Title: How to Construct a Fishbone Diagram | Fishbone diagram | Invensis Learning
Summary
TLDRThis video provides a comprehensive understanding of the fishbone diagram, also known as the Ishikawa or cause-and-effect diagram. It explains its purpose in identifying root causes of problems across various industries. The video covers types of fishbone diagrams, steps to create one, and advantages like team focus and problem-solving. Additionally, it discusses the 6 M’s used in manufacturing and the 'Five Whys' technique for deeper analysis. Viewers are also introduced to brainstorming tips and fishbone diagram applications in Six Sigma and agile project management.
Takeaways
- 💡 A fishbone diagram, also known as an Ishikawa or cause-and-effect diagram, helps identify potential root causes of problems in various domains.
- 👨🏫 It was developed by Kaoru Ishikawa in 1960 and is widely used in Six Sigma and quality management processes.
- 🎯 The diagram visually displays causes as branches on a 'fishbone' structure, making it easier for teams to identify issues and find solutions.
- 🧠 Brainstorming is crucial when creating a fishbone diagram, and teams should be encouraged to contribute ideas without fear of rejection.
- 📊 There are different types of fishbone diagrams based on industries, such as the 4S diagram (systems, surroundings, skills, suppliers) and the 8P diagram (price, people, processes, etc.).
- 🏭 The 5M and 1E fishbone diagram is widely used in manufacturing, covering categories like machinery, methods, manpower, materials, measurements, and environment.
- 🔍 Steps to create a fishbone diagram include gathering a team, defining the problem statement, categorizing causes, analyzing deeper causes, and finding solutions.
- ✅ Advantages of the fishbone diagram include visualizing the root cause of issues, improving team focus, and facilitating problem-solving.
- ⚠️ Disadvantages include potential confusion during brainstorming and the difficulty of resolving all root causes if resources are limited.
- 🔧 The '5 Whys' technique can complement the fishbone diagram by asking 'why' multiple times to uncover the deeper root cause of a problem.
Q & A
What is a fishbone diagram and why is it also known as the Ishikawa diagram?
-A fishbone diagram, also known as the Ishikawa diagram, is a visual tool designed to identify the potential causes of an issue and brainstorm solutions. It is named after Kaoru Ishikawa, a quality management innovator, who developed it in 1960.
What are the main purposes of using a fishbone diagram in business problem-solving?
-The main purposes of using a fishbone diagram are to visually represent the causes of an issue, analyze and improve quality problems, and help teams identify the root cause of a problem to develop a solution.
What are the key steps involved in constructing a fishbone diagram?
-The key steps are: gathering the team, defining the problem statement, creating categories, brainstorming potential causes, analyzing the causes, and finally fixing the issue by identifying and removing the root cause.
What are the 6 M's in a fishbone diagram, particularly in the manufacturing domain?
-The 6 M's in a fishbone diagram for manufacturing are Manpower, Machinery, Materials, Methods, Mother Nature (environmental factors), and Measurement. These categories help analyze the different aspects contributing to an issue.
What are the advantages of using a fishbone diagram in problem-solving?
-The advantages include its simple and effective visualization, helping teams stay focused on the problem, enabling brainstorming, identifying issues easily, and enhancing team understanding and collaboration.
What are the disadvantages of using a fishbone diagram?
-Disadvantages include the potential for too many irrelevant ideas during brainstorming, a divergent approach that can overwhelm teams, and the complexity of diagrams with multiple contributing factors, which can become difficult to manage.
When should a fishbone diagram be used?
-A fishbone diagram should be used when analyzing complex issues with multiple causes, seeking different perspectives on a problem, uncovering root causes, and improving processes where traditional methods are time-consuming.
How does the 'Five Whys' technique complement a fishbone diagram?
-The 'Five Whys' technique helps identify the deeper root cause of a problem by asking 'why' five times in succession. It complements the fishbone diagram by helping teams dig deeper into the causes that are visually mapped out.
What are some tips for conducting a successful brainstorming session for a fishbone diagram?
-Tips include providing multiple options for idea contributions, giving participants time to prepare, avoiding rejecting ideas, and inviting the right people, even from outside the team, to encourage diverse perspectives.
What are the different types of fishbone diagrams?
-Types of fishbone diagrams include the Simple Fishbone Diagram, 4S Fishbone Diagram (Systems, Surroundings, Skills, Suppliers), 8P Fishbone Diagram (Price, People, Processes, etc.), and the 5M or 1E Fishbone Diagram, used for manufacturing.
Outlines
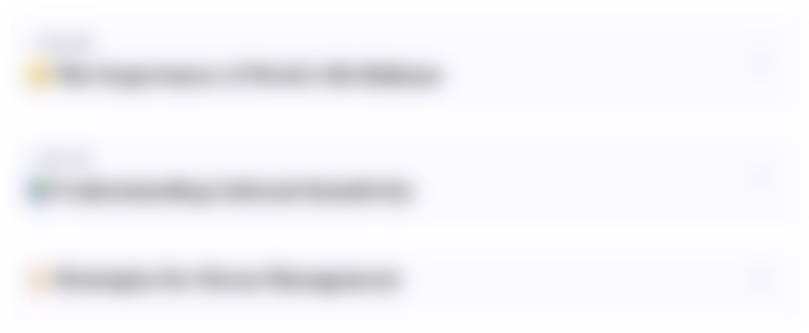
Esta sección está disponible solo para usuarios con suscripción. Por favor, mejora tu plan para acceder a esta parte.
Mejorar ahoraMindmap
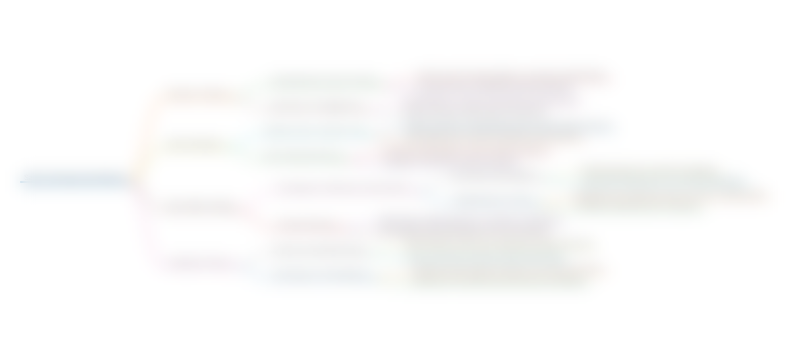
Esta sección está disponible solo para usuarios con suscripción. Por favor, mejora tu plan para acceder a esta parte.
Mejorar ahoraKeywords
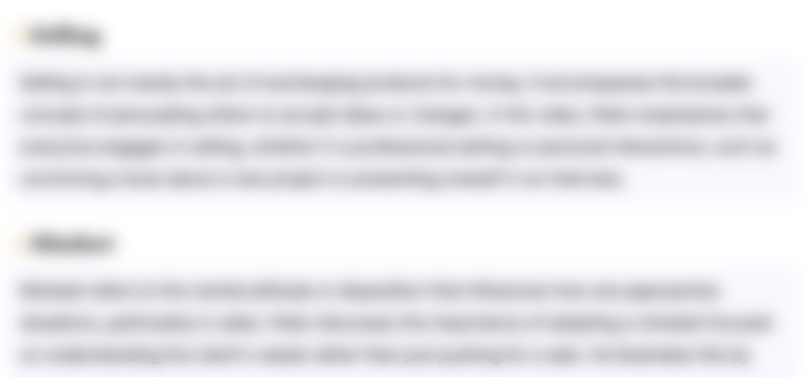
Esta sección está disponible solo para usuarios con suscripción. Por favor, mejora tu plan para acceder a esta parte.
Mejorar ahoraHighlights
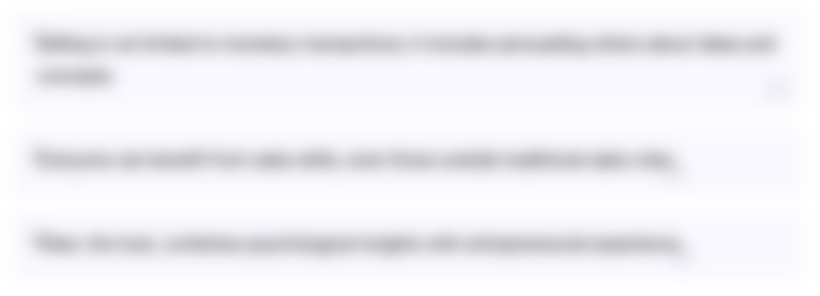
Esta sección está disponible solo para usuarios con suscripción. Por favor, mejora tu plan para acceder a esta parte.
Mejorar ahoraTranscripts
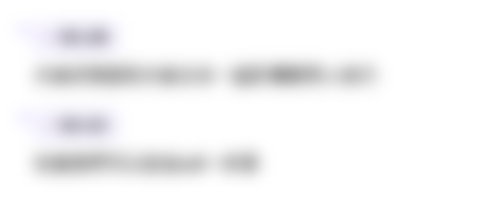
Esta sección está disponible solo para usuarios con suscripción. Por favor, mejora tu plan para acceder a esta parte.
Mejorar ahoraVer Más Videos Relacionados
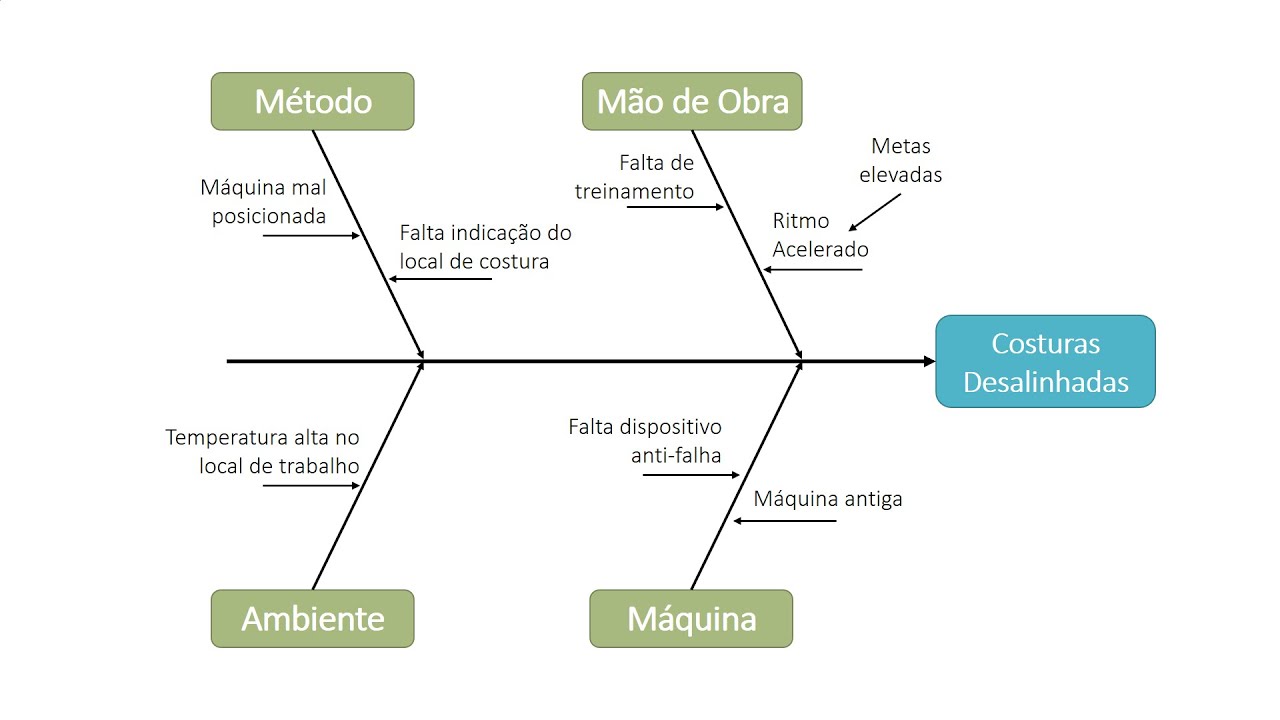
Diagrama de Ishikawa (Ferramenta da Qualidade): Teoria + Exemplo Prático
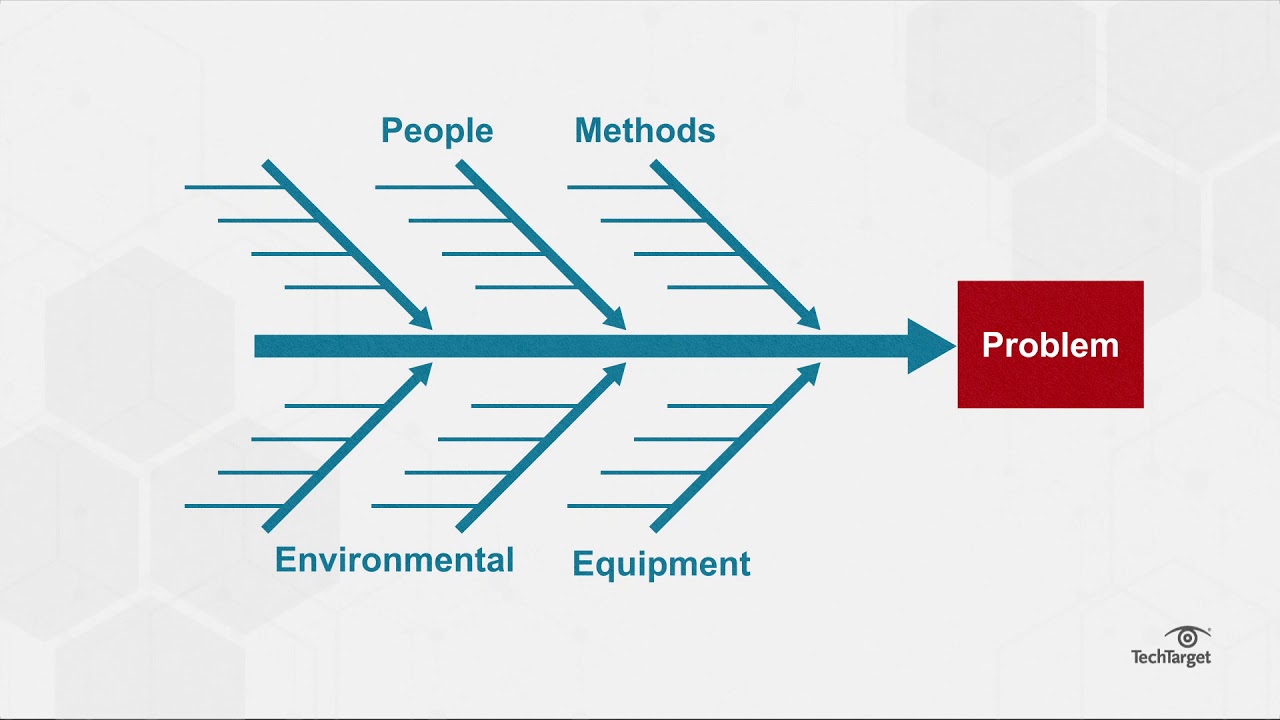
What is a Fishbone Diagram (Ishikawa Diagram)?
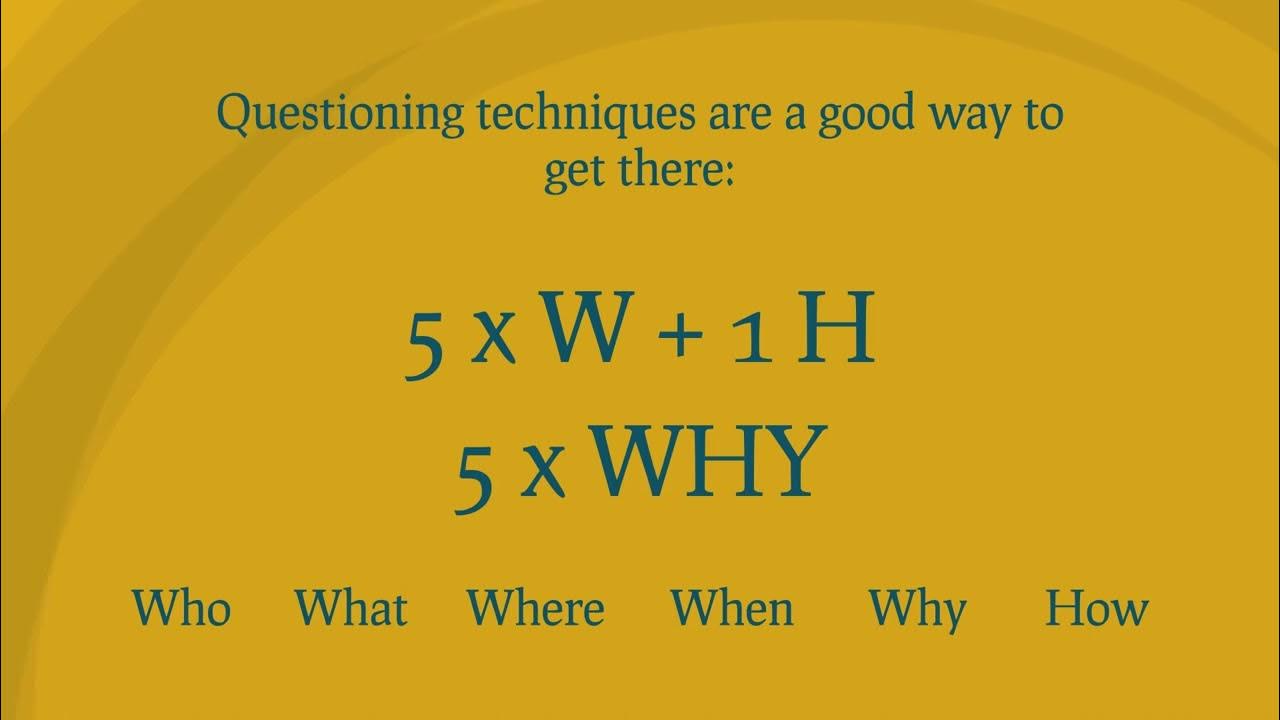
What is 5 x W + 1H?

O Diagrama de Ishikawa
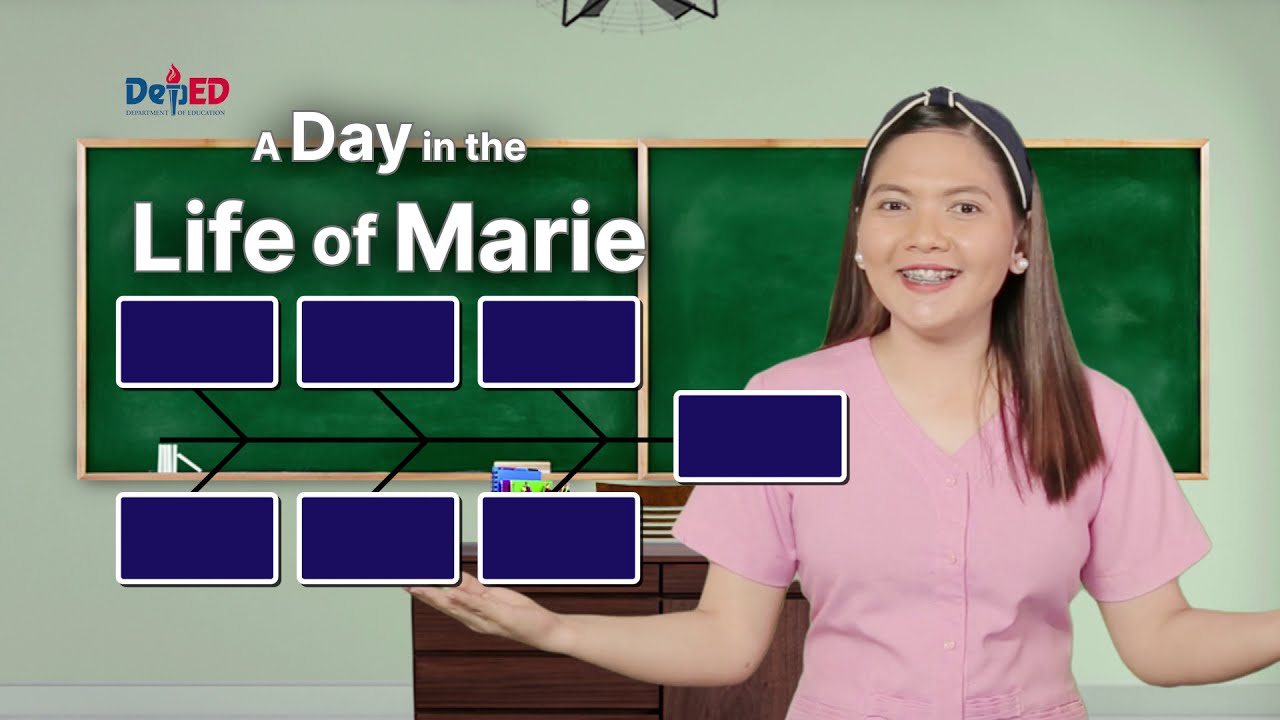
Grade 10 English Q1 Ep3: Textual Aids in Understanding Text
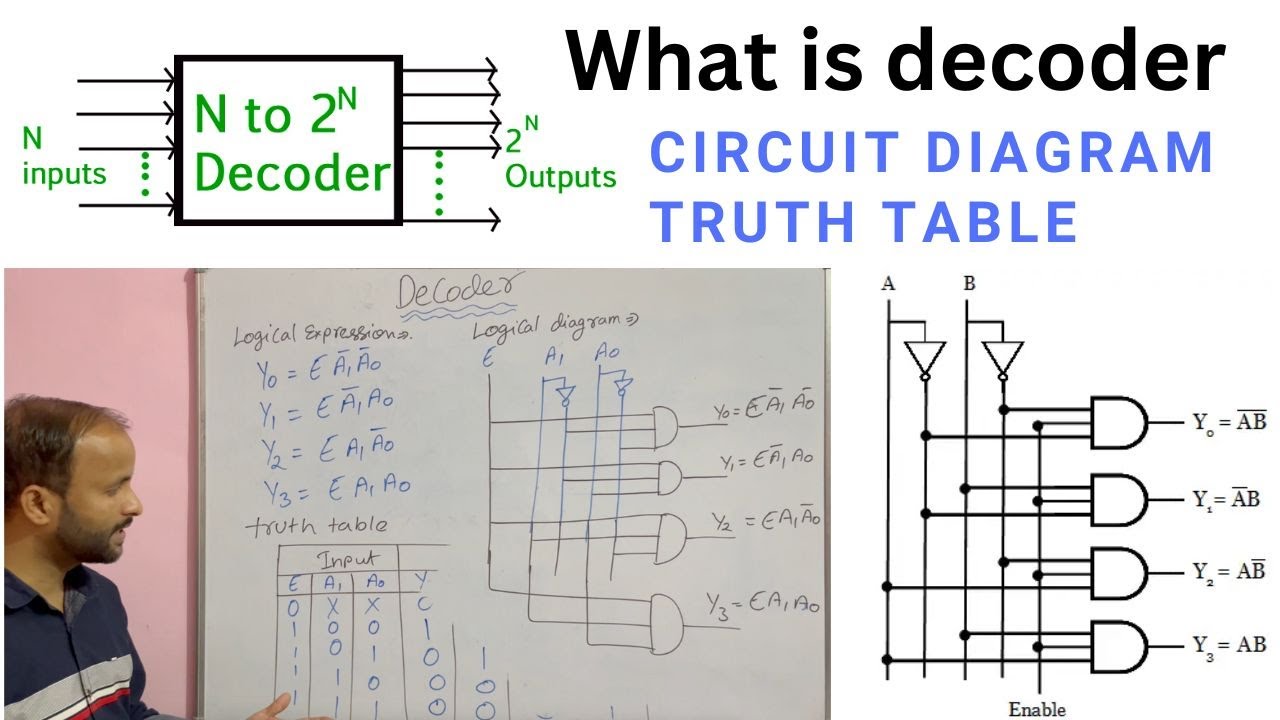
Explain Decoder with Truth Table | Circuit Diagram | Logical Expression in Digital electronics
5.0 / 5 (0 votes)