These factory workers get paid to go to school
Summary
TLDRThe manufacturing industry is evolving, transitioning from low-skilled labor to a demand for skilled workers due to automation. Despite projected job growth, a significant skills gap exists, highlighting the need for expanded apprenticeship programs. Unlike the U.S., where apprenticeships are often undervalued, countries like Germany successfully integrate them across various fields, leading to lower youth unemployment. Companies such as BMW in the Carolinas are adopting tailored apprenticeship models that combine education and practical experience, ultimately enhancing workforce skills. As automation progresses, investing in human capital becomes essential to ensure workers thrive alongside technology.
Takeaways
- 🏭 The manufacturing workforce is experiencing a significant overhaul, moving towards more skilled and diversified job roles.
- 🤖 Automation and offshoring have drastically reduced traditional manufacturing jobs, but new opportunities are emerging.
- 🔧 Apprenticeships are gaining bipartisan support as a solution to bridge the skills gap in the manufacturing sector.
- 📚 Apprenticeships combine classroom learning with on-the-job training, allowing individuals to earn while they learn.
- 🔍 There is a widespread stigma in the U.S. that associates apprenticeships with low-skilled blue-collar work, limiting their appeal.
- 🌍 In contrast, countries like Germany and Australia integrate apprenticeships across various professions, leading to lower youth unemployment rates.
- 📈 Manufacturers in the U.S. face a projected skills gap, with millions of jobs expected to go unfilled due to a lack of qualified candidates.
- 🧠 The modern manufacturing worker is required to possess a diverse skill set, often referred to as a 'Swiss army knife' of abilities.
- 💰 Investment in employee training and development is crucial for companies to enhance productivity and adapt to automation.
- 🎓 The partnership between companies and educational institutions, as seen in apprenticeship programs, can tailor training to meet industry needs.
Q & A
What is the current state of manufacturing jobs in the U.S.?
-Manufacturing jobs are experiencing a major overhaul, with the industry currently adding jobs despite previous declines due to automation and offshoring.
What is the role of apprenticeships in the modern workforce?
-Apprenticeships provide a combination of classroom learning and on-the-job training, allowing individuals to earn while they learn and gain practical skills needed in various industries.
How do apprenticeships in the U.S. differ from those in countries like Germany?
-In the U.S., apprenticeships are often seen as outdated and primarily associated with blue-collar work, while in Germany, they are integrated across various professions and widely accepted as a pathway to success.
What are the projected job openings in the manufacturing industry over the next decade?
-The manufacturing industry is projected to create three and a half million new jobs in the next decade, but two million of these may remain unfilled due to a skills gap.
What skills are in high demand for manufacturing jobs?
-Higher proficiency in math, computers, and technology is increasingly required for manufacturing jobs, reflecting the need for a more skilled workforce.
What is the perceived issue regarding wages in the manufacturing sector?
-Many employers express a desire for workers with advanced skills while offering low wages, leading to a perception of a wage shortage in the industry.
How does public perception affect the recruitment of workers in manufacturing?
-The stigma associated with manufacturing jobs, rooted in historical notions of dirty and low-skilled work, deters many potential workers from considering careers in the industry.
What benefits do apprenticeships provide to companies like BMW?
-Companies benefit from apprenticeships by developing a skilled workforce tailored to their specific needs, while also covering tuition and providing valuable hands-on training.
How do employers in the U.S. view investment in training compared to those in Germany?
-U.S. employers are often hesitant to invest in training without clear returns on investment, whereas German employers view workers as long-term investments that enhance productivity.
What is the future outlook for the role of humans in manufacturing amidst rising automation?
-While automation is becoming more prevalent in manufacturing, there is still a critical need to develop the human workforce to ensure that workers can adapt and thrive in this changing landscape.
Outlines
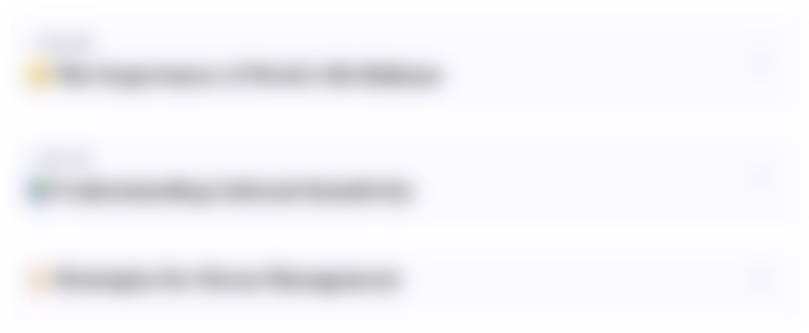
Esta sección está disponible solo para usuarios con suscripción. Por favor, mejora tu plan para acceder a esta parte.
Mejorar ahoraMindmap
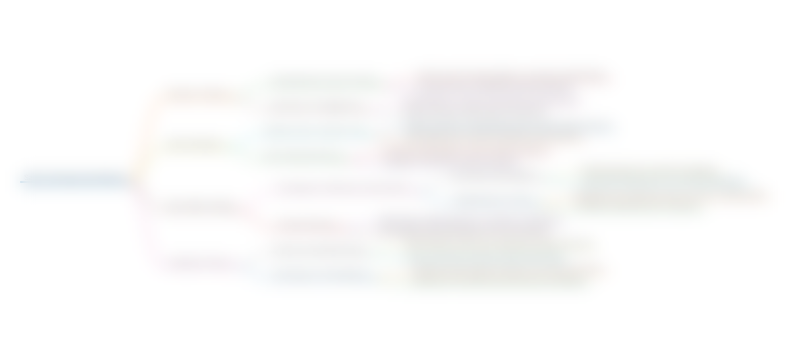
Esta sección está disponible solo para usuarios con suscripción. Por favor, mejora tu plan para acceder a esta parte.
Mejorar ahoraKeywords
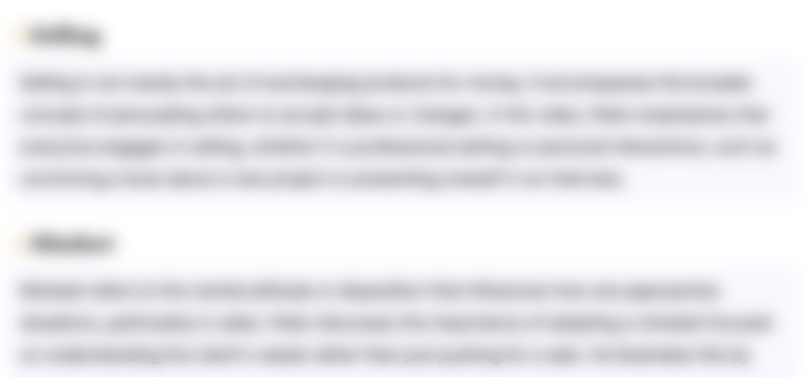
Esta sección está disponible solo para usuarios con suscripción. Por favor, mejora tu plan para acceder a esta parte.
Mejorar ahoraHighlights
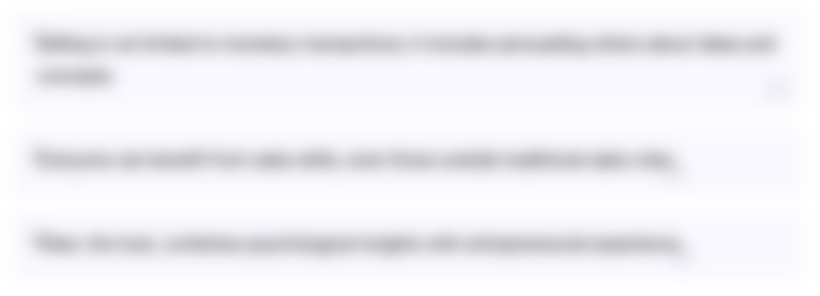
Esta sección está disponible solo para usuarios con suscripción. Por favor, mejora tu plan para acceder a esta parte.
Mejorar ahoraTranscripts
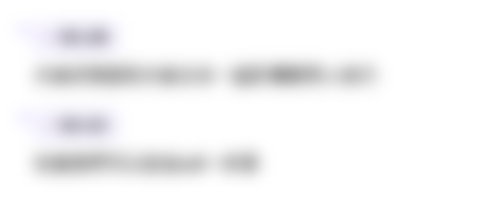
Esta sección está disponible solo para usuarios con suscripción. Por favor, mejora tu plan para acceder a esta parte.
Mejorar ahoraVer Más Videos Relacionados
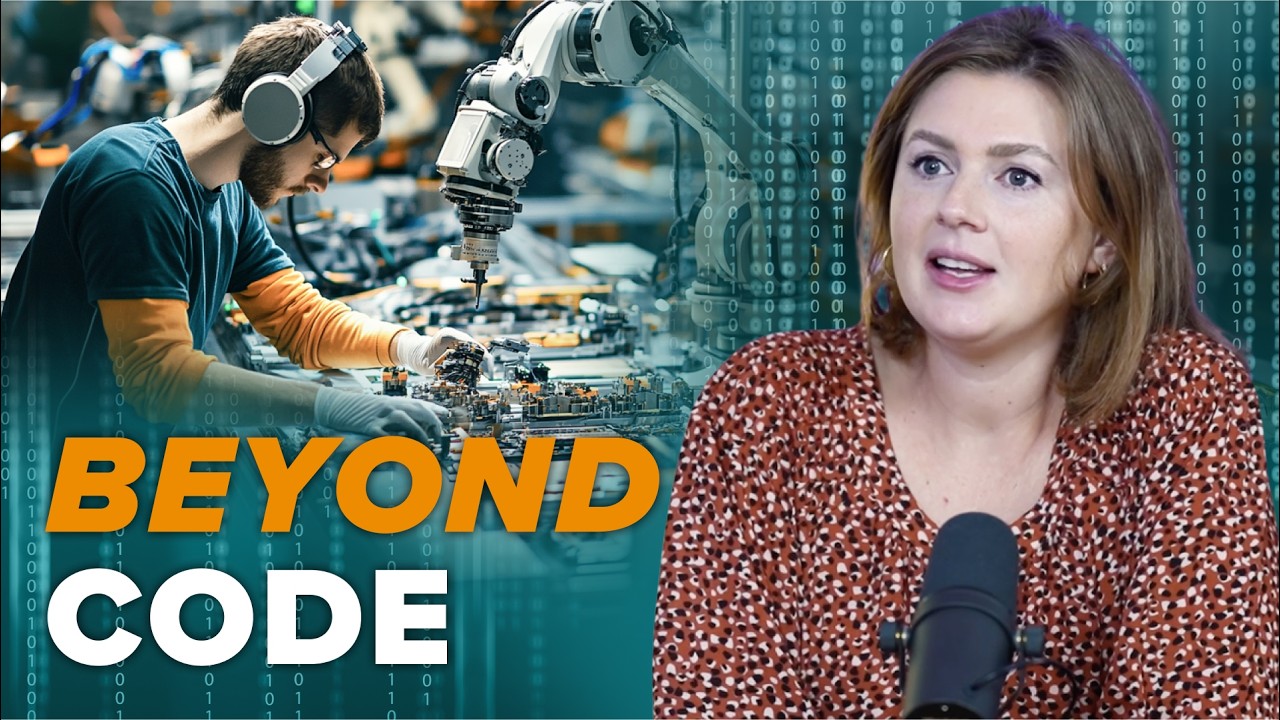
Jobs of the Future: Where Hardware Meets Software

Como a INDÚSTRIA 4.0 vai ROUBAR o seu Emprego? (E como se proteger dela..)

Unidad 4. Modelo de Heckscher-Ohlin. Parte 2 de 3.
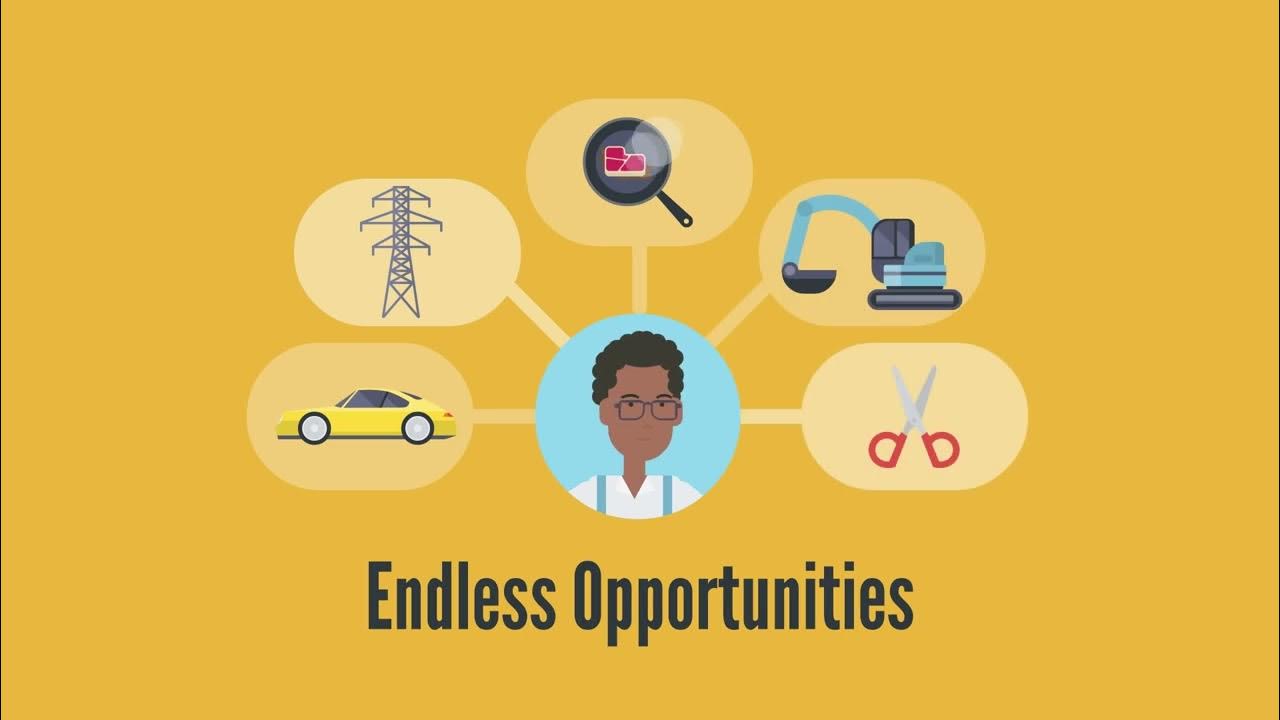
Skilled Trades as a Career v2 3

How T-Shirts Are Made In America | From The Ground Up

Massive UK Visa Salary Hike? You Won’t Believe This!😱
5.0 / 5 (0 votes)