Topological Optimization Case Study - Additive Manufacturing
Summary
TLDRThis case study highlights the benefits of additive manufacturing in optimizing hydraulic manifold designs. Traditional subtractive manufacturing methods often lead to inefficiencies such as turbulent flow and excess material. In contrast, additive manufacturing enables the creation of complex geometries, reducing material usage and enhancing fluid flow for improved hydraulic performance. By utilizing techniques like Direct Metal Laser Sintering (DMLS) and stereolithography, the optimized manifold reduces weight, pressure losses, and manufacturing costs while increasing system efficiency and lifespan. The study demonstrates how 3D printing can transform design, offering significant improvements in hydraulic systems, particularly in the offshore drilling sector.
Takeaways
- 😀 Additive manufacturing (AM) includes three main technologies: sintering, DMLS/EBM, and stereolithography, each with distinct processes for creating complex 3D objects.
- 😀 Additive manufacturing offers the ability to create complex geometries, which traditional manufacturing methods cannot achieve due to limitations like straight-line designs and intersecting bores.
- 😀 Additive manufacturing reduces material waste by enabling the optimization of component designs, such as the hydraulic manifold block studied in this case.
- 😀 A topological optimization study of the manifold led to a 64% reduction in weight and an 87% reduction in material volume, greatly decreasing production costs.
- 😀 The optimized manifold design eliminates turbulent flow, improving hydraulic performance by reducing pressure losses by 48%.
- 😀 Computational Fluid Dynamics (CFD) simulations confirmed that the optimized manifold design eliminated turbulence, improving efficiency and reducing noise and vibration.
- 😀 Additive manufacturing allows for smoother fluid channels, which improves overall system performance and efficiency, as well as reduces operational issues like pump strain and excessive noise.
- 😀 3D printing a manifold with traditional support structures posed challenges; however, optimized slicing software was used to minimize the need for supports, though further design refinements were required.
- 😀 For industrial applications, aluminum is the recommended material for the manifold due to its lightweight, flexibility, strength, and resistance to corrosion, making it ideal for hydraulic systems.
- 😀 Selective Laser Sintering (SLS) is the most suitable method for industrial-scale 3D printing of the manifold, offering advantages like the use of unfused powder as support structures and reduced post-processing efforts.
- 😀 The case study demonstrates that optimizing manifold designs using additive manufacturing not only improves hydraulic system efficiency but also reduces material costs, weight, and improves the working environment in industrial settings like offshore drilling.
Q & A
What are the three broad types of additive manufacturing technologies mentioned in the script?
-The three broad types of additive manufacturing technologies are Syntherin, Direct Metal Laser Sintering (DMLS), and Stereolithography.
How does Syntherin work, and what materials are involved?
-Syntherin works by heating the material without melting it to create complex high-resolution objects. It uses metal powders in Direct Metal Laser Sintering (DMLS) and thermoplastic powders in Selective Laser Sintering (SLS).
What is the main advantage of additive manufacturing over subtractive manufacturing in the context of hydraulic manifolds?
-Additive manufacturing allows for the creation of complex geometries that would be impossible to fabricate with subtractive manufacturing, improving fluid flow and hydraulic performance by reducing turbulence and pressure losses.
What impact does the topological optimization study have on the manifold block?
-The topological optimization study resulted in a 64% reduction in component weight and an 87% reduction in the volume of material needed, lowering material costs while meeting all operational constraints.
What does CFD simulation reveal about the performance of the optimized manifold design?
-CFD simulation showed that the optimized design reduced pressure losses by 48% and eliminated turbulent flow, improving the hydraulic system's overall efficiency and reducing noise and vibration.
What issue was identified regarding support structures when 3D printing the manifold, and how was it resolved?
-The challenge was removing complex support structures, especially in long channels. This was resolved using slicing software to reduce or remove the necessary support structures, and a prototype was successfully printed and tested.
Why is PLA material used for prototyping in 3D printing, and what are its limitations?
-PLA is used for prototyping because it is easy to use, low cost, and environmentally friendly. However, its brittleness makes it unsuitable for high-stress applications or functional prototypes.
Why is aluminum considered the best material for manufacturing hydraulic manifolds?
-Aluminum is ideal for hydraulic manifolds because of its lightweight, high strength, excellent thermal properties, and corrosion resistance, which are critical for oilfield equipment exposed to harsh environments.
What is the key benefit of using the Selective Laser Sintering (SLS) method for 3D printing the manifold?
-SLS eliminates the need for additional support structures, as the unfused powder acts as support. This results in cleaner designs, especially for complex internal channels.
What post-processing steps are necessary for improving the manifold's finish after 3D printing?
-After 3D printing, the manifold requires post-processing steps like cutting threads, sandblasting the external features, polishing internal bores, and anodizing the surface to improve appearance, strength, and corrosion resistance.
Outlines
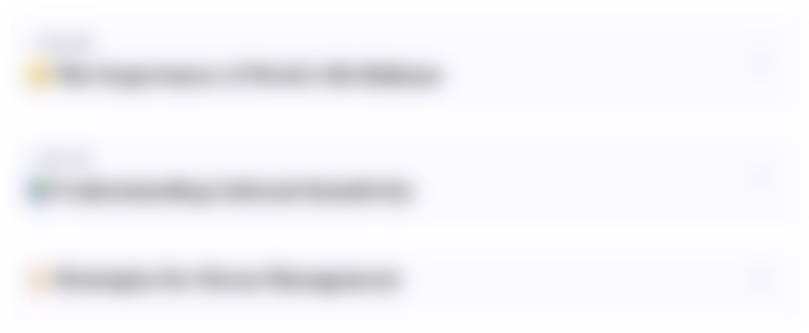
هذا القسم متوفر فقط للمشتركين. يرجى الترقية للوصول إلى هذه الميزة.
قم بالترقية الآنMindmap
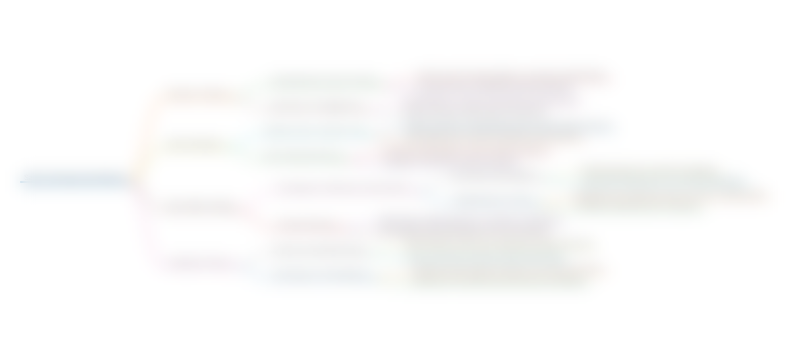
هذا القسم متوفر فقط للمشتركين. يرجى الترقية للوصول إلى هذه الميزة.
قم بالترقية الآنKeywords
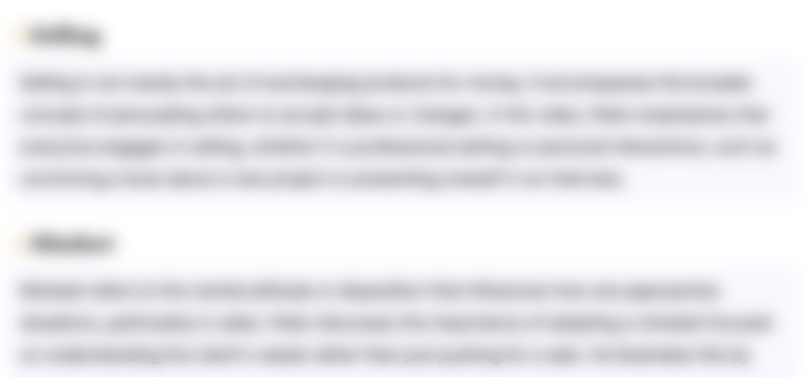
هذا القسم متوفر فقط للمشتركين. يرجى الترقية للوصول إلى هذه الميزة.
قم بالترقية الآنHighlights
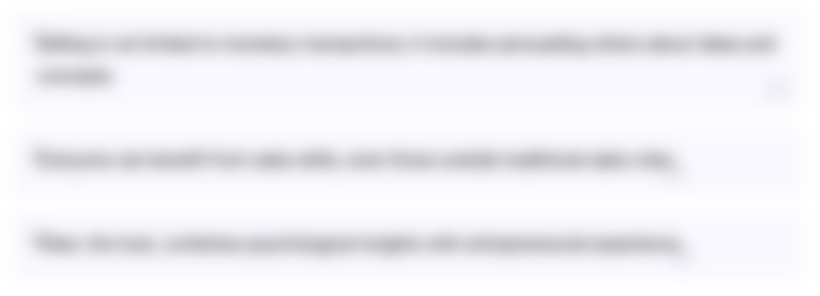
هذا القسم متوفر فقط للمشتركين. يرجى الترقية للوصول إلى هذه الميزة.
قم بالترقية الآنTranscripts
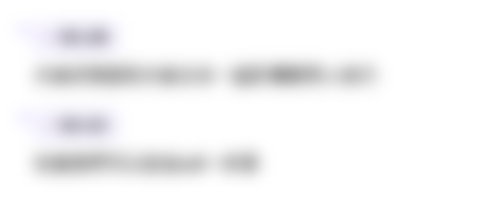
هذا القسم متوفر فقط للمشتركين. يرجى الترقية للوصول إلى هذه الميزة.
قم بالترقية الآنتصفح المزيد من مقاطع الفيديو ذات الصلة
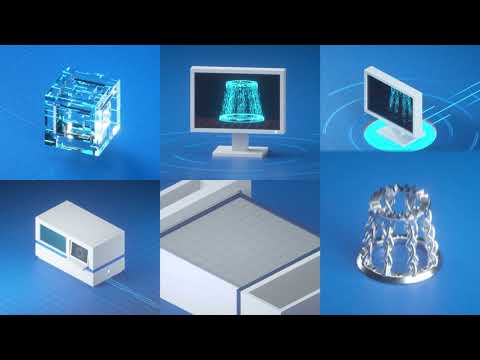
What is additive manufacturing? | GE Additive
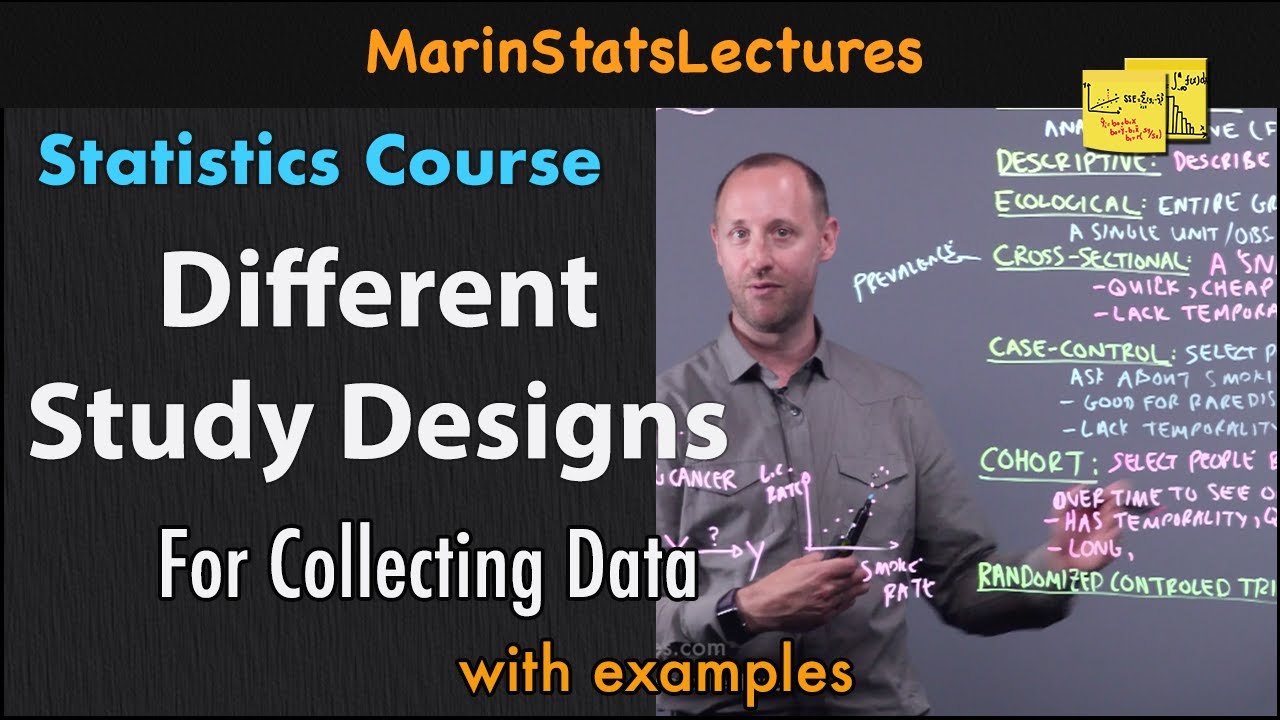
Study Designs (Cross-sectional, Case-control, Cohort) | Statistics Tutorial | MarinStatsLectures
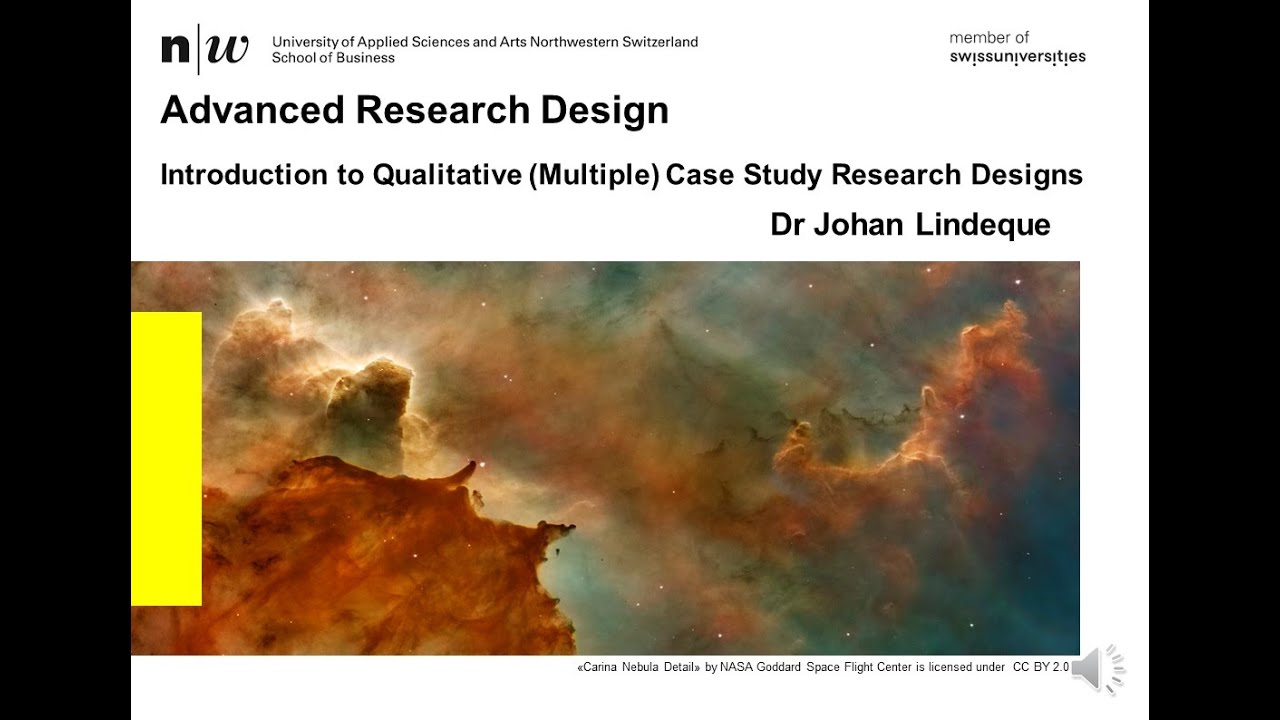
IMRM 2020 Lecture Slides Lecture 04 4 Logic of Case Studies 1080
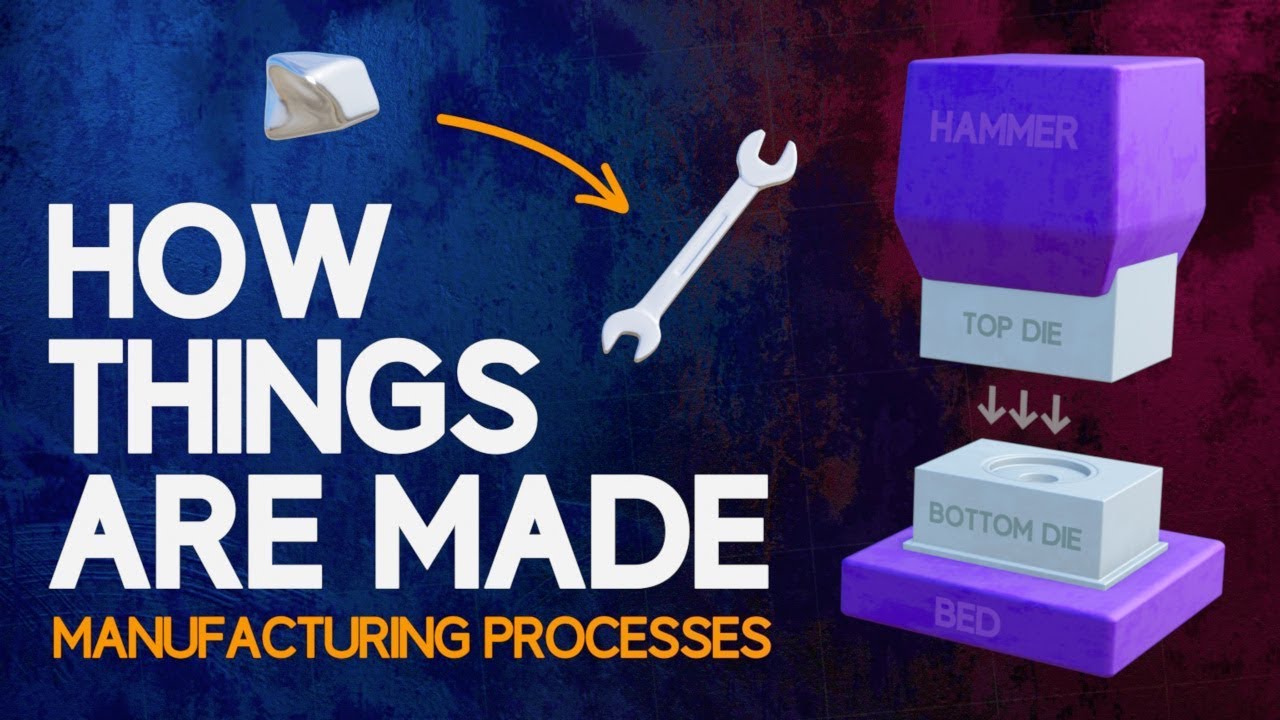
How Things Are Made | An Animated Introduction to Manufacturing Processes

Design Studio 3 Digital Fabrication

Additive Manufacturing Processes
5.0 / 5 (0 votes)