Beading, Rolling, and Welding Boiler Tubes - The Boiling Point
Summary
TLDRIn this video, Steve Taylor, director of the rental division, and Jimmy Kurtzinger demonstrate the intricate process of tube rolling, welding, and beating in boiler maintenance. They explain that rolling is essential for sealing tubes to the tube sheet, while beading helps dissipate heat and prevent cracks. The video showcases the technical steps, including using different types of rolls and the importance of not over-rolling to avoid thinning the tubes. The demonstration highlights the skill and strength required for beating, ensuring a smooth and secure seal.
Takeaways
- 🔨 Labor Day is a time to celebrate the hard work of those in trades, like tube welding and boiler maintenance.
- 🛠 Rolling a tube is essential for sealing it against the tube sheet, not the weld itself.
- 🌡 Beading is a technique used to prevent overheating and cracking of the tube ends, especially in high-temperature areas.
- 🔥 The hot pass, or the first pass of welding in a boiler, is crucial for heat management and preventing leaks.
- ⚒ Welding on the hot pass helps create a better seal and is often recommended by manufacturers.
- 🛡 Over-rolling a tube can thin it out, making it difficult to re-roll and repair if it leaks.
- 🔩 Proper tube rolling is vital as new boilers can sometimes leak until they are heated and fired for the first time.
- 🛠️ The rolling process involves using a tapered pin and rolls to press the tube against the tube sheet.
- 🛠️ After welding, a tube is re-rolled to ensure a tight seal, using a different type of roll known as a Collins roll.
- 🔧 Beading involves flaring the tube end and then beating it to create a smooth, sealed surface.
- 👨🏫 The process of beating requires skill and strength, and it's important for the final appearance and integrity of the tube end.
Q & A
What is the main purpose of rolling a tube in boiler work?
-The main purpose of rolling a tube in boiler work is to seal the tube to the tube sheet by pressing the tube out against the tube sheet. This process ensures a tight seal and prevents leaks.
Why is it important to bead the end of a boiler tube?
-Beating the end of a boiler tube is important to transfer heat away from the tube end and towards the tube sheet. This helps prevent overheating and cracking, which could lead to leaks.
What is the role of welding in the tube sealing process?
-Welding plays a role in the tube sealing process by providing a better seal from the end of the tube to the tube sheet, especially in the hot pass where temperatures can reach 1800-1900 degrees.
What is the potential issue with rolling a tube too much?
-Rolling a tube too much can thin out the tube material, making it difficult or impossible to re-roll if a leak occurs later. This could result in the need to cut out and replace the tube.
Why might a new boiler have leaking tubes when it first arrives on site?
-A new boiler might have leaking tubes due to the tubes loosening up during transit. Once the boiler is heated and fired for the first time, the tubes expand, and any leaks can be tightened up.
What is the difference between a straight roll and a beading process in tube work?
-A straight roll is used to seal the tube to the tube sheet without flaring, while the beading process uses a special roll to flare the end of the tube and then beat it to create a smooth, sealed surface.
How does the use of a collins roll differ from other types of rolls in tube work?
-A collins roll is used for a straight roll without flaring the tube end. It's typically used after welding to tighten the tube against the tube sheet.
What is the significance of the tube's curvature when beating the end of a boiler tube?
-The curvature of the tube when beating is significant because it determines the final shape and seal quality. A properly formed curvature ensures a smooth, tight seal against the tube sheet.
Why is it necessary to clean the inside of the tube before re-rolling after welding?
-Cleaning the inside of the tube before re-rolling after welding is necessary to prevent any weld splatter from getting caught in the rolls, which could compromise the seal and cause leaks.
What is the importance of speed when beating the end of a boiler tube?
-The speed when beating the end of a boiler tube is important for achieving a smooth surface. If done too slowly, it can result in an uneven and jagged appearance, which is not only unsightly but could also affect the seal quality.
Outlines
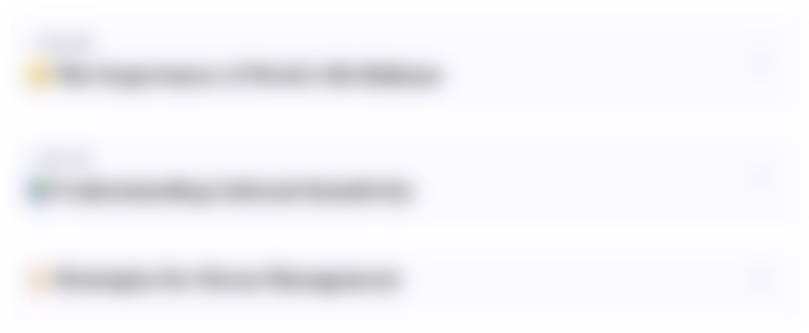
Esta sección está disponible solo para usuarios con suscripción. Por favor, mejora tu plan para acceder a esta parte.
Mejorar ahoraMindmap
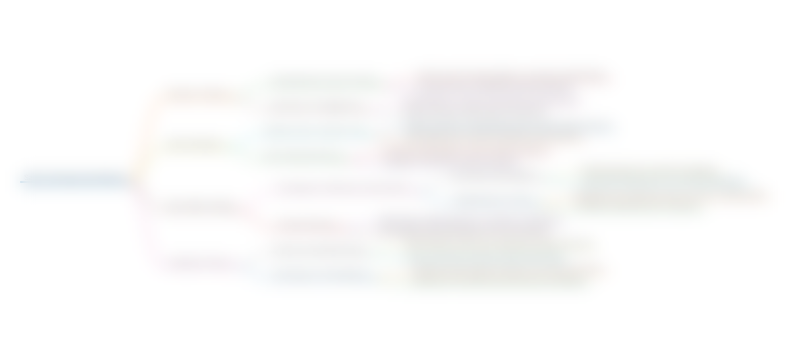
Esta sección está disponible solo para usuarios con suscripción. Por favor, mejora tu plan para acceder a esta parte.
Mejorar ahoraKeywords
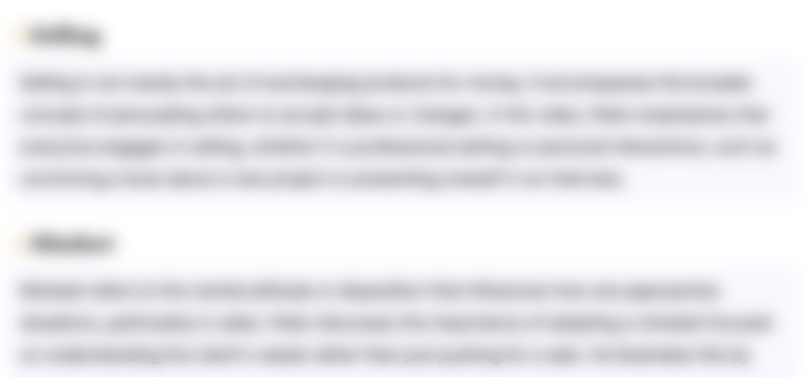
Esta sección está disponible solo para usuarios con suscripción. Por favor, mejora tu plan para acceder a esta parte.
Mejorar ahoraHighlights
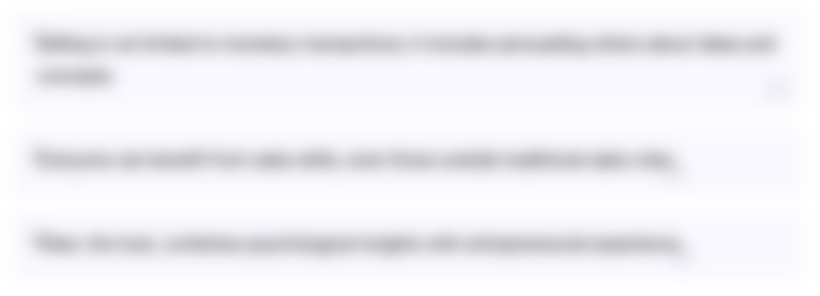
Esta sección está disponible solo para usuarios con suscripción. Por favor, mejora tu plan para acceder a esta parte.
Mejorar ahoraTranscripts
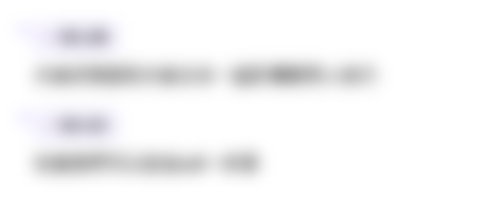
Esta sección está disponible solo para usuarios con suscripción. Por favor, mejora tu plan para acceder a esta parte.
Mejorar ahora5.0 / 5 (0 votes)