The Barcode Warehouse, TagworX and Zebra Avant case study
Summary
TLDRThe script discusses the successful implementation of new technology in a warehouse to improve efficiency and reduce bottlenecks. After initial challenges with incorrect parts selection, the introduction of the TC21 device and TagWorks software streamlined the picking process, enhancing staff confidence and reducing errors. This technology not only satisfied immediate needs but also facilitated easier onboarding for new team members and provided evidence for customer claims. The company is now considering expanding the use of these tools across more business areas.
Takeaways
- 😀 The implementation of new technology in the warehouse significantly improved efficiency and sped up processes.
- 🔍 The company faced bottlenecks and inefficiencies in their warehouse operations, which led to the search for technological solutions.
- 📈 The system was quickly implemented, taking only a few weeks to be fully operational in the warehouses.
- 🤝 Barcode Warehouse was contacted for tools that could suit the company's business needs and improve their operations.
- 🔧 Staff were previously picking up the wrong parts due to similar appearances, causing customer dissatisfaction and financial losses.
- 📱 The TC21 device was chosen for its reliability and ease of use, which helped to address the issue of incorrect part selection.
- 📝 TagWorks was introduced as a platform that evolved based on customer feedback and specific requirements for the picking process.
- 🛠️ The company described their processes to TagWorks to ensure a tailored solution that would fit their needs.
- 🛡️ The new technology provided confidence to team members, reducing the time to train new staff and preventing potential mistakes.
- 📈 The implementation of the tool resulted in a faster turnaround on orders and less anxiety for staff about packing the correct products.
- 📊 The tool also provided evidence for any client claims, ensuring that the right products were sent to the right customers.
- 🌐 The success of the tool has led to plans for expanding its use in other areas of the business and looking for specific devices for further integration.
Q & A
What was the primary motivation behind implementing new technology in the warehouse?
-The primary motivation was to improve the efficiency of the team and to address the bottleneck issues in the business caused by the warehouse.
How long did it take for the new system to be fully operational in the warehouses?
-It took only a few weeks for the system to be up and running.
What was the initial problem that Tim faced when he first reached out to Barcode Warehouse?
-The initial problem was that the products looked very similar, causing staff to pick up the wrong parts, especially in large orders with thousands of items.
What was the solution provided by Barcode Warehouse to address the issue of picking the wrong parts?
-Barcode Warehouse sent over different devices for testing, and the TC21 device was chosen for its reliability and ease of use.
What platform did Barcode Warehouse introduce to improve the picking process?
-Barcode Warehouse introduced the 'Tag Works' platform to improve the picking process.
How did the customers' feedback influence the evolution of the Tag Works platform?
-The customers' feedback was listened to and specific ideas around the picking process were implemented, ensuring the platform met their requirements.
What was essential for the company when implementing the new tool?
-It was essential to ensure that the tool was implemented without any issues and that enhanced features were added to satisfy the needs of the business.
How did the technology impact the team members' confidence in their work?
-The technology allowed team members to have more confidence in their work, which significantly improved the turnaround time on orders.
What benefits did the new tool provide for new team members in terms of training?
-The tool helped new team members to start effectively from their first day without needing extensive training, as it prevented potential mistakes.
How did the implementation of the tool affect the staff's anxiety levels and their roles?
-The tool helped staff feel more relaxed in their roles, reducing anxiety about packing the correct products and providing evidence for any client claims.
What are the future plans for the company in terms of expanding the use of Tag Works and Barcode Warehouse solutions?
-The company is looking at expanding the areas of the business that use Tag Works and Barcode Warehouse solutions, including implementing the tool within the production line.
Outlines
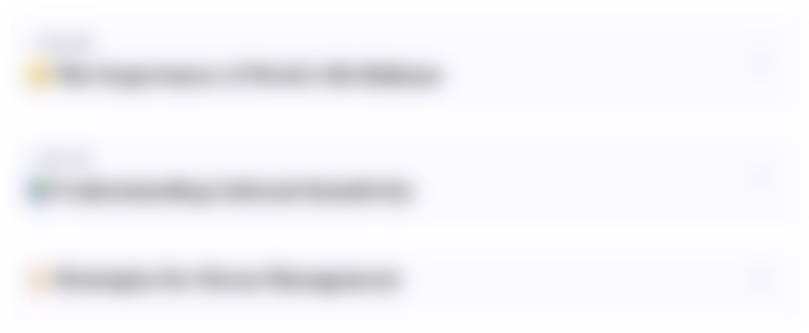
Esta sección está disponible solo para usuarios con suscripción. Por favor, mejora tu plan para acceder a esta parte.
Mejorar ahoraMindmap
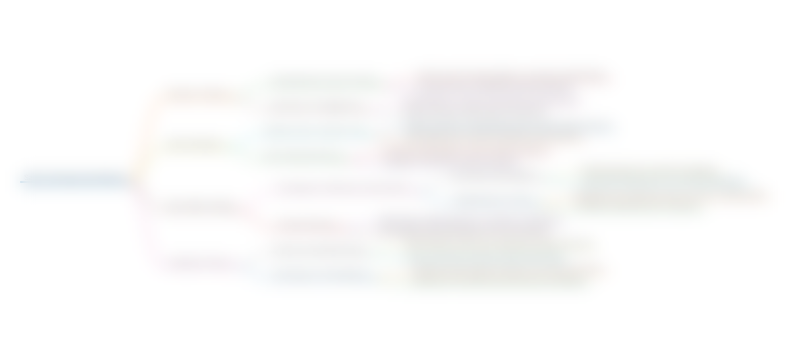
Esta sección está disponible solo para usuarios con suscripción. Por favor, mejora tu plan para acceder a esta parte.
Mejorar ahoraKeywords
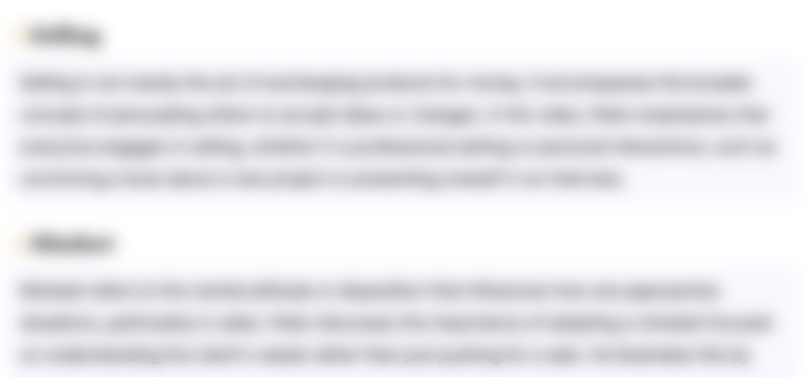
Esta sección está disponible solo para usuarios con suscripción. Por favor, mejora tu plan para acceder a esta parte.
Mejorar ahoraHighlights
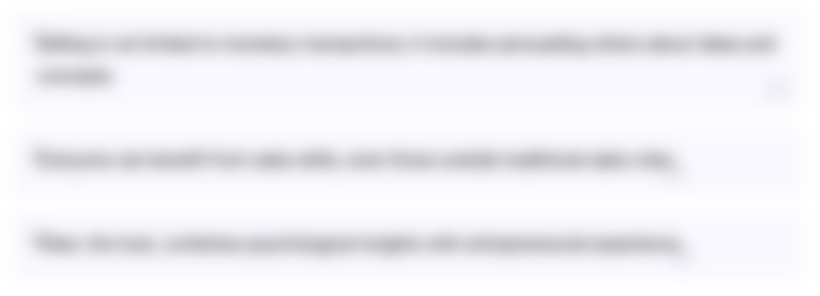
Esta sección está disponible solo para usuarios con suscripción. Por favor, mejora tu plan para acceder a esta parte.
Mejorar ahoraTranscripts
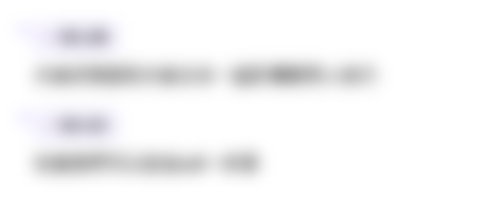
Esta sección está disponible solo para usuarios con suscripción. Por favor, mejora tu plan para acceder a esta parte.
Mejorar ahoraVer Más Videos Relacionados
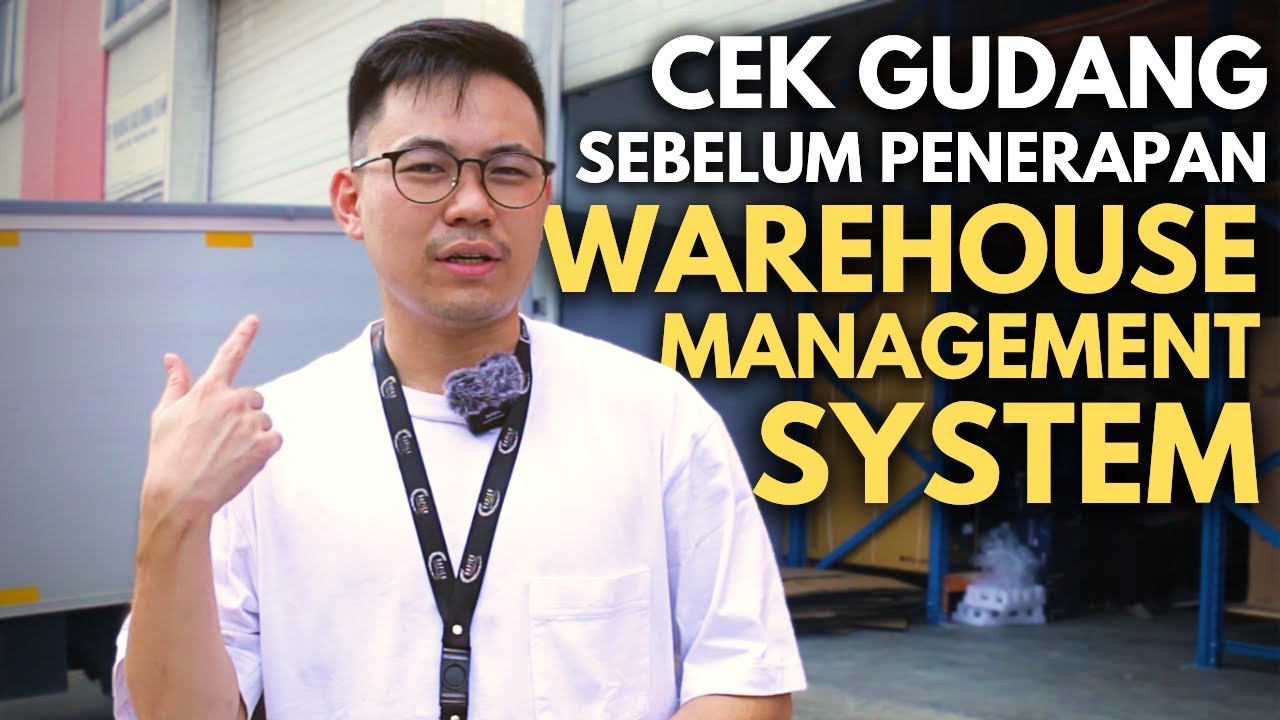
Persiapan Penerapan Warehouse Management System (WMS) | Life At Rapier Eps.5
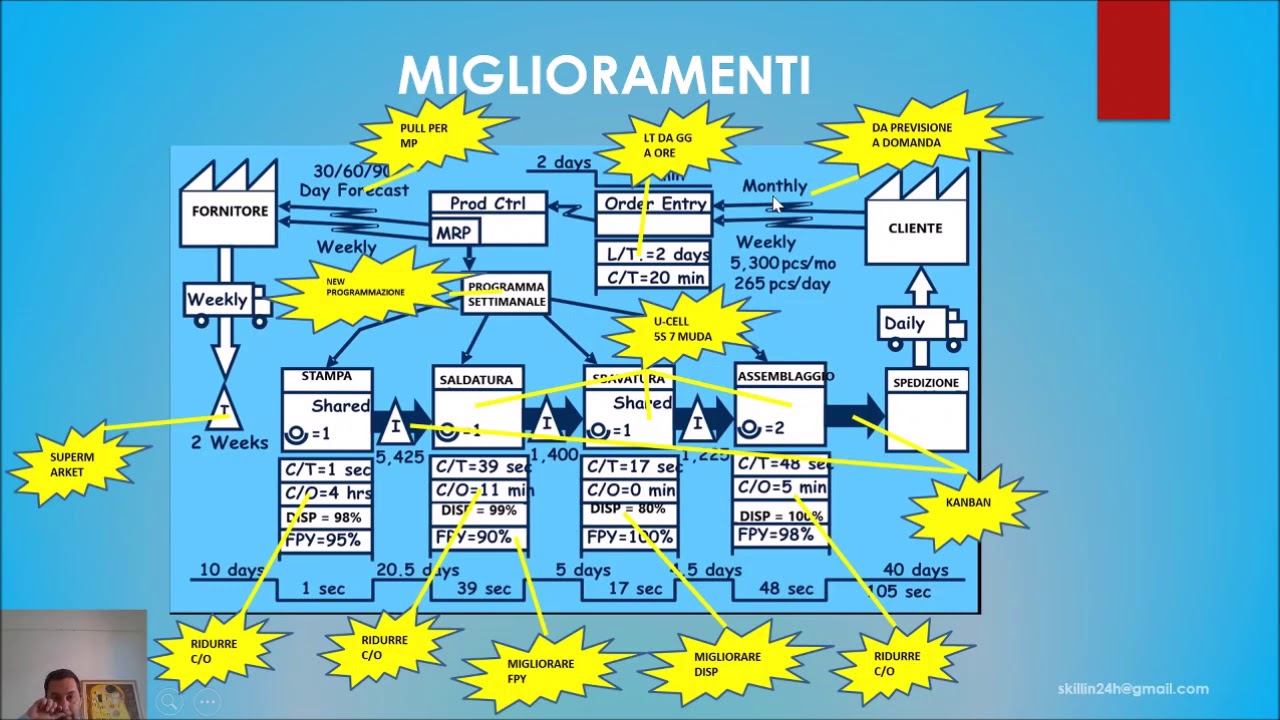
Lezione 4D - CREAZIONE VSM - Parte 4 di 4 - Lean Thinking e Toyota Producition System - Zero sprechi
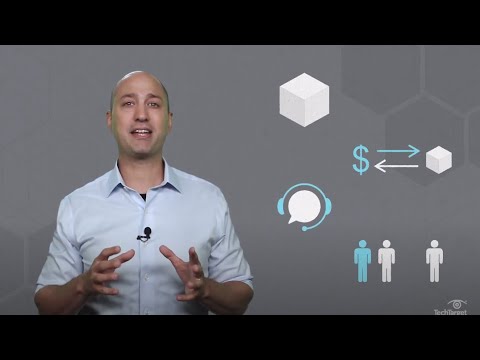
What is Business Process Management? (In About A Minute)

Cisco - Change Management Training Video

Optimizing Your Space: A Step-by-Step Guide to Designing an Efficient Warehouse Layout
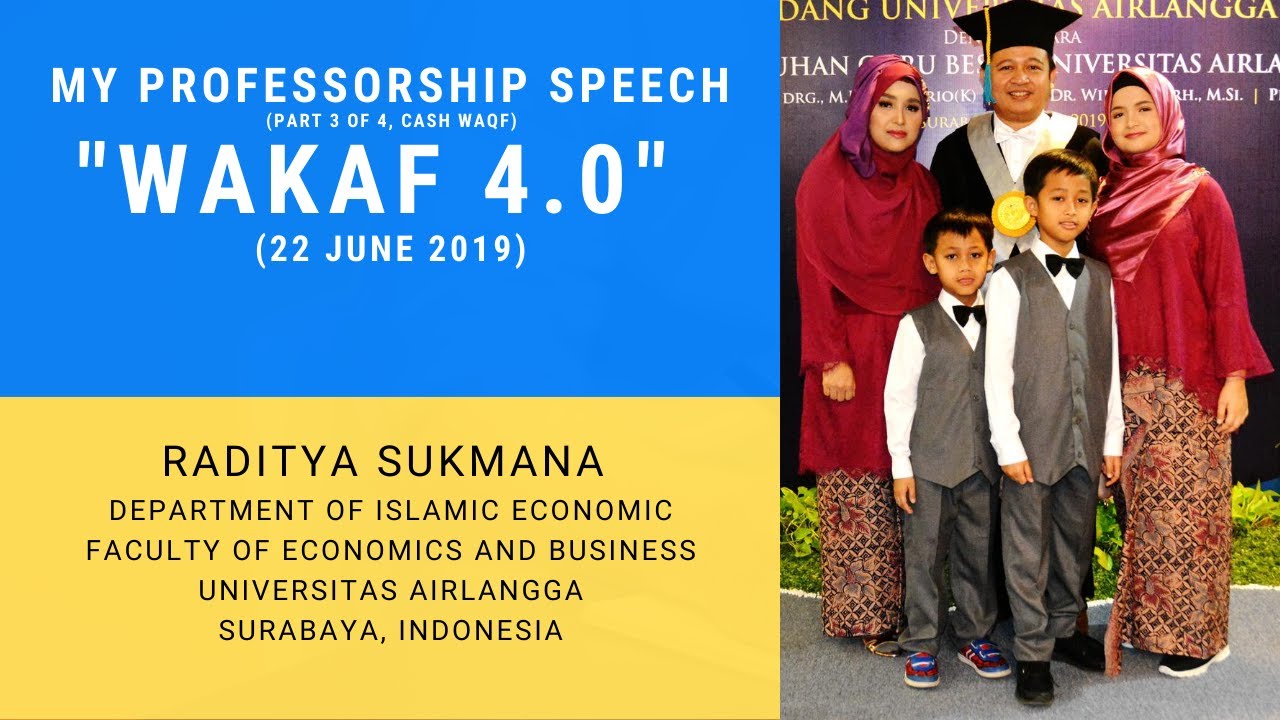
(Part 3 of 4) WAKAF 4.0 My Professorship speech, (Important of cash waqf)
5.0 / 5 (0 votes)