LEKCJE ROBOTYKI, ODC. 1: WPROWADZENIE DO ROBOTÓW PRZEMYSŁOWYCH (2016)
Summary
TLDRThis video introduces FANUC Polska's expertise in industrial robots, focusing on how they enhance production processes. Mateusz Amroziński explains the core components of an industrial robot, including the mechanical unit, controller, and iPendant for programming. The video highlights FANUC’s global leadership, with over 400,000 robots installed worldwide, and explores their adaptability in various industries. With features like lifting capacity, speed, and additional sensors for vision and force control, FANUC robots provide flexible and efficient solutions to meet evolving production needs, improving both business outcomes and the economy.
Takeaways
- 🤖 FANUC is a global leader in industrial robots, automation, and robo-machines, headquartered in Japan.
- 📈 Over 400,000 FANUC robots are installed worldwide, setting a global record.
- 🎓 The video aims to raise awareness about industrial robots, their construction, applications, and benefits for Polish enterprises.
- ⚙️ Industrial robots consist of three main components: a mechanical unit, a controller, and a programming panel (iPendant).
- 💡 FANUC robots are highly flexible, allowing for tool changes that enable them to perform multiple tasks with different tools.
- 📊 Key robot parameters include lifting capacity, range, repeatability, and speed, which are selected based on specific application needs.
- 🌐 FANUC robots can be adapted for various conditions, including industries like food and automotive, with protection against dust, water, and chemicals.
- 👁️ FANUC's iRVision system adds visual capabilities, allowing robots to inspect parts and ensure quality control.
- 🔧 FANUC provides a range of robots with 3 to 6 axes, tailored for different industrial tasks from simple transfers to complex operations.
- 🛡️ The DCS system monitors robot speed and position, enhancing safety and reducing space requirements for robotic installations.
Q & A
What does FANUC Polska specialize in?
-FANUC Polska specializes in industrial robots, robo-machines, and numerical controls. They also offer support to ensure the appropriate use of these technologies.
How many FANUC industrial robots have been installed globally?
-Over 400,000 FANUC industrial robots have been installed globally, setting a world record.
What is the main goal of the video series introduced by Mateusz Amroziński?
-The main goal of the video series is to raise awareness about industrial robots, explaining their construction, applications, and benefits for industries.
What are the key components of an industrial robot?
-The key components of an industrial robot include the mechanical unit (robot), a controller, and a programming panel called a teach pendant or iPendant.
How does FANUC ensure the flexibility of their robots?
-FANUC robots are flexible due to their ability to manually or automatically change tools, allowing them to perform various tasks by selecting the appropriate tool and program for different operations.
What are the main factors that define an industrial robot's performance?
-The main factors defining an industrial robot’s performance are its lifting capacity, range, repeatability, speed, efficiency, and adaptability to working conditions.
What differentiates FANUC robots from others in terms of production and reliability?
-FANUC produces all its robot components 100% in-house in Japan, ensuring reliability and high quality. Their robots are also used to manufacture subsequent robots.
What is the role of the iPendant in controlling FANUC robots?
-The iPendant is a panel used for controlling and programming FANUC robots. It includes a touch screen, keyboard, and safety features like the emergency stop button and deadman switches.
What is the purpose of FANUC’s iRVision system?
-FANUC’s iRVision system equips robots with vision capabilities, allowing them to locate objects, inspect details, and eliminate the need for complex mechanical positioning systems.
How does the FANUC DCS system enhance robot safety?
-The FANUC DCS system allows users to monitor and control the robot’s position and speed, ensuring it operates within predefined zones and preventing collisions with nearby equipment or people.
Outlines
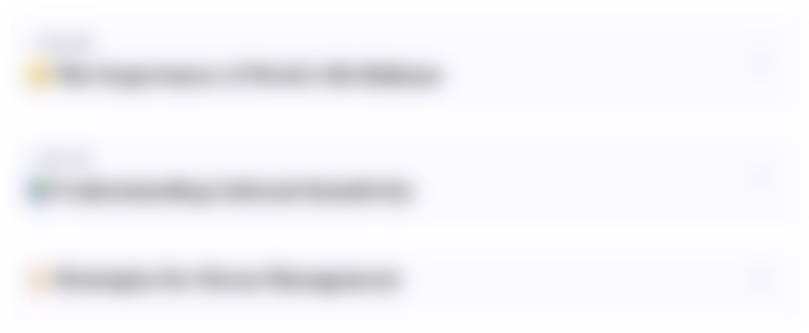
Esta sección está disponible solo para usuarios con suscripción. Por favor, mejora tu plan para acceder a esta parte.
Mejorar ahoraMindmap
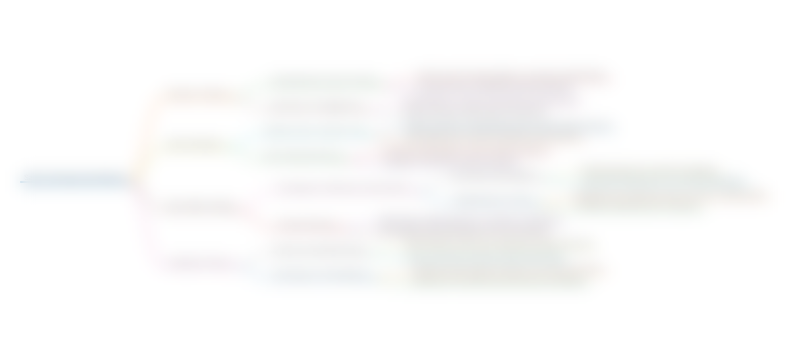
Esta sección está disponible solo para usuarios con suscripción. Por favor, mejora tu plan para acceder a esta parte.
Mejorar ahoraKeywords
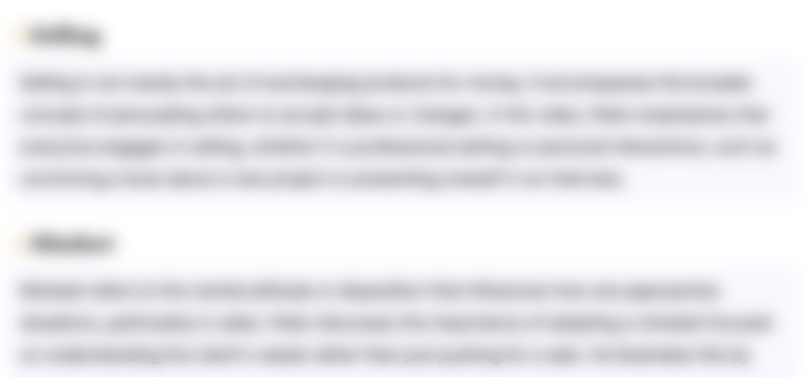
Esta sección está disponible solo para usuarios con suscripción. Por favor, mejora tu plan para acceder a esta parte.
Mejorar ahoraHighlights
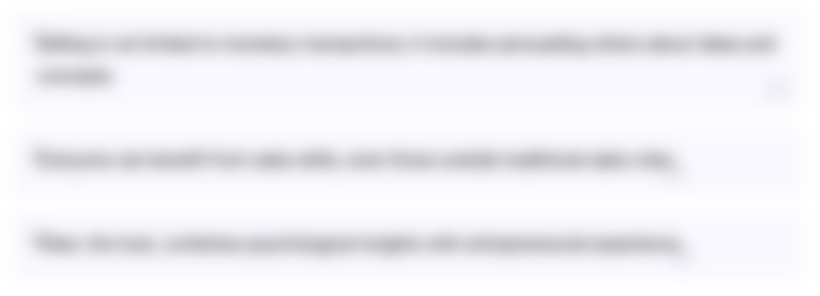
Esta sección está disponible solo para usuarios con suscripción. Por favor, mejora tu plan para acceder a esta parte.
Mejorar ahoraTranscripts
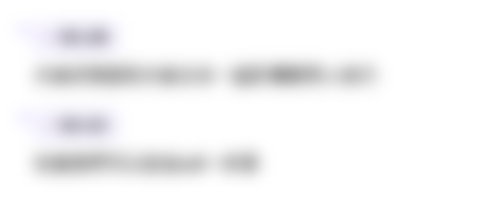
Esta sección está disponible solo para usuarios con suscripción. Por favor, mejora tu plan para acceder a esta parte.
Mejorar ahora5.0 / 5 (0 votes)