Semiconductor Packaging - ASSEMBLY PROCESS FLOW
Summary
TLDRIn this video, Lito Galera provides an insightful introduction to semiconductor packaging, detailing the intricate processes involved in transforming silicon wafers into functional electronic devices. He explains key steps such as wafer sawing, die attachment, wire bonding, molding, marking, and the final trim form and singulation. Each process is crucial for ensuring device integrity and performance, with a focus on precision and efficiency. Lito emphasizes the importance of electrical testing to guarantee quality before market release, inviting viewers to engage further with his channel for more in-depth videos on these topics.
Takeaways
- 😀 Semiconductor packaging is a crucial process that transforms silicon wafers into usable electronic devices.
- 🔪 The wafer saw process cuts the wafer into individual chips, called dies, using diamond blades to minimize damage.
- 📏 Wafer sizes vary, with 4, 5, 6, 8, and 12-inch diameters used for different semiconductor applications.
- 📦 Die attach involves mounting the die onto a lead frame, typically using adhesive epoxy or soft solder.
- ⚡ Lead frames are primarily made of copper due to its excellent electrical conductivity and cost-effectiveness.
- 🧪 After die attach, an oven is used to cure the adhesive epoxy before proceeding to wire bonding.
- 🔗 Wire bonding connects each die terminal to corresponding leads using materials like gold, copper, silver, or aluminum.
- ⚙️ The bonding cycle consists of precise movements to create secure connections between the die and leads.
- 🌡️ Molded devices are protected from environmental damage, with epoxy molding compound (EMC) used for encapsulation.
- ✅ After packaging, devices undergo electrical testing to ensure they meet specifications before being released to the market.
Q & A
What is semiconductor packaging?
-Semiconductor packaging is the process of transforming semiconductor devices from wafer form into molded, ready-to-use devices for electronic systems. It involves several steps including wafer cutting, die attachment, wire bonding, and molding.
What are wafers and why are they significant in semiconductor manufacturing?
-Wafers are thin slices of semiconductor material, typically silicon, that contain numerous devices or chips. They are significant because they serve as the starting point for producing semiconductor devices, with each wafer potentially holding thousands of individual chips.
What happens during the wafer saw process?
-During the wafer saw process, the wafer is cut into individual chips, known as dies. This process is delicate, requiring precision to avoid damaging the wafer, as any breakage can be costly.
What materials are commonly used for die attach, and why?
-Common materials for die attach include silver-filled epoxy for ICs and soft solder or eutectic methods for diodes and transistors. The choice of material depends on the application, as it must ensure a reliable electrical connection and withstand operating conditions.
How does wire bonding work in semiconductor packaging?
-Wire bonding connects each die terminal to corresponding leads of the lead frame. This complex process involves several cycles where wires are bonded to the die and lead frame, using various types of wires like gold, copper, silver, or aluminum.
What is the purpose of molding in semiconductor packaging?
-Molding encapsulates the semiconductor device to protect it from environmental factors and mechanical damage. It ensures the integrity of the device, especially after wire bonding, which can make it vulnerable.
What information is typically included during the marking process?
-The marking process includes printing essential information such as the company logo, device code, manufacturing date code, manufacturing location code, and pin one orientation on the package.
What is trim, form, and singulation (TFS) in semiconductor packaging?
-TFS is the final step in the packaging process that involves removing tie bars to separate the leads, forming the leads into the desired shape (usually gull wing), and singulating the devices from the lead frame.
What is the significance of testing after the packaging process?
-Testing after the packaging process ensures that only devices meeting electrical specifications and aesthetic quality are released to the market, which is crucial for maintaining reliability and customer satisfaction.
Why is it important to use known good dies (KGD) during the die attach process?
-Using known good dies (KGD) during die attach is important to avoid wasting materials and time on defective dies. It ensures that only functional dies are processed further in the packaging workflow.
Outlines
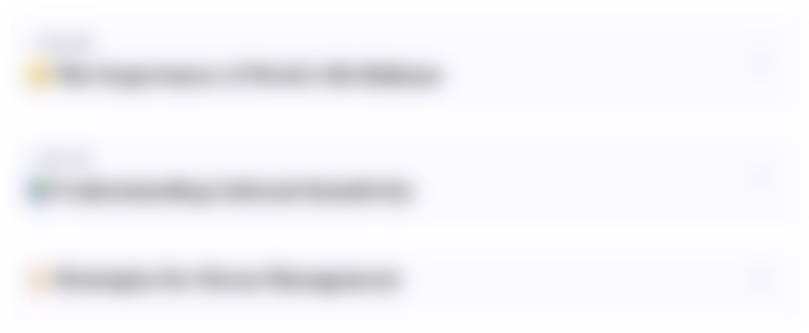
هذا القسم متوفر فقط للمشتركين. يرجى الترقية للوصول إلى هذه الميزة.
قم بالترقية الآنMindmap
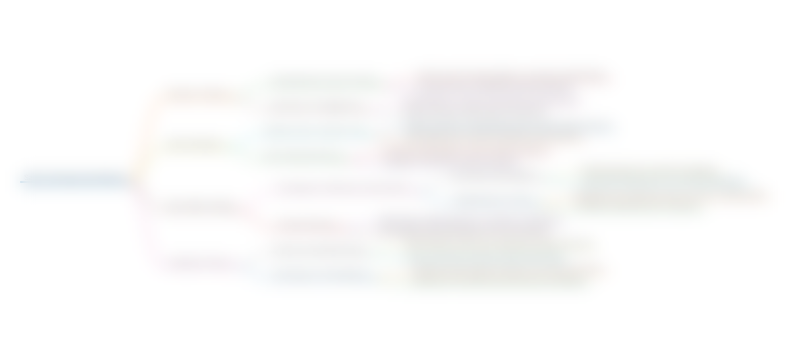
هذا القسم متوفر فقط للمشتركين. يرجى الترقية للوصول إلى هذه الميزة.
قم بالترقية الآنKeywords
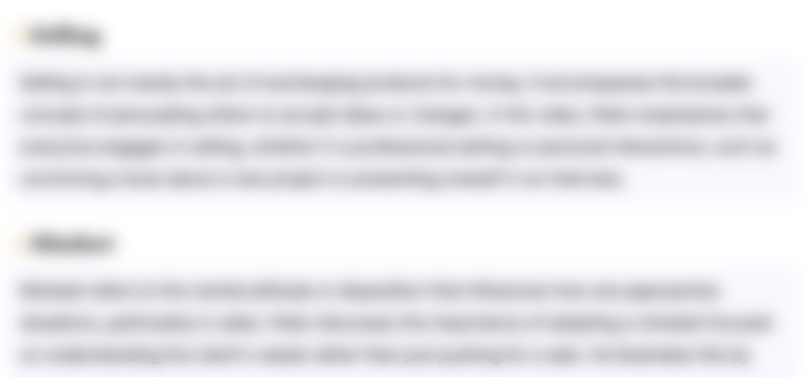
هذا القسم متوفر فقط للمشتركين. يرجى الترقية للوصول إلى هذه الميزة.
قم بالترقية الآنHighlights
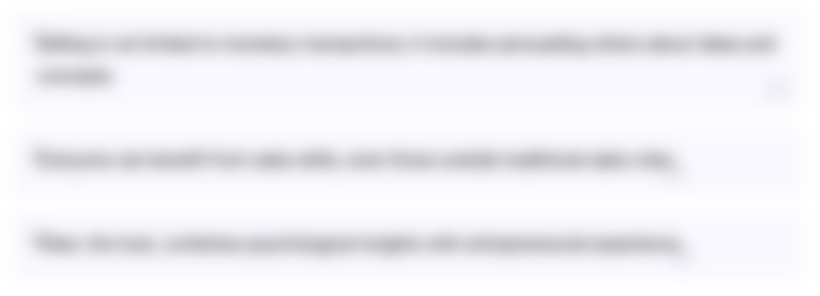
هذا القسم متوفر فقط للمشتركين. يرجى الترقية للوصول إلى هذه الميزة.
قم بالترقية الآنTranscripts
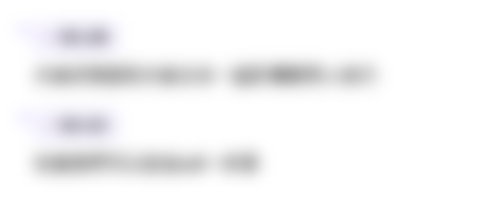
هذا القسم متوفر فقط للمشتركين. يرجى الترقية للوصول إلى هذه الميزة.
قم بالترقية الآنتصفح المزيد من مقاطع الفيديو ذات الصلة
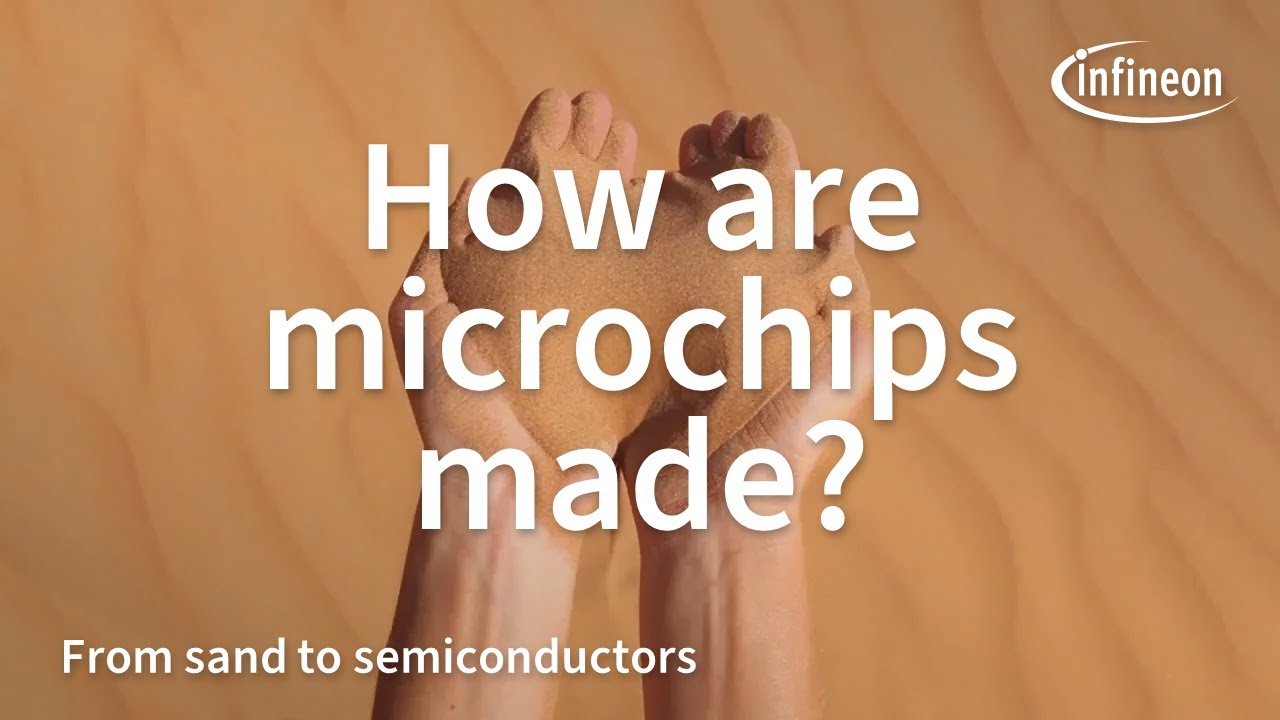
Chip Manufacturing - How are Microchips made? | Infineon

💻 How Are Microchips Made?
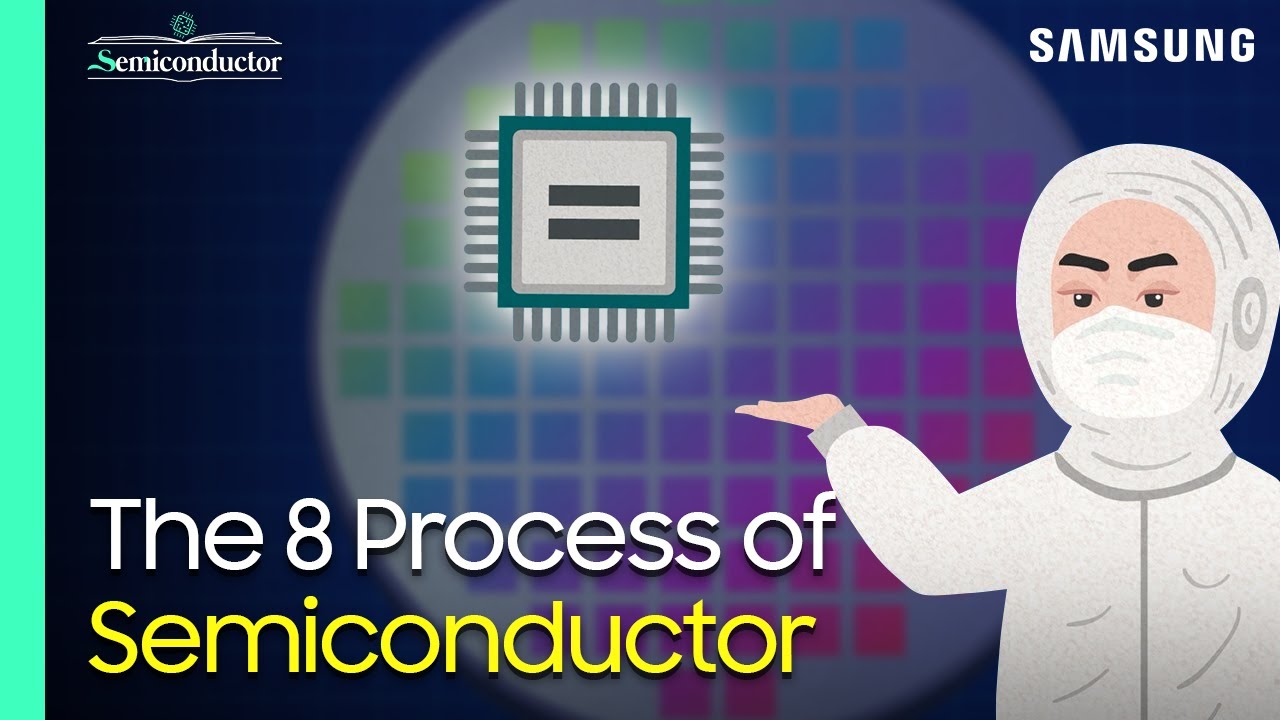
‘Semiconductor Manufacturing Process’ Explained | 'All About Semiconductor' by Samsung Semiconductor
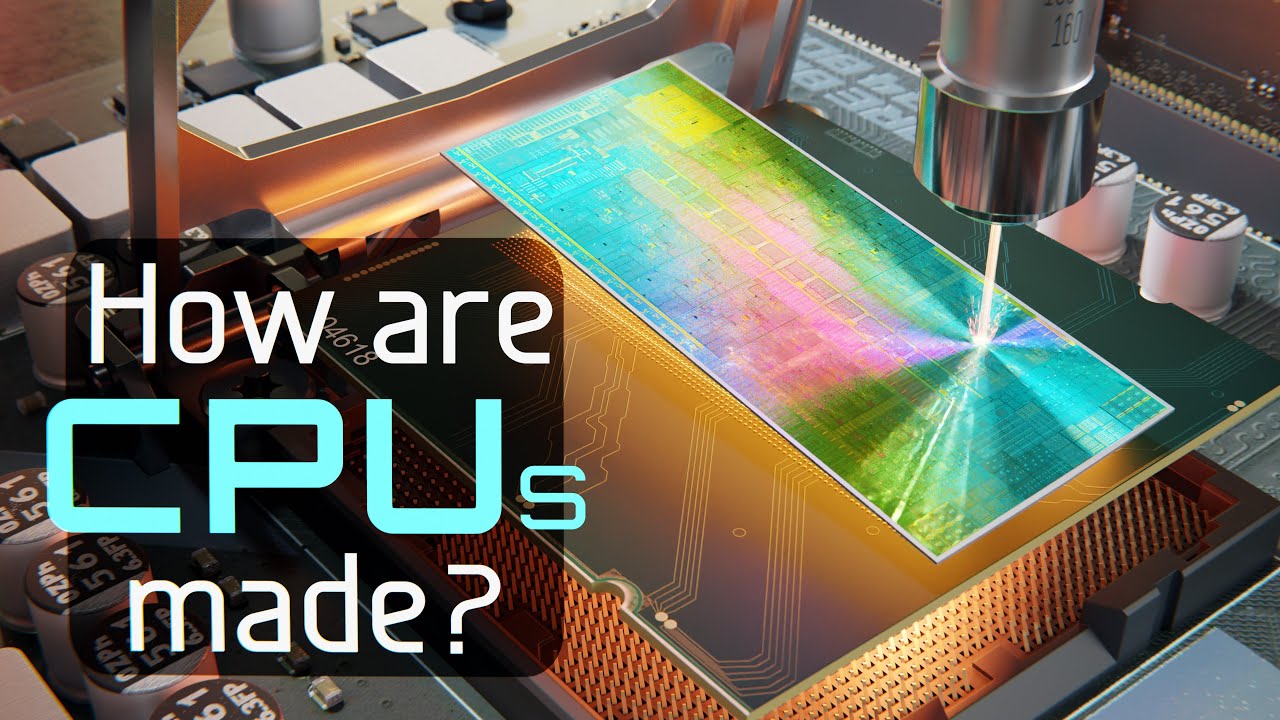
How are Microchips Made? 🖥️🛠️ CPU Manufacturing Process Steps
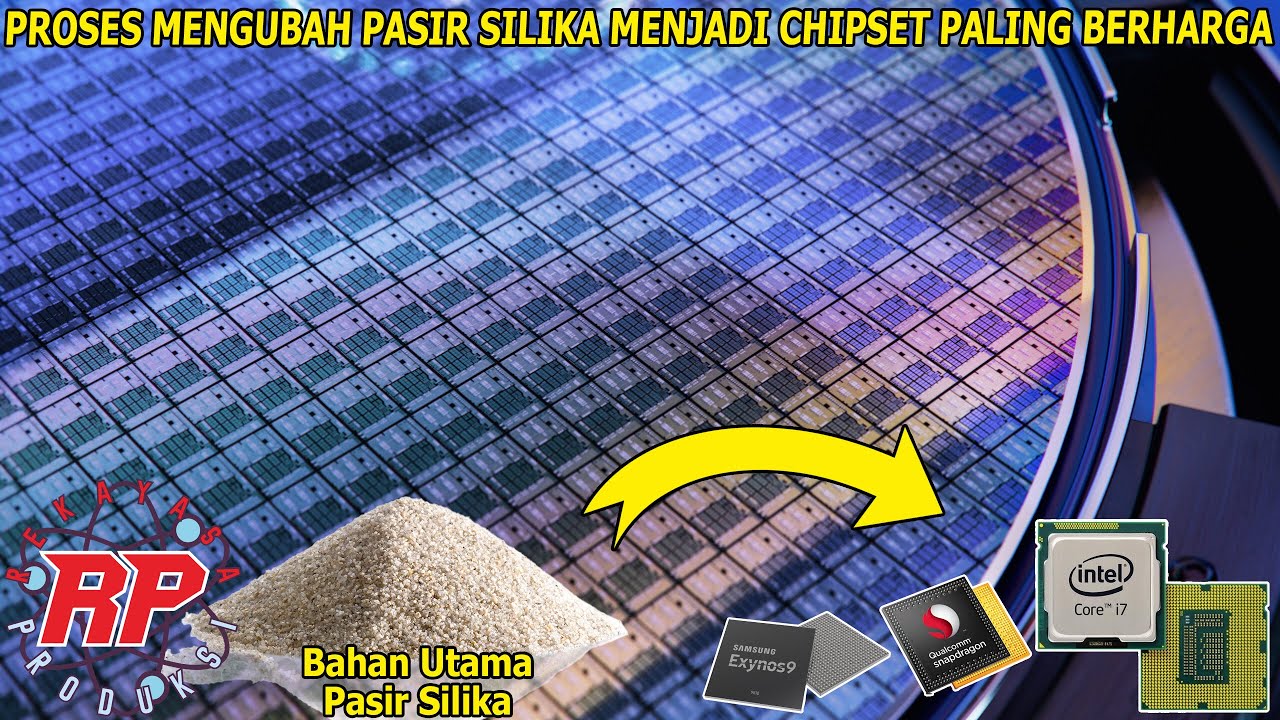
INTIP PROSES PRODUKSI CHIP SEMIKONDUKTOR TERMODERN DARI SILIKON MURNI KE REVOLUSI DIGITAL PROCESSOR
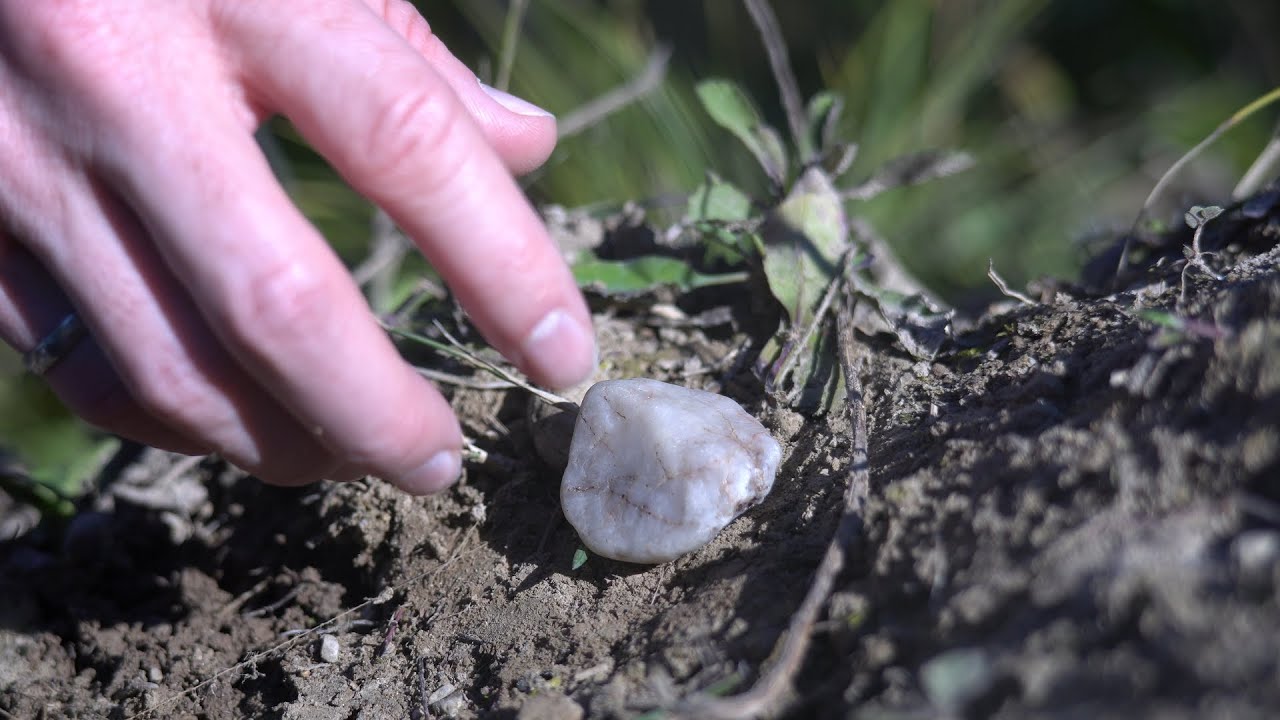
How To Make A CPU
5.0 / 5 (0 votes)