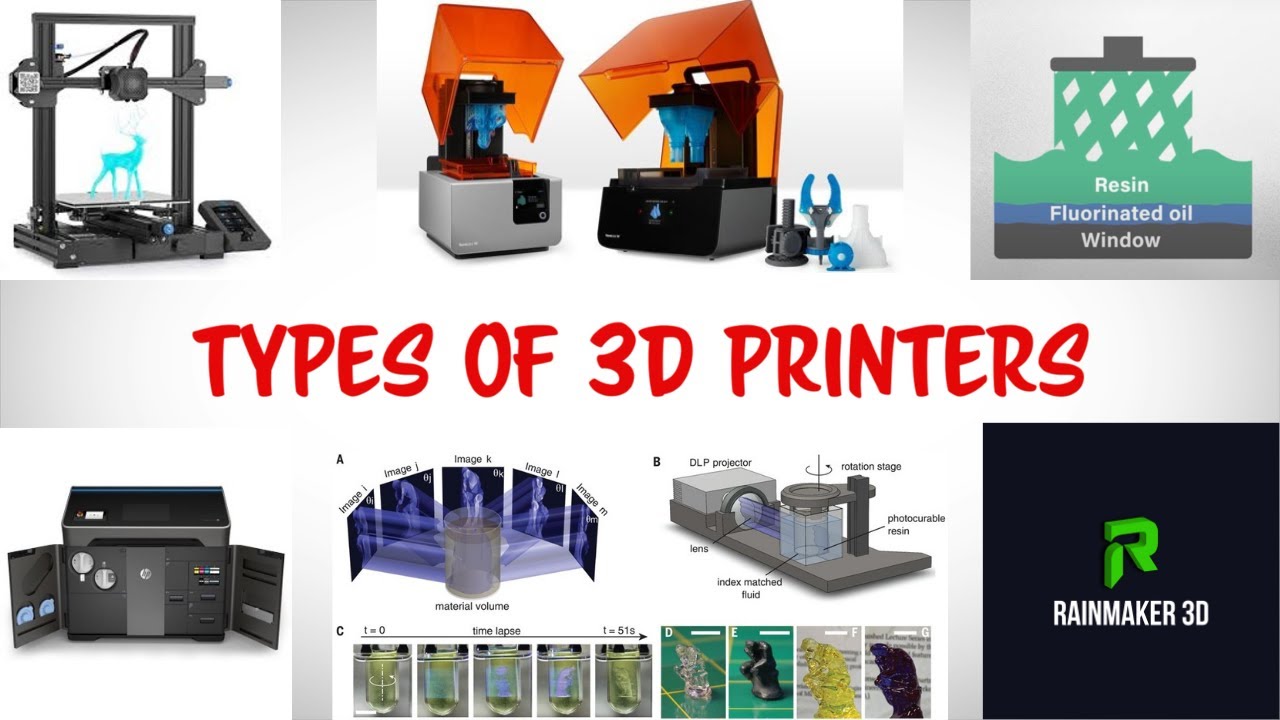
Types of 3D Printers - 11 Different Types of 3D Printers - Introduction to 3D Printing
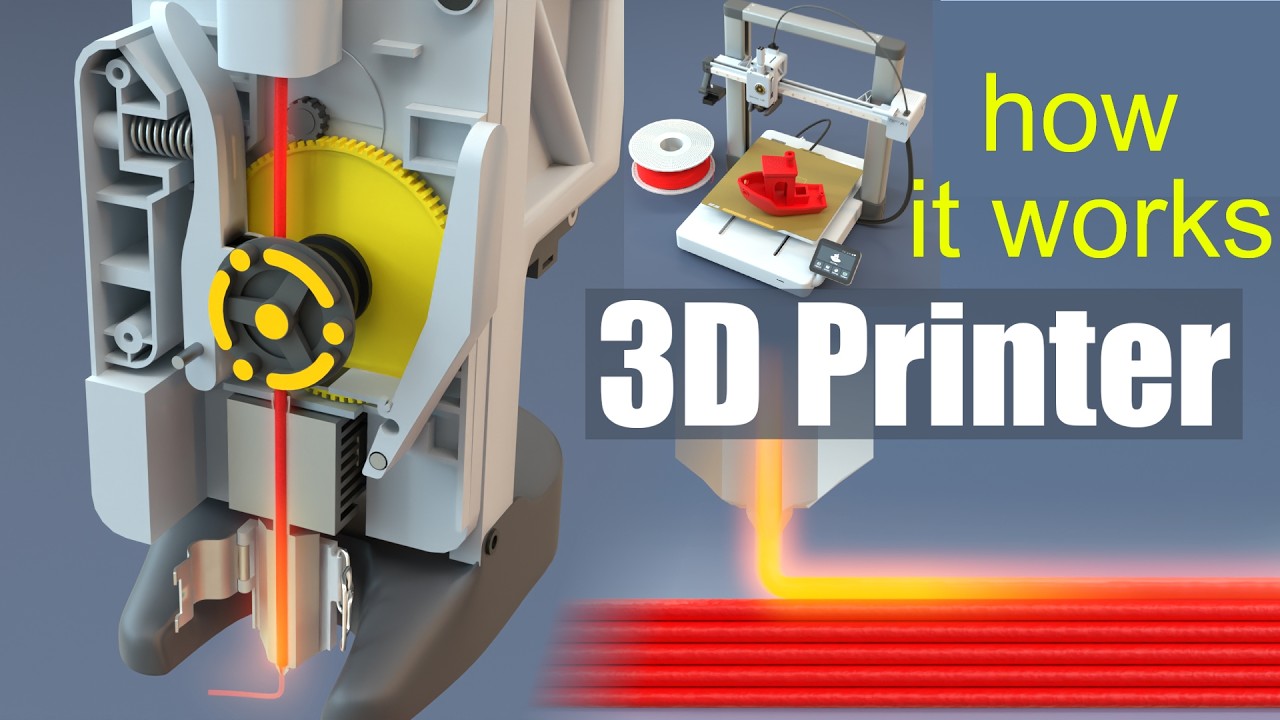
How does a 3D Printer work? (A1 by Bambu Lab)
5.0 / 5 (0 votes)